How Welding Affects the Properties of Stainless Steel
Aug 28th 2023
Stainless steel is an iron-based alloy that is known for its natural resistance to corrosion and rust. It contains variable amounts of chromium, which gives stainless steel its resistance as it creates a passive film that can protect the material and self-heal in the presence of oxygen. The degree of chromium can vary from 11% to 30%, and each variation can have slightly different chemical compositions that influence how the material performs during the welding process.
Stainless steel is a versatile and widely used material in various industries due to its excellent corrosion resistance and durability. However, when stainless steel is subjected to welding processes, its properties can be significantly affected. Welding can create profound changes to the material’s mechanical properties, corrosion resistance, and microstructure. Understanding these impacts is crucial for engineers, fabricators, and welders to ensure the integrity and performance of welded stainless steel components.
Changes in Mechanical Properties in Stainless Steel
Welding stainless steel can introduce changes in its mechanical properties, potentially affecting its strength, ductility, and toughness. The heat generated during welding causes localized melting and subsequent solidification, leading to the formation of the weld pool and the heat-affected zone (HAZ).
In the HAZ, the stainless steel experiences a rapid thermal cycle, resulting in the formation of various microstructures. These microstructural changes can lead to a reduction in mechanical properties. For instance, the weld and HAZ are susceptible to increased hardness, reduced elongation, and decreased impact toughness compared to the base metal. Therefore, careful consideration must be given to welding parameters and post-weld heat treatment to minimize these detrimental effects.
Learn more about how to handle stainless steel during the welding process and reduce distortion and warping through our handy guide: How to Weld Stainless Steel Without Warping.
Influence on Corrosion Resistance
One of the key advantages of stainless steel is its exceptional corrosion resistance. However, welding stainless steel alters its metallurgical structure, potentially affecting its resistance to corrosion. During the welding process, the material experiences thermal gradients and rapid cooling rates, leading to the formation of chromium carbide precipitates in the HAZ.
The presence of chromium carbides can deplete the chromium content near the grain boundaries, reducing the material's ability to form a protective passive layer. This phenomenon is known as sensitization and can render the stainless steel susceptible to intergranular corrosion. Proper selection of filler materials with low carbon content and post-weld surface treatments, such as pickling and passivation, can mitigate these effects and restore the stainless steel's corrosion resistance.
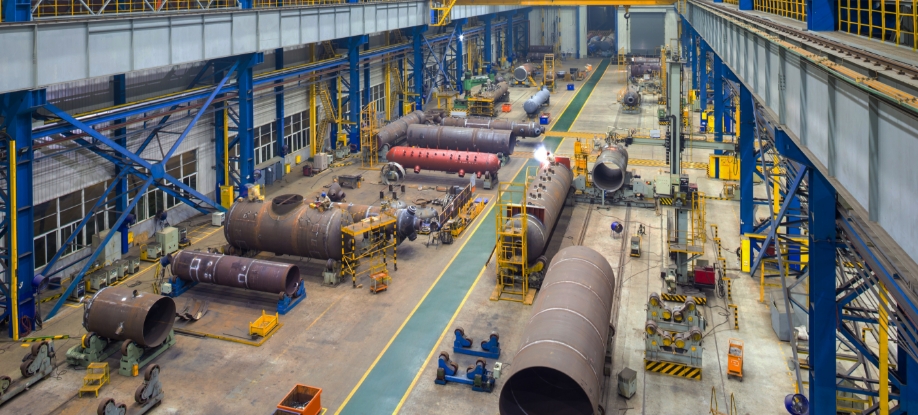
Microstructural Changes and Distortion
Welding introduces significant changes to the microstructure of stainless steel, affecting its mechanical and corrosion-resistant properties. The high temperatures during welding cause grain growth, which can result in coarser microstructures in the HAZ compared to the base metal. This change may lead to reduced mechanical strength and increased susceptibility to corrosion.
