How to Choose Welding Wire for Carbon Steel
Oct 20th 2023
Welding carbon steel takes a fair amount of skill, but skill doesn’t mean much if you’re not welding with the right equipment. When it comes to welding carbon steel, selecting the appropriate welding wire is essential for achieving strong, dependable welds. There are several factors to consider when choosing the right welding wire for carbon steel among the many different types that exist, so let’s explore them in detail.
Understanding Carbon Steel
Carbon steel is a versatile material widely used in construction, manufacturing, and various industrial applications due to its strength and affordability. It consists primarily of iron and carbon, but it may also contain small amounts of other alloying elements like manganese, silicon, and sulfur. There are three types of carbon steel that are commonly welded in various industries: low carbon steel, medium carbon steel, and high carbon steel.
Low carbon steel, or mild steel, is commonly used for fabrication and construction due to its formability and affordability. It is easily weldable and offers good ductility. It features relatively low hardness so it’s less susceptible to cracking and excellent toughness but has limited strength.
Medium carbon steel offers more strength and hardness compared to low carbon steel, so it’s utilized in the fabrication of pressure vessels, structures, and other applications that require higher mechanical properties. Although it offers increased wear resistance and durability, it has reduced ductility and increased risk of cracking.
High carbon steel is one of the strongest types of carbon steel that is often used for the manufacturing of high-strength appliances and equipment. It features excellent hardness and wear resistance but offers limited ductility and toughness, making it more prone to cracking.
Understanding AWS Welding Wire Designations
Every official welding wire designation follows the American Welding Society’s (AWS) uniform specifications. Each letter and number indicate a very specific detail that helps determine the chemical and mechanical properties of the filler metal. Let’s take one of the most common solid welding wires, ER70S-6, and break it down.
