How to Weld Stainless Steel: A Complete Guide
Aug 30th 2023
Welding stainless steel doesn’t have to be a challenge with this complete guide. Known for its exceptional corrosion resistance, durability, and aesthetic appeal, stainless steel is a popular choice across various industries. Its unique properties can pose challenges when it comes to welding, but this complete guide will provide you with valuable insights, best practices, and essential tips for successfully welding stainless steel.
Whether you're a beginner or an experienced welder, we'll cover common questions, the necessary preparations before welding, and specific techniques for three popular welding methods: MIG, TIG, and flux-cored welding. From preparation to quality filler wire selection, we'll equip you with the necessary knowledge to overcome the challenges, achieve high-quality stainless-steel welds, and unlock stainless steel’s full potential in your next project.
Common Questions on Welding Stainless Steel
In this section, we address some of the common questions that arise when welding stainless steel. Understanding some of the basics about the properties of stainless steel can provide clarity and guidance to help you navigate particular welding challenges and ensure the best possible outcome. We’ll cover the difficulty level of welding stainless steel, the nature of welding dissimilar metals to stainless steel, and some of the best welding wire types for the task.
Can You Weld Stainless Steel?
Yes, you can weld stainless steel. In fact, stainless steel can be welded with a range of welding methods to achieve varying results depending on the application.
Is Stainless Steel Easy to Weld?
Though more difficult than welding carbon steel or mild steel, welding stainless steel is certainly doable with the right materials, tools, and procedures. However, stainless steel poses more challenges than other metals, like carbon steel. For example, stainless steel has a higher propensity to warp due to heat retention at welding temperatures, while the cooling process can also cause warping or cracking if not performed carefully. Due to its bright finish, stainless steel also shows scratches and defects more easily than other metals, meaning that extra care and control are needed to ensure the structure and appearance of the steel are maintained properly throughout the welding process.
Can You Weld Dissimilar Metals to Stainless Steel?
Some dissimilar metals can be welded to stainless steel, but serious considerations should be made concerning whether doing so is appropriate for the intended application. Carbon steel, low-carbon mild steel, galvanized steel, and cast iron may be welded to stainless steel, but doing so will require special techniques not covered in this guide. Welding stainless steel to dissimilar metals is a risk and calls for great care and attention to details in both the material types, filler metals, techniques, and procedures used. Consult a welding distributor or filler metal manufacturer like NS ARC if doubts or concerns arise about welding dissimilar metals to stainless steel.
Read our detailed and comprehensive guide on How to Weld Carbon Steel to Stainless Steel to learn more about welding dissimilar metals together.
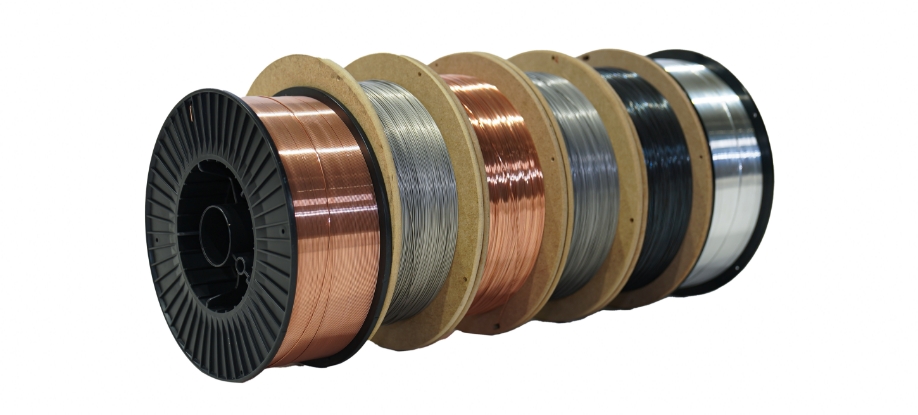
What Are the Best Welding Wires for Stainless Steel?
