Guide to Mild Steel MIG Welding
Dec 4th 2023
MIG (Metal Inert Gas) welding is a versatile and popular welding process, especially when it comes to working with mild steel. Easy to learn, this is a straightforward process that helps any welder achieve the ideal weld for a wide range of applications and industries. This comprehensive guide to MIG welding mild steel is designed to walk you through each step of the process, providing practical information that can help make the process even easier than it already is.
Understanding Mild Steel
Low carbon steel, or mild steel, is one of the most commonly used grades of carbon steel thanks to its weldability and affordability. It is comprised of 0.05% to 0.30% carbon and features relatively low strength but high ductility. With high formability and machinability, it exhibits excellent toughness to resist impact and deformation. This type of carbon steel is often used in construction, general fabrication, automotive manufacturing, and many other industries and applications.
Prepare the Right Welding Equipment
In order to achieve a successful weld, you need the right welding equipment. Before using your welding machine, it’s important to check all the cable connections to ensure that they’re tight and undamaged. Make sure that you are using the correct electrode polarity and appropriate gas flow and ensure that the welding wire spool tension isn’t too tight or too loose.
Other equipment you may need may include a temperature tracker, which could be an electronic infrared thermometer, electronic surface temperature probe, or temperature sticks; a wire brush to clean the mild steel that will be welded; and clamps or fittings to hold the joint in place during welding.
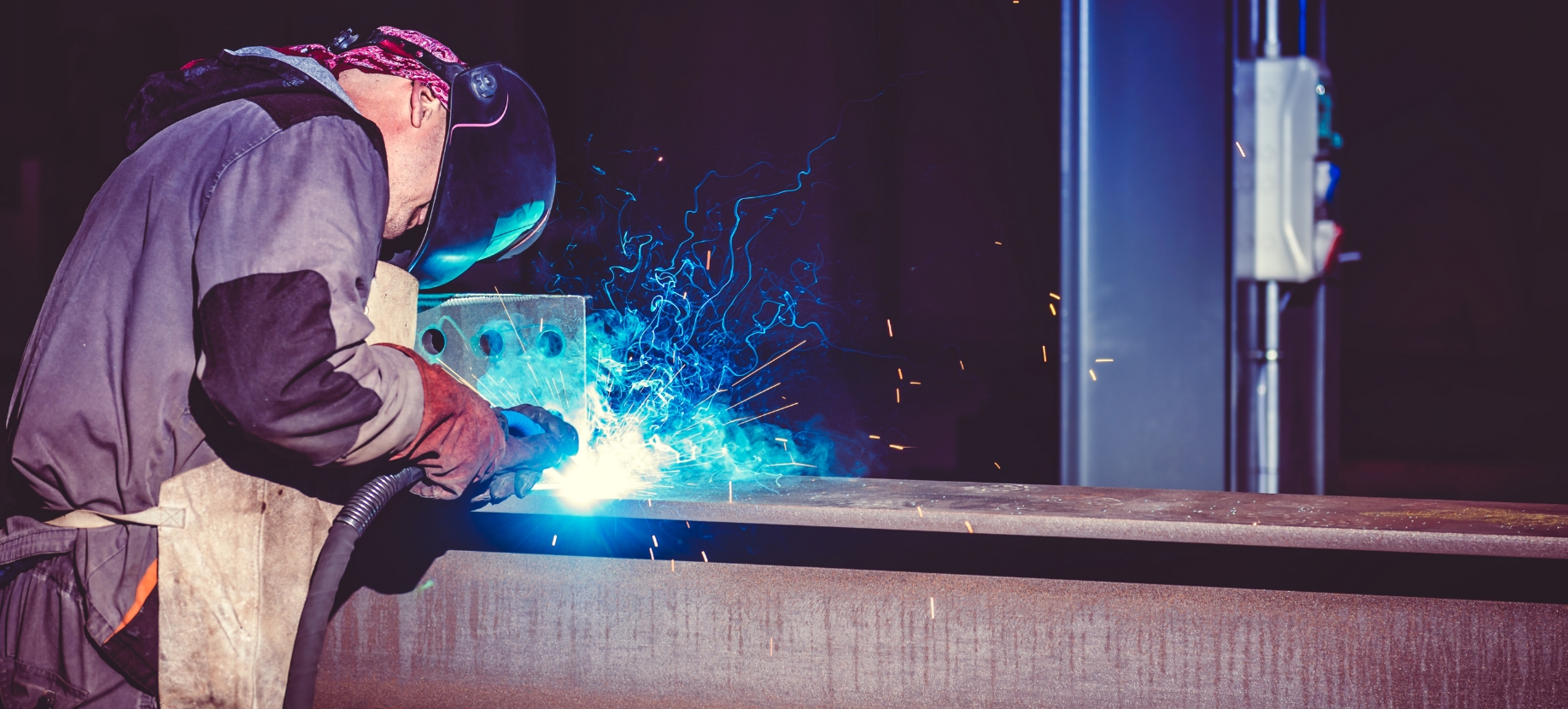
Safety Equipment
Always wear the appropriate personal protective equipment whenever you are welding. Since you’re exposing yourself to intense heat and powerful equipment, you need to wear the following:
- Welding Helmet with Darkened Lens
- Welding Jacket or Flame-Resistant Clothing
- Welding Gloves
- Steel-Toed Boots
- Welding Mask or Respirator for Fume Protection
- Ear Protection
- Safety Glasses
- Welding Goggles
Welding Wire Selection for MIG Welding Mild Steel
There is a wide variety of welding wire that can be used for welding low carbon steel materials. There are a lot of factors that go into choosing the right welding wire, including the size of the material, application, welding position, and cost. It’s best to explore all your options before determining which one is right for the job. For a full list of different types of welding wire options, check out our guide: Best Welding Wires for Carbon Steel.
