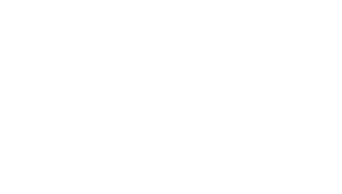
Women-Owned Business
Stainless-steel welding wire is a high-quality, versatile welding consumable used in a wide range of industries, including aerospace, automotive, construction, oil and gas, food and beverage, medical equipment, and marine. This welding wire is specifically designed for welding stainless-steel alloys and is available in various types and grades, each with unique properties and characteristics. NS ARC carries a wide range of high-quality stainless-steel welding wire, and each of our products is designed to meet the specific requirements of each application, with varying levels of corrosion resistance, strength, and other properties as qualified.
Stainless-steel welding wire like NS ARC Satin Glide® wire comes with several unique benefits that make it a top choice for strength and resilience across a number of industries. As a highly versatile and dependable metal, stainless steel remains a popular choice for welding. Some of the most prominent benefits of welding with stainless-steel welding wire include:
Welding with stainless-steel wire results in strong, durable welded joints that can withstand heavy loads and stress and are resistant to deformation and cracking. This strength is important in industries where structural integrity is crucial, such as construction and aerospace.
Additionally, stainless-steel alloys are highly resistant to higher service temperatures, which is important in industries where welded products are subjected to high-heat environments. NS ARC Satin-Glide® products help prevent the welded joint from breaking down or becoming weakened due to exposure to extreme heat.
Stainless-steel welding wire is highly resistant to corrosion, making it ideal for use in industries where exposure to corrosive elements is a concern. This resistance helps ensure that the welded joint maintains its strength and integrity over time when proper welding procedures are followed.
Stainless-steel wire is relatively easy to use and can be welded using a variety of welding techniques, including TIG (Tungsten Inert Gas), and MIG (Metal Inert Gas), or GMAW (Gas Metal Arc Welding).
As a versatile option, stainless-steel welding wire can be used with a wide range of stainless-steel alloys for various applications. This flexibility allows for a greater range of options when selecting type of welding wire, from welding pipes and tanks to building structures and architectural features.
Stainless steel is a non-porous material, which makes it resistant to bacteria growth and easy to clean. It's an ideal material for welding in industries such as food processing and medical devices.
Stainless steel is a durable material that can withstand high temperatures and extreme conditions, making it an excellent choice for welding in heavy-duty industries. It can withstand the tougher jobs with greater efficiency.
Stainless-steel welding wire has the ability to produce a clean, aesthetically pleasing finish that is highly desirable in industries such as architecture and design when post-weld finishing is performed. The welded joint blends in seamlessly with the surrounding material, resulting in a high-quality, professional appearance.
There are plenty of benefits of Satin-Glide® stainless-steel welding wire from NS ARC that make it a reliable and efficient option for welding stainless steel in a variety of industries. Its durability and versatility match its resistance to corrosion and high temperatures so that it can lend its strength to many different welding applications.
Thanks to its high versatility, stainless-steel welding wire lends itself well to a wide variety of applications and tasks. From fabrication and manufacturing to modification and more, stainless-steel welding wire is useful across several types of welding jobs. Some of the most common uses for stainless-steel wire include:
Stainless-steel welding wire can be used to manufacture and repair agricultural equipment that requires high corrosion resistance, durability, and precision welding.
When repairing and manufacturing auto bodies, precision and control are key. That’s why stainless-steel welding wire is essential for automotive components that require precision welding and corrosion resistance.
For this type of application, the welding wire needs to have high resistance to extreme temperatures and corrosion, which is exactly what you get from NS ARC automotive grade stainless-steel welding wires.
Reinforcement tasks for industrial equipment, machinery, and vehicles can be easily and confidently completed with stainless-steel welding wire. Its corrosion resistance and dependable mechanical properties make it perfect for welding heavy-duty equipment.
Stainless-steel wire can be used to weld together various components to fabricate structures, machines, and equipment. Its high weld strength and durability make it perfect for heavy-duty, industrial products.
When it comes to welding pipes, the welder can greatly benefit from a stainless-steel welding wire as it reliably provides them effective control over the entire process.
Stainless-steel welding wire is engineered to withstand exposure to high pressures and temperatures that are often encountered when working on pressure vessels and joining their components together.
Welding wire used in the manufacturing of passenger railcars needs to offer the highest level of quality to protect the countless passengers that depend on this form of travel. Our wire is more than capable of handling the job.
Often used for construction purposes, such as welding steel beams and columns, handrails, and other architectural features, stainless-steel wire provides incredible structural support that millions rely upon every day.
Trailers are often exposed to demanding conditions, such as heavy loads, impacts, and the elements, so high-quality stainless-steel welding wire is very necessary to build, repair, and maintain trailers.
The shipbuilding industry requires optimal welding strength when fabricating components for its vessels. This industry relies on high-quality stainless-steel welding wire in order to achieve complete and solid bonds.
With stainless-steel welding wire, you can perform a wide range of tasks, from simple repairs to complex fabrication projects, making it an ideal welding wire choice for many different types of businesses.
Stainless-steel welding wire offers several unique benefits that make it particularly suitable for certain applications. Some of these common applications include:
From stainless steel to stainless steel or stainless steel to carbon steel, NS ARC Satin-Glide® welding wire can be used to join two or more pieces of metal together, either temporarily or permanently to create a dependable solid weld joint.