When it comes to welding stainless steel, choosing the right welding wire is crucial for achieving optimal results. There are different types of welding wires available, each with its own unique characteristics and advantages. The three most commonly used welding wires for stainless steel are solid stainless steel, cut-length stainless steel, and flux-cored stainless steel, and the most commonly used welding processes are MIG (GMAW), TIG (GTAW), and flux-cored (FCAW), respectively. Understanding the differences between these wires and processes is essential in selecting the best option for your specific stainless steel welding application.
MIG Welding Wires Are Best For:
- Simplicity: MIG welding wire is known for its simplicity and ease of use, making it a popular choice for both beginners and experienced welders.
- Decent deposition rates: MIG wires provide decent deposition rates, allowing for faster welding speeds and increased productivity.
- Decent bead appearance: MIG welding with appropriate settings and techniques can result in a decent bead appearance.
- Minimal slag: MIG welding produces minimal slag compared to other welding processes such as stick welding.
TIG Welding Wires Are Best For:
- Precise heat control: TIG wires enable welders to fine-tune the heat output, resulting in precise heat control and reduced heat-affected zones.
- Optimal bead appearance: The precise control over the heat and the ability to add filler material separately enable TIG welding to produce clean, aesthetically pleasing weld beads with minimal spatter.
- Discolored stainless steel: TIG wires can help minimize the discoloration and oxidation of stainless steel often associated with other welding processes.
- Minimal slag: TIG welding should produce minimal to zero slag, ensuring clean and precise welds that require minimal post-weld cleaning.
Flux-Cored Welding Wires Are Best For:
- High deposition rates: There are two types of flux-cored welding wire, gasless and what is known as a dual shield utilizing both shielding gas and flux. The gasless flux-cored welding wire provides shielding and promotes efficient molten metal transfer, resulting in higher deposition rates. While the dual shield flux-cored welding wire provides added alloying elements and deoxidizers to promote high quality, high deposition welds.
- Dirty or slightly imperfect stainless steel: The flux within the wire contains compounds that help remove surface contaminants, allowing for effective welding even on dirty or contaminated surfaces.
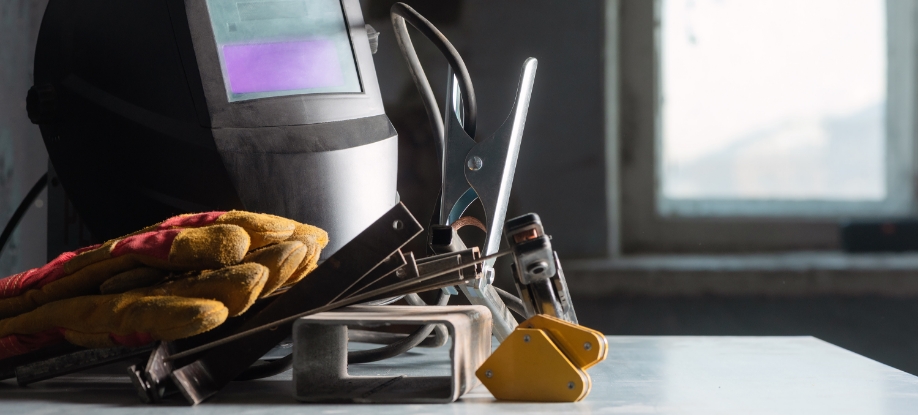
Tools & Equipment for Welding Stainless Steel
Having the right tools and equipment for welding stainless steel is essential for creating high-quality welds. From selecting the appropriate welding machine to ensuring the welding wire and shielding gas are appropriate for the application, each tool plays a crucial role in the welding process. Whether you are a beginner or an experienced welder, having these tools on hand will ensure that you have everything you need to tackle your stainless-steel welding project with confidence.
List of Stainless-Steel Welding Tools & Equipment
- Welder / welding machine: This welder can be a MIG or TIG machine depending on your preferred method. A MIG welding machine is generally the easiest to use for stainless steel. Get a welder with a gun.
- Gun replacement contact tips
- Appropriate size and material gun liner to smoothly guide the wire to the contact tip
- Welding wire feeder vs all in one integrated wire feeder for improved control: Welders who weld often or who work in a professional setting will have a separate wire feeder. A wire feeder that is integrated all-in-one is consistent with a casual or hobbyist welder.
