Guide to Welding Grooves
Jan 24th 2024
Proper joint preparation and configuration are the keys to crafting some of the strongest and most durable welds, and among various configurations, welding grooves play a pivotal role in shaping the outcome of the weld. These specially crafted recesses or grooves are designed to provide the foundation for the deposit of molten metal and the welding wire to properly fuse the materials together during the welding process.
A welding groove enhances the strength and quality of the weld joint as it allows for better penetration of the welding wire into the joint. The design, shape, and dimensions of the groove depend on a number of factors, including material type and thickness, welding position, welding process, and joint configuration.
Welding groove types range from the straightforward square groove to the more complex double V groove. Each type offers different characteristics, and the choice of which welding groove is best for the application depends on the welding requirements and the materials. Proper preparation of the welding groove is essential for achieving a successful and structurally sound weld.
Understanding Welding Groove Symbols
The American Welding Society (AWS) established a standardized system of visual representations, known as AWS A2.4, for communicating the desired weld type, size, and other details. They’re commonly found on blueprints and technical drawings to convey this information to designers, engineers, and welders at a glance.
Understanding welding groove symbols is essential for interpreting welding blueprints and communicating the intended joint design. Groove symbols are graphical representations used in welding drawings to indicate the specific groove geometry and welding details.
Welding Groove Types: A Breakdown of Their Differences and Advantages
Welding grooves come in a variety of types that feature different shapes and configurations. When we delve into the unique characteristics of these grooves, we unravel the intricacies that are behind achieving precision and strength in welding. Whether you’re working in structural fabrication, automotive manufacturing, or pipe welding, understanding the diversity of welding grooves allows you to tailor your approach to meet the demands of these challenging welding applications.
Flare-Bevel Groove Weld
