How to Weld Carbon Steel: A Complete Guide
Oct 9th 2023
Welding carbon steel is an endeavor that nearly every welder encounters. Renowned for its strength, versatility, and widespread use in numerous industries, carbon steel is a top choice for various applications.
While welding carbon steel presents unique challenges, NS ARC has created this comprehensive guide that aims to provide you with valuable insights, comprehension, and essential tips for mastering carbon steel welding. Both novices and veterans can benefit from an in-depth look at what it takes to weld steel properly.
In this guide, we'll explore common questions, essential welding prep, the right kind of equipment required, and specific techniques for three popular welding methods: MIG, TIG, and flux-cored welding. From meticulous preparation to selecting the right welding wire, we'll arm you with the knowledge you need to conquer carbon steel welding challenges, produce high-quality welds, and harness the full potential of carbon steel in your upcoming projects.
Understanding Carbon Steel
Carbon steel is a versatile material that contains varying properties based on its carbon content. The level of carbon content directly affects the steel’s strength, hardness, and weldability.
There are three main types of carbon steel: low carbon steel, medium carbon steel, and high carbon steel. Each type features different characteristics that best suit different applications, so knowing and understanding which type is the right choice for the job can not only help you select the appropriate welding process, technique, and welding wire to use, but can also help prevent problems down the line.
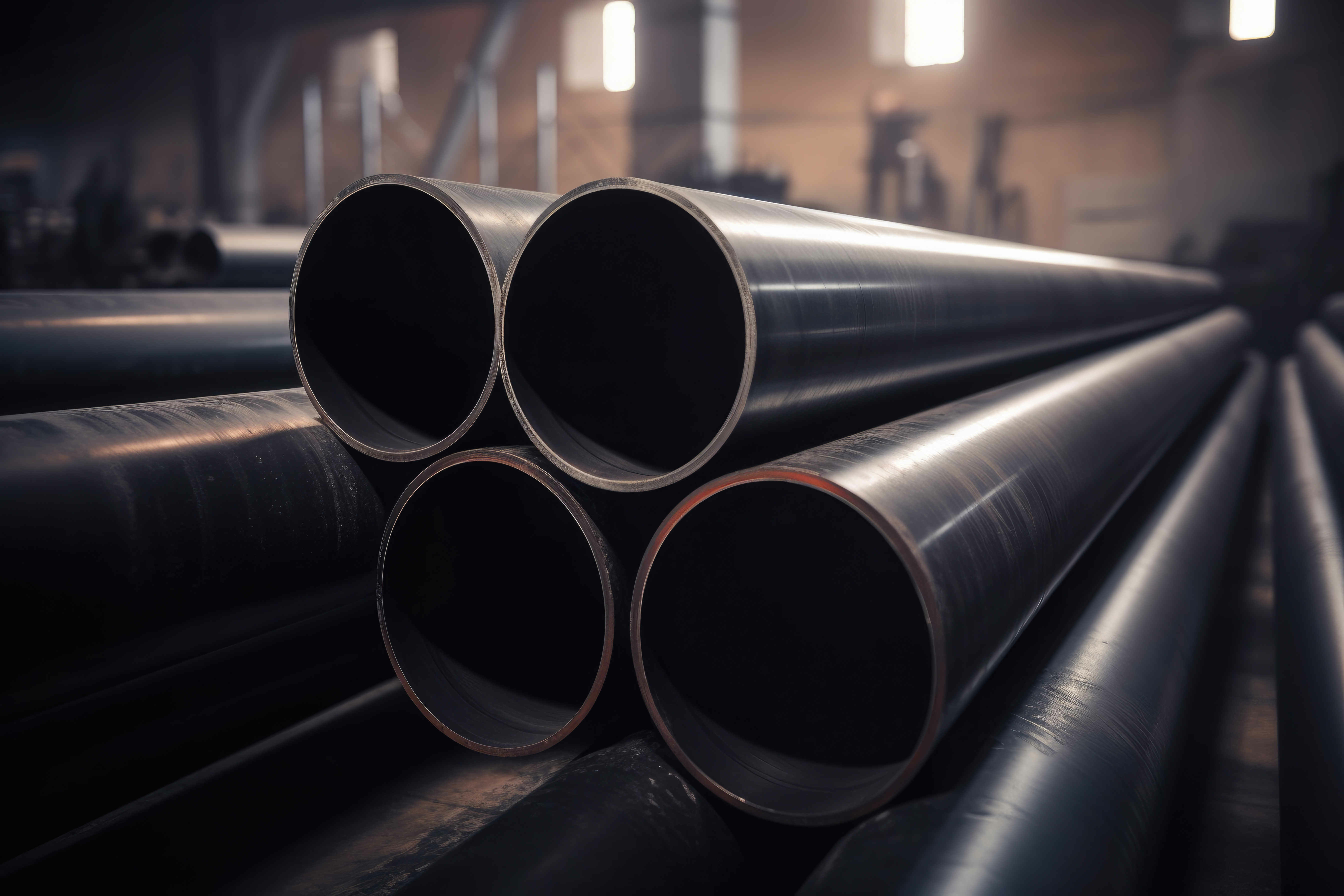
Low Carbon Steel
Low carbon steel, also known as mild steel, is one of the most commonly used materials due to its ease of fabrication and affordability. Containing 0.05% to 0.30% carbon, it has relatively low strength but high ductility, making it suitable for various welding applications. Low carbon steel is often used in construction, automotive components, and structural projects.
