Welding Carbon Steel Tips and Tricks
Nov 28th 2023
Welding carbon steel is a common endeavor that both seasoned welding veterans and new beginners encounter in their welding careers. Known for its versatility and strength, carbon steel is utilized in various applications, including general fabrication, automotive manufacturing, and shipbuilding. Still, there’s always something new to learn when welding carbon steel, so we’ve gathered some of the top tips and tricks to make the process a lot easier.
Selecting the Right Welding Wire
The choice of which welding wire to use is critical for successfully welding carbon steel. It’s the heart of the weld that holds the pieces together, so you need to ensure that you’re working with the right one. Several factors need to be considered for making the right choice, including the welding wire type, wire diameter, material type, material thickness, composition, and application.
Solid carbon steel welding wires are excellent for thinner sheets of carbon steel where precision and control are key to a good weld. A copper-coated welding wire promotes excellent electrical and arc stability while copper-free welding wire is a great choice for applications where copper contamination is a concern.
Flux-cored welding wires, on the other hand, are great for thicker sections of carbon steel and provide excellent penetration. They also offer higher productivity with their higher deposition rate for more efficient welding.
The welding wire diameter you choose is closely linked to the thickness of the material. In general, thicker parts of carbon steel require larger-diameter welding wire while thinner parts require smaller-diameter welding wire. The thicker section requires more heat for proper penetration and fusion, so it needs a thicker wire to carry more current and produce more heat. A thinner section can’t handle too much heat, so it needs a smaller wire for better control of the heat input to avoid burn-through.
A general rule is that the welding wire you choose for the project needs to match the chemical and mechanical composition of the base material, so a welding wire used on high carbon materials needs to match the higher amount of carbon. Otherwise, the incompatibility will produce a weak and structurally threatening weld.