The localized heating and cooling cycles during welding can induce residual stresses and distortion in the welded components. If not properly controlled, these stresses can compromise the structural integrity of the welded stainless steel and lead to premature failures. Techniques such as preheating, controlled cooling, and the use of clamping devices can help minimize distortion and residual stresses.
Post-Weld Heat Treatment
Post-weld heat treatment is often employed to relieve residual stresses and restore the mechanical properties of welded stainless steel. The specific heat treatment process depends on the stainless steel grade and the desired properties. Annealing, solution annealing, and stress relieving are common post-weld heat treatment techniques used to optimize the microstructure and reduce residual stresses.
Additionally, post-weld heat treatment also plays a vital role in minimizing sensitization and restoring the corrosion resistance of stainless steel. Heat treatments that promote the reformation of the passive oxide layer and the dissolution of chromium carbides can effectively enhance the material's resistance to corrosion.
The Different Stainless Steel Grades
The five grades of stainless steel that have been classified according to their material properties and welding requirements are austenitic, ferritic, martensitic, precipitation hardening, and austenitic-ferritic (duplex). Each one possesses distinct material properties that significantly influence the welding process. Here’s a quick overview of each type and their distinctive characteristics.
Stainless Steel Grade | Composition | Crystal Structure | Welding Characteristics | Applications | Recommended Filler Metal |
Austenitic | 16-26% Cr 8-22% Ni |
Face-Centered Cubic (FCC) | Low Thermal Conductivity Hot Cracking Sensitivity Carbide Precipitation Susceptibility |
Aerospace Automotive |
Matching composition to base material, e.g., Type 308, Type 347 |
Ferritic | 10.5-30% Cr up to 0.20% C |
Body-Centered Cubic (BCC) | High Thermal Conductivity Low Carbon Content |
Appliances Coins Solar Heaters |
Matching or exceeding Cr level, e.g., Type 409, Type 430, Austenitic Types 309, 312 |
Martensitic | 12-18% Cr Low Ni up to 1.20% C |
Body-Centered Tetragonal (BCT) | High Hardenability Cracking Sensitivity |
Medical Tools Cutlery |
Chromium and carbon matching, e.g., Type 410, Type 308, Type 309, Type 310 |
Precipitation Hardening | 14-17% Cr 4-30% Ni Alloying Elements |
Varies | Heat Input Sensitivity Post-Weld Heat Treatment Required |
Aerospace Oil & Gas Energy |
Filler materials designed for precipitation hardening, e.g., 17-7 filler |
Austenitic-Ferritic (Duplex) | 22-26% Cr 4-7% Ni 0-3% Mo |
Mixed Austenite-Ferrite | Balanced Heat Input Intermetallic Phase Precipitation |
Pipelines Pressure Vessels Energy |
ER2209, ER2307, ER2553, ER2594 |
Now, let's dive deeper into how each grade affects stainless steel during welding.
Austenitic Stainless Steel: Formable & Reliable
Austenitic stainless steel, such as the commonly used 300 series, is highly popular due to its excellent corrosion resistance and formability. It typically has a composition within the range of 16-26% chromium (Cr) and 8-22% nickel (Ni). For example, Type 304 contains approximately 18% Cr and 10% Ni while Type 316 contains approximately 17% Cr and 11% Ni. This grade is non-magnetic and has a face-centered cubic (FCC) crystal structure.
Austenitic stainless steel is often utilized within the aerospace and automotive industries in which its strength and corrosion resistance is needed. They are typically welded with welding wires that have matching composition to the base material. However, there are some exceptions in which some alloys require the inclusion of a microstructure with some ferrite to avoid hot cracking. For example, a Type 308 filler metal should be used for welding Type 302 and Type 304 alloys while a Type 347 filler metal should be used for welding Type 321.
