How to MIG Weld: A Complete Guide
Jan 22nd 2024
MIG welding, or Metal Inert Gas welding, is a widely used welding process that is known for its versatility and efficiency. Also referred to as GMAW, or Gas Metal Arc Welding, this process utilizes a continuous solid wire electrode, a shielding gas, and a welding gun to join metals together. This comprehensive guide explores the many facets of MIG welding, including an examination of the fundamentals, step-by-step procedures, and specialized techniques for working with different materials. This guide will provide valuable insights to enhance your MIG welding skills, whether you’re just starting out in the field or you’re an experienced welder.
Essential MIG Welding Equipment Needed for Successful Welding
When MIG welding, you’ll need specific equipment and gear to weld safely and effectively. The following is a list of recommended items for MIG welding:
- MIG welder
- Gun replacement tips
- Welding gun liner to smoothly guide the wire to the contact tip
- Welding wire feeder for improved control
- PPE (Personal Protective Equipment)
- Welding helmet with darkened lens
- Safety glasses
- Welding apron or jacket or flame-resistant clothing
- Welding gloves
- Welding steel-toed boots
- Welding mask or respirator for fume protection
- Ear protection
- Ventilation system (if welding indoors)
- MIG welding wire (see details below)
- Gas selection (see details below)
- Wire brush (not steel wire), grinder, or solvent to scrape away metal and clean the area. (Steel wire can contaminate the weld and cause rust)
- Metal clamps to keep the material stabilized
- Angle grinder for pre-weld and post-weld operations
- Temperature tracker (electronic infrared thermometer, temperature indication sticks, or electronic surface temperature probe)
- Welding table for shop work or safe workstation at a large facility
- 1 = flat position
- 2 = horizontal position
- 3 = vertical position
- 4 = overhead position
- G = groove weld
- F = fillet weld
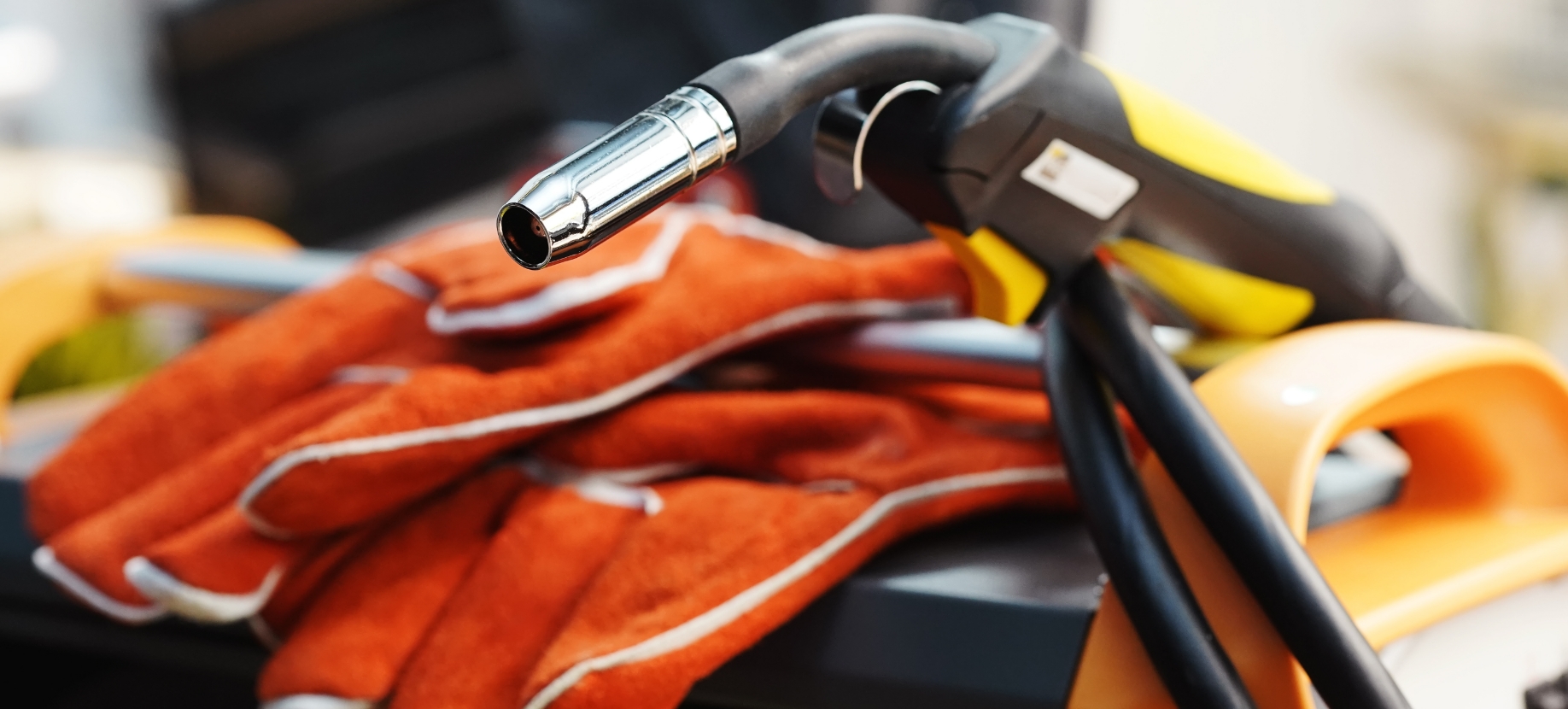
How to Choose the Right Welding Wire for MIG Welding
The right welding wire for your MIG welding operation can mean all the difference. It directly impacts the quality and performance of the weld. There are many different types of welding wire that are designed to work with various base materials and welding applications. We’ll give a quick overview of just a few of these welding wires and their characteristics.
Carbon Steel Welding Wires
Carbon steel welding wires, which are available as copper-coated and copper-free, are designed for welding carbon and mild steels. They demonstrate great versatility, allowing welders to utilize their strengths for various applications. They offer good performance and provide stable arcs, minimal spatter, and excellent bead appearance. Some of the most common wires include ER70S-3, ER70S-6, and ER80S-D2. Check out our helpful article to learn more: How to Choose the Right Welding Wire for Carbon Steel.
Stainless-Steel Welding Wires
Stainless-steel welding wires are designed for the various grades of stainless steel with different alloy compositions. Their inherent resistance to corrosion makes them especially useful for applications that rely on the weld maintaining its strength even in corrosive environments. The ER308 is used for welding austenitic stainless steels, like 304; ER309 is more suitable for welding stainless steel to mild steel; ER316 can be used for working with 316 and other similar grades. Go learn more about which stainless steel welding wires are best for the job using our handy guide: The Best Welding Wires for Stainless Steel.
Aluminum Welding Wires
Aluminum welding wire is specifically formulated for welding aluminum alloys, exhibiting higher strength-to-weight ratios to complement the lightweight characteristic of aluminum. These wires can achieve proper penetration with minimal risk of porosity while maintaining the strength of the weld. Common welding wires include ER4043, which is a general-purpose wire for welding 3003, 3004, 5052, 6061, and 6063 alloys, as well as ER5356, which is usually used for higher-strength alloys like 5050, 5052, 5083, 5356, and 5456.
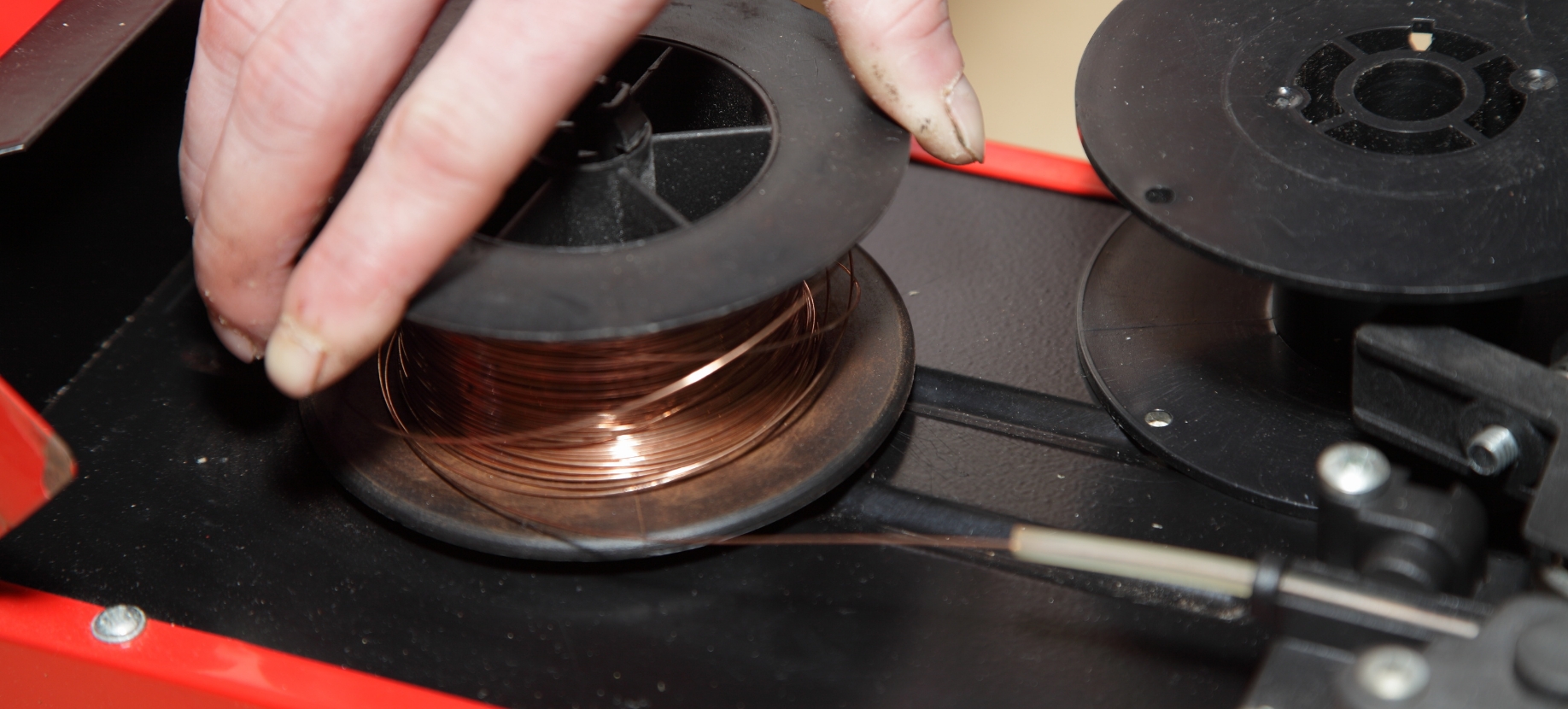
The Influence of Welding Wire Diameter
One of the most important deciding factors of your welding wire selection is the diameter of the welding wire compared to the thickness of the base material. The thickness of your mild steel outwardly determines the size of the welding wire you’ll be using for the job. To put it simply, the thicker the material, the larger the welding wire diameter.
