Top Welding Wires for Mild Steel Welding
Dec 13th 2023
The choice of which welding wire to use for welding mild steel plays a significant role in determining the overall quality and strength of your weld. At the heart of the weld, it ensures that the pieces of mild steel are reliably joined together and that the resulting weld is strong enough to endure the heavy-duty demands and pressures of the job.
There is no one-size-fits-all welding wire solution that encompasses every kind of mild steel application in various industries. There is no “best” welding wire on the market, but there is the “best” welding wire solution that fits the numerous factors that need to be taken into account when choosing a wire for your specific application. Here, we’ll list some of the top welding wires for mild steel welding, taking into account the different factors that make them the most suitable choice for your particular requirements.
Solid Carbon Steel Welding Wires
When it comes to MIG welding mild steel, some of the most popular types of welding wires are solid carbon steel welding wires. Welders often rely on these wires since they effectively produce high-quality and high-performing welds, making the job a lot easier. Offering exceptional weldability, carbon steel welding wires can be categorized into two types: copper-coated and copper-free.
Copper-Coated Vs. Copper-Free
Copper-coated welding wires are known for their ability to produce stable arcs for more consistent welding and smoother weld bead appearances. The copper coating offers enhanced electrical conductivity and corrosion resistance, which helps improve the overall quality of the weld results.
Copper-free welding wires, on the other hand, are often preferred for applications in which copper could be a contaminant. They’re known for producing less spatter for a cleaner weld while also providing good arc characteristics and smooth wire feeding. This type of wire is also known for being a more environmentally friendly alternative since it does not release as many copper particles into the air during welding.
ER70S-6 Welding Wire
One of the most popular types of carbon steel welding wire is ER70S-6, which is available in both copper-coated and copper-free types. This welding wire contains higher levels of manganese and silicon, offering deoxidizers that make it a reliable choice for working with dirty and grimy surfaces of mild steel. It offers superior performance and an ease of weldability, allowing welders to achieve high-quality welds with smooth bead appearance using minimal effort.
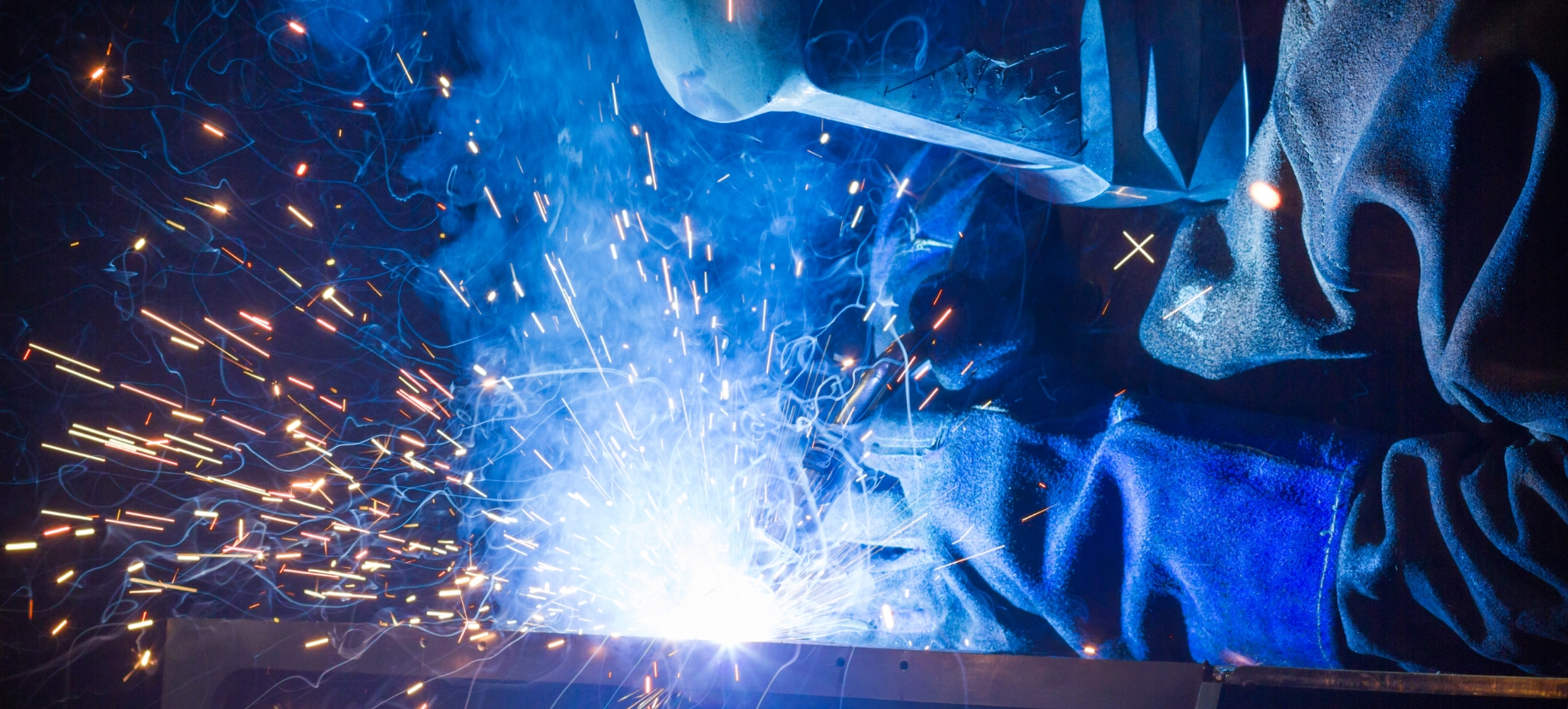
ER70S-3 Welding Wire
The ER70S-3 welding wire, which is also available in both copper-coated and copper-free options, is very similar to ER70S-6 but with lower levels of manganese and silicon. With its enhanced weldability, it’s well suited for single- and multi-pass welds. Popular in the automotive and construction industries, where the parts will be coated post-welding, this type of welding wire offers excellent penetration and smooth wire feeding for effectively efficient welding.