Ferritic Stainless Steel: Crack Resistant & Stable
Ferritic stainless steel is commonly found in the 400 Series. It typically has a composition within the range of 10.5-30% Cr and up to 0.20% C. Some types of this alloy, such as Type 430, are known for their good resistance to corrosion, especially in high-temperature environments. It has a body-centered cubic (BCC) crystal structure and is magnetic. The material properties of ferritic stainless steel affect the welding process as follows:
- High Thermal Conductivity: Ferritic stainless steel possesses higher thermal conductivity compared to austenitic stainless steel. This characteristic requires careful consideration of welding parameters to ensure proper heat distribution and prevent distortion. At high temperatures, it can undergo rapid grain growth, which can lead to brittle HAZ. This is especially so on thicker materials, so it’s recommended to weld on thin sections that are no less than 6mm. Employing a low heat input to minimize the width of the grain coarsened zone and introducing an austenitic filler can help produce a tougher weld metal in thick materials.
- Low Carbon Content: This grade of stainless steel typically has a lower carbon content, which reduces the risk of sensitization and intergranular corrosion during welding. However, it is still essential to select appropriate filler materials and control the heat input to avoid detrimental effects on the material's corrosion resistance.
To avoid most of the complications of welding ferritic stainless steel, it is recommended to weld in sections that are less than 6mm thick. This type of alloy is best utilized for the manufacturing of kitchenware, large domestic appliances, solar heaters, coins, and more. Filler metals used to weld ferritic stainless steel should match or exceed the Cr level of the base alloy. Type 409 and Type 430 are commonly used as fillers, and austenitic Types 309 and 312 can be used for dissimilar joints.
Martensitic Stainless Steel: Hard & Durable
Martensitic stainless steel, with Type 410 being one of the most common types, is valued for its high strength, hardness, fatigue resistance, and wear resistance. This alloy typically has a composition in the range of 12-18% Cr with low Ni but relatively high carbon content of up to 1.20% C. This grade has a body-centered tetragonal (BCT) crystal structure and is magnetic. The material properties of martensitic stainless steel influence the welding process as follows:
- High Hardenability: Martensitic stainless steel has high hardenability, which means it can easily undergo phase transformation and become hard and brittle when rapidly cooled during welding. Preheating, cooling control, using low hydrogen processes, and using post-weld heat treatment techniques (such as tempering) are necessary to prevent the formation of excessive martensite and ensure proper mechanical properties. Typically, low carbon thin sections that are less than 3mm can be welded without preheating if certain precautions are taken.
- Sensitivity to Cracking: Martensitic stainless steel is susceptible to cracking, especially in thick sections or if the material is improperly welded. It is crucial to carefully control the heat input, use suitable filler materials, and employ preheating techniques to minimize the risk of cracking. Immediate post-weld heat treatment can help toughen the structure as it enables the hydrogen to diffuse away from the weld metal and HAZ.
The wear resistance of this type of alloy is what makes it well-suited for the construction of medical tools and cutlery. When it comes to welding martensitic stainless steel, filler metals with chromium and carbon content should generally match the elements in the base metal. Type 410 filler as a solid welding wire or a cored welding wire can be used to weld Types 402, 410, 414, and 420 steels. For matching the carbon in Type 420 steel, Type 420 filler metals should be used. Additionally, Type 308, Type 309, and Type 310 austenitic filler metals can also be used to weld martensitic stainless steel to themselves or to other steels when toughness is required.
Precipitation Hardening Stainless Steel: Strong & Resilient
Precipitation hardening stainless steel is a unique category of stainless steel known for its excellent combination of high strength and corrosion resistance. These alloys can be strengthened through a precipitation hardening process, which involves heat treatment to promote the formation of fine particles or precipitates within the microstructure. This alloy typically contains elements such as approximately 14-17% Cr, 4-30% Ni, and sometimes other alloying elements like copper, aluminum, or titanium. The composition of these alloys plays a crucial role in their weldability and response to the welding process. Precipitation hardening stainless steels can be welded using conventional welding techniques such as TIG or MIG. However, due to their unique metallurgical characteristics, special considerations are necessary during welding:
Precipitation hardening stainless steels are often used in the oil and gas, nuclear, energy, and aerospace industries where high strength, corrosion resistance, and an acceptable level of toughness are needed. Selecting the appropriate filler material is crucial for welding precipitation hardening stainless steel. Ideally, the filler material should have a similar composition to the base metal to ensure compatibility and optimize the mechanical and corrosion-resistant properties of the weld joint. Filler materials specifically designed for precipitation hardening stainless steels are available, and their use is recommended to achieve the desired performance. For example, Grade 17-4 is commonly welded with 17-7 filler and can be welded without preheating.