In the end, if you are still unsure of which welding wire to use, consult the manufacturer’s recommendations for both your welding machine and the welding wire. The welding wire’s manufacturer can provide you with the proper guidance for selecting the ideal choice for your specific welding application. Check out our detailed guide on how to make the right choice: The Best Welding Wire for Carbon Steel.
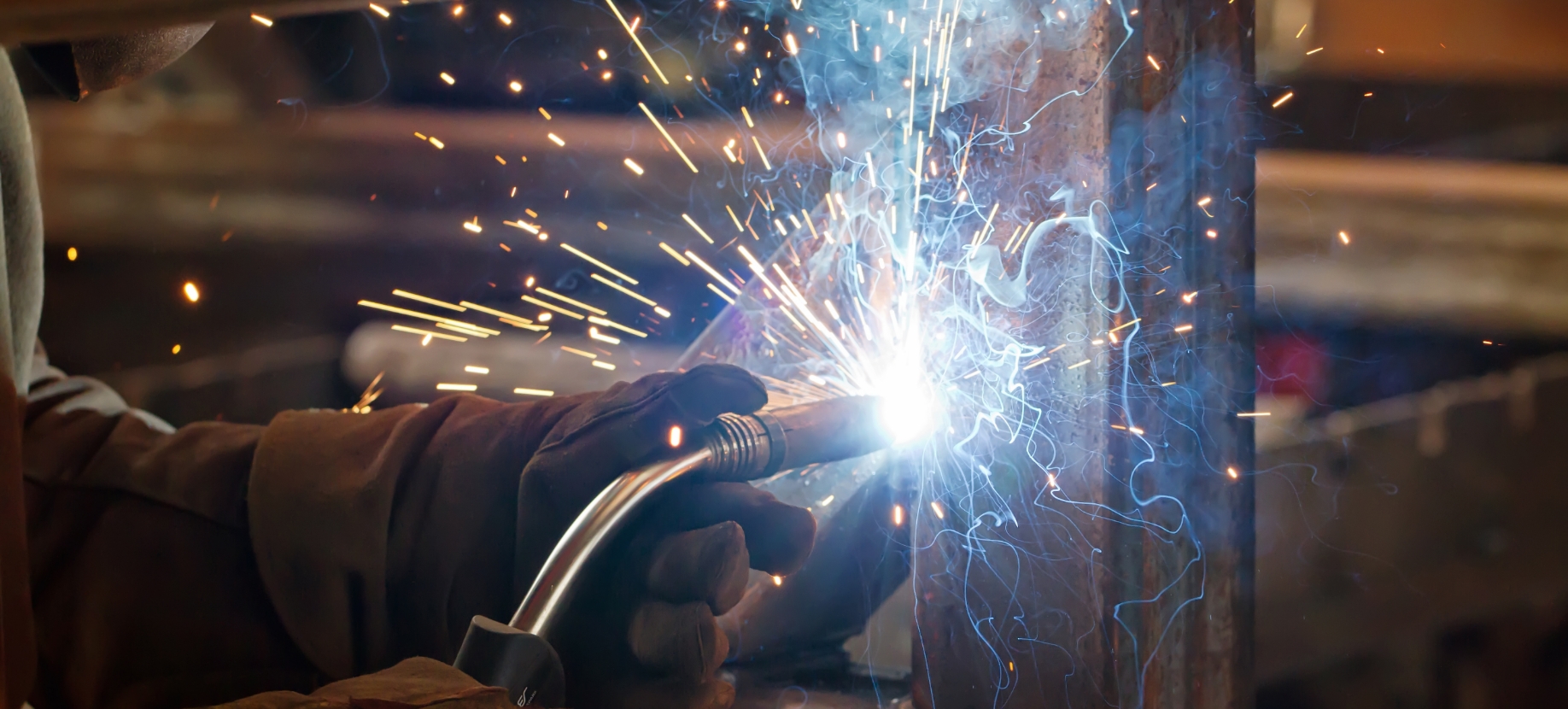
Remember to Practice Welding Carbon Steel
One of the biggest and most essential tips we can give is this: PRACTICE. Dedicated practicing still stands as one of the most reliable ways to improve your welding skills. Here are some of the things that you should look out for when you practice carbon steel welding:
Porosity
Porosity is the presence of cavities in the welded metal that are caused by unwanted gases trapped within the weld puddle during solidification. It can weaken the quality of the weld, so ensure that the area is free of contaminants before welding. Improper shielding gas can also cause porosity, so use the right shielding and gas flow rate combination.
Ripples, Humps, and Underfills
Ripples, humps, or underfills are common weld bead irregularities. They affect the overall quality of the weld, both superficially and integrally. These types of defects can be prevented by achieving a consistent travel speed with proper fusion and penetration. Steadiness is the key to achieving improved bead appearance by avoiding abrupt stops and starts throughout the process.
Always Remember PPE
Always remember to wear your personal protective equipment. When you’re welding, you’re exposing yourself to extreme heat and powerful equipment. Without the proper equipment, you risk radiation exposure, burns, shocks, cuts, and much worse. We strongly discourage engaging in any welding operation without wearing the following:
- Welding helmet
- Welding gloves
- Safety glasses
- Flame-resistant clothing
- Welding jacket or apron
- Steel-toed boots
- Respirator or dust mask
- Ear protection
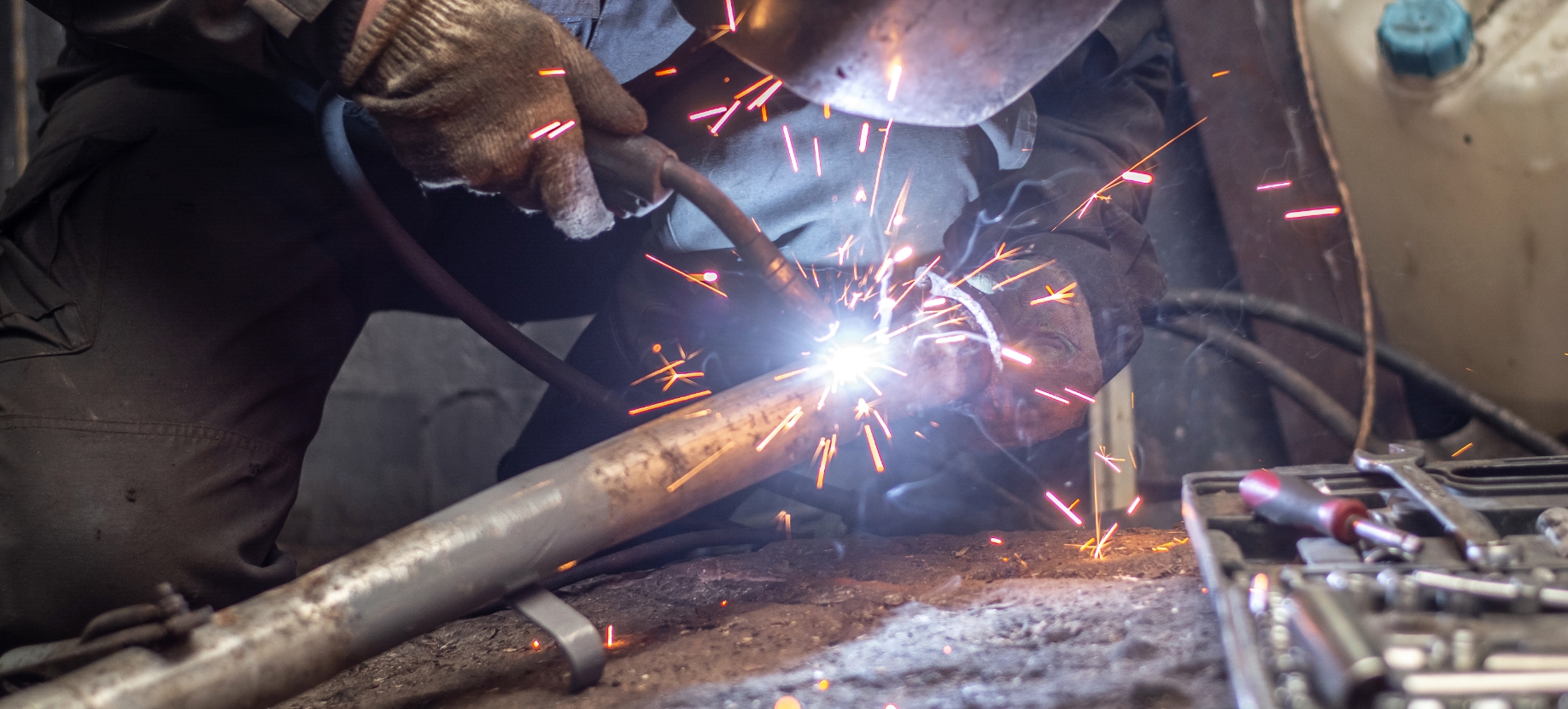
Contamination
Contamination can cause various issues that threaten the integrity of the weld. It can lead to porosity, cracking, weakened corrosion resistance, poor joint strength, excessive spatter, and inconsistent weld bead appearance. Thoroughly cleaning the material before welding with a wire brush can help eliminate the risk of contamination. Frequently performing maintenance and cleaning your welding gear can also help reduce the risk.
