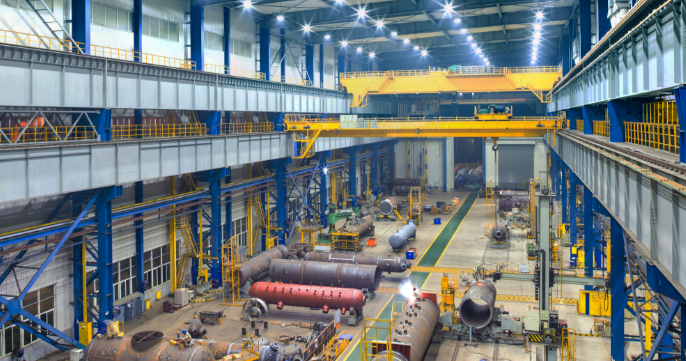
Weld managers and operational leaders in industrial manufacturing applications turn to welding wire suppliers like NS ARC to get the job done and to help eliminate production challenges. NS ARC helps its customer’s operational challenges like production line inefficiencies, project rework, excessive cleanup, prolonged downtime, irregular feedability, and limited welding filler material availability.
By employing a welding wire that has exceptional feedability, unwavering consistency, and superior weld quality, NS ARC welding wire is the key to tackling obstacles. Our quality wire will not only enhance uptime and productivity but will also ensure consistent operational success.
Welding wire is a vital and versatile material that brings advantages to various applications. The specific application of the wire depends on the type of metal being welded, the welding process being used, and the project’s specific needs. NS ARC carries a wide variety of wire tailored to customers' specifications, allowing them to find the type of wire best suited for their welding application.
NS ARC Welding Wire for Manufacturing & Fabrication
Our high-quality welding wires are designed to provide superior performance and reliability, and we offer a wide range of products to meet the diverse requirements of our customers. Our welding wires are made from high-quality materials.
NS ARC welding wires are manufactured to meet or exceed the specifications of the AWS (American Welding Society) and/or the CWB (Canadian Welding Bureau) by using advanced technology and processes to ensure consistent quality and performance. We offer a range of welding wire options, including carbon steel, stainless-steel, aluminum, and other alloys, as well as various diameters and packaging options.
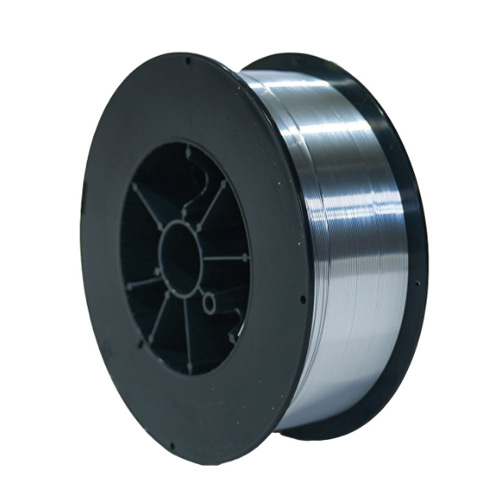
Aluminum Welding Wire Applications
Aluminum welding wire is excellent for working with lightweight structures, and its high strength-to-weight ratio and corrosion resistance make it ideal for a variety of applications, including:
- Manufacturing and repairing trucks, trailers, automotive parts and equipment, boats, ships, and pressure vessels
- Non-heat treatable weldments
- Welding 6XXX series alloys and most aluminum cast alloys (mold repair)
- Welding 5XXX/6XXX series with less than 2.5% magnesium
- Applications where weldments are subject to elevated temperatures such as above 150°F
Stainless-Steel Welding Wire Applications