- Easily weldable due to its low carbon content and good ductility
- High formability and machinability
- Relatively low hardness, making it less susceptible to cracking during welding
- Excellent toughness, which helps resist impact and deformation
- Limited strength compared to higher carbon steels
Medium Carbon Steel
Medium carbon steel features a composition of about 0.30% to 0.60% carbon. Compared to low carbon steel, medium carbon steel offers increased strength and hardness, making it suitable for applications where higher mechanical properties are required, including pressure vessels, building structures, and railway tracks. However, medium carbon steel can be more challenging to weld due to the potential for cracking and reduced ductility.
- Higher tensile strength and hardness compared to low carbon steel
- Moderate formability and machinability
- Increased wear resistance and durability
- Reduced ductility and increased risk of cracking during welding
- Preheating and careful control of welding parameters are often necessary to prevent cracking
High Carbon Steel
High carbon steel is known for its exceptional hardness and wear resistance and features a carbon content range of 0.60% to 2.0%. It is commonly used for cutting tools, springs, and high-strength applications. While high carbon steel offers superior hardness, it is less weldable due to its brittleness and increased susceptibility to cracking.
- Excellent hardness and wear resistance
- Limited ductility and toughness
- Prone to cracking during welding due to brittleness
- Preheating and post-weld heat treatment may be necessary to prevent cracking
- Often used in specialized applications where strength and hardness are critical
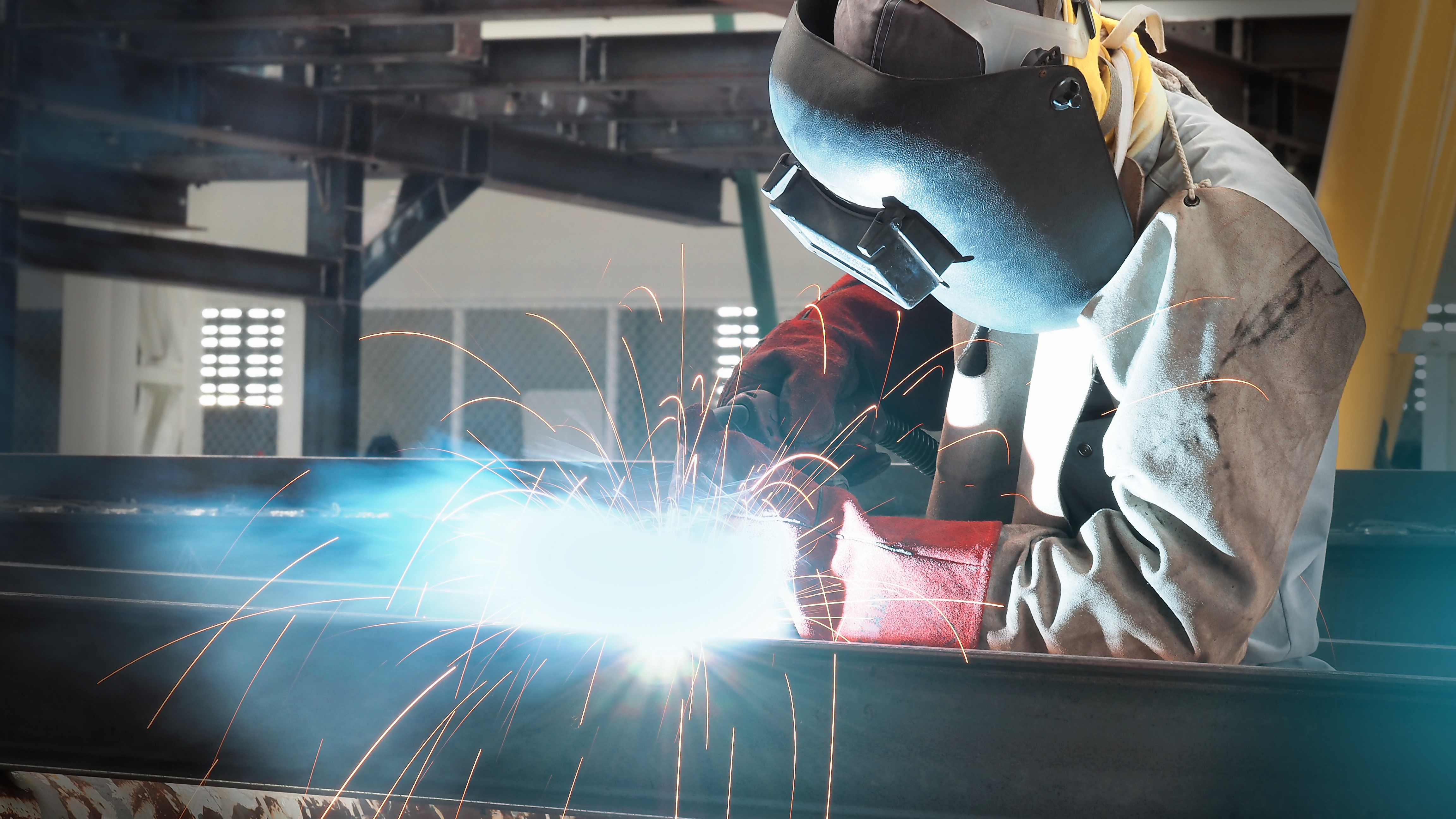
Common Questions on Welding Carbon Steel
Welders often have similar questions when it comes to handling carbon steel. It’s a common material that takes a bit of skill to fully control and manipulate through welding. Most of these questions involve which welding process is best used for working with carbon steel, how can a welder achieve good penetration and fusion, how to avoid cracking, and how to weld different levels of carbon steel thickness together.
