When to Use Cored Welding Wire Over Solid Welding Wire
Sep 7th 2023
In the dynamic world of welding, choosing the right type of welding wire can significantly impact the outcome of your projects. One question that often arises is whether to opt for cored welding wire or solid welding wire, since each type brings its own set of advantages, disadvantages, and considerations to the table. By understanding the unique characteristics of both cored and solid welding wire, you can make an informed decision on choosing the right type of welding wire for your application.
Productivity & Versatility: Why Choose Flux-Cored Welding Wire Over Metal-Cored?
Flux-cored welding wire has earned its place as a preferred choice in specific welding applications thanks to its distinct advantages. While it might have a higher up-front cost compared to solid wire, it proves to be a cost-efficient solution for large-scale welding endeavors. This cost-effectiveness stems from its high deposition rates, which translate into increased productivity. The absence of the need for shielding gas with self-shielded flux-cored welding wire further adds to its convenience and economic viability, making it a favorable option for welders seeking efficient solutions.
However, the use of flux-cored welding wire comes with important considerations. Flux-cored wire emits toxic fumes and produces spatter during welding, which necessitates proper ventilation and adherence to safety precautions. Despite these concerns, the unique attributes of flux-cored wire render it suitable for environments where surface cleanliness is a challenge. Its ability to tolerate relatively dirty surfaces makes it an attractive choice when extensive cleaning is not feasible. This can help to save both time and effort.
While flux-cored welding wire might not deliver optimal results for welding thin materials, it does feature high penetration, making it particularly suited for thicker metals. The welding appearance of flux-cored wire often includes slag and spatter, which may require additional post-weld cleaning. Additionally, the versatility of flux-cored wire shines through its compatibility with a range of metals, including steel, cast iron, and galvanized steel, enabling its application across diverse welding scenarios.
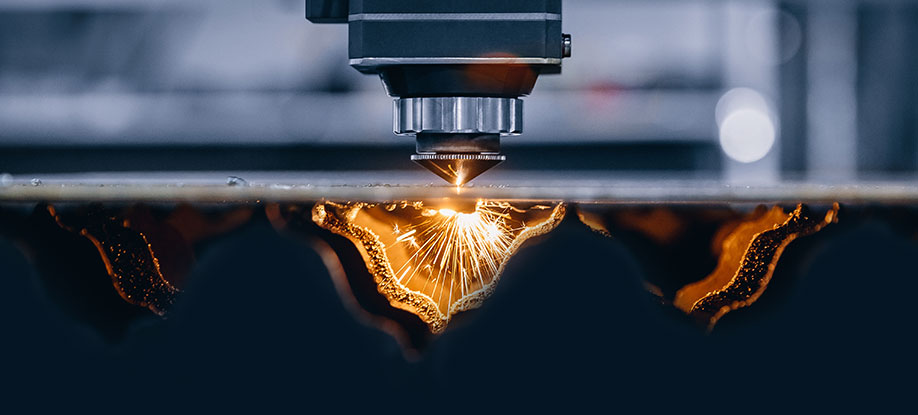
Precision & Efficiency: Why Choose Metal-Cored Welding Wire Over Flux-Cored?
Metal-cored welding wire offers a range of benefits thanks to its unique composition featuring metal powder alloying elements. This type of wire provides higher deposition rates, easier cleanup, and smoother bead appearances compared to solid welding wire, which translates to increased efficiency. Excelling in applications requiring precise control and minimal spatter, metal-cored welding wire boasts no-slag characteristics that eliminate the need for post-weld cleaning and helps to save time and effort. However, it's important to note that metal-cored wire is generally limited to flat and horizontal welding positions, which may impact its suitability for certain projects.
Despite these drawbacks, the efficiency, ease of cleanup, and control offered by metal-cored welding wire make it a preferred choice for scenarios where speed and quality are paramount. Its ability to deliver smoother welds, while reducing post-weld tasks, showcases its potential for enhancing productivity and ensuring consistent results in welding operations.