Travel Speed
Travel speed needs to be consistent. Standing in a comfortable position and keeping a steady hand can help with this. Moving too slowly can result in excessive heat input and possible burn-through, but moving too fast can lead to insufficient fusion and poor penetration. The ideal travel speed depends on various factors, such as material thickness, welding wire diameter, welding parameters, etc.
Inadequate Gas Coverage
Inadequate gas coverage can compromise the quality of the weld and lead to issues involving porosity, incomplete fusions, oxidation, scaling, cracking, and excessive spatter. It is incredibly important to ensure adequate shielding gas coverage by correctly setting the gas flow rate, selecting the appropriate gas mixture for the welding process, and maintaining consistent gas flow throughout the welding operation. For MIG welding carbon steel, the typical shielding gas mixture utilized is 75% argon/25% carbon dioxide for short-circuit arc transfer.
Cracking
Cracking may occur if you are using an inadequate welding wire. It’s important to remember that the welding wire’s chemical composition should match the base metal. In terms of diameter, it’s recommended to use smaller diameter welding wire for thinner materials to reduce heat input and larger diameter welding wire for thicker metals to increase it. In regards to the type of wire used, copper-coated wires are excellent for improved electrical conductivity, but copper-free wires can offer lower amperage for reduced spatter and heat input.
Excessive Distortion
Excessive distortion is an issue that many welders face and can be caused by a number of factors, including incompatible welding materials, poor joint fit-up, and overwelding. Planning before welding can help prevent distortion. Plan to distribute the heat evenly across the joint with a balanced welding sequence that minimizes localized heating and cooling. It’s best to properly align the joint edges so that there’s an adequate gap and fit-up between the materials and to size the beads to match the joint requirements. Minimizing welding heat input and performing post-weld heat treatment can also help control distortion.