Stainless-steel welding wire offers high strength and durability with high-temperature resistance, making it the right choice for handling heavy-duty applications that demand superior quality, including:
- Spray-arc, short-circuiting, or pulsed-arc transfer welding
- Automatic, semi-automatic, mechanized, or manual welding
- Single- to multi-pass weld applications
- Dissimilar base metal welding
- All metal transfer modes of GMAW
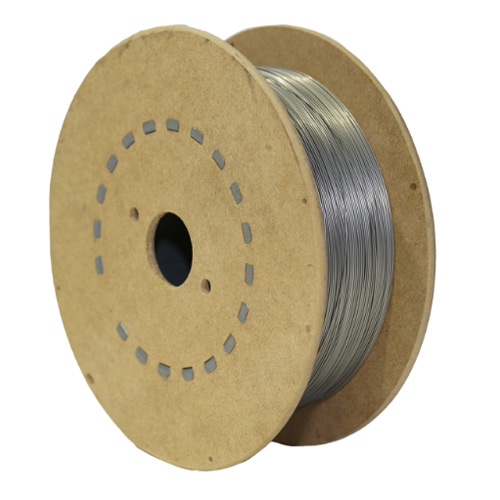
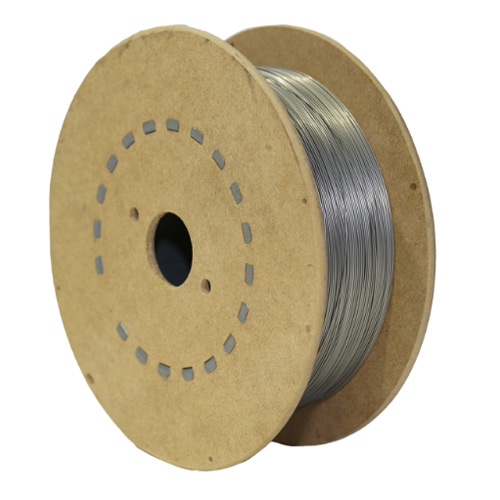
Stainless-Steel Welding Wire Applications
Stainless-steel welding wire offers high-strength and durability with high-temperature resistance, making it the right choice for handling heavy-duty applications that demand superior quality, including:
- Spray-arc, short-circuiting, or pulsed-arc transfer welding
- Automatic, semi-automatic, mechanized, or manual welding
- Single- to multi-pass weld applications
- Dissimilar base metal welding
- All metal transfer modes of GMAW
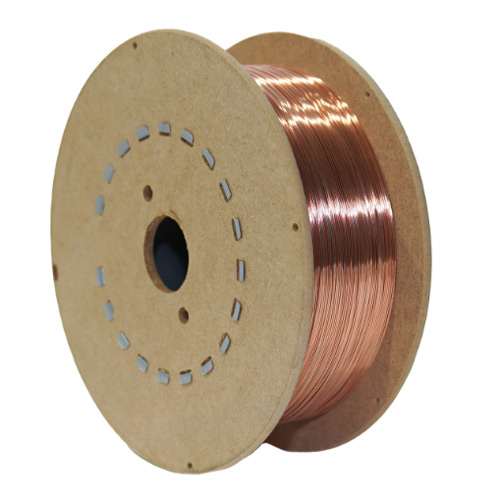
Carbon Steel Welding Wire Applications
NS ARC offers carbon steel welding wire in two versions: copper-free and copper-coated, providing optimized flexibility to support GMAW welding operations along with other applications, including:
- All metal transfer modes of GMAW
- Robotic, mechanized, or semi-automatic welding
- General purpose, clean surfaces
- Low carbon killed and semi-killed steel
- Automatic or semi-automatic welding
- Short circuit, globular, axial spray, spray transfer, and pulse welding
- Single arc weld applications
- Light, moderate, and heavy mill scale, rust, or oil steel
- Single to multi-pass weld applications
- Pipe welding, structural steel, rimmed steel, and steel buildings
Flux-Cored Welding Wire Applications
Thanks to its superior efficiency, weld quality, and versatility, flux-cored welding wire can be utilized in several applications. These benefits include:
- Work on earthmoving equipment, machine tool bases, structural steel, heavy equipment, railcar construction, mining machinery, power generation equipment, offshore oil structures, subsea components of oil and gas systems, shipbuilding, and general fabrication
- Welding most carbon steels and certain low alloy steels
- Welding gauges varying from 10-gauge sheet metal to heavy plate sections, where “all position” welding capability, stable arc characteristics, and excellent mechanical properties are needed
- Applications with any combination of all position welding, good welder appeal, a minimum tensile strength of 80 KSI, and good CVN values at lower temperatures