Control & Cost: Why Choose Solid Welding Wire Over Flux-Cored or Metal-Cored?
Regarding welding wire choices, solid welding wire stands as a constant staple across several industries. Featuring a lower initial cost compared to cored welding wire, solid welding wire is generally cost-effective and caters to welding projects that do not demand the rapid deposition rates of cored welding wires.
One of the key characteristics of solid welding wire is its reliance on shielding gas for protection against atmospheric contamination during welding. This dependency on shielding gas contributes to controlled and consistent welds. Solid wire offers moderate penetration, making it well-suited for a variety of welding tasks. Furthermore, its high feedability ensures smooth welding operations.
Solid welding wire produces minimal fumes and spatter, fostering a safer and cleaner working environment. Moreover, the requirement for meticulous base metal cleaning prior to welding ensures proper fusion and optimal weld quality. However, it's important to note that the necessity of shielding gas in the case of solid wire does contribute to the overall cost, and this aspect should be taken into account when making your selection.
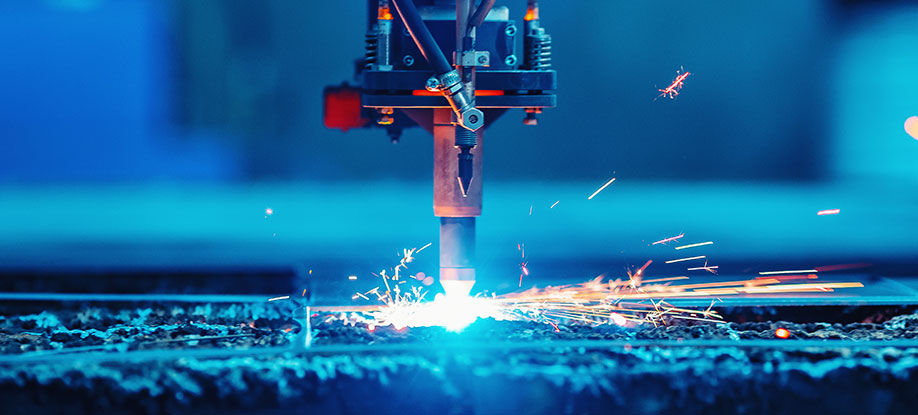
Solid welding wire demonstrates its versatility in welding thin metals as it delivers precise and aesthetically pleasing welds. Additionally, solid welding wire displays consistent and satisfactory performance across an array of metals like steel and aluminum.
Choose Welding Wire Wisely: The Key to Successful Welding
When faced with the decision between cored welding wire—including metal-cored and flux-cored—and solid welding wire, there is no universal answer. Your choice should align with the specific demands of your welding requirements and application, and each type of wire brings distinct advantages and considerations to the table.
For extensive projects prioritizing high productivity, flux-cored and metal-cored welding wires prove to be valuable options. Their high deposition rates, ability to handle thicker materials, and tolerance for less-than-ideal surfaces make them compelling choices. Conversely, solid welding wire appeals to welders seeking a cost-effective solution for precision and uniformity as solid welding wires excel in welding thin metals.
Ultimately, understanding the strengths and considerations of both cored and solid welding wires empowers you to make a well-informed decision. Your welding journey is as unique as your projects, and by selecting the appropriate welding wire, you lay the foundation for welding success.
Wondering Which Welding Wire is Right for You? Order a Sample Today
If you’re wondering which welding wire would be the right choice for your unique requirements and application, contact an expert at NS ARC today and order a sample to try our welding wire for yourself. The Pit Crew is happy to listen closely to your concerns and find the right welding wire for your business.
Carbon steel is one of the most commonly welded materials in multiple industries. Understanding which type of welding wire, solid or cored, to use for the project is incredibly crucial to achieving the best weld. That's why we created this handy guide to figuring out exactly how to find the ideal welding wire. Check it out!
Learn MoreDISCLAIMER: This information is descriptive in nature and not purely prescriptive. Refer to your own welding machine’s user manual for proper settings and consult a welding expert for support.