A flare-bevel weld is a type of butt joint in which the curvature of one or both pieces of metal causes one or both curved pieces to flare away from each other. This type occurs when welding a round, tubular, or curved metal directly to a flat piece. The curved piece causes a natural bevel that needs to be filled with the weld.
- Advantages: Creates a strong weld, doesn’t require excessive joint preparation, less likely to create distortion.
- Disadvantages: Suitable only for thicker materials, rounded edge that creates the groove can deflect heat toward the other piece of metal.
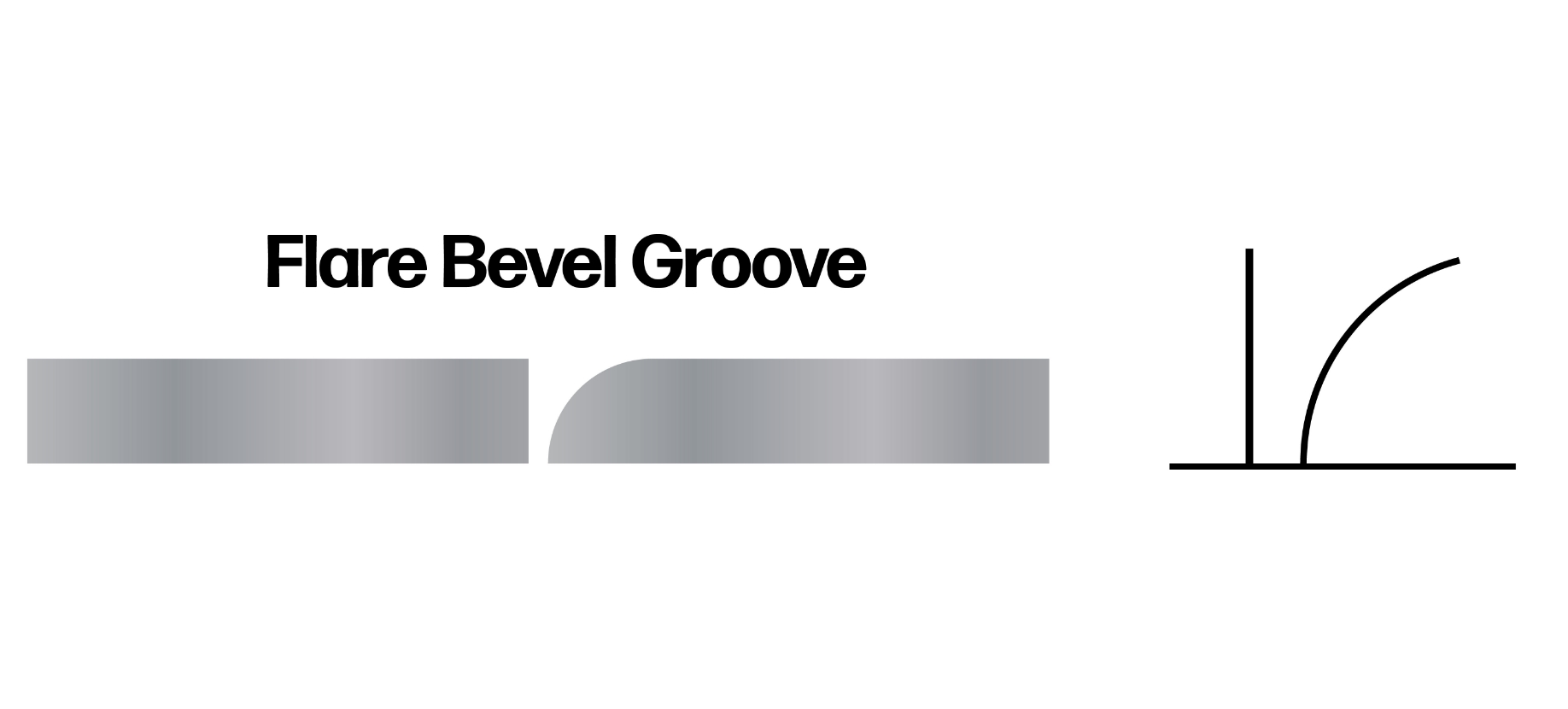
Flare-V Groove Weld
Similar to a flare bevel groove, the flare-V groove creates a natural V shape when joining two curved pieces of metal. It’s most suitable for welding thicker materials as it makes it easier to apply the weld to the metal. This type requires the edges of both pieces to be chamfered, either singly or doubly, to create the groove.
- Advantages: Can be produced in any welding position, offers improved joint access, good penetration capabilities.
- Disadvantages: Requires skill and experience, risks distortion in thicker materials.