Duplex Stainless Steel: Tough & Corrosion Resistant
Austenitic-ferritic stainless steel, also known as duplex stainless steel, offers a combination of the good cracking and corrosion resistance of ferritic and the high strength of austenitic. The typical composition of this type of alloy ranges from 22-26% Cr, 4-7% Ni, and 0-3% Molybdenum (Mo). It has a mixed microstructure of austenite and ferrite, providing unique welding challenges and considerations:
- Balanced Heat Input: Duplex stainless steel requires a balanced heat input during welding to maintain the appropriate ferrite-to-austenite ratio in the welded joint. The procedure to maintain the heat input range must be strictly followed during the welding process. Excessive heat input can lead to the formation of detrimental phases, such as sigma phase, which compromises the material's mechanical and corrosion-resistant properties.
- Intermetallic Phase Precipitation: Duplex stainless steel is susceptible to intermetallic phase precipitation, such as sigma and chi phases, during cooling. These phases can degrade the material's toughness and corrosion resistance. Proper heat treatment, controlled cooling rates, and the selection of suitable filler materials are essential to mitigate intermetallic phase formation.
Duplex stainless steels are often used in the construction of pipelines and pressure vessels, particularly in the energy industry, as well as having applications within the architecture and infrastructure industries. The selection of the filler metal should be well-researched beforehand. The choice heavily depends on the type of application and the properties of the welded material. The most common filler metals used for welding duplex stainless steel are ER2209, ER2307, ER2553, and ER2594.
Understanding the distinct material properties of each stainless steel grade enables welders and fabricators to choose the appropriate welding techniques, filler materials, and heat treatments to optimize the welding process and ensure the integrity and performance of the welded stainless steel components. Before welding, always make sure to consult the manufacturer’s recommendations and refer to experts, welding standards, and guidelines for specific applications.
Welding Stainless Steel
Welding has a profound impact on the properties of stainless steel and each of its different grades. The localized heating and cooling cycles during welding induce changes in mechanical properties, corrosion resistance, and microstructure. Understanding these effects is crucial for ensuring the reliability and performance of welded stainless-steel components. By carefully selecting welding parameters, understanding which grade to weld, employing suitable filler materials, and implementing appropriate post-weld heat treatment, welders, engineers, and fabricators can mitigate the adverse effects of welding and maximize the potential of stainless steel in various applications.
NS ARC Stainless-Steel Welding Wires
NS ARC carries a wide variety of different types of stainless-steel welding wire within our Satin Glide® selection. These exceptional welding wires offer superior corrosion resistance to ensure that the welded joints are not only durable but also capable of withstanding the harshest environments. Offering exceptional weld strength and high-temperature resistance, our stainless-steel welding wires are versatile enough to be utilized in various applications, including auto body repair, general fabrication, pipe welding, structural welding, and so much more.
If you’re interested in discovering more about how our Satin Glide® stainless-steel welding wire can benefit your welding operations, contact our dedicated team of experts. As the largest dedicated women-owned welding wire brand in the United States, we carry a wealth of knowledge and experience to share with you. Contact us today for advice, guidance, and assistance in selecting the right welding wire for your next project.
Check out our extensively comprehensive guide on stainless steel that provides tips, tricks, techniques, and more if you're looking to become a pro welder!
DISCLAIMER: This information is descriptive in nature and not purely prescriptive. Refer to your own welding machine’s user manual for proper settings and consult a welding expert for support.