- Welding wire / electrodes: Choose the best and most appropriate welding wire for the job. Generally, joining two pieces of stainless steel will require stainless steel welding wire. See below sections on choosing the right welding wire for the different welding methods of MIG, TIG, and flux-cored (FCAW).
- Shielding gas: This is for MIG and TIG, and flux-cored (FCAW) if the wire isn’t self-shielded. A common shielding gas mixture for welding stainless steel is argon, or argon mixes to include: oxygen, helium, and carbon dioxide. See below sections on choosing the right shielding gas for the different welding methods of MIG, TIG, and flux-cored (FCAW).
- Wire brush (not carbon steel wire, must be stainless steel wire), grinder, or solvent: These can be used to scrape away metal and clean the area. Carbon steel wire will contaminate the weld and cause oxidation/rust.
- Temperature tracker: This can be an electronic infrared thermometer, electronic surface temperature probe, or temperature sticks.
- Welding table for shop work or safe workstation at a large facility
- Welding PPE (Personal Protective Equipment)
- Welding helmet
- Safety glasses
- Welding apron or jacket
- Welding gloves
- Welding boots
- Ventilation system (if welding indoors)
- Welding PAPR System
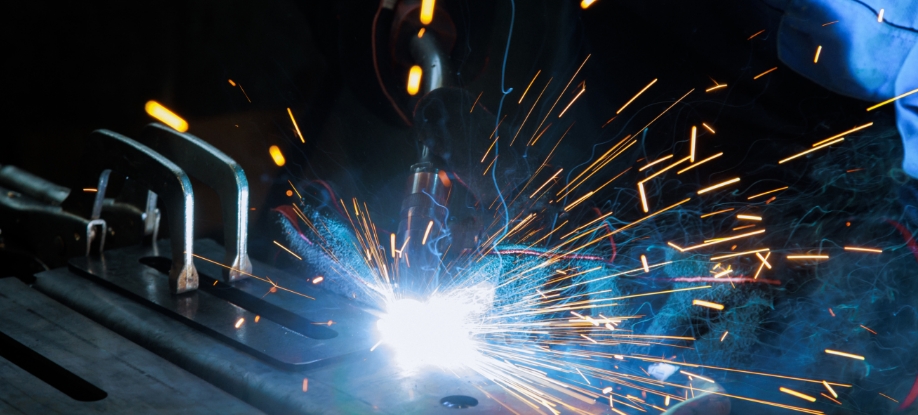
Best Practices for Welding Stainless Steel
Achieving high-quality and reliable welds in stainless steel requires the application of best practices throughout the welding process. Due to the unique properties of stainless steel, it is essential to follow specific guidelines and techniques to ensure optimal weld integrity and performance. By incorporating these best practices into your welding process, you can confidently tackle stainless steel projects and produce welds that are strong, durable, and visually impressive.
- Ensure that all materials needed for the job are present and that your equipment is properly set up before beginning the welding process.
- Use ventilation systems if welding indoors.
- Use welding PAPR System.
- Maintain appropriately low heat levels on your welding machine due to risks of warping and cracking. One way to achieve this is to avoid using large filler metal diameters since larger wires require higher temperatures. Match the wire diameter to the specific welding application.
- Ensure a proper fit-up between mating parts. Creating the right degree of contact can minimize the risk of gaps, warps, and poor aesthetic appearance.
- Use a filler metal that matches the base material for the best results. Even though stainless steel can be welded with carbon steel welding wire, it is often best to use stainless steel welding wire if the goal is to achieve stainless base material properties post welding.
- Maintain a high enough travel speed to avoid overheating the stainless steel and causing warps or cracking.
- Minimize the risk of rust by utilizing the right shielding gas and cleaning the finished weld with your wire brush (not carbon steel wire but a stainless-steel brush), grinder, solvent, or correct pickle and passivation process. Again, carbon steel wire will contaminate the weld and cause rust.