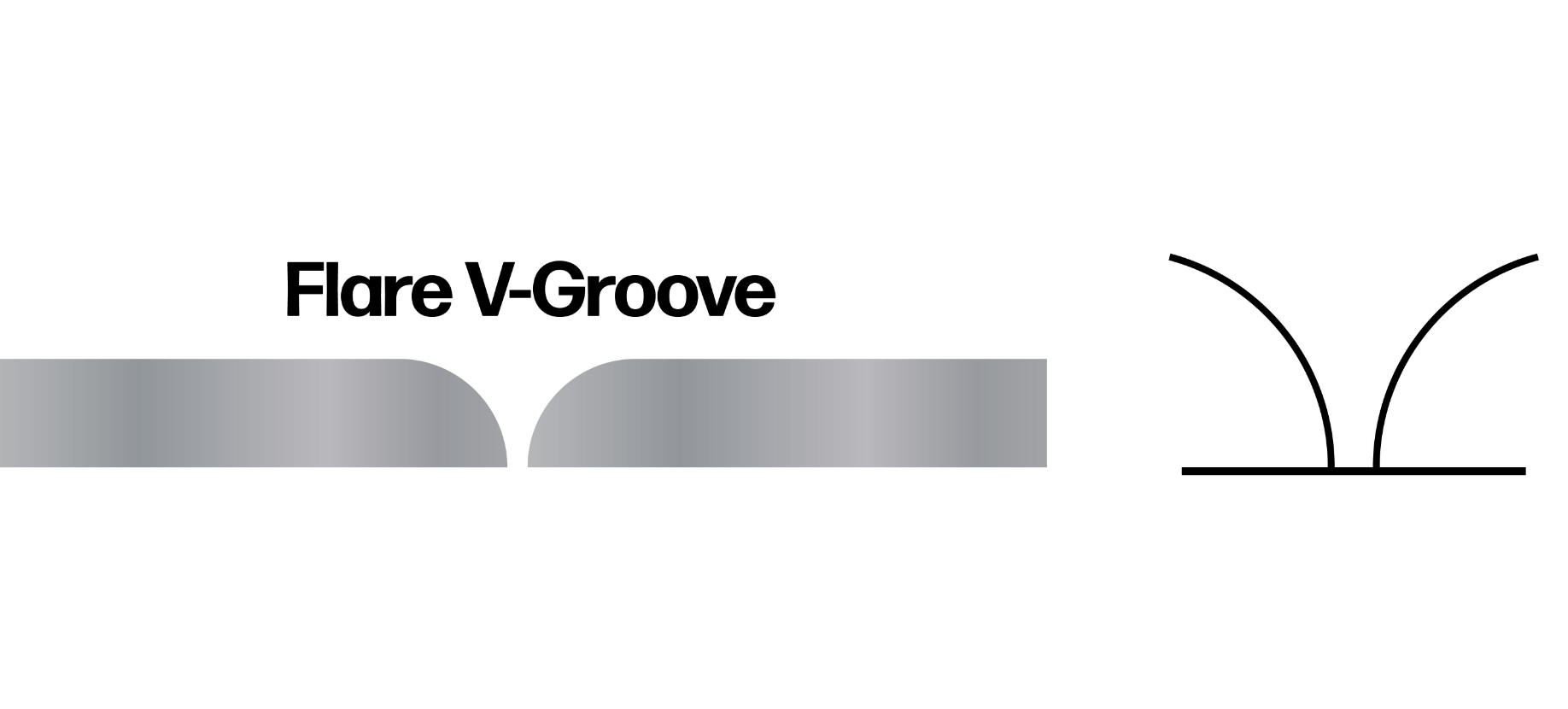
Single-Bevel Groove Weld
For a single-bevel groove weld, only one side of the material is beveled. The angle is typically between the metal’s surface and a plane perpendicular to the surface. This allows for deeper penetration that results in a stronger joint. This type of groove is useful for achieving full penetration on one side of the weld when the back side isn’t accessible. A double-bevel groove weld uses less filler metal, and the other weld also helps cancel out distortion in one direction.
- Advantages: Achieves full penetration from one side when the other is inaccessible, offers better penetration when welding dissimilarly sized metals.
- Disadvantages: Requires precision as the bevel angle and root gap will affect weldability, may require multiple passes.
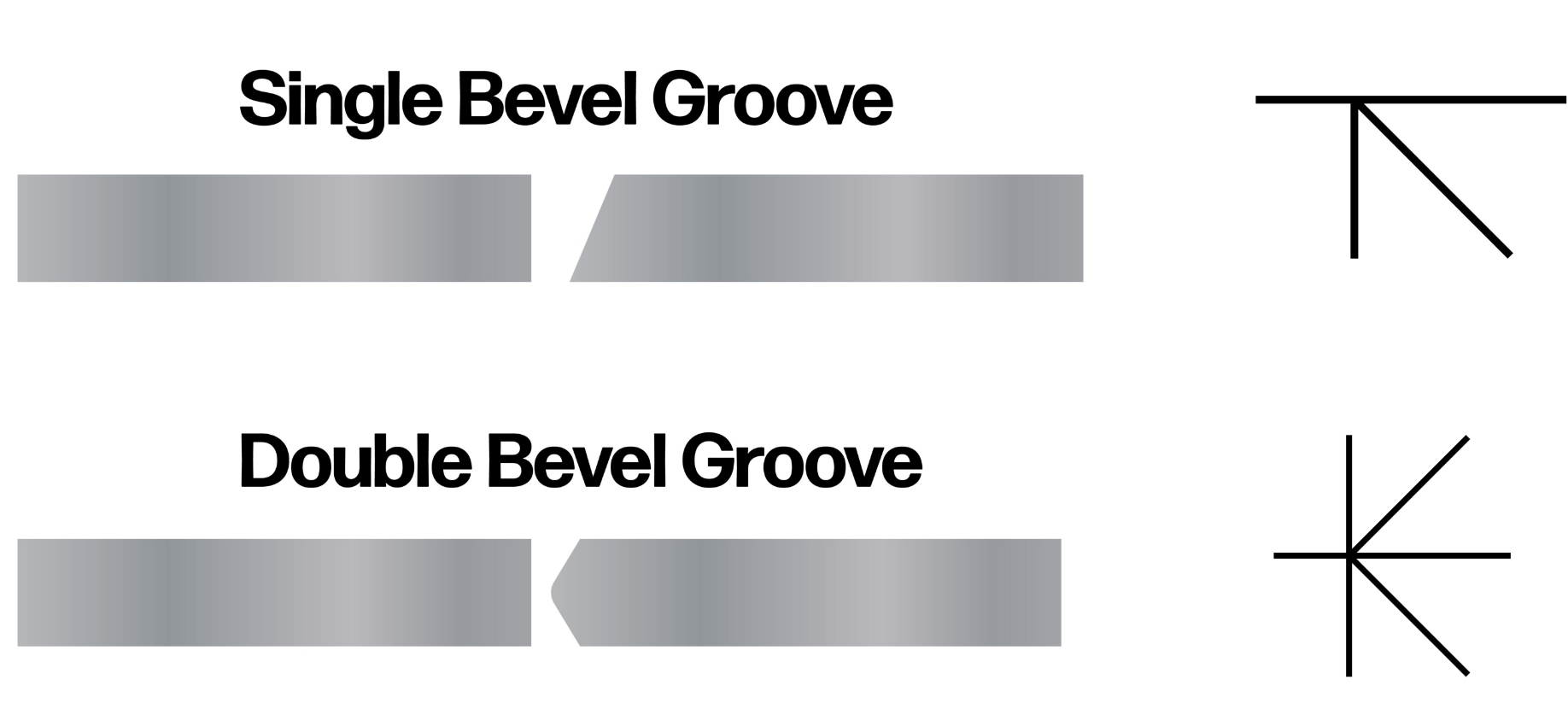
J Groove Weld
A J groove weld is where a J shaped groove is created in the joint between two pieces of metal. It requires special machinery to precisely shape the groove. This type of groove can be used to join thicker materials by creating a narrow groove weld configuration. It also creates a larger surface area for the weld for lower weld deposit volume.