Thicker materials generally require more heat for proper penetration and fusion, so a larger-diameter welding wire is needed to properly carry the right amount of current to effortlessly penetrate to the root of the weld. For sections of materials that are about 1/8” to 3/8” thick, a 0.035” to 0.045” welding wire would be a good choice.
Thinner materials are usually less forgiving of heat and are very susceptible to distortion caused by excessive exposure to heat during welding. Successfully welding thinner sections requires precise control over the heat input. This is where a more versatile, smaller-diameter welding wire is the best choice for the job. For certain materials that are about 24-gauge to 14-gauge, a 0.025” to 0.030” welding wire would work ideally.
A lot of welding issues can emerge if you’re mismatching the diameter of the welding wire and the thickness of the material. Welding a thin section with a large diameter welding wire can cause burn-through while welding a thick section with a small diameter welding wire can cause inadequate penetration. The structural integrity of the weld relies on this type of compatibility between the welding wire and the material, so careful consideration needs to be taken in order to do the job right.
How to Select the Right Shielding Gas for MIG Welding
During the welding process, the weld pool is developed as the base material and the welding wire are fused together. Shielding gas is used to protect the pool from atmospheric contaminants to prevent porosity and other welding defects. The type of gas used depends on the welding process, application, type of welding wire used, among other factors. The shielding gas can affect spatter levels, arc performance, and arc stability, so careful consideration needs to be taken when making your selection.
One of the most common selections for shielding gases is a 75% argon/25% carbon dioxide mix, which is known for producing minimal spatter while providing good arc characteristics. However, argon can be expensive, so it’s not the most cost-effective choice for shielding gases.
An alternative is 100% carbon dioxide, which provides very deep weld penetration that allows you to create a solid and reliable weld with ease. However, it doesn’t provide the same arc stabilizers as an argon/carbon dioxide mix and the end result is more spatter.
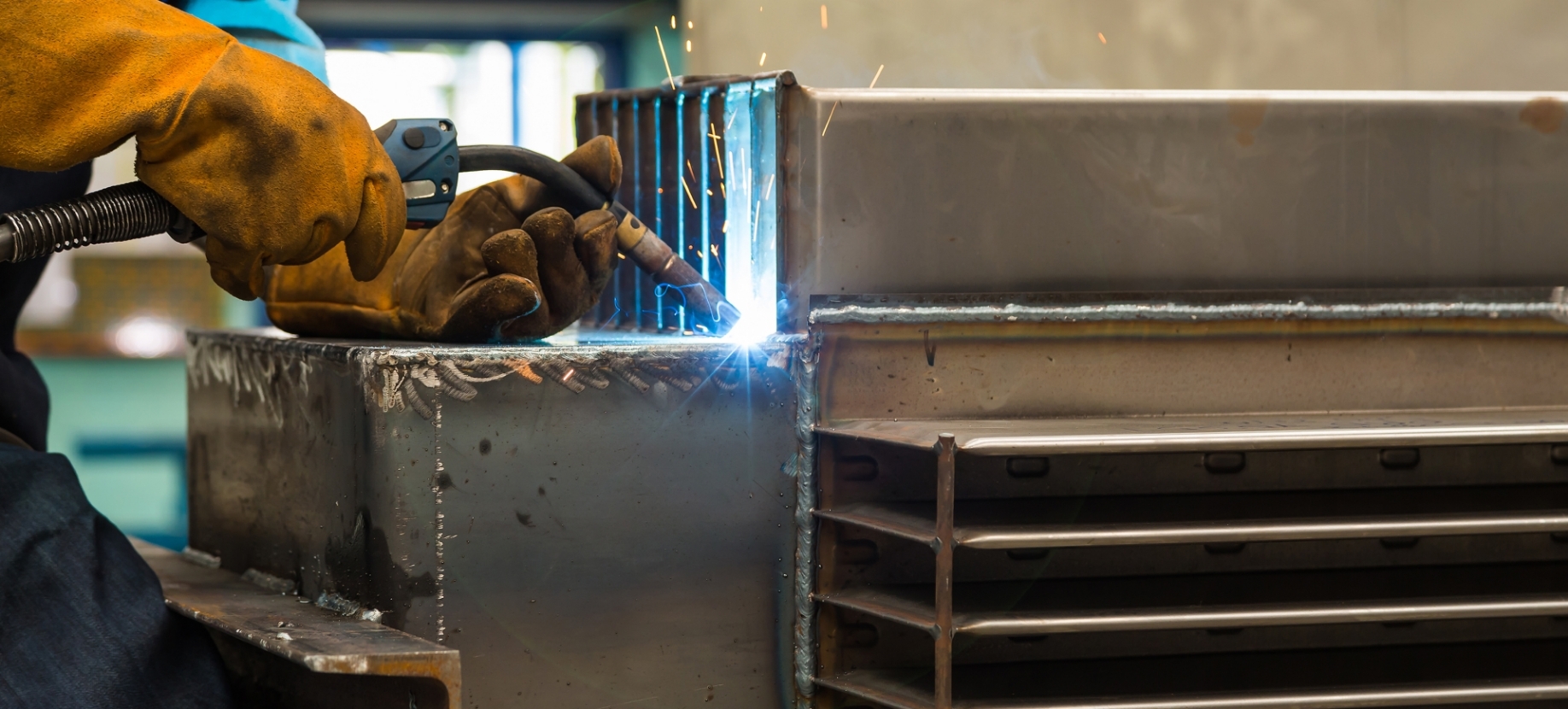
Common MIG Welding Techniques to Master for a Successful Weld
There are several techniques that a new welder can practice to master MIG welding. Understanding the different MIG welding positions, the types of metal transfer modes, and the various joint preparations can be the key to achieving strong and precise welds for every MIG welding operation.
Familiarity with welding positions is crucial for adapting techniques to different orientations. Joint preparation is a critical step, and a welder needs to understand the various joint types for proper preparation. Metal transfer modes help guide the selection of the most suitable technique for a specific welding task, and understanding each mode’s distinct characteristics can influence that choice. By mastering these welding techniques, welders can enhance their versatility, tackle diverse projects, and produce high-quality welds.
A Rundown on MIG Welding Positions
Due to the versatility of MIG welding, this process can be performed in various positions to accommodate different welding applications. The official positions are standardized and defined by the American Welding Society (AWS) using letters and numbers to indicate the position and the type of weld joint required – 1G, 2G, 3G, 4G or 1F, 2F, 3F, 4F. The positions are identified by letters, and each letter corresponds to a specific orientation of the weld joint relative to the welder. A fillet weld joins two pieces of metal that are perpendicular or at an angle. A groove weld occurs between materials or their edges.
So, using this system, you can conclude that a 1F weld is a fillet weld in the flat position. Let’s dive a little deeper into the different types of welding positions.
Flat Position (1G or 1F): One of the most basic welding positions, the flat position is where the weld is performed from the top side of the joint with the weld facing horizontally. This is an easy position to work in since the weld pool isn’t fighting gravity, so it stays fluid.
Horizontal Position (2G or 2F): The weld is produced on the top side of a horizontal surface and against a vertical surface where the weld axis is horizontal. The weld pool may fall victim to gravity, so make sure to adjust welding parameters to keep control over the heat input to carry the weld bead in the weld joint.
Vertical Position (3G or 3F): Welding is accomplished on a vertical surface in either vertical up or vertical down motions. Reducing the wire feed speed and voltage can help keep control over the puddle, making sure that it doesn’t fall out of the joint.
Overhead Position (4G or 4F): This position involves welding from the underside of the joint. It’s recommended that welders find a comfortable position to work in and wear extra protection against the sparks that may rain down.