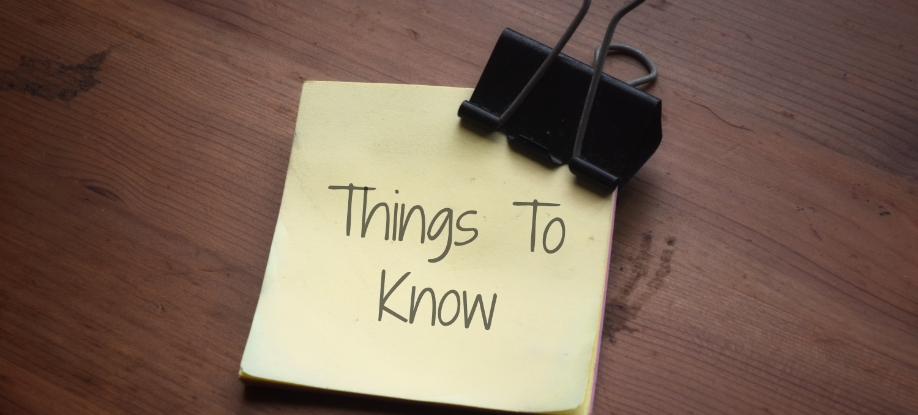
How to Weld Stainless Steel – Preparation & Tips
Welding stainless steel requires careful consideration and specialized techniques to achieve optimal results. In this section, we will delve into the MIG, TIG, and flux-cored welding methods for stainless steel. Each method offers its own advantages and challenges, and understanding the specific preparations and top tips for each technique is crucial for successful welds. From essential preparation steps to expert tips and techniques, we will provide you with guidelines to ensure successful stainless-steel welds with MIG, TIG, and flux-cored welding (FCAW).
Preparing for MIG Welding Stainless Steel
- Welding Wire: Choose the appropriate wire alloy and size for the desired weld. ER308L stainless steel welding wire is a common choice, but be sure to consult a welding wire chart to determine the most appropriate welding wire for the job.
- Amperage & Voltage: Consult your welding machine’s manual or welding settings chart for recommended amperage and voltage settings. When it comes to setting your welder’s amps for welding stainless steel, consider using lower amp settings to reduce heat input and warpage. Adjust voltage settings according to your welding machine’s manual to achieve optimal weld quality and consistent welding bead results.
- Polarity: The MIG (GMAW) welding machine should be set to DCEP (direct current electrode positive) polarity for gas shielded wires.
- Flow Rate: Set the flow rate of the shielding gas properly by checking the welding machine manual or chart to prevent weld contamination. A good starting point is 35 CFH but the right setting will be application-specific. High travel speeds require more flow but take caution; too much shielding gas, just like too little shielding gas coverage, will cause other weld quality issues.
- Wire Feed Speed: Determine the appropriate wire feed speed for stainless steel alloys by checking your welding machine’s manual or configuration chart.
- Shielding Gas: Select a suitable shielding gas, like a tri-mix of helium, argon, and carbon dioxide. Avoid using pure inert gases like helium or argon, as they are not ideal for MIG welding stainless steel.
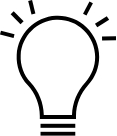
Tips for MIG Welding Stainless Steel
- Weld Pool: When starting, allow enough time for the weld pool to form, then maintain that consistent weld pool size to produce a consistent, finished weld.
- Welding Angle: Hold the MIG weld gun at an angle of around 5 - 15 degrees for optimal penetration and reduced splatter while avoiding horizontal and vertical angles, which can result in a weld appearance like that of a blotch or glob.
- Travel Speed: Weld relatively quickly to avoid heat concentration (qualification of weld bead size will determine application travel speed), but don’t go too fast or the bead will be too narrow. A push technique and stringer bead are recommended for better weld appearance and penetration.
- Shielding Gas Coverage: Use post-welding shielding gas flow to prevent oxidation and ensure shielding gas protection until the pool has completely cooled down. Contamination can be prevented by holding the MIG nozzle close to the stainless steel for a few seconds.
