When to Use Copper-Free Welding Wire
Sep 7th 2023
When faced with the decision of using copper-coated or copper-free carbon steel welding wire, the choice depends on various factors, such as the welding process, material type, and specific application. Seeking guidance from welding experts or reference materials is advised, and the NS ARC Pit Crew team is readily available to offer information and tips for your welding projects.
Selecting between copper-coated and copper-free welding wire is a pivotal decision that hinges on the unique demands of each welding application. Copper-coated welding wire's enhanced electrical conductivity and corrosion resistance make it a go-to option in certain scenarios, while copper-free welding wire's focus on weld quality, health and safety, and environmental responsibility renders it preferable in specific applications. Below, we’ll dive into the nuances of both options to empower welders to make an informed decision.
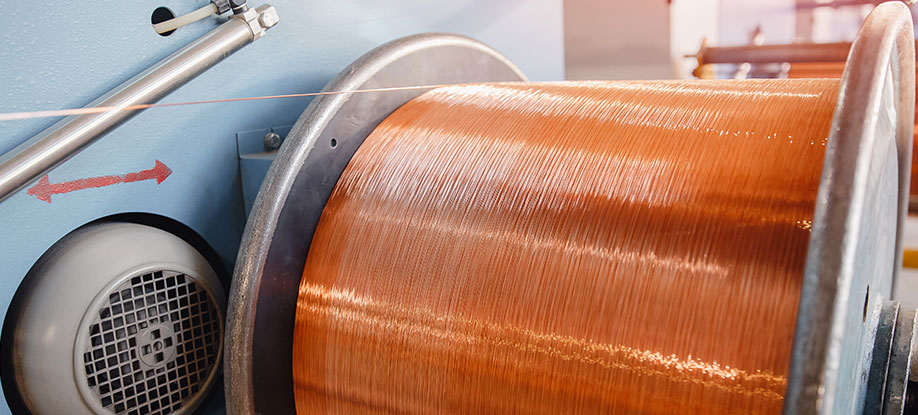
The Advantages of Copper-Coated Carbon Steel Welding Wire
Copper-coated carbon steel welding wire comes with several distinct advantages that make it the optimal choice in certain applications. The inclusion of a copper coating on carbon steel welding wire not only introduces enhanced electrical conductivity but also acts as a catalyst for improved overall weld quality. The inherent properties of copper work harmoniously with the welding process, elevating the fusion of materials and significantly minimizing the risk of potential defects.
The corrosion-resistant characteristics of copper also come into play to act as a protective barrier that safeguards the wire against deterioration. This attribute becomes especially important when considering applications where the carbon MIG welding wire might encounter moisture or humidity before being utilized. Another advantage is the smooth and consistent wire feeding facilitated by the copper coating, which helps to provide precise control over the welding process. The synergy between the copper coating and the welding process creates an environment conducive to achieving consistent and reliable welds.
What Are Some of the Most Common Applications for Copper-Coated Welding Wire?
Copper-coated carbon steel welding wire finds diverse applications across industries, from agricultural equipment and auto body repairs to automotive and general fabrication. Its corrosion resistance suits marine applications, while its strength serves heavy equipment fabrication and pressure vessel construction. In railcar manufacturing and structural projects, it excels in producing robust bonds. Additionally, this wire is favored for welding thin-gauge metals, high-speed automation, and high-strength steel due to its stability and electrical conductivity. These versatile applications underscore its essential role in a wide range of welding scenarios.
The Advantages of Copper-Free Carbon Steel Welding Wire
Copper-free carbon steel welding wire stands as a trustworthy alternative to copper-coated wire, offering a comprehensive array of benefits that can significantly enhance welding performance for certain applications. One of the key advantages offered is elevated weld quality, which ensures not only strong bonds but also structural integrity. Post-welding cleanup can also be reduced with the right settings and procedures.
Moreover, copper-free welding wire may be the best choice when health factors are considered since copper can be an irritant with potential health hazards when inhaled or ingested. Opting for copper-free wire minimizes these risks for welders and individuals in the surrounding area, making it an astute choice, particularly when working within confined spaces.
NOTE: Always insure and utilize proper PPE. Also, proper ventilation is recommended when using copper-coated welding wire to minimize the risk of these complications. Opting for copper-free welding wire also aligns with environmental consciousness as copper, being a heavy metal, can carry potential toxicity for the environment. By selecting copper-free welding wire, the release of potentially harmful copper into the ecosystem is mitigated, which can help welders and welding businesses comply with stringent environmental regulations.
Certain welding techniques, like Gas Tungsten Arc Welding (GTAW) or Tungsten Inert Gas (TIG) welding, require the utilization of copper-free carbon steel welding wire to achieve desired outcomes. In instances where these methods are employed, the choice to use copper-coated welding wire might not be available. Always consult manufacturer recommendations to determine if copper-free welding wire is the right choice for your particular project.
What Are Some of the Most Common Applications for Copper-Free Welding Wire?
Copper-free carbon steel welding wire is the welding wire of choice for a select range of applications and industries. It plays a pivotal role in the agricultural sector and is crucial for welding frame components, fuel tanks, and engine mounts, necessitating robust strength and dependability.
In automotive repair, this wire is a preferred choice for joining body panels and thin-gauge metal parts, ensuring durable welds that uphold structural integrity. Its significance also extends to general fabrication applications, including structural steel and machinery components. In industries like oil and gas, copper-free wire excels in pipe welding where it generates clean and precise welds without spatter.
Contact NS ARC Today for a Copper-Coated or Copper-Free Welding Wire Sample
If you're ready to experience the superior performance of our copper-coated or copper-free welding wires firsthand, don't hesitate to get in touch with us. We understand the value of finding the perfect welding solution to match your specific application, and we're here to help. Whether you're looking to enhance weld quality or improve efficiency, our team of experts is ready to listen to your unique situation and provide tailored assistance. Contact NS ARC today and we'll provide you with a sample welding wire spool that aligns with your welding project requirements and provides the quality necessary to get the job done right.
Try out the difference between copper-coated and copper-free welding for yourself. Order a sample today!
DISCLAIMER: This information is descriptive in nature and not purely prescriptive. Refer to your own welding machine’s user manual for proper settings and consult a welding expert for support.