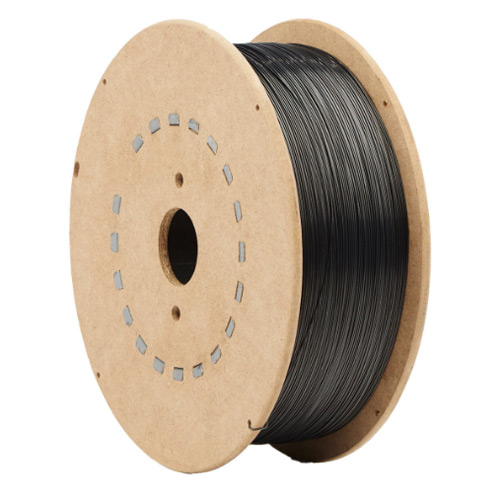
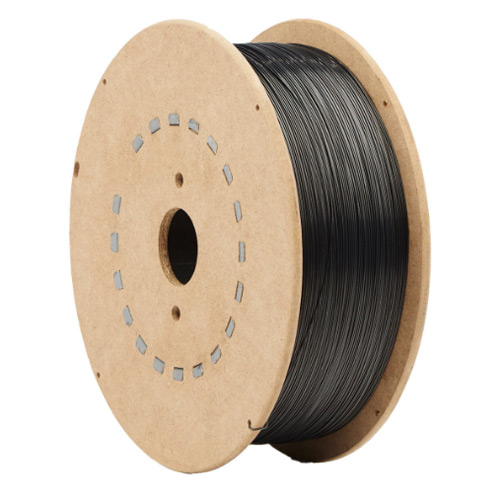
Flux-Cored Welding Wire Applications
Thanks to its superior efficiency, weld quality, and versatility, flux-cored welding wire can be utilized in several applications. These benefits include:
- Work on earthmoving equipment, machine tool bases, structural steel, heavy equipment, railcar construction, mining machinery, power generation equipment, offshore oil structures, subsea components of oil and gas systems, shipbuilding, and general fabrication
- Welding most carbon steels and certain low alloy steels
- Welding gauges varying from 10-gauge sheet metal to heavy plate sections, where “all position” welding capability, stable arc characteristics, and excellent mechanical properties are needed
- Applications with any combination of all position welding, good welder appeal, a minimum tensile strength of 80 KSI, and good CVN values at lower temperatures
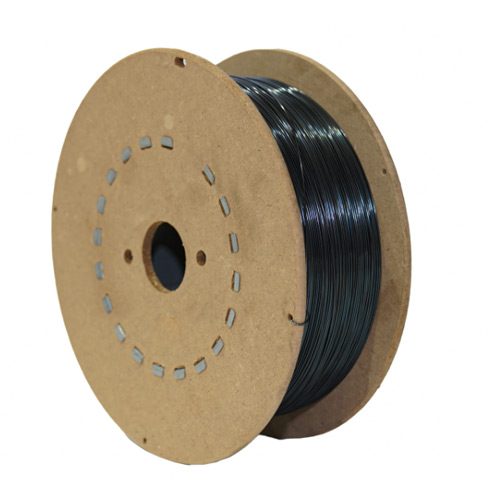
Metal-Cored Welding Wire Applications
Weld shop managers can use metal-cored welding wire to improve quality, control, and efficiency in their operations that include:
- Work on water heaters, shipbuilding, structural steel, power transmission poles, mining machinery, construction equipment, agricultural equipment, railcar construction, and truck frames
- Work on pressure vessels, pressure piping systems, and crane frames and components
- Most carbon steels and certain low alloy steels
- Gauges ranging from heavier sheet metal to thick plate
- Automatic, semi-automatic, mechanized, or manual welding
NS ARC Pit Crew & ARC Assessment
The NS ARC Pit Crew is a dedicated team of welding specialists available to redefine your operation. Beyond providing exceptional welding wires, the Pit Crew offers tailored support, expertise, and resources to optimize your welding procedures. Comprising industry veterans, the Pit Crew is committed to enhancing operational efficiency and driving your enterprise to success. With this in mind, we introduce the ARC Assessment – a comprehensive service designed to revolutionize your welding facility.
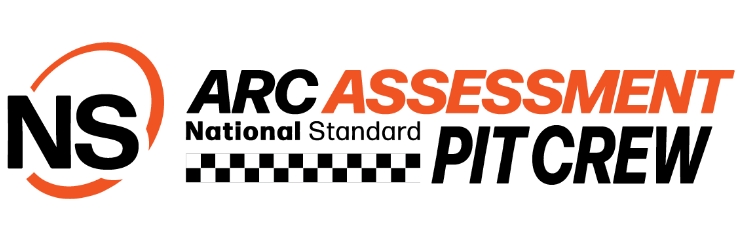
Our seasoned specialists conduct an in-depth on-site examination, dissecting every facet of your operations against a specific list of criteria. This evaluation results in a sensible strategy meticulously designed to address areas requiring improvement, positioning your business for peak performance and unparalleled success.