Like any skill, welding takes time and dedication. Practicing the craft can help build experience over time, leading to a quicker, more confident welding result. Welders who are more skilled are more likely to recognize and identify potential issues and take preventive and/or corrective measures. Keep practicing, consult the manufacturer’s recommendations, and ask for helpful advice when needed.
What type of welding process is best for welding carbon steel?
The choice of which welding process is best for carbon steel depends on several factors, including the thickness of the material, the type of joint, the desired weld quality, and the available equipment. The three most common welding processes for carbon steel are Gas Metal Arc Welding (GMAW/MIG), Flux-Cored Arc Welding (FCAW), and Shielded Metal Arc Welding (SMAW). Let’s take a minute to explore each option.
GMAW is widely used by welders due to its efficiency and ease of use. It offers good control over the welding parameters while producing high-quality welds with minimum spatter. A versatile welding method, this option is suitable for a wide range of material thicknesses and joint configurations. This process requires a shielding gas, which is usually a mixture of argon and carbon dioxide for carbon steel welding, to protect the weld from atmospheric contamination. Check out our in-depth guide to MIG welding carbon steel specifically to learn more about this welding process.
FCAW is reserved for welding thicker carbon steel sections. Known for its deep penetration, it’s often preferred for structural and heavy-duty applications due to its high deposition rate and ability to handle large weld beads. The two types of FCAW are self-shielded (with no external gas required) and gas-shielded (which requires external shielding gas).
SMAW, which is commonly known as stick welding, is a versatile choice that is suitable for various carbon steel applications. It’s mainly ideal for welding thick carbon steel sections and can handle dirty or rusty materials. While this technique requires more operator skill than most others, it’s a reliable choice for its portability and adaptability.
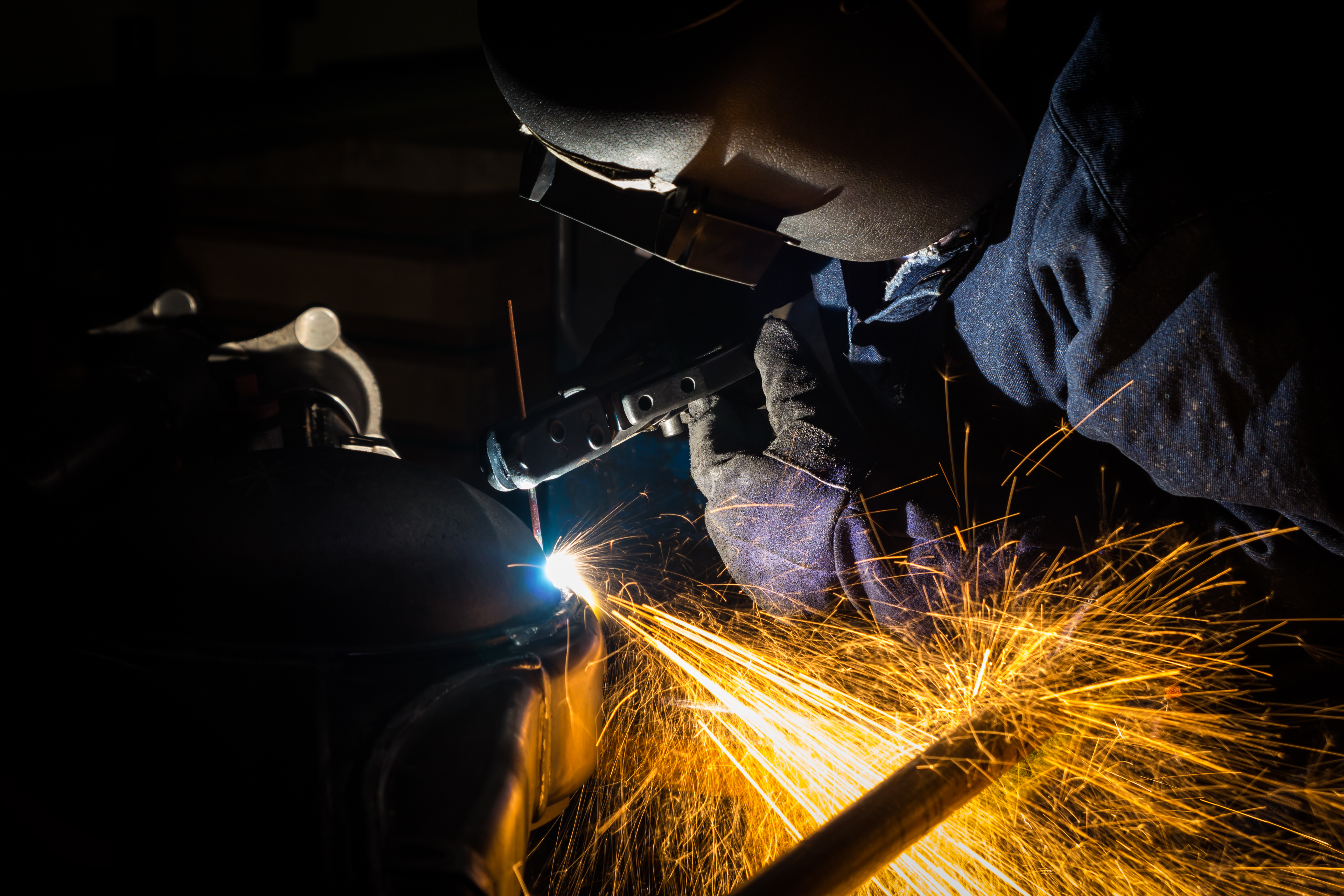
How do I achieve good penetration and fusion in carbon steel welds?