- Advantages: Cuts into less material, uses less filler metal, allows for deeper penetration.
- Disadvantages: Difficult to produce, more expensive than bevel grooves, requires more specialized preparation.
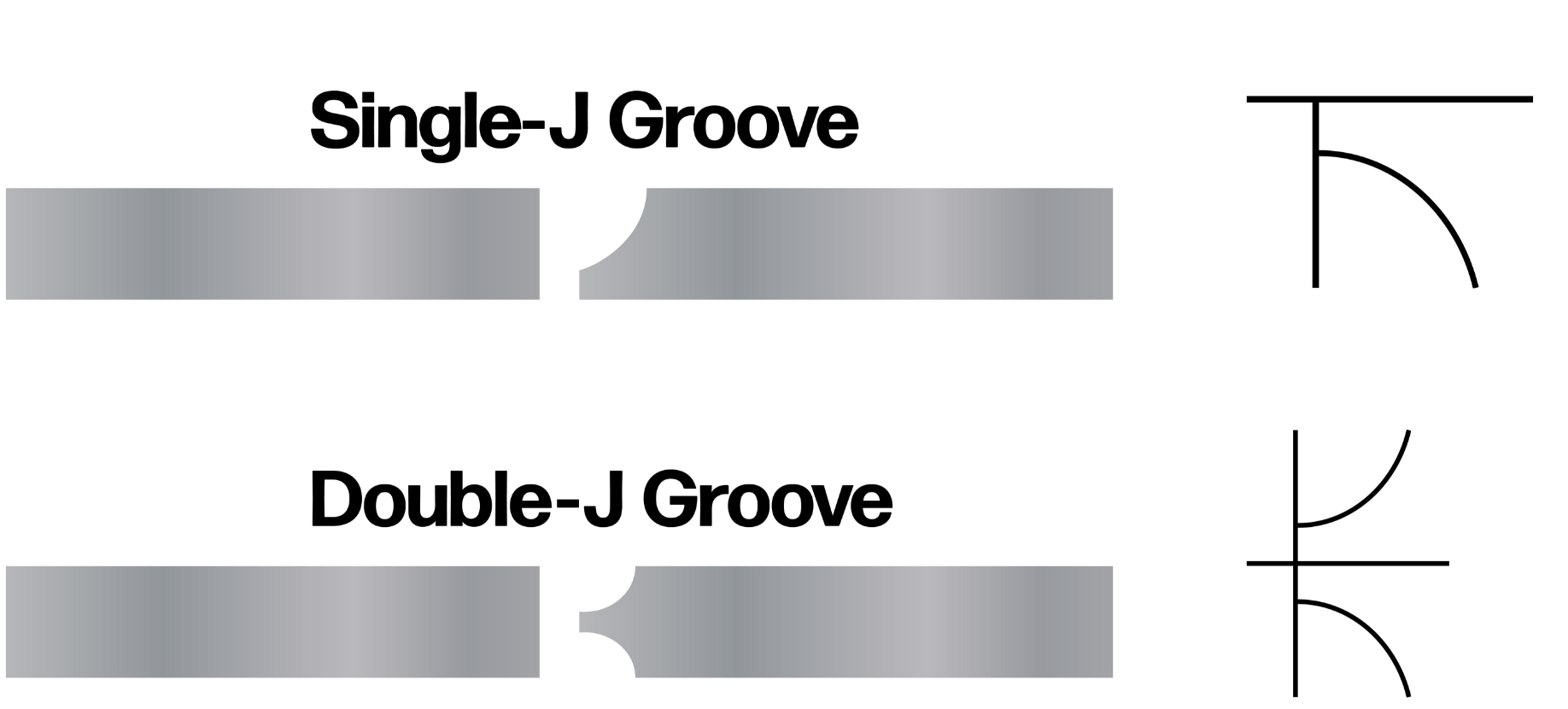
U Groove Weld
Similar to the J groove, the U groove is used on thicker materials. Its shape allows for better control of the weld pool, which results in a cleaner and more robust weld. Due to its larger weld area, it offers a more substantial joint, but it does take more time and filler metal to create.
- Advantages: Suitable for a wide variety of materials, easy to weld in all welding positions, achieves complete fusions.
- Disadvantages: Requires careful preparation, groove machining is difficult due to shape, may require multiple passes.
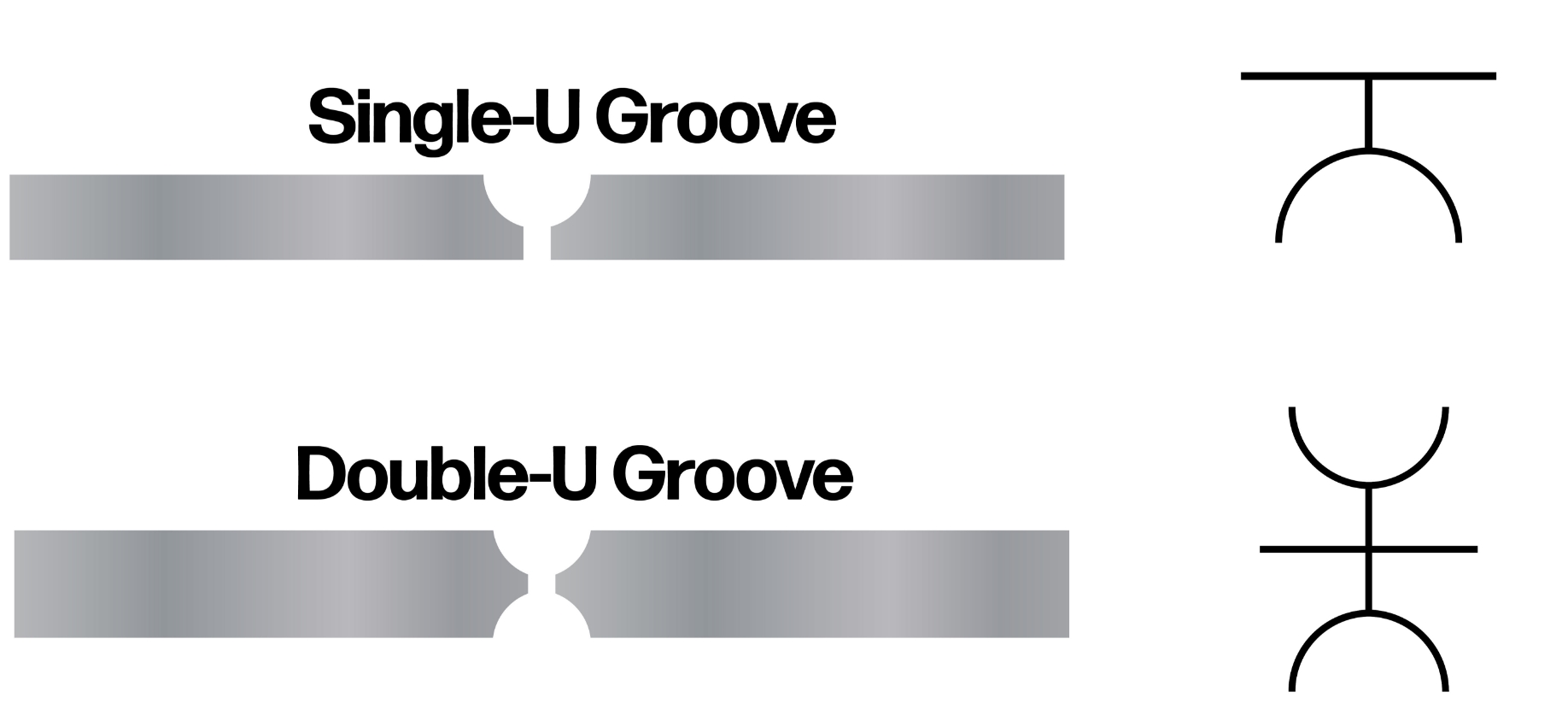
V Groove Weld
V groove welds demonstrate good welding strength and have a high resistance to stress. This makes it a popular choice for many metalworking and shipbuilding applications. This type of welding groove is used when both components can be modified, unlike with a single bevel groove weld.