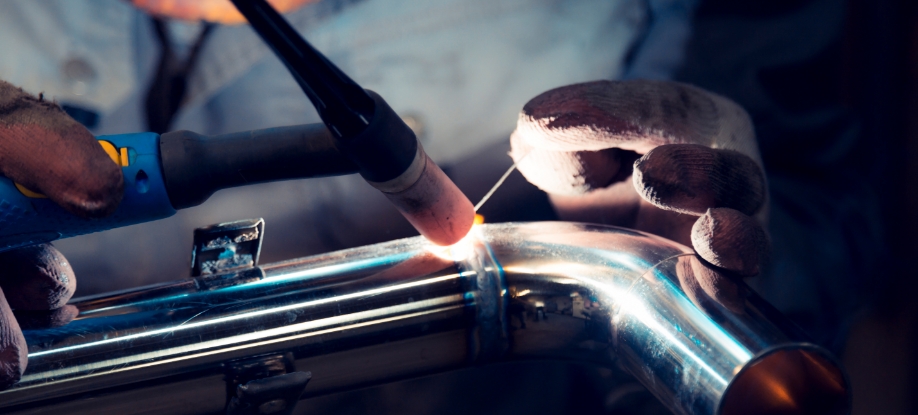
Preparing for TIG Welding Stainless Steel
- Welding Wire: Ensure the welding wire to be used is the correct alloy, matches the base material, and is appropriate for the job. Stainless steel welding wire is often the best choice for welding stainless steel.
- Amperage: Set the proper maximum amperage on your TIG welder according to the alloy and thickness of the stainless steel. The setting of the amps will directly affect the heat. Utilize a chart for this to get the right number. Some TIG welders allow for finger- or foot-controlled amp settings while you weld.
- Tungsten Electrode: Ensure the tungsten electrode used is correct for the job based on the amps and base material thickness.
- Polarity: The DCEN (direct current electrode negative) setting is necessary for your TIG welding machine when welding stainless steel to prevent the tungsten electrode from being used up.
- Flow Rate: Check the welding machine recommendations for setting the proper flow rate.
- Shielding Gas: Utilize the proper shielding gas when TIG welding stainless steel. The most common shielding gas for this purpose is pure argon, but other mixtures including helium, nitrogen, and hydrogen may be used for special properties. Consult a TIG welding shielding gas chart to determine the proper gas for the type of stainless steel to be welded.
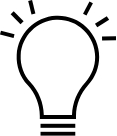
Tips for TIG Welding Stainless Steel
- Weld Pool: Have the weld pool diameter match the thickness of the base material to ensure a consistently strong and clean weld.
- Welding Angle: Commonly used angles include a 70-degree angle for the torch and a 10- to 25-degree angle for the welding wire. Make adjustments as necessary according to the joint type.
- Travel Speed: Keep a steady pace to avoid overheating the stainless steel, but don’t move the torch too fast as it can blow the gas away from the electrode. This can result in a blackened electrode and make it challenging to start the next weld.
- Shielding Gas Coverage: Keep the gas flowing and directed at the weld pool until the orange color fades. By maintaining post-flow gas coverage, both the pool and electrode can cool properly.
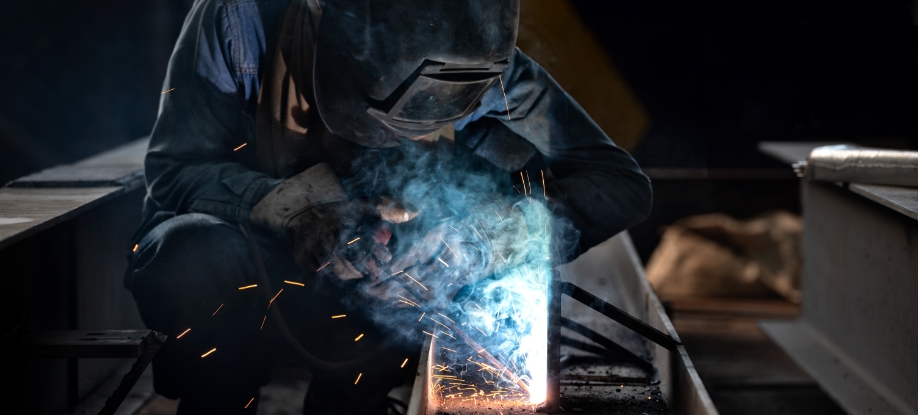
Preparing for Flux-Cored Welding Stainless Steel
- Welding Wire: Carefully select the appropriate flux-cored wire considering its unique composition and the role of the consumable electrode wire has on the weld. Take note of the flux composition as well as the base material alloy and thickness when determining which wire type to choose, and consult a welding wire chart for optimal results. NOTE: using a gasless, self-shielded wire works in windy conditions but is typically limited to flat and horizontal welding applications.