The following are useful tips, but only through a robust welding procedure can you ensure the results will produce a quality weld.
Achieving proper penetration and fusion in carbon steel welds is crucial to ensure strong and reliable joints. While welding, keep a consistent arc length between the electrode or welding gun and the workpiece. Too short an arc can result in excessive heat input, leading to burn-through or distortion. Too long an arc may cause insufficient penetration, leading to a weak weld.
Maintain a steady travel speed that allows the weld pool to properly fuse with the base metal. If you move too slowly, it can lead to excessive heat input, but if you move too quickly, it might result in incomplete fusion. Also, ensure there's a proper fit-up of joint parts to maintain a consistent root gap (if applicable). A proper root gap allows the weld metal to penetrate into the joint and create a strong bond.
How do you prevent weld cracking in carbon steel?
Before you begin the welding process, you need to ensure the joint edges are clean, properly beveled, and free of defects. Make sure that you avoid excessive root gaps, as they can lead to uneven heating and cooling, increasing the risk of cracking. Preheating the base metal before welding can help reduce the temperature gradient, and we recommend using the appropriate welding parameters, including current, voltage, and travel speed, to avoid excessive heat input.
While welding, maintain a consistent and steady welding technique for even heat distribution and uniform fusion. It’s best to avoid abrupt starts and stops since those can cause stress concentrations that can lead to cracking. We recommend using a peening technique or backstep sequence when welding longer sections. These techniques can help relieve residual stresses and reduce the risk of cracking.
Can you weld different thicknesses of carbon steel together?
While this is a common practice, it does require specific considerations and techniques to ensure a reliably strong weld. One proper thing to consider is to employ a technique that ensures good penetration in the thicker material while preventing burn-through in the thinner material, so we recommend welding from the thicker side to the thinner side, gradually decreasing the heat input as you move from one material to the other.
It’s important to maintain control over both the arc and the material. Tack welds can be used to hold the materials in place before making the final weld, maintaining proper alignment. Backing bars or copper backing can also support the weld and prevent burn-through in the thinner material. Once finished, as with any welding job, conduct thorough visual inspections and possibly non-destructive testing to ensure proper penetration, fusion, and weld quality.
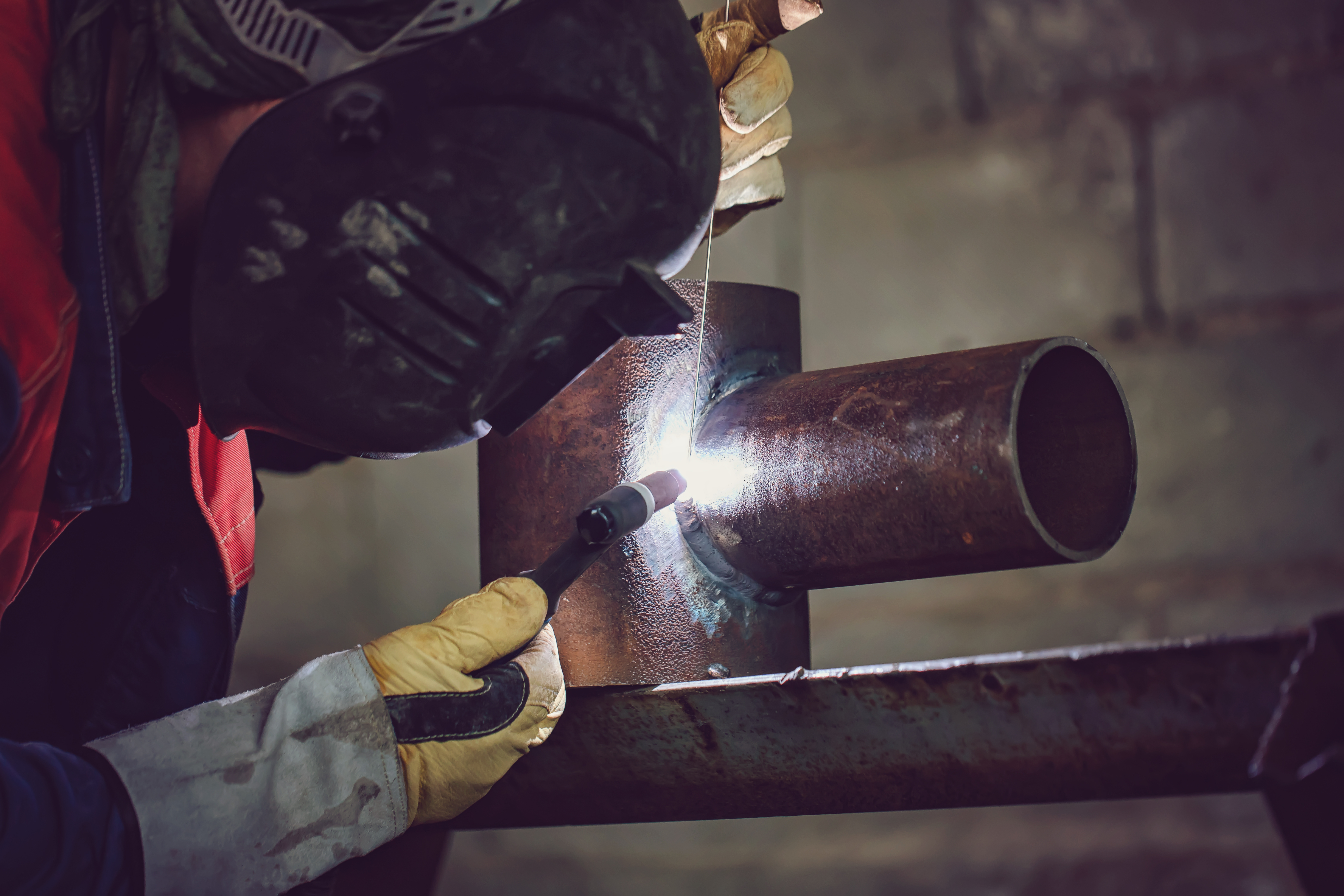
Recommended Welding Wires for Carbon Steel
The choice of the best welding wire for welding carbon steel depends on various factors, including the welding process and the specific application. Some of the most common welding wires that are utilized for this type of job fall under three categories: copper-coated welding wire, copper-free welding wire, and flux-cored welding wire.
Best Copper-Coated Welding Wires:
The presence of a copper coating on carbon steel welding wire enhances electrical conductivity and augments arc stability. This type of welding wire is best suited for GMAW and SAW processes, where a dependable, enduring, and consistently performing solution is required. However, it's worth noting that in scenarios where the inclusion of copper could potentially lead to problems, opting for NS ARC copper-free welding wire is advisable, as it can yield superior outcomes.
- ER70S-6: This is one of the most commonly used solid wires for welding carbon steel in GMAW/MIG processes. It offers good bead appearance, excellent arc stability, and minimal spatter. It contains higher levels of silicon and manganese, which enhance its arc stability and deoxidizing properties. It's suitable for a wide range of carbon steel applications, including automotive manufacturing, general fabrication, and structural construction.
- ER70S-3: Similar to ER70S-6 but with slightly lower levels of silicon and manganese, this welding wire is suitable for applications where lower silicon content is preferred, such as welding agricultural equipment and pipes. It is often used for welding carbon steel components that require improved ductility and minimal impact on the base metal's mechanical properties.
Best Copper-Free Welding Wires:
Copper-free carbon welding wire is an excellent choice to ensure high weld quality with superior safety and less risk to the environment. Using a copper-free carbon steel welding wire can lead to higher quality welds, overall higher operator satisfaction, and, when set correctly, reduced post-welding cleanup.
- ER70S-(3/6): Copper-free solid wires are selected in applications where copper contamination is a concern, such as in the food industry or where strict environmental regulations apply. ER70S-(3/6) is designed to provide excellent welding performance on carbon steel while eliminating the presence of copper. It maintains good weldability and reliability without the use of copper coatings.
Best Flux-Cored Welding Wires:
Flux-cored welding wires are known for their versatility and ease of use when it comes to working with carbon steel. They offer much more flexibility regarding welding position compared to other welding consumables as they can be used vertically and overhead. Additionally, their superior penetration means they’re far better suited to welding thicker sections of carbon steel materials.
- E71T-1: E71T-1 is a popular choice for FCAW of carbon steel. It features a tubular wire filled with flux compounds that provide the flux needed for the weld. E71T-1 is known for its high deposition rates and good penetration, making it suitable for applications where productivity is crucial. It can be used in various welding positions and is often preferred in heavy fabrication and structural welding. AWS requires this product to be qualified with CO2, but argon/CO2 mixes can also be qualified.
- E71T-GS: This self-shielded flux-cored wire is commonly used for hobbyist and light-duty welding applications, particularly when an external shielding gas is not available. It's known for its ease of use and is suitable for thin to medium-thickness carbon steel. E71T-GS is often chosen for outdoor or field welding where portability and simplicity are important.
- E70T-1: E70T-1 is an excellent choice for heavy-duty applications that require strong, impact-resistant welds. It offers exceptional mechanical properties and is often used in construction, transportation, and other demanding industries. E70T-1 is known for its ability to provide reliable welds in challenging environments.