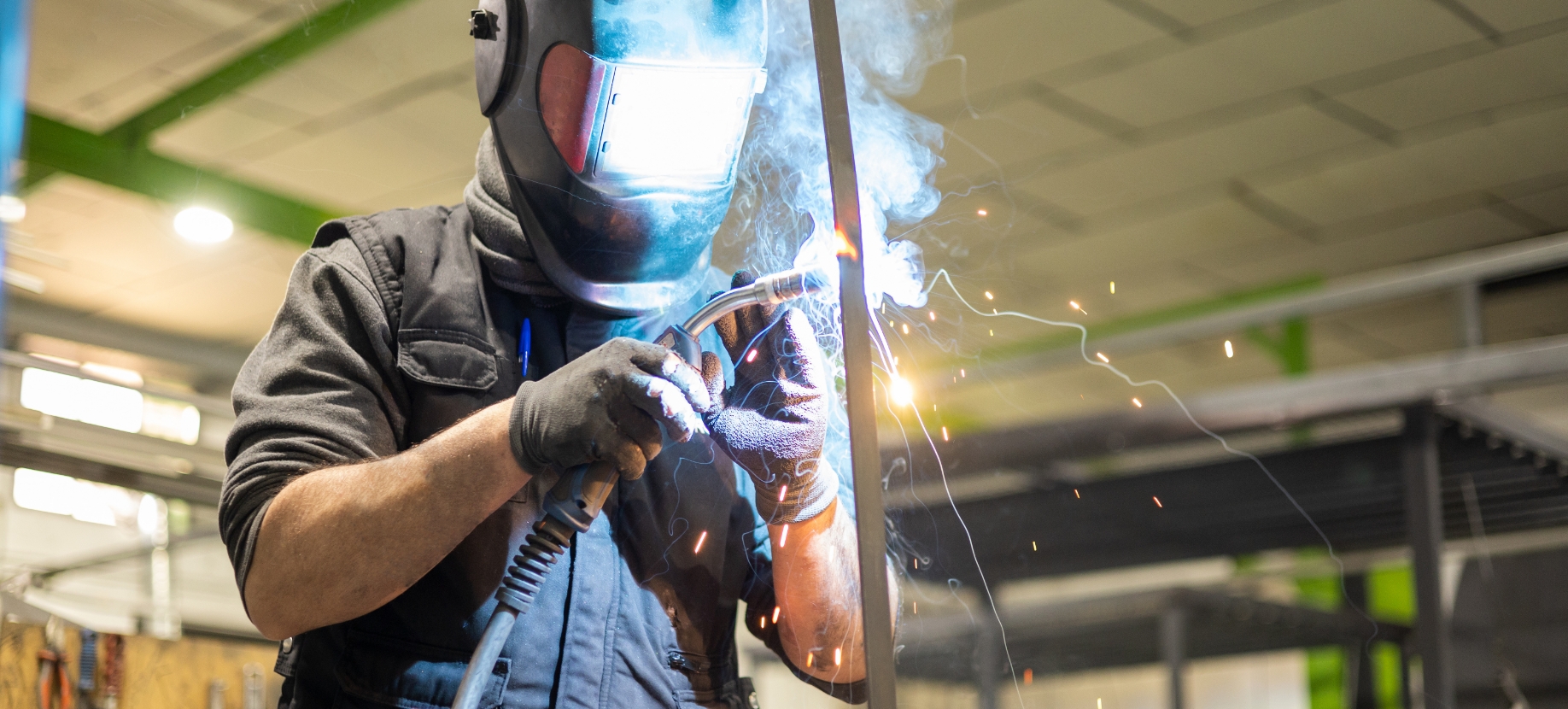
Joint Preparation for Different Types of Joints
Joint preparation is a critical step in MIG welding since it helps the welder achieve a reliable, good weld. Neglecting this step can lead to improper or poor fusion, which can jeopardize the integrity of the weld.
There are five basic types of joints recognized by the AWS: butt joints, corner joints, edge joints, lap joints, and T-joints. The type chosen for the job determines the type of weld that needs to be produced to meet acceptable quality standards. Butt joints require a groove weld; corner joints can be fillet or groove welds; edge joints require a groove weld; lap joints require fillet welds; and T-joints require fillet welds. Let’s give a quick rundown over each type of joint.
Butt Joints: This joint combines two materials in the same plane with edges meeting or parallel root openings. It features good mechanical strength when fitted and welded properly and can be welded with or without backing. The edges may require no edge preparation, but beveled edges are common, so the welding job may require a specific bevel angle. This type is commonly used in automotive repair for car exhaust systems and door panel fabrication.
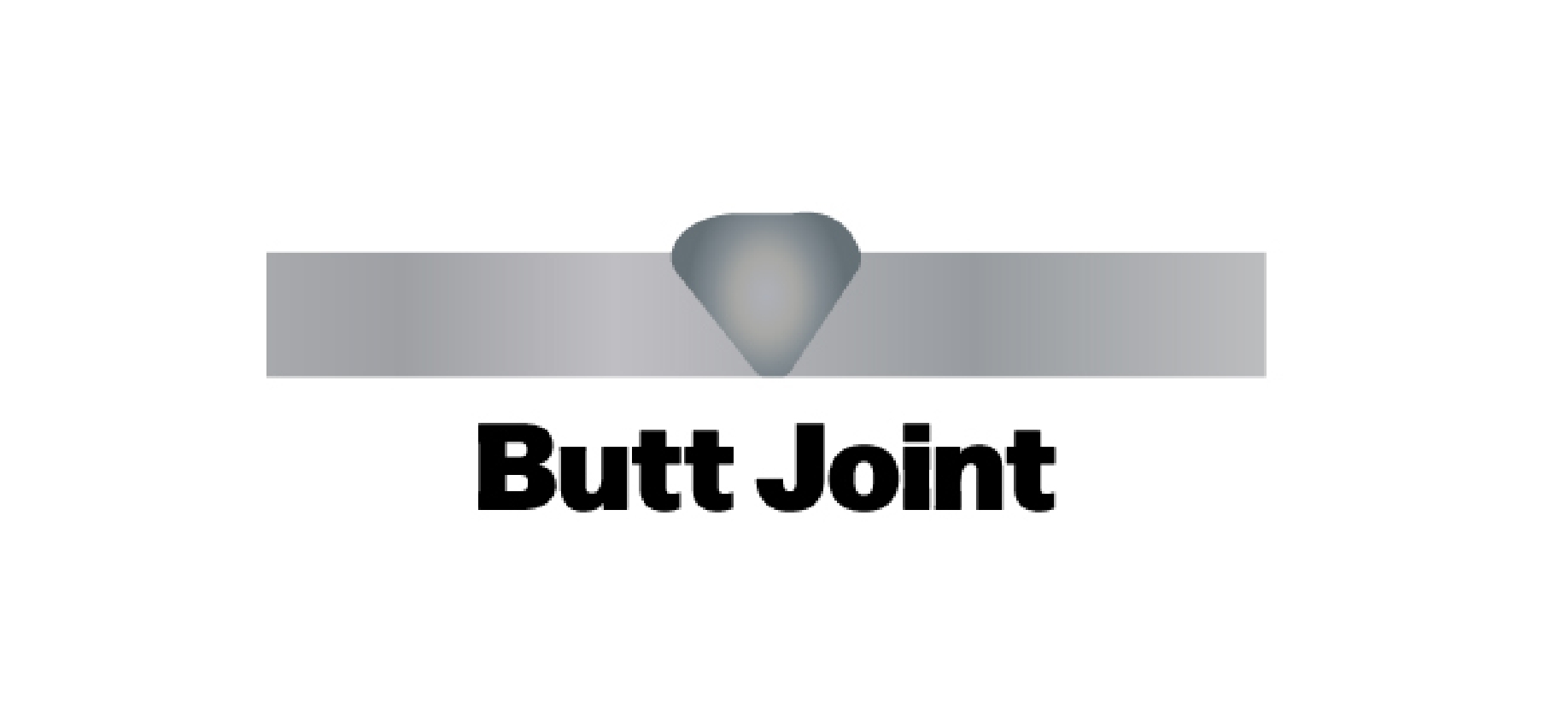
Corner Joints: This joint forms an L-shape when the pieces are joined at 90 degrees. It can be an open corner, when two edges meet at their corners and there’s an opening that shows the thickness of each metal, or a closed corner, when the edge of one piece lies flush against the edge of the other. Corner joints are easy to create and are commonly used on applications that require a square frame.