- Advantages: Offers high joint strength, can be used in multiple welding positions.
- Disadvantages: Uses more filler metal, requires precise preparation, including proper bevel angle and root face dimensions.
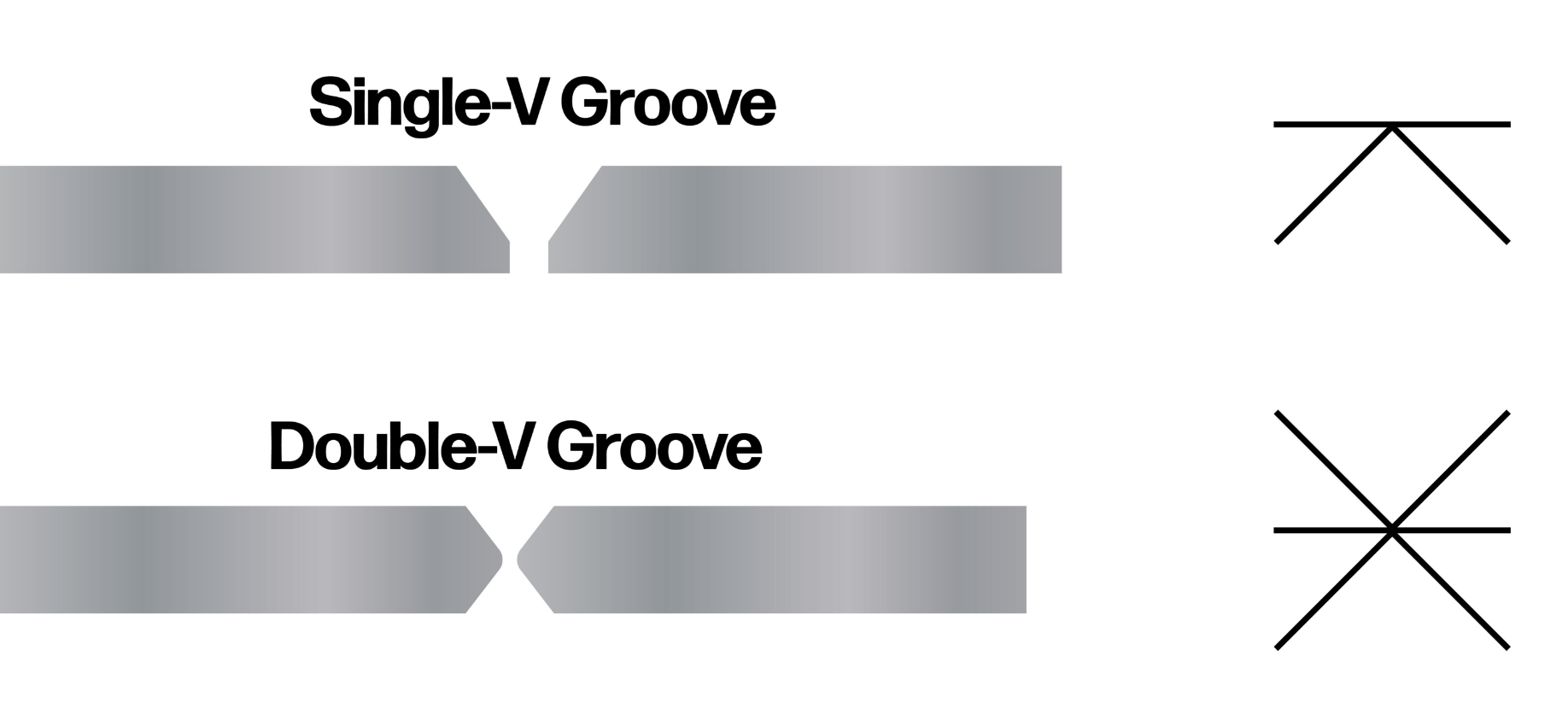
Square Groove Weld
The square groove weld is made by depositing weld metal in the space between two pieces of metal that are flat and parallel to each other. This type of groove typically produces less distortion because of the simplicity of the weld preparation. It’s relatively easy to make and doesn’t require any advanced welding skills or special equipment.