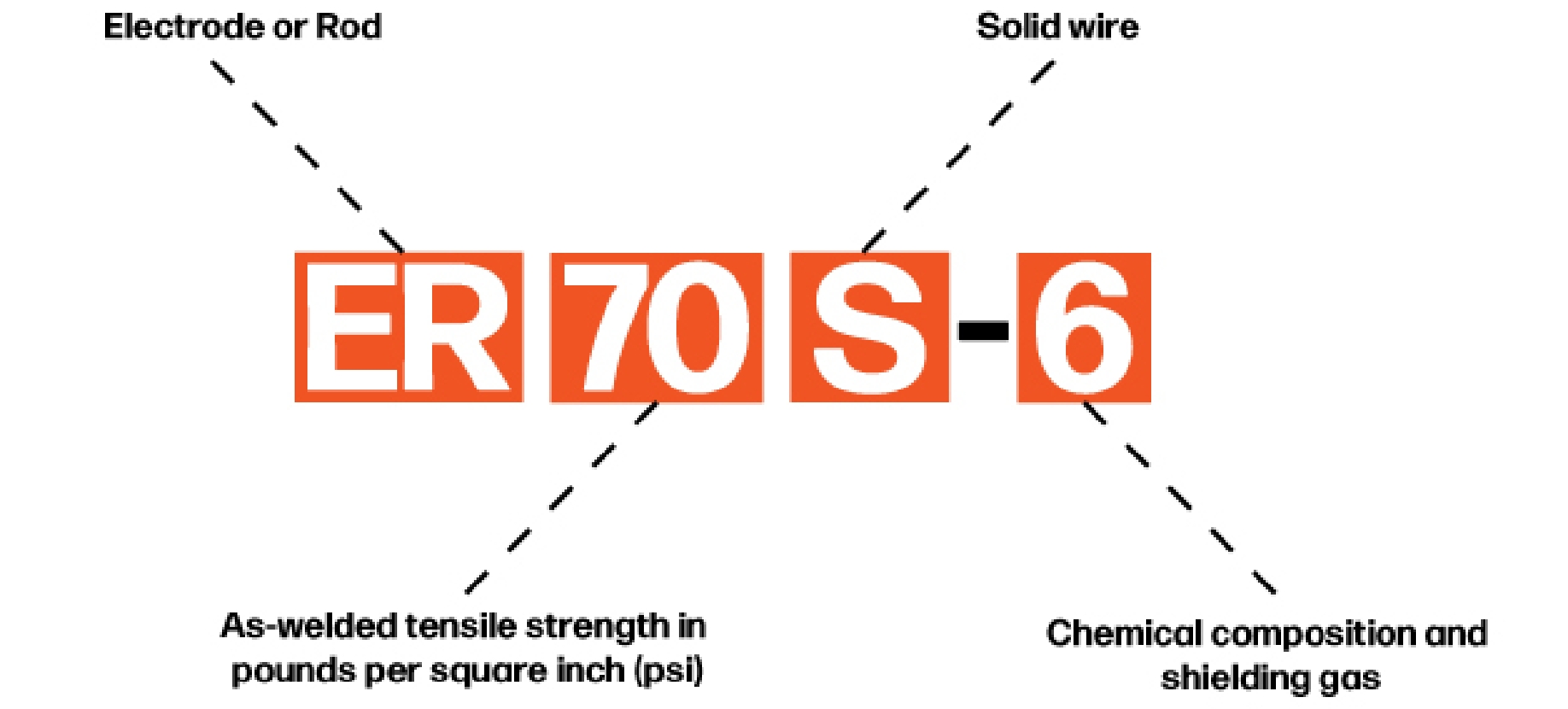
ER = electrode or rod – this means that the filler metal can be used in electrode or rod form (in which case, it can be cut into lengths for GTAW)
70 = 70,000psi – this is the as-welded tensile strength in pounds per square inch
S = solid wire – this is not a tubular electrode
6 = chemical composition – this reflects that is contains more manganese and silicon than classifications with a smaller number, such as ER70@-3
Both gas-shielded and self-shielded flux-cored welding wire also have their own designations to determine their properties at a glance. For an example, let’s break down the E71T-1C-H8 gas-shielded flux-cored welding wire, which is typically used for heavy fabrication and shipbuilding applications.
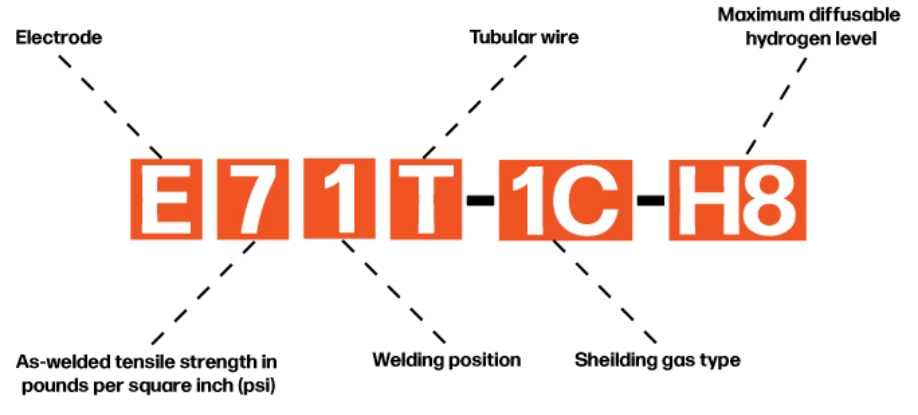
E = electrode – flux-cored wires can only be used as electrodes
70 = 70,000psi – this is the as-welded tensile strength in pounds per square inch
1 = welding position – 0 indicates flat or horizontal positions only, whereas 1 indicates all positions
T = tubular wire – this is not a solid electrode
1 = usability designator – 1-14 or “G” (or “GS”) refers to the usability of the electrode with requirements for polarity and general operating characteristics. “G” indicates that the polarity, shielding gas (if any), and general operating characteristics are not specified. “GS” indicates that the electrode is suitable only for single-pass welding.
C = shielding gas type – “C” indicates 100% CO 2, whereas “M” indicates a blend (typically 75% Argon/25% CO2)
H8 = maximum diffusible hydrogen level – this one represents 8 ml/100 grams of weld metal
Understanding these designations can help you determine exactly which type of welding wire is the right match for your next welding project. Memorizing the codes and their meanings can help you determine and grab the right welding wire needed for the project at just a glance at the designation.