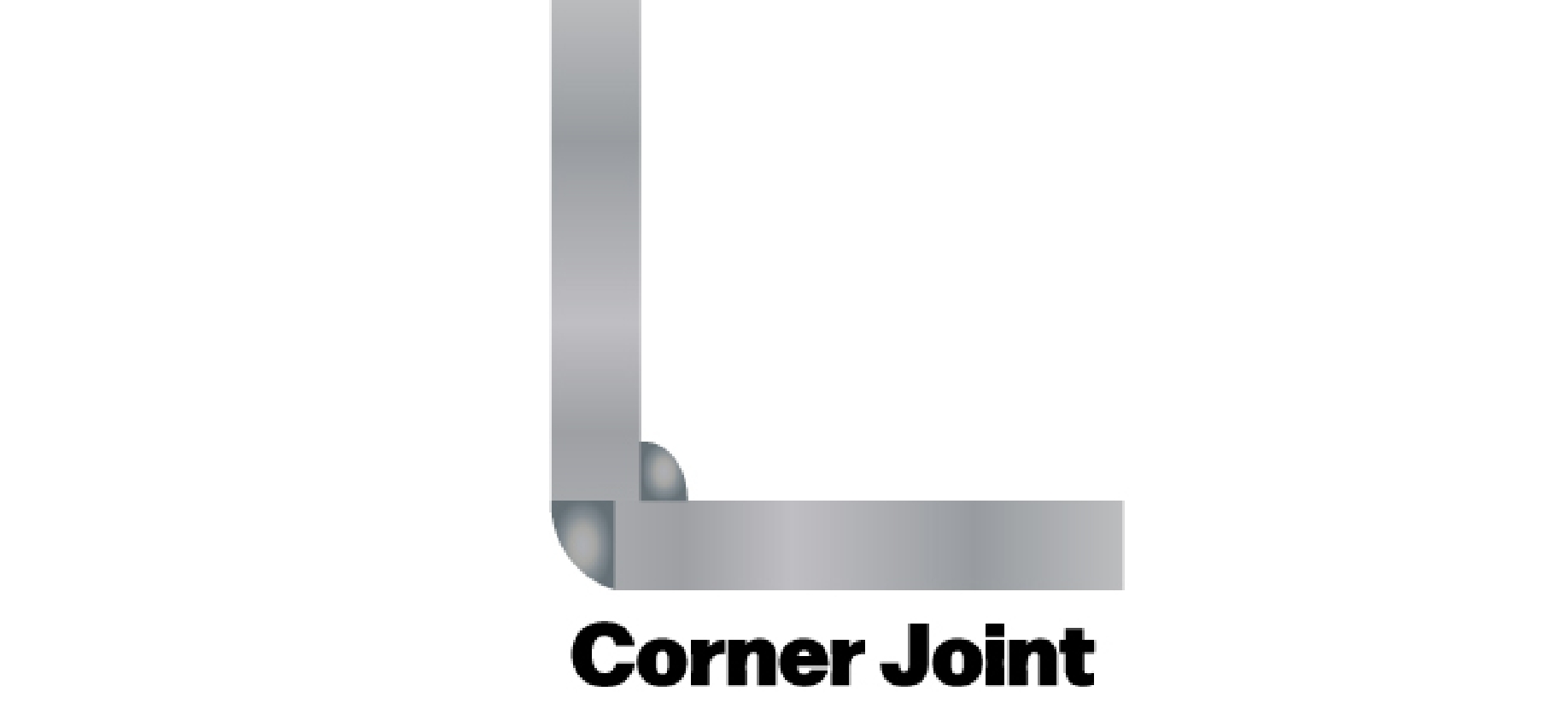
Edge Joints: This joint is created when the materials’ edges are parallel. There are different types, depending on how you prepare the edges, including square grooves, V-grooves, J-grooves, and U-grooves. Welding an edge joint on all four sides can provide extra reinforcement, but this joint type is often reserved for projects in which the weld won’t be subjected to added stress.
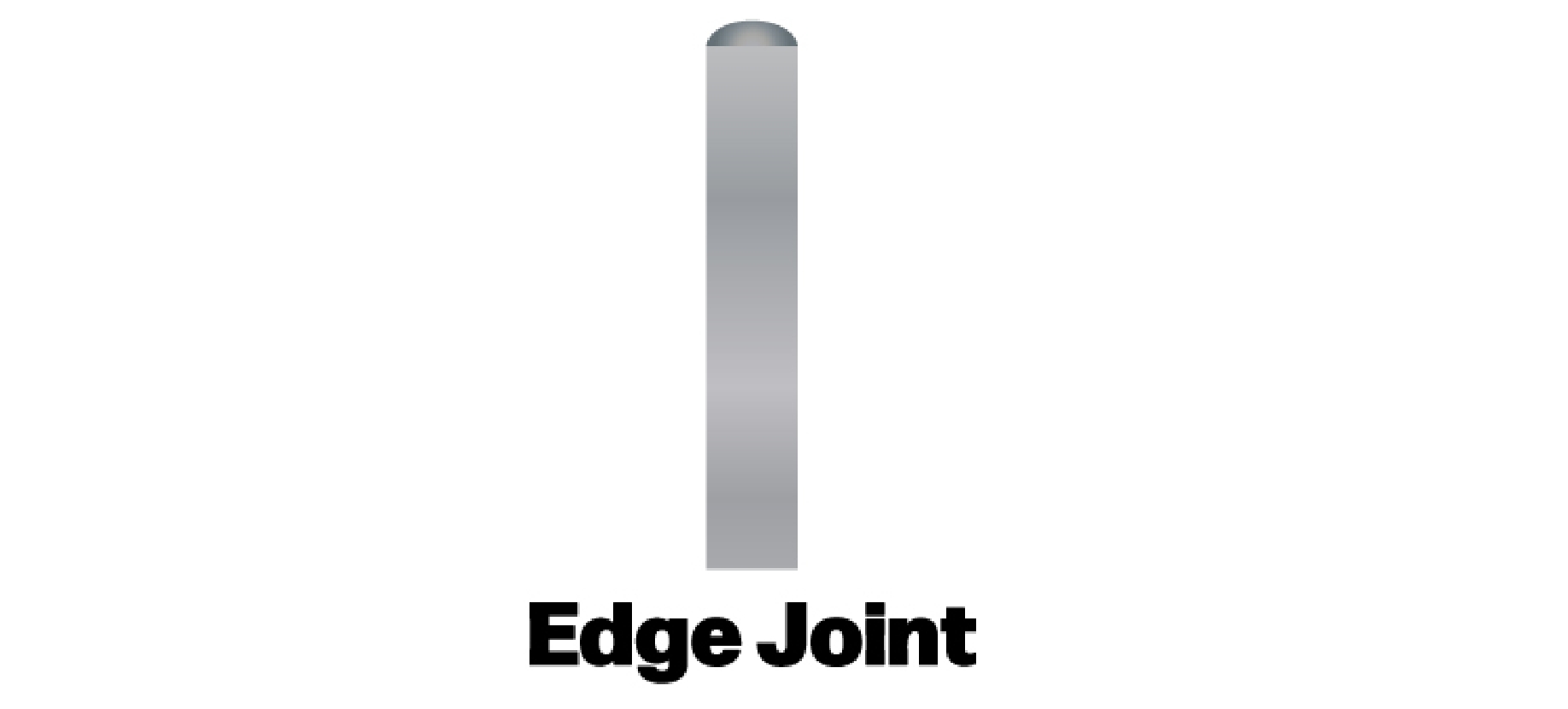
Lap Joints: This joint forms when two pieces overlap, and the weld is deposited in the joint where the two intersect. The amount of overlap is determined by how thick the materials are, with thicker materials requiring more overlap. It’s important to minimize gaps between the materials to ensure flush alignment.
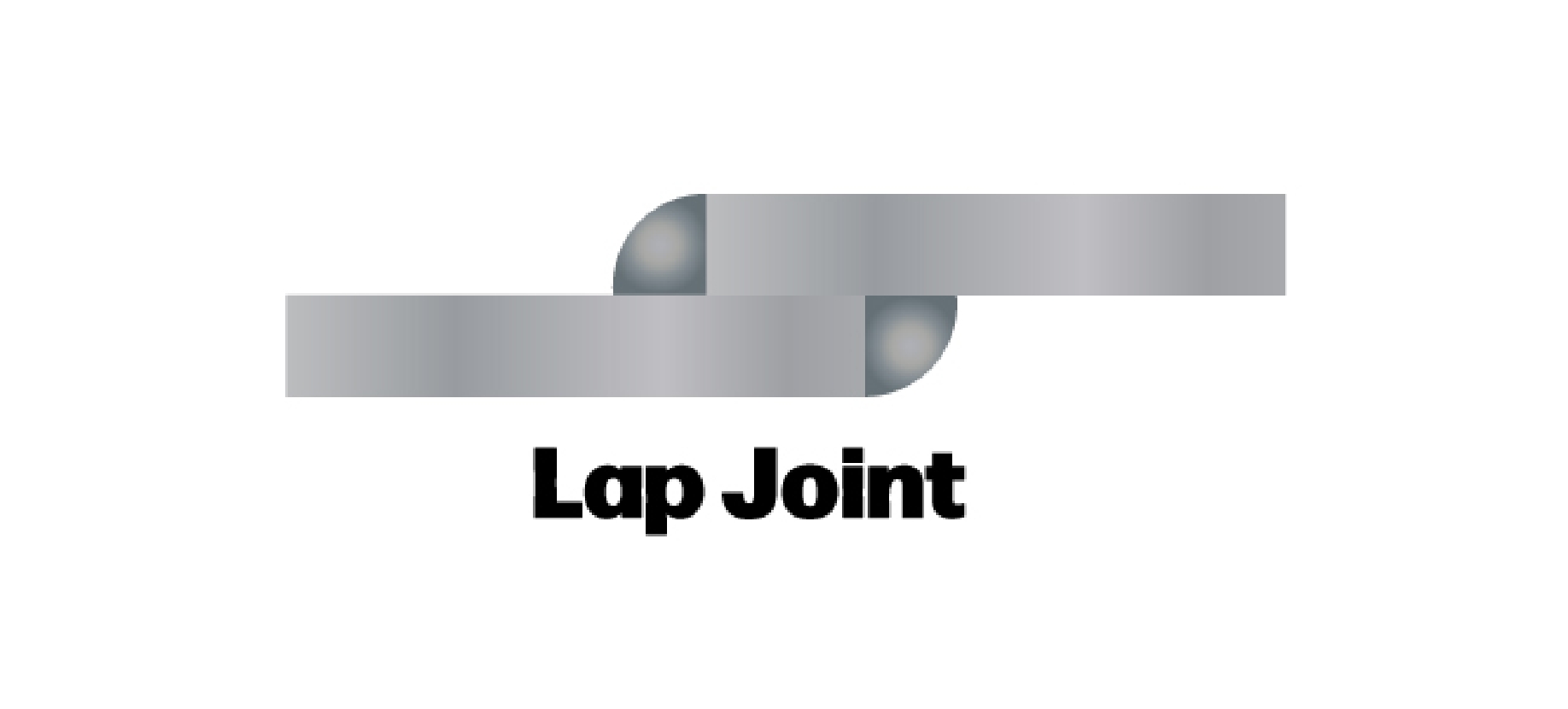
T-Joints: This joint is produced when the edges of two materials meet at approximately 90 degrees, resembling a T shape. When welded from both sides, it offers good mechanical strength. This joint generally requires almost no joint preparation and is often welded using a 45-degree work angle to ensure proper penetration.