Flux-Cored Welding Wires
Ideal for the thicker sections of mild steel, flux-cored welding wire delivers superior penetration and increased deposition rates for higher productivity. This type of wire contains a flux compound that provides shielding that helps remove impurities from the weld. It can typically be used for all-position welding, bringing an increase in versatility to the jobs that require more flexibility when welding.
E70T-1 Welding Wire
The E70T-1 is a common gas-shielded flux-cored welding wire that offers high tensile strength and excellent impact resistance. A reliable choice for applications that require heavy demands, such as structural steel or heavy fabrication, this type of welding wire can be used for both flat and horizontal welds. It is known for providing good bead appearance and high travel speeds on mild steel materials.
E71T-1 Welding Wire
For a more versatile option, there’s the E71T-1 gas-shielded flux-cored welding wire that is capable of all-position welding. Offering increased travel speeds and producing flatter bead profiles, this type of welding wire is commonly utilized in general fabrication, pipe welding, and shipbuilding. This flux-cored welding wire is known for its great weldability and deep weld penetration capabilities. It also features a higher tensile strength and helps reduce the risk of porosity for cleaner welds.
Metal-Cored Welding Wires
Metal-cored welding wires are another tubular type of welding consumable that generates a smooth and stable arc for a consistent bead profile. This type of welding wire offers superior deposition rates, which means an increase in efficiency for more productive welding projects. Unlike flux-cored welding wires, metal-cored wires don’t produce slag, which means there’s less time spent on post-weld cleanup.
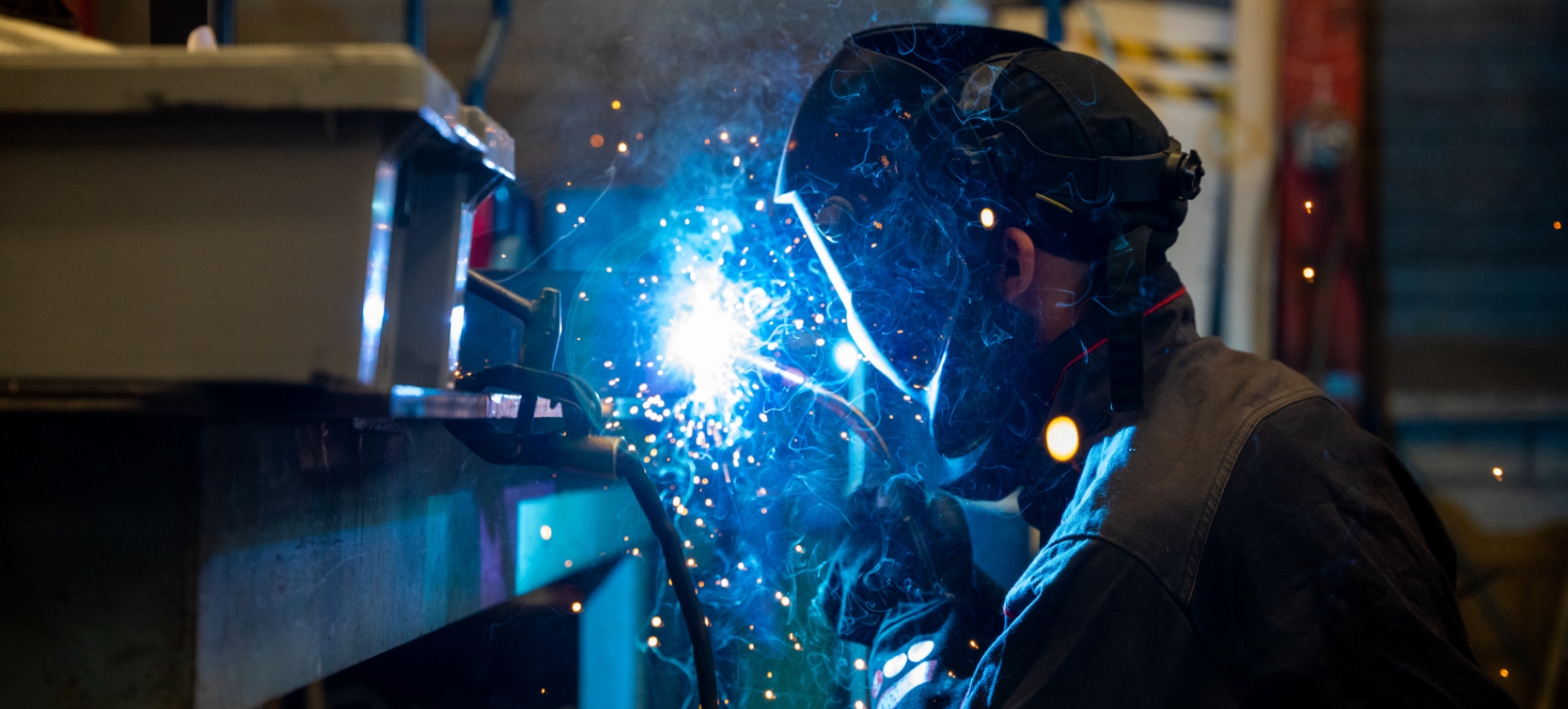
E70C-6M Welding Wire
The E70C-6M gas-shielded metal-cored welding wire is an excellent choice for working with mild steel. It features excellent mechanical properties and feedability while producing smooth arc transfers at high deposition rates. It offers quicker, cleaner welding for higher efficiency and productivity. A versatile option, this welding wire is best suited for heavy-demanding applications, including automotive manufacturing and heavy equipment.
E80C-Ni1 Welding Wire
Offering a higher tensile strength, the E80C-Ni1 type of gas-shielded metal-cored welding wire is a reliable choice for handling mild steel. Engineered to deliver optimal quality to the welding job, its unmatched flexibility and performance help it produce strong and reliable welds. Featuring flat bead geometry and smooth arc transfer, it allows for slag-free welds for easier cleanup and increased productivity.
The Influence of Mild Steel Thickness on Welding Wire Diameter