Factors to Consider When Choosing Welding Wire
- Carbon Steel Grade: Determine the grade or type of carbon steel you'll be welding. Low, medium, and high carbon steel each have their specifications and requirements. Common grades include A36, A572, and A516, among others. The specific grade will influence the choice of welding wire.
- Wire Type: Welding wires come in various forms, including solid wires and flux-cored wires. Consider the welding process you'll be using (e.g., MIG, TIG, or FCAW) and the specific requirements of your project when selecting wire type.
- Material Thickness: The thickness of the carbon steel you're welding plays a role in welding wire selection. Thinner materials may require smaller-diameter wires, while thicker sections might benefit from larger-diameter wires.
- Joint Configuration: The joint design and geometry are important. Bevels, grooves, or gaps in the joint may require specific welding wire types or sizes for proper penetration and fusion.
- Welding Position: Different welding positions (e.g., flat, horizontal, vertical, overhead) may require different welding wire types to ensure proper bead placement and control.
Common Welding Wire Options for Carbon Steel
Carbon steel is a versatile material, so it's compatible with a number of different types of welding wires. The choice of which one is the best depends on the job, so it's important to be fully informed about each of your options before making that choice. If you want extra details on what's the difference between copper-coated and copper-free welding wires, check out our other post! If you want a more in-depth look at flux-cored welding wires, check out What's the Best Flux-Cored Welding Wire for Carbon Steel.
- ER70S-6 (Solid Copper-Coated Welding Wire): This is the most commonly used solid wire for welding carbon steel. It's a mild steel wire with a balanced composition of silicon and manganese, providing good arc stability, minimal spatter, and smooth welding performance. It works well for a wide range of carbon steel applications, including general fabrication, automotive, construction, and structural welding projects.
- ER70S-3 (Solid Copper-Coated Welding Wire): Similar to ER70S-6 but with slightly lower levels of silicon and manganese, making it suitable for applications where lower silicon content is preferred, such as welding thin materials or when silicon levels may affect the final weld properties.
- ER70S-G (Solid Copper-Free Welding Wire): For applications where copper contamination is a concern, ER70S-G is a solid wire that offers good welding performance without the presence of copper. It maintains good weldability while eliminating the risk of copper contamination, and it also ensures the integrity of the weld in sensitive environments.
- E71T-1 (Flux-Cored Welding Wire): This is a popular choice for Flux-Cored Arc Welding (FCAW) of carbon steel. It's known for high deposition rates and good penetration, and it performs well in various positions. It's commonly used in heavy fabrication, structural welding, shipbuilding, and other applications where high welding speeds and high productivity are required.
- E70T-1 (Flux-Cored Welding Wire): Suitable for heavy-duty applications, E70T-1 offers excellent mechanical properties and impact resistance. It's often used for demanding welding scenarios in structural and heavy fabrication work. It delivers exceptional strength and impact resistance in the finished welds and is ideal for projects where the welds will undergo significant stress or loading.