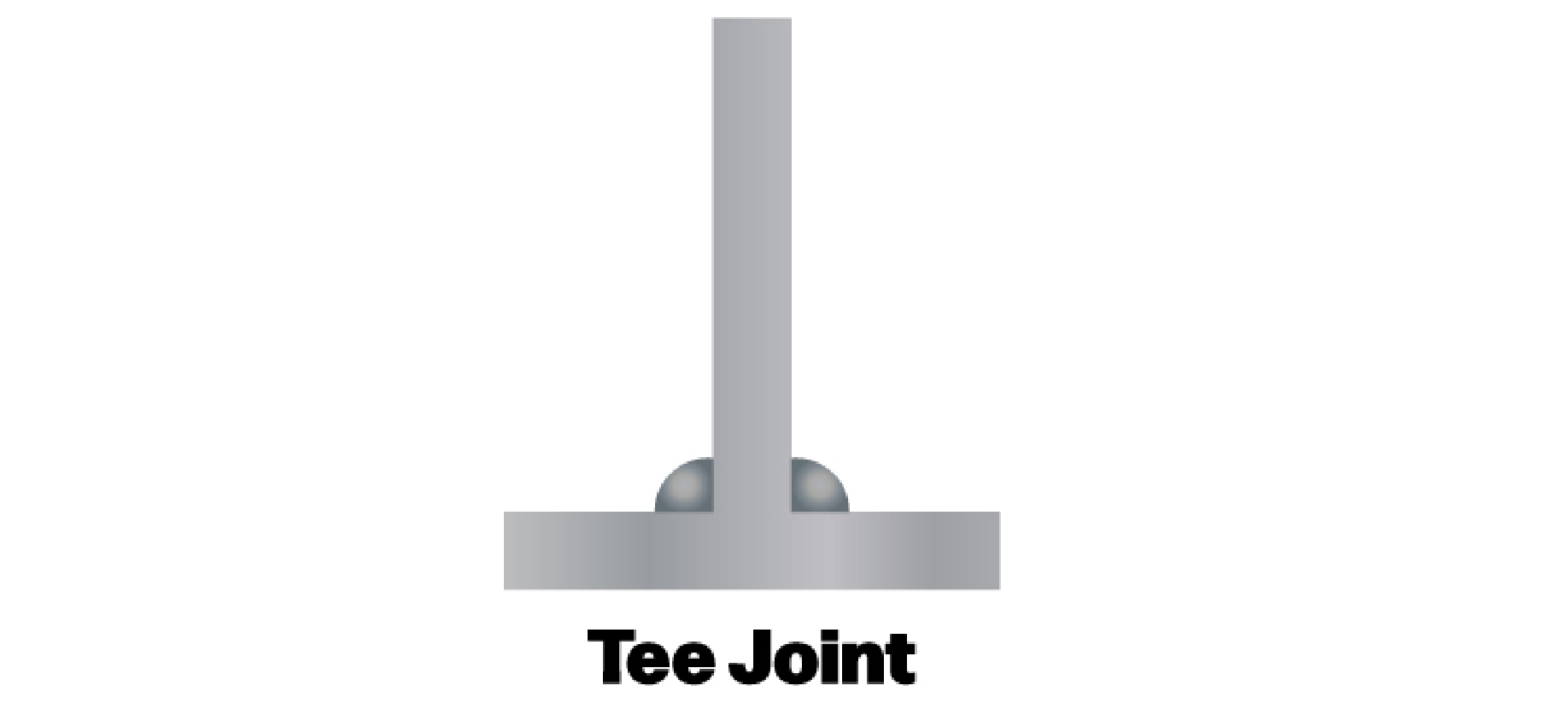
Understanding Metal Transfer Modes
In MIG Welding, metal transfer modes can help determine the overall level of quality of the weld. Each mode has its advantages and limitations, so it’s important to understand which transfer mode should be used for the current project and application. Utilizing the appropriate mode for the project can increase the effectiveness of the welding wire, improving its arc performance, bead appearance, weldability, and more.
It is important to note which welding wire should be used with which metal transfer mode. The choice of which metal transfer mode to use carries its own advantages and disadvantages, depending on the welding operation and parameters.
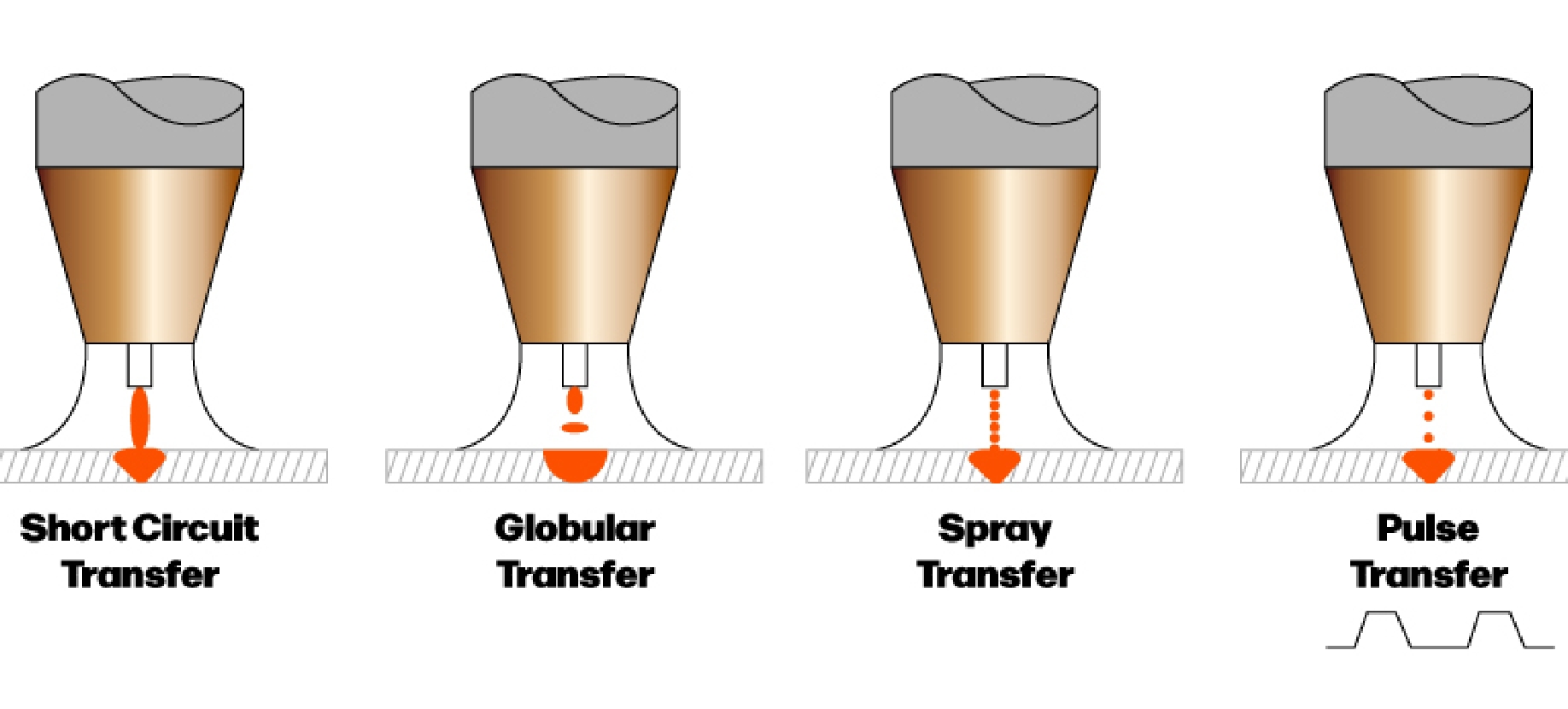
Short-circuit welding: This is the coldest and most commonly used mode that uses the lowest current and voltage ranges. It occurs when the welding wire touches the base material directly, generating a short electrical contact that binds the weld metal to the joint. A versatile method, short-circuit welding can be used in all positions and is most effective when used with smaller diameter welding wires in which it produces a relatively small weld pool that can be easily controlled with adjustments to the welding parameters. However, it generates lower deposition rates and poor fusion and penetration when used on thicker materials or during multi-pass welds.