- Advantages: Produces less distortion, offers greater penetration, easy to make without special equipment.
- Disadvantages: Requires consistency on both sides of the material, unsuitable for thicker material.
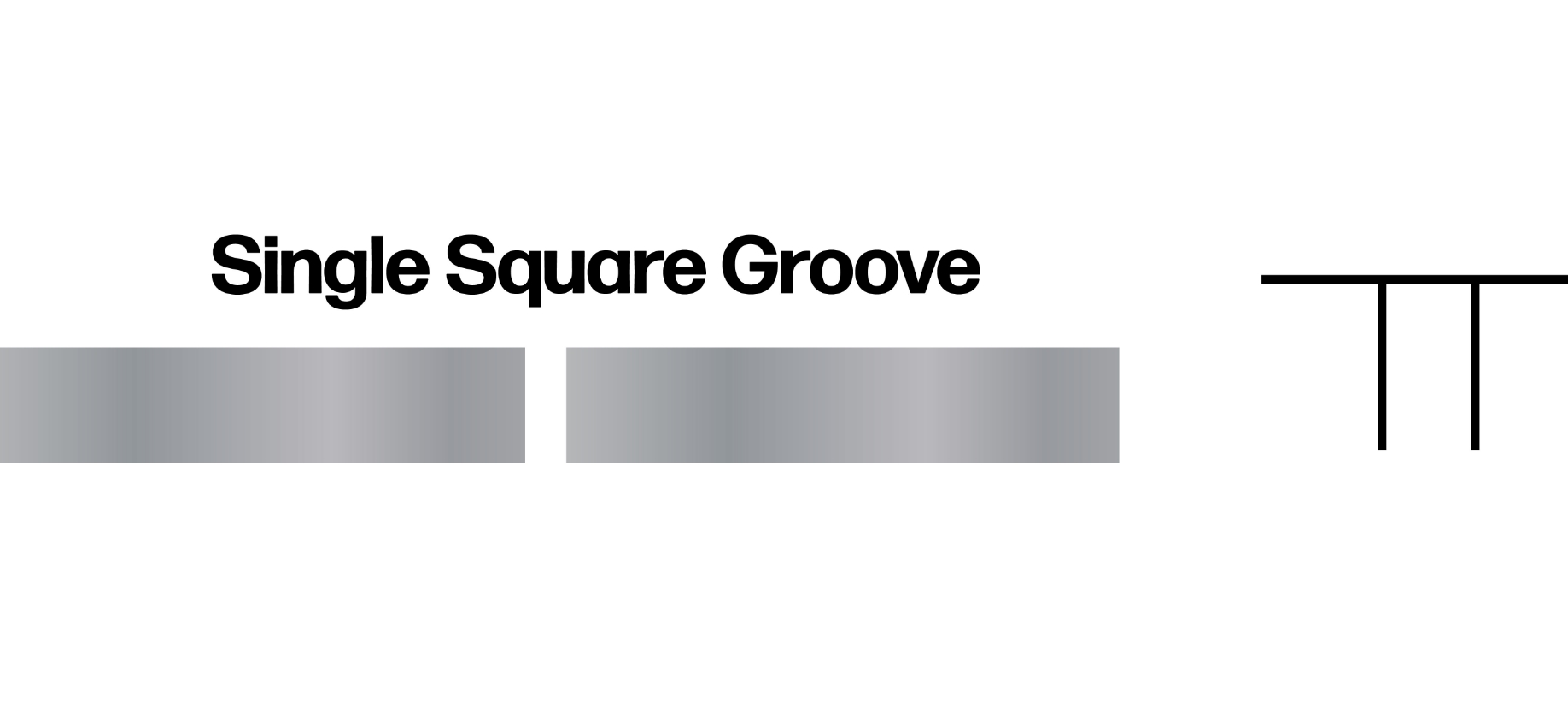
Groove Weld Vs. Fillet Weld: What’s the Difference
A groove weld and a fillet weld are two of the most basic types of joints in welding. Though they come in several variations, they can be easily differentiated by understanding where the weld is going in relation to the metals being welded. A groove weld is when the weld is between the two workpieces, while a fillet weld is when the weld is beside the two workpieces.