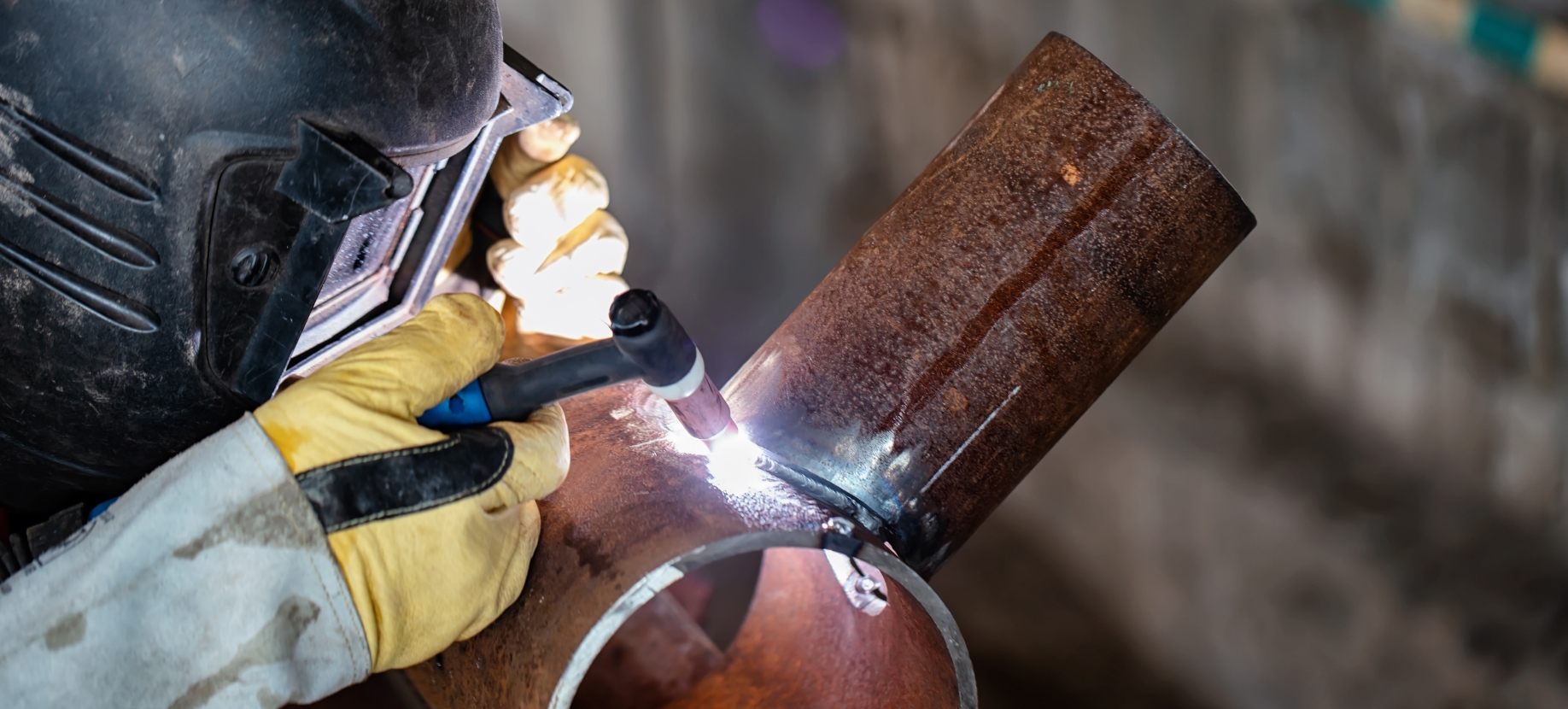
Choosing the Right Diameter
A welding wire’s diameter plays a crucial role in the welding process. The diameter of the welding wire should be selected based on the material thickness and the welding machine's capabilities. Smaller-diameter wires are typically used for thinner materials or for more complex joints and welding positions, while larger-diameter wires are better suited for thicker sections or for simpler joints and welding positions.
Consult Manufacturer Guidelines
Always consult the manufacturer's recommendations and welding procedures for the specific wire you plan to use. They provide valuable information on the welding wire's suitability for various applications and welding parameters.
NS ARC Quality Carbon Steel Welding Wire
Choosing the right welding wire is a critical step in ensuring successful carbon steel welding. Consider factors like the carbon steel grade, wire type, material thickness, joint configuration, and welding position to make an informed choice. By selecting the appropriate welding wire and following proper welding procedures, you can achieve strong, reliable welds in your carbon steel projects.
We recommend that you browse our selection of carbon steel welding wire that is engineered to promote excellent feedability, consistency, and welding strength. Our Copper-Glide™ copper-coated welding wire provides improved electrical conductivity, corrosion resistance, and smooth wire feeding. For situations where copper contamination is a concern, we also have our line of Silver-Glide™ CopperFree™ welding wire is a reliable alternative as it offers great weld quality, promotes health and safety of the welder, and is excellent for environmental considerations. Contact the Pit Crew today so that our team of industry experts can guide you through selecting the ideal welding wire solution that best suits your next welding project.
Try out one of our high-quality carbon steel welding wires for yourself today! Order a sample to start welding with results!
Learn MoreDISCLAIMER: This information is descriptive in nature and not purely prescriptive. Refer to your own welding machine’s user manual for proper settings and consult a welding expert for support.