Globular transfer: This mode requires higher current and voltage levels than short-circuiting, but lower levels compared to spray welding. Large, irregular drops of molten metal transfer across the arc into the weld pool. With the higher welding parameters, this transfer mode helps increase productivity but may result in increased spatter, which will require post-weld cleanup. It is also generally limited to flat position welding with the possibility of creating inconsistent penetration and uneven weld beads.
Spray welding: This easy-to-use mode features increased welding current and voltage for a high deposition rate. A spray of tiny droplets is generated across the arc to the weld pool, which provides better penetration and fusion capabilities and results in good bead appearance. Due to these positive characteristics, this mode is generally used on thicker sheets of materials in flat and horizontal welding positions. It also produces minimal spatter for quicker post-weld cleaning.
Pulsed mode: The lower heat input with this mode means it’s ideal for welding thinner materials. The welding wire is transferred in a controlled droplet form and propelled toward the weld pool while creating almost virtually no spatter. This mode is known for providing excellent arc stability, high deposition rates, and minimal spatter, and, when used with metal-cored welding wires, promotes greater versatility for all-position welding operations.
Step-by-Step Guide: How to MIG Weld Like a Pro
In MIG welding, the wire is fed through the welding gun, creating an electric arc between the wire and the base material. The arc melts the wire, which then generates a weld pool, allowing the welder to manipulate and shape the joint. The shielding gas plays a critical role in preventing atmospheric contaminants, such as oxygen and nitrogen, from interacting with the pool, protecting it to ensure a clean and sound weld. All of these components working together form the foundation of a reliable and strong weld that provides structural integrity and durability. Understanding the role of each component is a fundamental aspect of successful MIG welding projects.
Precision Preparation for MIG Welding
Pre-welding preparation is extremely important if you want to produce a strong and supportive weld with minimal risks of defects. Thoroughly cleaning the base material before welding is an incredibly crucial step. This involves running a wire brush or other abrasive scrubber over the material to eliminate excessive amounts of dirt, mill scale, rust, and other debris. Welding over dirty surfaces can lead to numerous defects, such as porosity and cracking, which can ultimately weaken the overall strength of the weld, jeopardizing the entire project.
Make sure that you are tackling this project with a full understanding of the type, size, and thickness of the metal you are working with, its application, welding position, and any other factors that could influence how you will MIG weld. Knowledge of these factors can contribute to a successful weld.
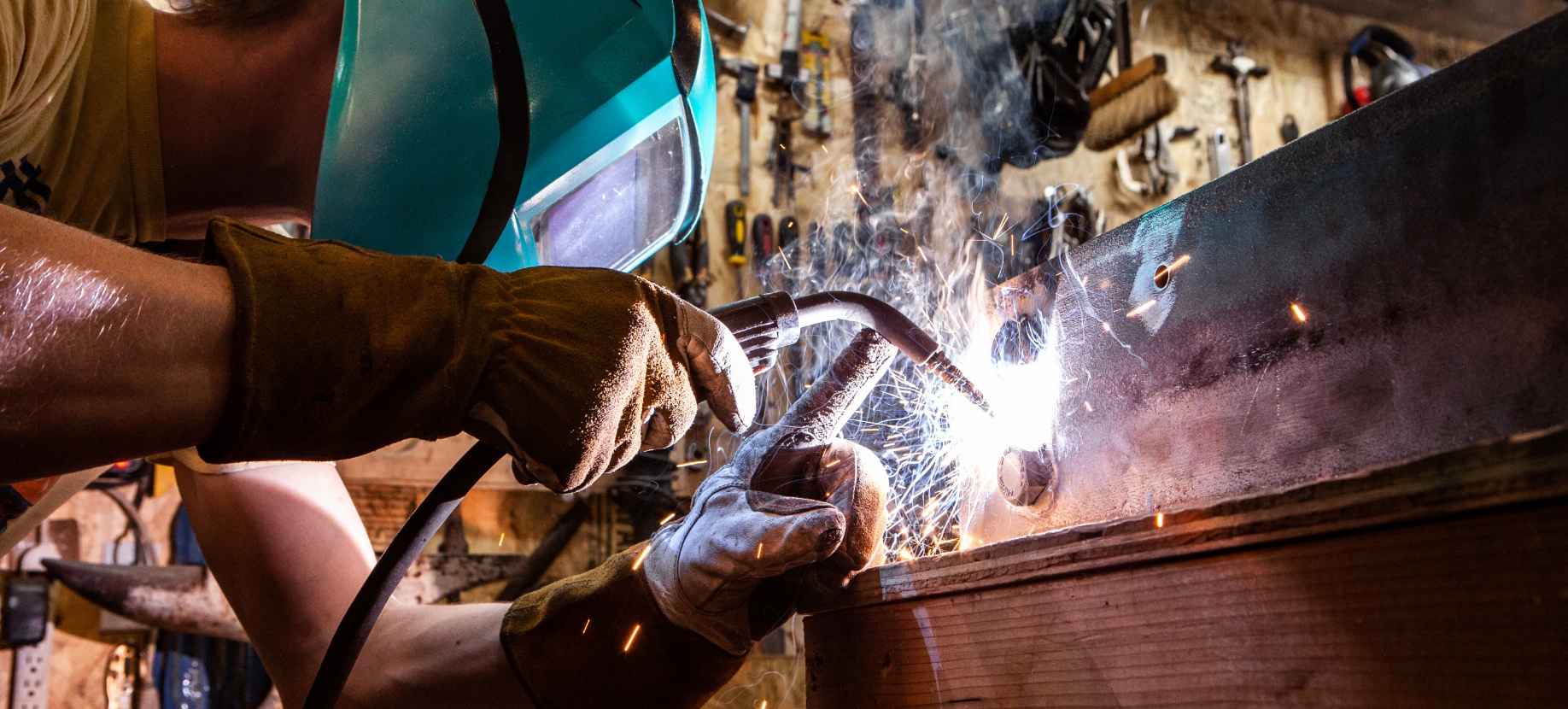
Executing the Perfect MIG Weld
After the initial preparation, which includes cleaning the material, checking all equipment, and putting on your PPE, now you can begin MIG welding. Throughout the entire process, it is incredibly crucial to keep focused. You need to maintain a consistent arc length while keeping an eye on the heat input to help prevent distortion, burn-through, or other welding defects. Be prepared to make any adjustments to the welding parameters as necessary throughout the process.
The joint should be properly prepared by cleaning the edges and ensuring that they are free of any defects. If you’re working with thicker materials, you should consider beveling or other types of edge preparations in order to allow for proper penetration. The joint should align and fit up accurately to ensure consistent welding and minimal distortion. Clamps, fixtures, or jigs can help keep the joint firmly in place.
With everything prepared and in place, begin MIG welding. Maintain a consistent arc length between the filler metal and the material to keep a stable arc with proper heat input. Don’t take your eyes off the job: check the weld pool, heat input, and weld to ensure it is penetrating and adhering to the joint. Keep a steady hand, control the motion of the welding gun, and use weaving (if applicable) to achieve an even bead appearance and fusion.
Post-Weld Steps for Strengthening the Weld
After you’re done MIG welding, you need to perform post-weld inspections. The first step is to use a chipping hammer and/or wire brush to remove any slag and spatter that may have accumulated. Once the area is cleaned thoroughly, you need to inspect the weld for any defects, including cracks, porosity, incomplete fusion, etc. Consider using non-destructive testing, such as X-rays or ultrasonic.
Depending on the type of material you’re working with, you may need to perform post-weld heat treatment to reduce the level of residual stresses in the joint. This is a common practice for MIG welding high-carbon and aluminum materials. The process restores the materials’ toughness and ductility while reducing any increased hardness levels that may have accumulated during the welding process.
What to Know About MIG Welding Aluminum: Care and Precision
MIG welding aluminum can be a difficult process if you’re unfamiliar with the material. A lightweight metal with excellent conductivity and corrosion resistance, aluminum features high thermal conductivity and oxide layer with a higher melting point than the metal itself. This means that it requires special preparation and attention during the MIG welding process.
Composition: Aluminum is primarily composed of metal aluminum and may contain traces of copper, manganese, silicon, or zinc.
MIG Welding Characteristics: This metal is more challenging to weld due to its high thermal conductivity and susceptibility to porosity. Proper joint preparation is crucial as well as thorough cleaning of the surface before welding.
Welding Wire: For aluminum, ER4043 and ER5356 are common welding wire choices with ER4043 being more suitable for general-purpose welding, while ER5356 is ideal for applications requiring higher strength.
Applications: Aluminum is commonly used in manufacturing aerospace and automotive components as well as in applications where weight is critical thanks to its lightweight and high strength-to-weight ratio.
Approach: It’s recommended to use a 10-15-degree push travel angle in which the tip and nozzle are pointed in the direction of travel. The spray transfer mode is the best option, so adjust for aluminum to include higher voltage and wire speed. While welding, maintain a 3/4" wire stick out to keep a stable arc.
