Best Welding Wires for Carbon Steel
Oct 20th 2023
Carbon steel is a versatile and common material that is utilized in a wide range of industries, from construction and manufacturing to automotive and energy. Its strength and formability make it one of the most reliable and easy-to-use types of materials. However, to utilize carbon steel to its fullest extent, it requires the right set of tools, especially the ideal type of welding wire that can help create the strongest weld on the material.
There is a wide variety of welding consumable types that are engineered from different materials in various diameters and lengths for different welding processes (MIG, TIG, FCAW, SMAW, etc.). However, which one is the arguable best welding wire for working with carbon steel? In this article, we’ll explore what is the definitive best welding wire when it comes to achieving the ideal weld on carbon steel materials.
Why the Right Welding Wire Matters
In most cases, the welding wire is the heart of the weld. It works together with the rest of the welding equipment to achieve a reliable fusion between two materials that supports the rest of the structure. It plays a crucial role in determining the strength of the weld along with its integrity and overall quality.
Using the wrong welding wire can lead to disastrous results. An incompatible wire can cause poor weld quality, including inadequate penetration, incomplete fusion, and improper bead appearance, compromising the strength and durability of the weld. Welding defects are also a common result, such as porosity, cracking, or excessive spatter.
A weak weld can lead to defects in the material, which can lead to costly repairs. Substandard welds will need to be repaired or redone, which is not only a waste of time and materials, but also increases project costs. The additional time and effort that needs to be taken to correct the issue can also lead to decreased productivity and project delays.
Factors to Consider When Selecting Your Welding Wire
Your choice of welding wire is influenced by a number of factors regarding your welding project. It is important to understand the application first, whether it’s automotive manufacturing, shipbuilding, heavy equipment, or general fabrication. You need to consider exactly what kind of challenges the welds are going to undergo and if the welding wire can create the strong welds that can endure.
Carbon steel grade is also a factor as different grades have varying compositions, and the welding wire should complement the base metal. These grades can be divided into three categories: low carbon steel, or A36; medium carbon steel, or A516; and high carbon steel, or A572. Additionally, thinner or thicker carbon steel sections require different wire diameters for proper penetration. There’s also the joint’s configuration and design, including bevels or gaps, that plays a factor in the selection process.
The Definitive Best Welding Wire for Carbon Steel Welding
One of the most common welding wires, and one that is the most go-to reliable choice for any welder for nearly any kind of applications, is the ER70S-6. When it comes to welding carbon steel, this type of welding wire brings the much-desired versatility and excellent performance that helps create a solid and reliable weld. Containing silicon and manganese for good arc stability and minimal spatter, this welding wire provides smooth, clean welds.
This type of welding wire is compatible with nearly any carbon steel grade, including low-alloy steels and medium and some high carbon steels. It’s primarily used in MIG welding processes and is suitable for single-pass and multi-pass welding. When welding with this wire, it’s used with a shielding gas, typically a mix of argon and carbon dioxide or pure carbon dioxide.
The versatility, ease of use, and ability to produce high-quality welds are what make the ER70S-6 the ideal choice for a wide variety of welding applications. It’s easy to find and is available in a range of diameters, lengths, and material types, including copper-coated and copper-free.