For certain applications, groove welds are preferred since they penetrate further into the metal, offering higher strength. They’re regarded as one of the best choices for structural applications with high loading conditions where maximum strength is required. On the other hand, they can be difficult to weld, take more time due to extensive joint preparation, and require training and skill.
However, fillet welds are the most commonly used since they’re relatively easy to achieve with little material and joint preparation required. This versatile weld can be used for many types of joints, whether the metal is at an angle, overlapping, or when the end of a cylinder needs to be welded to a flat sheet.
The choice of using either a groove weld or a fillet weld greatly depends on the design of the job and the purpose of the weld.
Welding Processes for Different Groove Types
Welding grooves and welding techniques go hand in hand. MIG welding, TIG welding, and stick welding all adapt to different groove configurations. Some processes complement certain welding grooves while others don’t react as well. Since types of welding grooves significantly influence which welding technique should be employed, it’s important to have an understanding of these factors before beginning the job.
MIG Welding Grooves: MIG welding is fast and efficient, working well with grooves that are straight and continuous. This process works particularly well with grooves like flare-bevel and V.
TIG Welding Grooves: TIG welding offers enhanced precision, requiring a steady and controlled hand to apply the weld. It’s well-suited for intricate grooves that demand this high level of precision, such as J and square grooves.
Stick Welding Grooves: Stick welding is adaptable to various groove types, offering greater versatility. For welding groove types that require deep penetration and strength, such as the V and U groove, this welding process excels in this field.
Learn more about each welding process with the help of our detailed and comprehensive guide: What's the Difference Between MIG, TIG, and Stick Welding.
Overcoming Common Welding Groove Challenges
Like any part of welding, welding grooves come with their own sets of advantages that support the project and challenges that welders need to overcome. Exploring the different problems and challenges that may arise can arm a welder with the knowledge to handle them.
Welding grooves take precise preparation. The joints need beveling and shaping, which is a time-consuming task. It is, however, very crucial to achieve a successful weld. Additionally, shaping the grooves and filling them demands complete control over the welding gun all throughout the welding process. This requires a steady and confident hand, which can only come from dedicated practice. Developing your skills over time can help you gain the experience and control required for the task.
While most welding defects such as distortion or porosity can be prevented by altering your welding parameters, some defects emerge from incorrectly misshaping the groove. If there’s insufficient penetration with the first welding layer or there are large deformations, the groove shape may be too large. If melting occurs even with the first layer or burrs occur easily, the shape may be too small.
If you’re experiencing incomplete fusion or slag inclusion, which can result in high-temperature cracking, the angle is too narrow. This can also be the reason why welding is difficult due to frequent contact between the nozzle and the base metal. Melting with the first layer and burrs occurring easily can also be caused by having too wide of an angle.
Elevate Your Welding with NS ARC Welding Wires
As a crucial component in the welding process, the choice of welding wire is paramount in assuring you’ve created a solid and reliable weld. That’s why NS ARC only offers our high-quality and high-strength welding wires to provide unmatched welding capabilities to our welders. It’s important to choose a welding wire that complements the intricacies of welding grooves, offering welders the opportunity to establish a firm and solid connection between those two materials. Find a carbon steel, stainless-steel, metal-cored, flux-cored, or aluminum welding wire that best suits your next project. Our team of experts is on standby to provide any assistance needed in making your selection.
Check out our guide on finding the right welding wire specifically for welding carbon steel to make your selection process even easier.
Learn MoreDISCLAIMER: This information is descriptive in nature and not purely prescriptive. Refer to your own welding machine’s user manual for proper settings and consult a welding expert for support.