Modifying existing components or structures to improve their performance or adapt them to new uses is one of the most common uses for stainless-steel wire. This is especially true in the automotive industry with custom-build communities and mod shops. Heavy equipment and machinery can also be modified to great effect in industrial applications.
Stainless-steel welding wire can be used to repair a vast range of damaged or broken components, such as pipes, tanks, structures, and machinery. This makes the wire a highly popular choice.
Stainless-steel welding wire can be used to create sculptures and art installations due to its malleability and aesthetic appeal.
Stainless-steel welding wire is best for a range of industries thanks to its sought-after qualities. In fact, stainless-steel welding wire is particularly useful in industries that require resistance to corrosion, high temperatures, and oxidation, as well as industrial and heavy-duty applications that require high levels of strength and durability. Some of the industries that benefit the most from stainless-steel welding wire include:
Used for welding various parts of vehicles, including exhaust systems and frames, stainless-steel welding wire is a popular choice in the automotive industry. The use of stainless-steel welding wire ensures that the parts have a level of corrosion resistance, which is important for the durability and longevity of the vehicle.
Learn moreThe incredible strength, durability, and corrosion resistance offered by stainless-steel welding wire makes it an optimal choice in the construction industry. This welding wire is often used to fabricate, maintain, and repair parts of buildings like structural frames, staircases, handrails, and more.
Learn morePipelines, storage tanks, power plants, and other equipment, components, and structures in the energy industry require the corrosion resistance, high temperature resistance, and resilience of stainless-steel welding wire to maintain quality and structural integrity of the welded structures and components.
Learn moreStainless-steel welding wire is highly versatile and can be used for welding a range of stainless-steel alloys, including austenitic and ferritic stainless steels. This versatility makes it an ideal choice for manufacturing industries that encounter a variety of welding applications.
Learn moreStainless-steel welding wire, with its high corrosion resistance, durability, and strength, is an ideal choice for transportation applications, including manufacturing vehicle frames, exhaust systems, and other components. The use of stainless-steel welding wire can help improve the longevity and reliability of transportation equipment, ultimately reducing maintenance costs and downtime.
Learn moreSeveral industries can benefit from stainless-steel welding wire, mainly due to its high strength, durability, and resistance to corrosion and high temperatures. If you require further consultation on which stainless-steel welding alloy would be the best choice in your industry, simply reach out to us today and we’ll be glad to help you find the best solution for your welding application.
The best way to use stainless-steel welding wire depends on the specific application and the type of stainless-steel being welded. However, there are some general guidelines that can help ensure successful welding with NS ARC Satin-Glide® stainless-steel welding wire.
First, you need to prepare the surface prior to welding. It needs to be clean and free of contaminants such as rust, dirt, and oil. Use a stainless-steel brush or an approved cleaning solution to clean the surface. This can help ensure a successful and consistent weld.
You also need to make sure that you are utilizing the right welding technique. The technique depends on the specific application and the type of stainless steel being welded. The most common welding techniques for stainless steel include TIG (Tungsten Inert Gas) welding, MIG (Metal Inert Gas) welding, or GMAW (Gas Metal Arc Welding). Once you decide the technique, use the appropriate welding wire for the specific application. Different types of stainless-steel welding wire are designed for different applications and have varying levels of corrosion resistance, strength, and other properties.
When welding with stainless-steel welding wire, it is important to use the correct shielding gas to prevent oxidation of the weld. Argon is the most common shielding gas used in stainless steel welding. You also need to be aware of the heat input. Stainless steel is sensitive to heat, so it is important to control heat input during welding to prevent distortion, warping, corrosion resistance and strength, or other damage. Follow the recommended heat input guidelines for the specific stainless steel being welded.
Finally, make sure that you are practicing good, proper welding techniques, including maintaining the correct angle, distance, and travel speed. Practice good techniques to ensure strong, high-quality welds. Also, remember to follow the manufacturer's recommendations and industry best practices, while also considering the specific application and type of stainless steel being welded. This can help ensure that your welding job is successful.
NS ARC offers a variety of packaging types, including spools, drums, and our specialty packages.
We offer three different bulk packaging options: drums, Smart Paks® and Tru-Tracs®. Drums keep the wire packed in a loose coil form in which the wire takes on a large sine wave or “S” shape. Inside our Smart Pak® package, a 12-sided cardboard core contains the wire, and the core is encompassed by a rugged outer cardboard box. All components of the Smart Pak® are 100% recyclable, helping to reduce waste and cut down on disposal costs. The Smart Pak® offers multiple engineered wire dispensing solutions and comes with lifting straps for easier positioning in your facility.
The proprietary winding technology of our Tru-Trac® Wood Reels features “twist-free” wire let-off that requires only a few ounces of drag. The design of this packaging maximizes productivity while lowering welding costs using the smaller dispersion pattern. The snag-free operations without the drive roll overload are there to deliver precise joint tracking.
Our drum, Smart Pak® and Tru-Trac® bulk package options are an excellent choice for your large-scale production operation. Each type of bulk packaging is designed to maximize productivity while reducing downtime caused by change-outs and providing better pay-off systems to produce greater quality welds.
For smaller package options, our fiber spools are randomly layer wound and our plastic spools are level-layer wound.
Our team of welding experts is available to provide you with the information that you’re looking for, whether you need some guidance or advice for your next welding project or you’re not sure which welding wire best suits your application.
If you have any questions before making a purchase chat with our online operators to get more information.
Ask An Expert or find our Questions & Answers