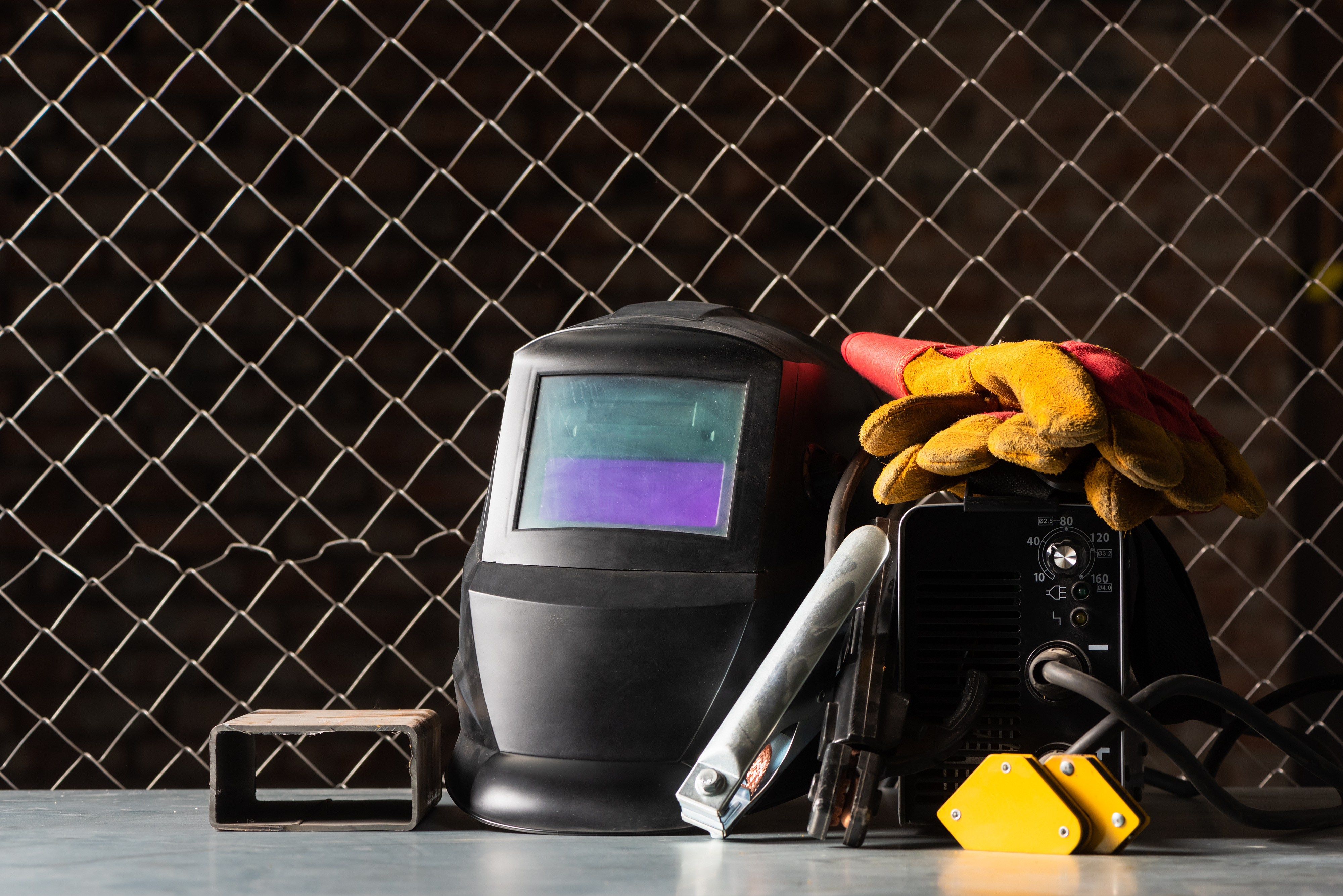
Tools & Equipment for Welding Carbon Steel
- Welding Machine: Choose the appropriate welding machine based on the welding process you'll be using (TIG, MIG, FCAW).
- Welding Wire/Electrodes: Choose the best suited welding wire or electrode for the job that is compatible with the carbon steel grade that’s being welded.
- Wire Brush: This is often needed to clean the surface of the material to remove mill scale, rust or paint before you begin welding to help prevent malformities in the weld that could lead to future weld failures.
- Temperature tracker: This can be an electronic infrared thermometer, electronic surface temperature probe, or temperature sticks used for ensuring proper pre/post heat and interpass temperatures.
- Welding wire feeder vs all-in-one integrated wire feeder for improved control: Welders who weld often or who work in a professional setting will have a separate wire feeder. A wire feeder that is integrated all-in-one is consistent with a casual or hobbyist welder.