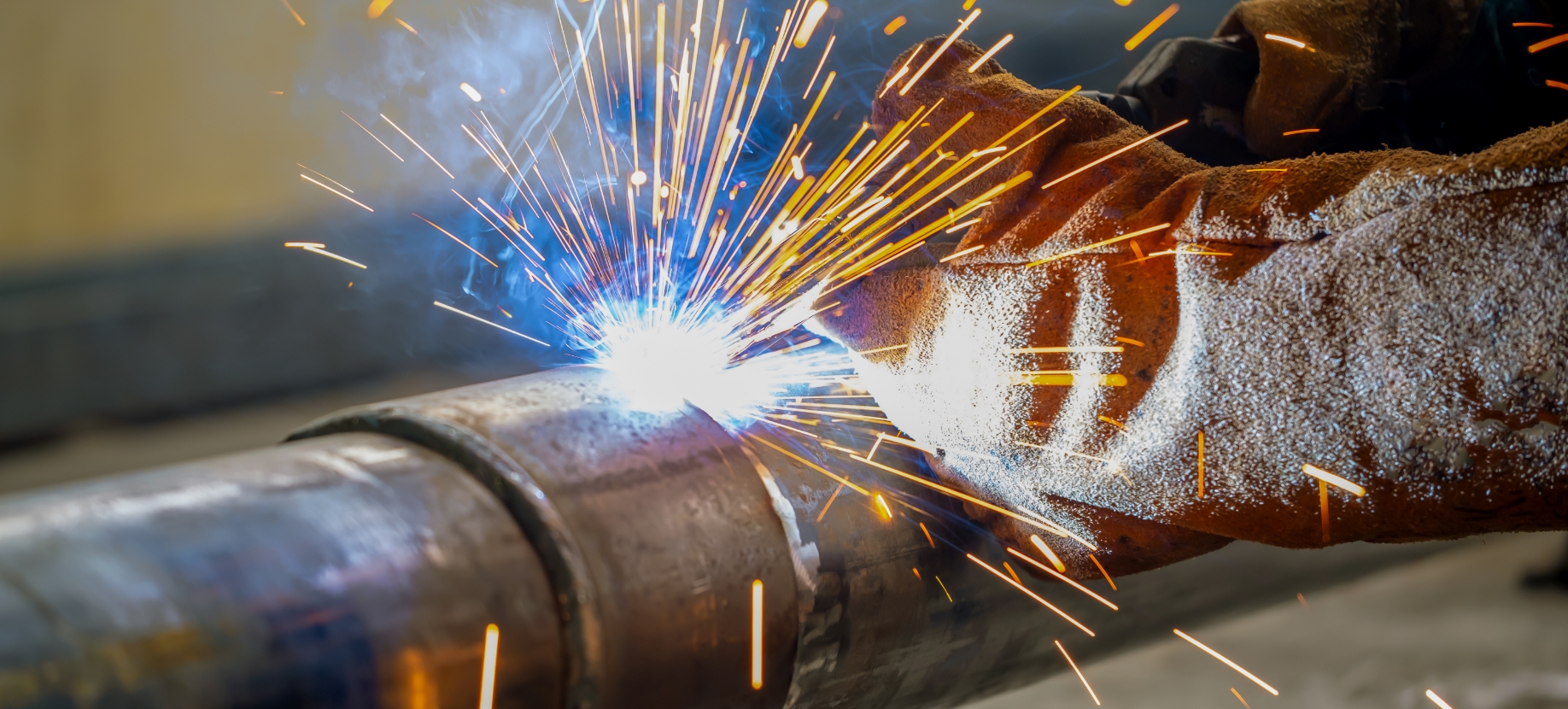
What to Know About MIG Welding Stainless Steel: Compatibility and Control
MIG welding stainless steel demands careful attention and stable control in order to properly produce a reliable weld. A material that is renowned for its corrosion resistance, stainless steel is utilized in various industries that rely on its high tensile strength and good formability. However, MIG welding stainless steel can prove to be a more difficult endeavor compared to welding carbon steel, so it requires careful consideration over the right equipment and welding parameters.
Composition: Stainless steel is primarily composed of chromium, nickel, and other alloying elements for corrosion resistance and comes in five distinct types: austenitic, ferritic, martensitic, duplex, and precipitation hardening.
MIG Welding Characteristics: Stainless steel can be more challenging to MIG weld due to its higher alloy content and potential for heat distortion. Special precautions need to be made regarding the heat input to prevent burn-through. The edges need to be beveled to ensure good penetration, and the surface area needs to be freed of any contaminants.
Welding Wire: The best welding wire for stainless steel depends on the specific grade you’re working with; the wire’s composition needs to match the composition of the base material. For example, when welding austenitic stainless steels, the wire needs a higher nickel content to produce the best results, such as with the ER308L. Other examples include the ER309L for welding dissimilar metals, the ER316L for welding molybdenum-bearing austenitic stainless steels, and the ER2209 for welding duplex stainless steels.
Applications: This material is often used in applications requiring corrosion resistance, including kitchen equipment, automotive exhaust systems, pipelining, and shipbuilding.
Approach: It's recommended to adjust your welding parameters to account for higher thermal conductivity. Welders can usually use spray, short-circuit, or pulsed transfer modes, depending on the type of stainless steel and its application. For shielding gases, some common choices include 98% argon/2% carbon dioxide or a tri-mix of 85-90% helium/10% argon/2.5% carbon dioxide. The travel speed is determined by the size and thickness of the material, but the typical travel angle is about 5-15 degrees using the push method.
What to Know About MIG Welding Carbon Steel: Versatility and Consistency
Carbon steel is the cornerstone of construction, manufacturing, and metalworking due to its strength and versatility. MIG welding carbon steel works to establish sturdy and reliable welds when joining carbon steel components together. With the right equipment and knowledge, working with carbon steel can become incredibly easy and straightforward.
Composition: A common material used for various industries, carbon steel is primarily composed of iron and carbon with small amounts of other elements. It can be divided into three types that are determined by the amount of carbon in each of them: mild steel, medium carbon steel, and high carbon steel.
MIG Welding Characteristics: Carbon steel is one of the easiest materials to work with due to its lower alloy content, versatility, ductility, and affordability. A welder needs to maintain a consistent and appropriately sized weld pool in order to achieve complete fusion.
Welding Wire: Carbon steel welding wires that are best for MIG welding include ER70S-6 and ER70S-3. The ER70S-6 carbon steel welding wire is one of the most commonly used solid filler metals that provides good bead appearance and arc stability. The ER70S-3 also provides improved arc stability with enhanced ductility and offers minimal impact on the base metal’s mechanical properties.
Applications: As one of the most common materials used in industries, MIG welding carbon steel can be found in structural applications, automotive components, pipelines, and general fabrication.
Approach: For MIG welding, it’s important to maintain a welding angle of about 10-15 degrees from perpendicular to the workpiece with a travel angle of about 5-15 degrees. A welder can also use all four MIG welder transfer types, including short circuit, globular, spray, and pulse transfer, depending on the size and thickness of the carbon steel. Make sure to maintain a consistent travel speed to prevent excessive heat input or insufficient fusion.
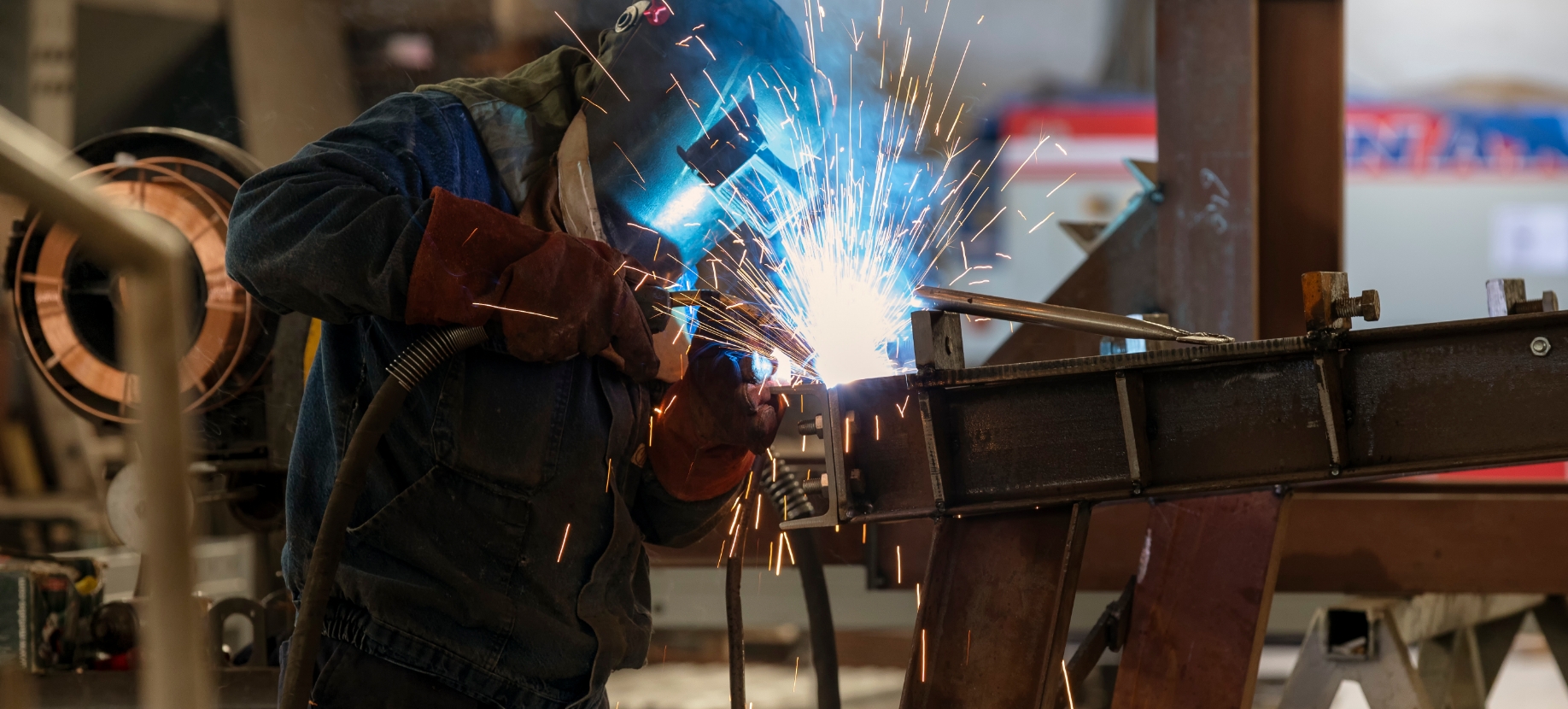
Common MIG Welding Questions (FAQs)
Like with any welding technique, there’s bound to be inquiries and uncertainties that you encounter, especially for those who are new to the craft. Let’s take a look at some of the most commonly asked questions regarding MIG welding:
Is MIG welding easy?