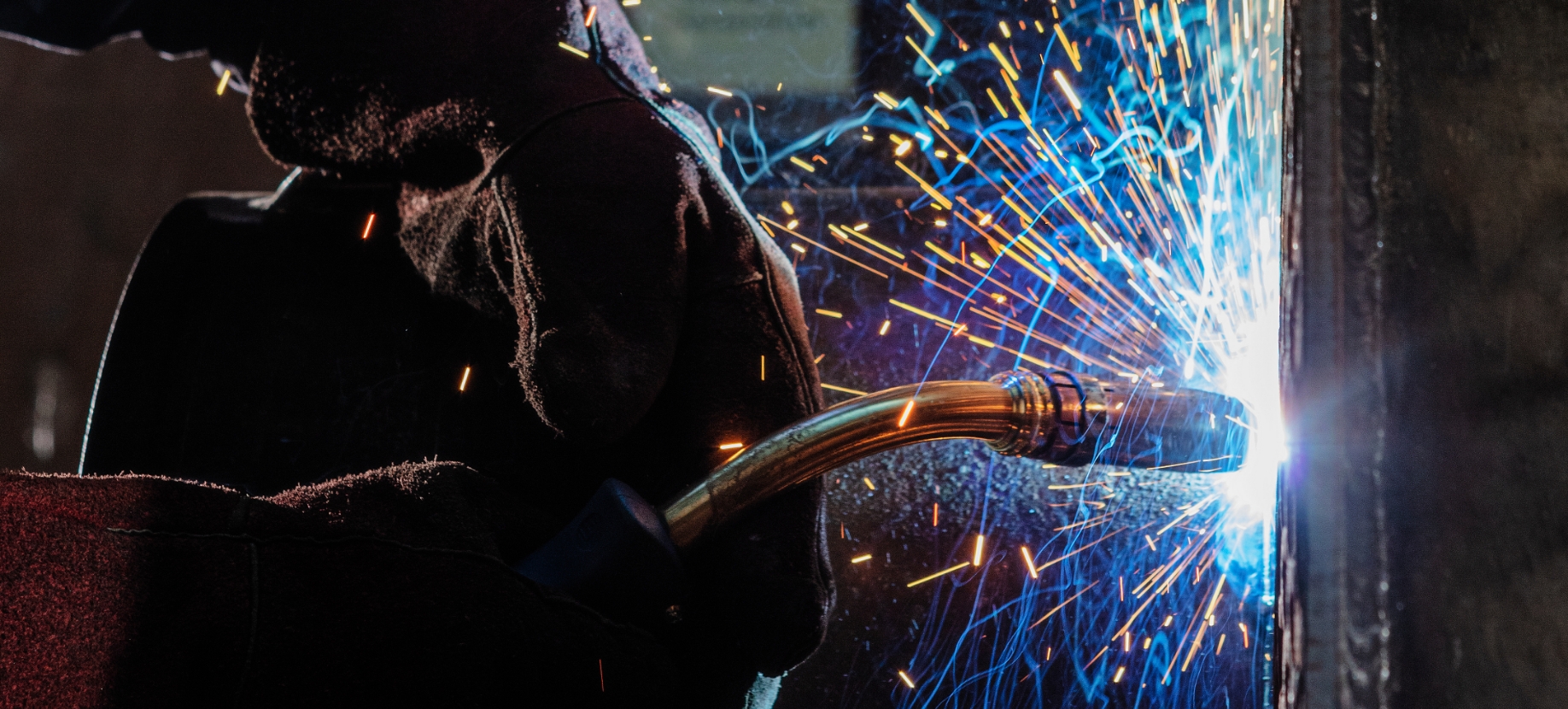
PRACTICE Your Carbon Steel Welding
Only through practice can you improve your skills and expand your experience with carbon steel welding. Carbon steel is generally cost-effective, so it’s easy to get your hands on some sample pieces to work on in your spare time. Examine each weld carefully and see if there are any signs of porosity, distortion, cracking, or other noticeable defects. Take note of what welding parameters you used: technique, position, voltage, welding wire, etc. What do you think caused that problem, and what can you do differently to prevent it on future welds?
Don’t forget that you have an entire community of fellow welders eager to share their own tips and tricks that they have developed over their careers. Maybe you have discovered some tricks of your own that you may want to share to help improve other welders’ experiences. Browsing online communities and forums is an excellent way to increase your welding spectrum, get in touch with beginners and veteran welders alike, and learn more about your craft.
NS ARC Quality Welding Wire for Carbon Steel
As previously mentioned, the welding wire is one of the most vital components in a successful welding job. It is crucial to use a strong and reliable welding wire to do the job properly, so the ideal choice would be NS ARC welding wire, which is engineered by our experts to promote significant weld strength, smooth feedability, and exceptional weldability. We carry a wide selection of various types, including carbon steel welding wire and flux-cored welding wire.
Our Copper-Glide™ copper-coated welding wires offer enhanced electrical conductivity and smooth wire feeding. If the project is sensitive to copper contamination, our Silver-Glide™ CopperFree™ welding wires are an excellent choice as they produce less spatter and minimal heat input for less burn-through risk. If you’re looking for a completely different type of welding wire, then our Tru-Core ® flux-cored welding wire is the answer with its higher deposition rate for improved productivity. Contact us now to learn more about our high-quality welding wire solutions.
Get a more in-depth look at the different flux-cored welding wires that can be used for carbon steel welding with our informative guide!
Learn MoreDISCLAIMER: This information is descriptive in nature and not purely prescriptive. Refer to your own welding machine’s user manual for proper settings and consult a welding expert for support.