- Polarity: Ensure that your welding machine is set to the correct polarity, as it can vary depending on the type of flux-cored welding wire being used. Best practice is DCEP for gas shielded flux-cored welding wires and DCEN for self-shielded flux-cored wires. Please consult the wire manufacturer for details).
- Shielding Gas: While shielding gas may not be necessary for some welds performed with self-shielded flux-cored welding wire, it is essential for welding stainless steel due to stainless steel’s unique properties. If not using a self-shielded flux-cored welding wire, ensure you have the appropriate shielding gas on hand. Some common mixtures for dual shield flux-cored wires used for stainless steel welding are 100% CO2, or 75% argon 25% CO2 mixture. Check with your welding wire manufacturer for recommendations for the mixture that’s appropriate for the alloy and thickness of the stainless steel being welded.
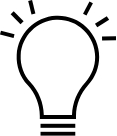
Tips for Flux-Cored Welding Stainless Steel
- Weld Pool: Flux-cored wire tends to have a higher deposition rate, so it is important to maintain a consistent and stable weld pool size to ensure proper fusion and penetration of the stainless steel. Controlling the wire feed speed and voltage settings helps regulate the molten weld pool and achieve desired results while keeping heat under control to prevent distortions.
- Weld Angle: Start with a 10-degree angle and make adjustments as needed to drag the electrode and minimize slag.
- Travel Speed: Try a practice run of flux-cored wire on a scrap piece of stainless steel to get the travel speed right. Moving too quickly may prevent the weld pool from fully penetrating, resulting in weak or incomplete welds, while moving too slowly can lead to excessive heat input, which can cause burn-through, distortion, and metallurgical property changes of the stainless steel.
- Shielding Gas Coverage: Flux-cored welding wire can generate more slag and by-products during welding. Maintaining post-weld shielding gas coverage and flow for a few seconds helps prevent the formation of defects, such as porosity or excessive oxidation.
NS ARC Stainless-Steel Welding Wires
NS ARC Satin Glide® stainless-steel welding wire is the ultimate choice when it comes to welding stainless steel. This welding wire excels in corrosion resistance, ensuring long-lasting and durable welds that can withstand harsh environments. Its exceptional weld strength and high-temperature resistance help guarantee the integrity and reliability of the welded joints. Offering ease of use and versatility, this welding wire is suitable for various joining, modification, and repair jobs. Whether your application is agricultural equipment, auto body, automotive exhaust, general fabrication, heavy equipment, pipe welding, pressure vessels, railcars, shipbuilding, structures, trailers, or more, this welding wire proves its efficacy across diverse industries.
Additionally, the Satin Glide® stainless-steel welding wire’s compatibility with mechanized, robotic, and semi-automatic welding methods allows for efficient and precise welding processes in your facility. With Satin Glide® stainless-steel welding wire, NS ARC delivers a superior solution that ensures exceptional weld performance and meets the highest standards of quality and reliability.
Contact Us for More Information on Stainless-Steel Welding Wires
Are you interested in learning more about how Satin Glide® stainless-steel welding wire from NS ARC can benefit your business? As the largest dedicated welding wire brand in the United States, we have the right team of experts to assist you. With their extensive knowledge and experience, they will guide you through your welding project and provide tailored solutions to meet your specific goals and requirements. Whether you require guidance, tips, or assistance in selecting the right welding wire for your welding project, we are here to help. Contact us today to start your journey toward welding success.
Get a more in-depth look at the different welding wires that can be used for stainless steel welding with our informative guide!
Learn MoreDISCLAIMER: This information is descriptive in nature and not purely prescriptive. Refer to your own welding machine’s user manual for proper settings and consult a welding expert for support.