One of the most important deciding factors of your welding wire selection is the thickness of your mild steel. This outwardly determines the size of the welding wire you’ll be using for the job. To put it simply, the thicker the material, the larger the welding wire diameter.
Thicker mild steel requires more heat for proper penetration and fusion, so you need a robust, larger-diameter welding wire that will carry the current necessary to effortlessly penetrate to the root of the mild steel. For sections of mild steel that are about 1/8” to 3/8” thick, a 0.035” to 0.045” welding wire would be a good choice.
Thinner mild steel, though very forgiving of heat, is still susceptible to distortion caused by excessive exposure to heat during welding. When dealing with thinner sections, you need precise control over the heat input, so a more versatile, smaller-diameter welding wire would be your best choice. For sections of mild steel that are about 24-gauge to 14-gauge, a 0.025” to 0.030” welding wire would work ideally.
As you can see, mismatching the diameter of the welding wire and the thickness of the material can lead to a lot of welding issues. Using a large wire on thin mild steel can cause burn-through while using a small wire on thick material can cause inadequate penetration. The structural integrity of the weld relies on this type of compatibility between the welding wire and the mild steel.
NS ARC Quality Mild Steel Welding Wires
Welding mild steel properly requires the right kind of equipment that can create reliable and solid welds that can sustain heavy impacts and highly demanding applications, which is exactly what you get from NS ARC welding wires. We carry a wide selection of welding wire that is engineered to provide unmatched strength when it comes to welding mild steel properly. Whether you need copper-coated, copper-free, flux-cored, or metal-cored, our extensive expertise can guide you toward the ideal solution for your application.
Our Copper-Glide™ copper-coated welding wires are an excellent option for those seeking greater electrical conductivity and smoother wire feeding. Our Silver-Glide™ CopperFree™ welding wires are an exceptional environmentally friendly alternative that offers good arc characteristics and superior feeding performance.
For FCAW welding, our Tru-Core ® flux-cored welding wires give the advantage of higher deposition rates and deeper penetration. Alternatively, our Tru-Core® metal-cored welding wires provide improved productivity at faster travel speeds. Contact us today to explore each option we have to offer.
For a more in-depth look at welding wires that best suit other types of carbon steel, check out our informative guide!
Learn MoreDISCLAIMER: This information is descriptive in nature and not purely prescriptive. Refer to your own welding machine’s user manual for proper settings and consult a welding expert for support.