Safety Equipment
Safety should always be a priority, so proper personal protective equipment (PPE) is essential to ensure your safety during the welding process. Before beginning, make sure that you are wearing the following:
- Welding Helmet with Darkened Lens rated for the amperage you will be welding
- Welding Jacket or Flame-Resistant Clothing
- Welding Gloves
- Steel-Toed Boots
- Welding Mask or Respirator for Fume Protection
- Ear Protection
- Safety Glasses
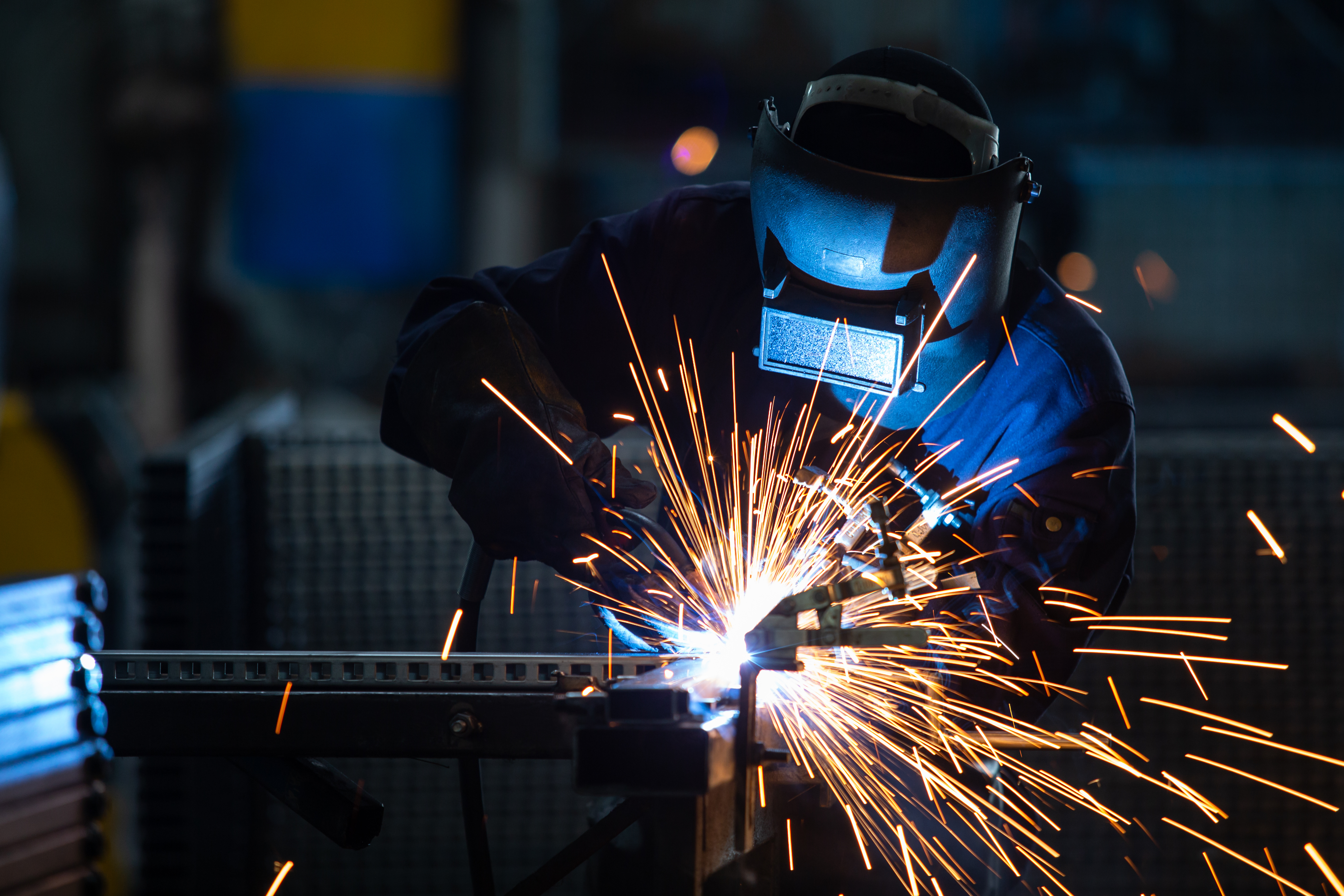
How to Weld Carbon Steel – Preparation & Tips
Welding with carbon steel involves several key steps and considerations to ensure a successful weld. Below is a step-by-step guide that details exactly what goes into the process and what any welder should be prepared for when they undertake the task. One of the most important things to remember is that you need to be fully focused when you’re welding. Maintaining a consistent arc length and keeping an eye on the heat input is crucial in order to prevent distortion or burn-through, which can result in a botched weld job.
Please note that welding carbon steel produces fumes containing harmful compounds like manganese and chromium. Before beginning, ensure proper ventilation and use fume extraction systems to maintain a safe working environment.
Before welding carbon steel, ensure you are wearing proper PPE, including your welding helmet, gloves, flame-resistant clothing, safety glasses, hearing protection, and boots. Make sure that you are also equipped with the type and grade of carbon steel that best suits your project's requirements. The material needs to be clean and free of contaminants like rust, paint, and grease.
The next step is to properly prepare the joint by cleaning the edges and ensuring they are free of defects. For thicker carbon steel materials, consider beveling or other edge preparations to allow for proper penetration. Align and fit up the joint accurately to ensure uniform welding and minimize distortion. Use fixtures, clamps, or jigs as needed to keep the joint firmly in place.
The base metal may need to be preheated before welding, especially if you’re handling thicker sections or are working in a cold environment. This can help reduce cracking. Welding parameters will also need to be adjusted, including the voltage, current, wire feed speed, and travel speed according to the manufacturer's recommendations and the specific welding procedure.
Begin welding and maintain a consistent arc length between the electrode or welding gun and the workpiece to ensure a stable arc and proper heat input. Keep a close eye on the heat input as excessive heat can lead to burn-through, distortion, or metallurgical changes. Don’t take your eyes off the job; ensure that the weld is penetrating and adhering to the joint. You’ll need a steady hand to control the motion, and you’ll need to use weaving (if applicable) to achieve an even bead appearance and fusion.