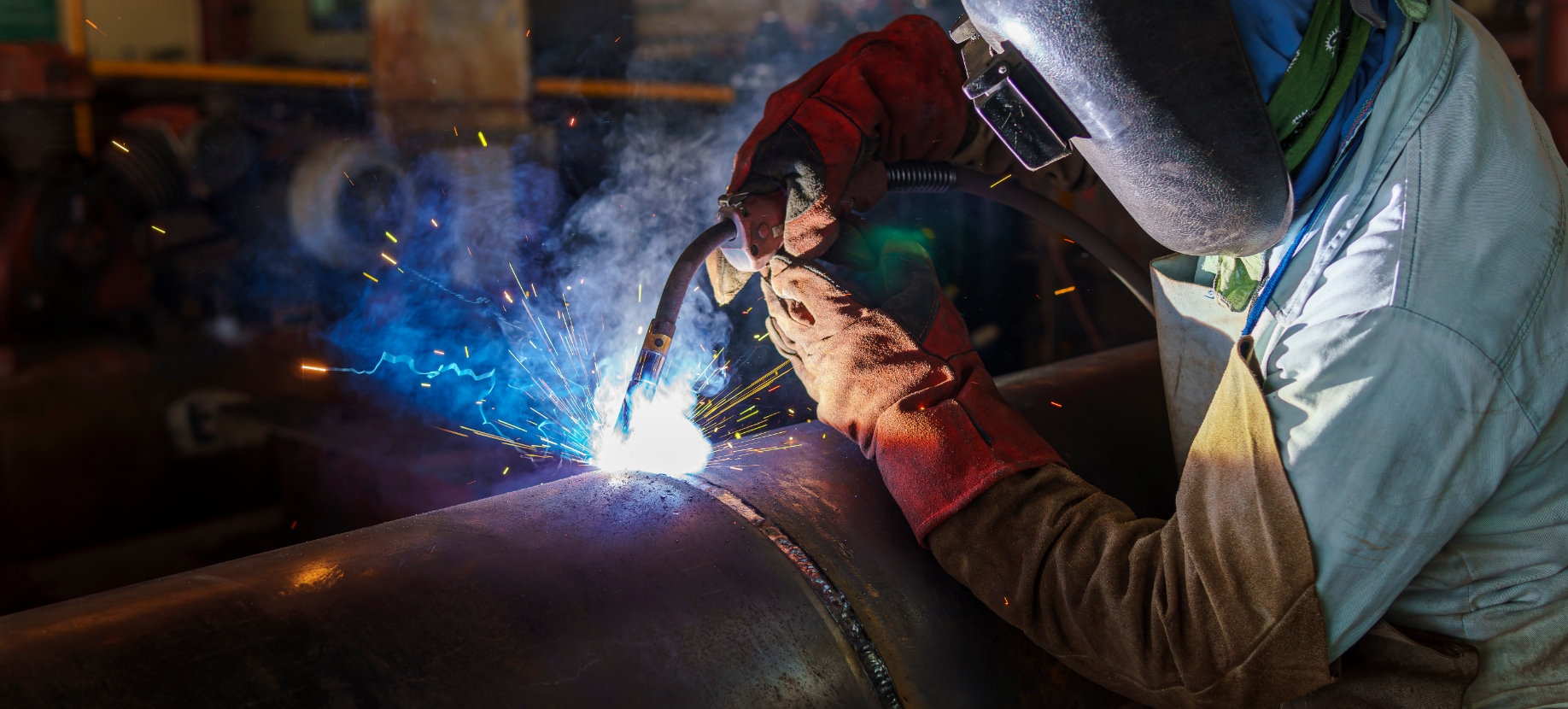
How to Make Your Choice – NS ARC Quality Welding Wire
Although the ER70S-6 is the widely used type of welding wire in the industry, the truth is that there is no definitive answer of which is truly the best welding wire for welding carbon steel. Selecting the best welding wire for carbon steel depends on the specific welding conditions and on your project's requirements, and the next project may differ from the last.
NS National-Arc™ Copper-Glide™ NS 115 Copper-Coated Welding Wire from NS ARC is an excellent choice for ER70S-6 applications as it offers unparalleled versatility and produces clean welds when working with carbon steel. On the other hand, Tru-Core® FC 71T Flux-Cored Welding Wire excels in high-speed applications and provides good penetration for FCAW operations on carbon steel.
Copper-Glide™ NS 115 provides good arc stability and smooth welding performance while Tru-Core® FC 71T provides high deposition rates and deep penetration. However, neither is the definitive “best” welding wire as both options have their advantages and provide exceptionally unparalleled weld results in various applications.
Consult the NS ARC Pit Crew if you’re unsure of which type of welding wire best suits your specific project, and our team of experts can guide you through our selection of wires. By carefully considering the numerous factors that go into the decision-making process, you can select the right welding wire to achieve strong, reliable welds and meet the demands of your carbon steel welding projects.
DISCLAIMER: This information is descriptive in nature and not purely prescriptive. Refer to your own welding machine’s user manual for proper settings and consult a welding expert for support.