MIG welding is commonly regarded as one of the easiest welding processes to learn and eventually master among the welding community. Suitable for beginners, its versatility and simplicity in set up and technique allow a new welder to grasp the basics of welding fairly quickly. It offers continuous wire feed and automatic arc length adjustment and can be used on a variety of materials of different thicknesses. MIG welding is the perfect chance for new welders to get a grasp on proper welding technique, joint preparation, welding position and posture, and welding parameters required to achieve the ideal weld.
Can MIG welding be used for thin materials?
Although it can be a challenge, MIG welding can be used for working on thin materials. When welding, the welder needs to pay close attention to prevent excessive heat input that could result in warping, burn-through, and other welding defects. One technique for welding thin materials is to use short pulses in second intervals to allow the material to cool down before hitting it with the arc again. Care, control, and practice can help make this process less of a challenge.
Can you MIG weld dissimilar materials?
MIG welding is a very versatile process that can be used to weld dissimilar materials together. The key to successfully welding the different materials lies in the type of welding wire used in the process. The welding wire should be metallurgically compatible with both base metals in order to reduce the risk of cracking and other defects that could weaken the weld. The welder also needs to pay close attention to each metal’s melting points, which will influence the heat input required for the weld.
The welder should have a clear understanding of the chemical composition and physical properties of each metal they’re working with, which will help determine the best welding wire to use. Some metals are more incompatible than others, such as aluminum and stainless steel, so extra precautions need to be taken before MIG welding. Please check out our article on how to weld carbon steel to stainless steel for a more in-depth look at the subject.
What is the difference between MIG and TIG?
MIG welding and TIG (Tungsten Inert Gas) welding are two very distinct welding processes that both use an electric arc and shielding gas to create a strong weld. Each comes with their own advantages, disadvantages, applications, techniques, and, most importantly, welding electrodes used to generate the arc. Check out our article that explores the differences between MIG, TIG, and stick welding in detail.
For MIG welding, the arc is created by continuously feeding a welding consumable as the filler metal and using a shielding gas to protect the weld. The process is generally regarded as easier to work with than TIG welding due to its efficiency and versatility. For TIG welding, the arc is produced using a non-consumable tungsten electrode and filler material is manually fed into the weld pool. Known for being a bit more difficult to master than MIG welding, this process requires greater control and precision and is best used for projects that require intricate details.
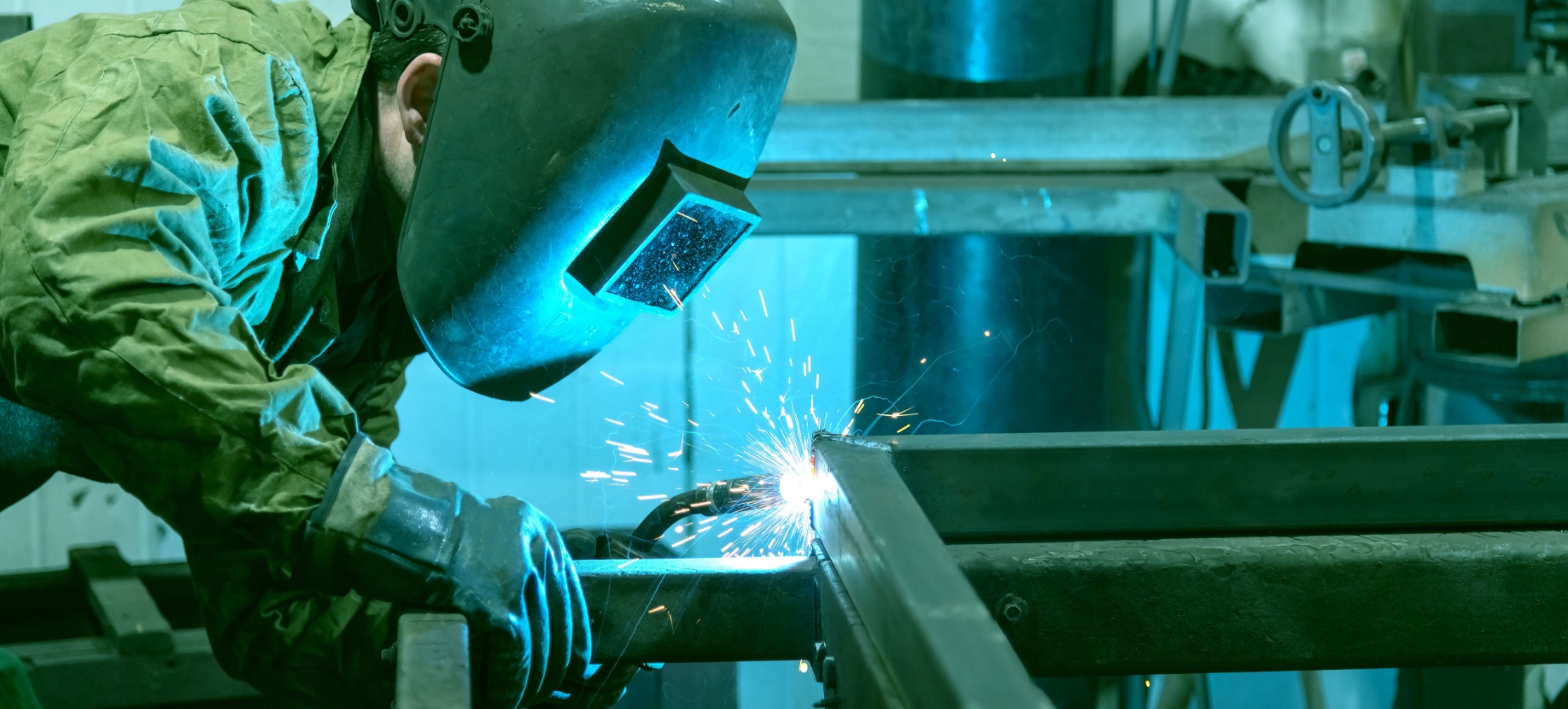
Can you MIG weld with flux-cored welding wire?
Yes, you can MIG weld using flux-cored welding wire. It’s very simple to use a flux-cored welding wire with your MIG welder, especially if you are using a self-shielded wire. This type utilizes the flux-cored electrode to provide gas protection over the weld pool. It works to contain the slag forming fluxing agents that produce shielding gases once exposed to the arc’s heat. It’ll quickly solidify the weld and prevent certain defects, like cracking. Among the many advantages of self-shielded flux-cored welding wires, this type allows for outdoor welding since there’s no shielding gas for the wind to blow away.
NS ARC High-Quality Welding Wires
In order to achieve the ideal weld that supports the integrity of the project, many welders opt to choose a trustworthy MIG welding wire that has the characteristics required for the job, such as NS ARC welding wires. As the ultimate choice for industrial and commercial MIG welding operations, NS ARC welding wires excel in promoting high-quality welding strength and reliable bonding capabilities.
Copper-Glide™, our line of copper-coated welding wires, is the choice for applications that require excellent arc stability and superior penetration. It’s generally used in automotive manufacturing, general fabrication, and pressure vessel welding operations, just to name a few.
On the other hand, our Silver-Glide™ CopperFree™ line of welding wires is engineered to produce superior welding arcs while offering smooth wire feeding for greater productivity. Typically, this type of welding wire can be used in agricultural equipment manufacturing and pipe welding applications.
When working with aluminum, our Alumi Glide® is a highly ductile choice with a higher strength-to-weight ratio. It’s very beneficial in heavy equipment, trailer, and railcar manufacturing, establishing a solid bond between metals for a more stabilized product.
Our Satin Glide® line of welding wires is engineered by our experts to promote superior versatility and durability with improved weld strength and high temperature resistance. Its natural resistance to corrosion makes it the best choice for shipbuilding and pressure vessel applications.
Contact us today, and our team of highly trained experts in welding can assist with your next welding project. We’ll guide you through our selection of welding wires to ensure that you’re working with the best product for your welding project.
Explore our selection of high-quality welding wire to arm yourself with the best tools for your next MIG welding operation!
DISCLAIMER: This information is descriptive in nature and not purely prescriptive. Refer to your own welding machine’s user manual for proper settings and consult a welding expert for support.