Once you’re done welding, you’ll need to remove any slag and spatter that may have accumulated using a chipping hammer and/or wire brush. The area should be cleaned thoroughly to inspect for defects such as cracks, porosity, or incomplete fusion. Using non-destructive testing, such as X-rays or ultrasonic, is recommended.
Here are some additional tips to consider while welding carbon steel:
Remember that becoming a proficient welder takes practice and experience. Any welder has the ability to continuously refine his or her techniques and adapt them to the specific requirements of each welding project. Keep practicing and follow best practices so that you can easily and effectively achieve high-quality welds when working with carbon steel.
Tips for MIG Welding Carbon Steel
- Weld Pool: The weld pool needs to be consistent and appropriately sized so that it isn’t too shallow or deep. It should be just large enough to ensure complete fusion but not excessively large, as this can lead to overwelding. A shallow pool may not penetrate adequately, while an overly deep pool can lead to a lack of control and potential defects.
- Welding Angle: For MIG welding, it’s important to maintain a work angle of around 10-15 degrees from perpendicular to the workpiece. This angle helps ensure good penetration while preventing excessive spatter. The travel angle, or push angle, should typically be around 5-15 degrees in the direction of the weld. However, this can vary based on joint type and personal preference.
- Travel Speed: The travel speed needs to be consistent. Too slow can result in excessive heat input and potential burn-through. Too fast may lead to insufficient fusion and poor bead appearance. The ideal travel speed depends on various factors, including material thickness, wire diameter, and welding parameters.
- Shielding Gas Coverage: The shielding gas flow rate needs to be set correctly according to the manufacturer's recommendations. Too little gas can lead to inadequate coverage, while too much can cause turbulence and spatter. Keep the nozzle or contact tip clean and free from spatter buildup, which can obstruct the gas flow and lead to poor shielding.
Tips for TIG Welding Carbon Steel
- Weld Pool: Maintain a consistent and appropriately sized weld pool. Similar to MIG welding, the pool should be just large enough for complete fusion but shallow enough to prevent overwelding. Control the heat input by adjusting the amperage to match the material thickness. Thicker materials generally require higher amperage.
- Welding Angle: Hold the torch at a work angle of around 15-20 degrees from perpendicular to the workpiece. This angle helps direct the heat into the joint for effective penetration. For fillet welds, position the torch at a 45-degree angle with the tungsten pointing toward the center of the joint.
- Travel Speed: As with MIG welding, maintaining a consistent and steady travel speed is essential. TIG welding is typically slower than other processes, but too slow or too fast can lead to defects. The ideal speed can vary based on material thickness and joint configuration.
- Shielding Gas Coverage: Ensure that the shielding gas flow rate is set correctly according to the manufacturer's recommendations. The typical gas used for this welding process is Argon, which provides a stable welding arc. It’s important to keep a consistent torch angle and distance from the workpiece to ensure uninterrupted shielding gas coverage over the weld pool.
Tips for Flux-Cored Welding Carbon Steel
- Weld Pool: Maintain a consistent and appropriately sized weld pool. It should be large enough for complete fusion but not excessively large. Adjust the welding parameters, such as voltage and wire feed speed, to control the size and shape of the weld pool.
- Welding Angle: Hold the gun at a work angle of around 15-45 degrees from perpendicular to the workpiece, depending on the joint type and position. For butt welds, the gun should have a 90-degree work angle and 5-15-degree travel angle. For lap joints, angle the gun 60-70 degrees to direct the heat into the bottom piece of the metal. For fillet welds, position the gun at a 45-degree angle with the wire directed toward the center of the joint. Typically, flat, horizontal, and overhead positions have a drag angle of 10-30 degrees while vertical welds have a push gun angle of 5-15 degrees.
- Travel Speed: Flux-cored welding is typically faster than other methods. However, like with other methods, the travel speed should be steady and consistent. Other factors, such as material thickness and joint configuration, can affect the speed. Experiment with different travel speeds to find the optimal rate for your specific welding application.
- Shielding Gas Coverage: Ensure the flux-cored wire you're using is designed for the specific shielding gas conditions you require (e.g., self-shielding or gas-shielded). Remember to maintain proper torch angle and distance from the workpiece to ensure adequate shielding and protect the weld from atmospheric contamination.
NS ARC Carbon Steel Welding Wires
For optimized welding performance, NS ARC offers a full selection of high-quality carbon steel MIG welding wires. Promoting superior strength, greater versatility, and effective compatibility, our carbon steel welding wires are an excellent choice for a wide range of welding applications, including automotive manufacturing, general fabrication, pipe welding, and so much more.
Our Copper-Glide™ copper-coated welding wire is engineered to provide improved electrical conductivity, corrosion resistance, and smooth wire feeding. On the other hand, our Silver-Glide™ CopperFree™ welding wire is a reliable alternative that offers great weld quality, promotes health and safety of the welder, and is excellent for environmental considerations. To learn more about our high-quality welding wire, contact the Pit Crew, our team of industry experts who can easily guide you through selecting the best welding wire for your next welding project.
We've compiled a list of handy tips and tricks when welding carbon steel. Check them out!
DISCLAIMER: This information is descriptive in nature and not purely prescriptive. Refer to your own welding machine’s user manual for proper settings and consult a welding expert for support.