An ER70S-6 copper-coated welding wire is an excellent, general-purpose choice as it’s known for providing smooth and consistent wire feeding and enhanced arc stability. The copper coating offers exceptional electrical conductivity and resistance to corrosion.
An ER70S-3 copper-free welding wire is similar to ER70S-6 but with slightly lower levels of silicon and manganese. It offers high wire feed speeds and generates a clean finished look to the weld. Because this type of welding wire doesn’t have copper, it allows for faster welding with reduced spatter and minimal heat input. It’s ideal for applications in which copper contamination is a crucial feature.
The thickness of the mild steel influences the diameter of the welding wire needed. The thicker the metal, the larger the wire needs to be. Welding with a wire that’s too small on a thick plate can result in a lack of penetration while using a wire that’s too large on a thin plate can cause burn-through. For thinner mild steel, a smaller welding wire is a good choice. For thicker mild steel, a larger welding wire can get the job done right.
Shielding Gas Selection for MIG Welding Mild Steel
MIG welding relies on the help of shielding gas to protect the weld from being contaminated. There are two common types of gases used for MIG welding: carbon dioxide and argon. Some welders use 25% carbon dioxide and 75% argon, which is an all-purpose mix for carbon steel that produces good arc transfer and appealing bead appearance. Others use 100% carbon dioxide, which might produce more spatter but deeper penetration. Check out our guide for a more detailed discussion on shielding gases for welding carbon steel.
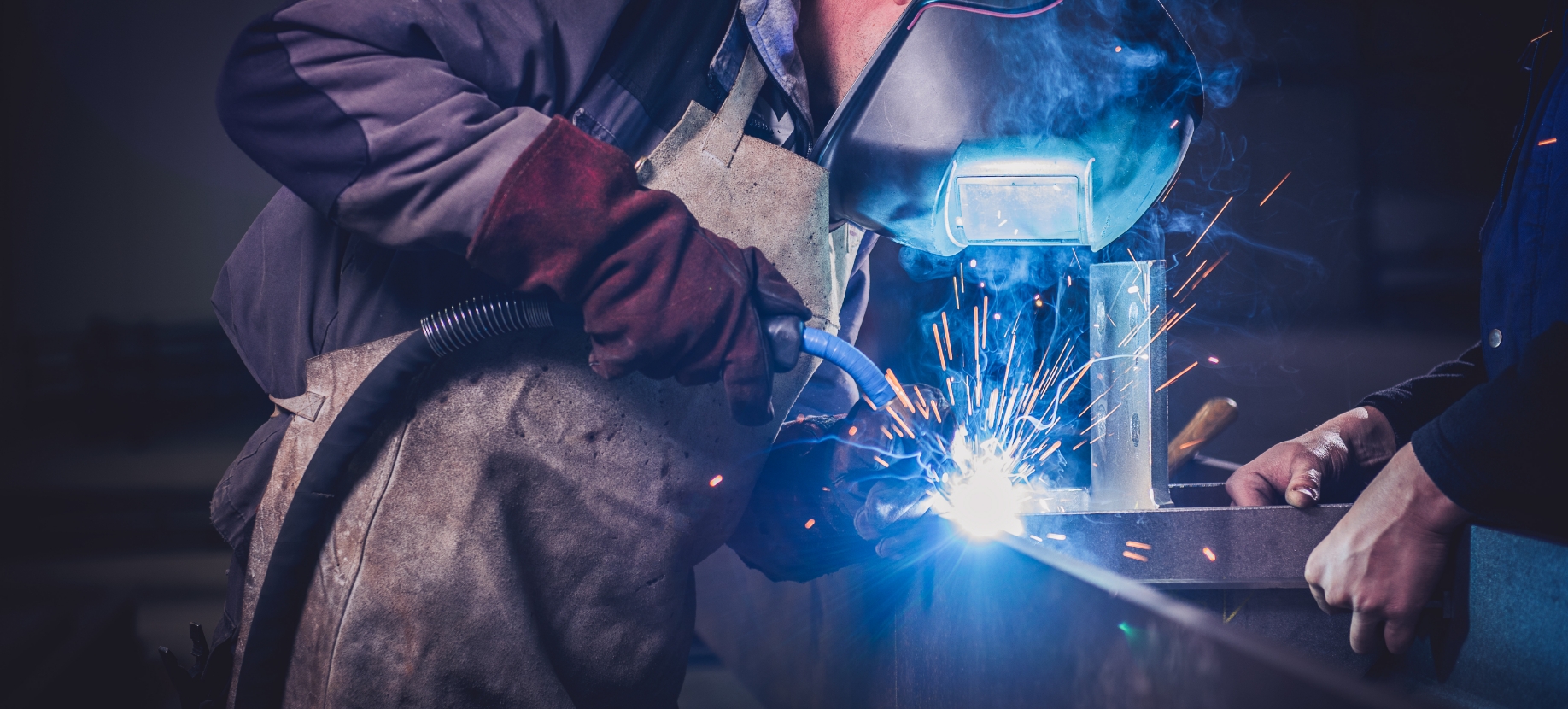
MIG Welding Mild Steel
With everything in order, it’s time to get started with the mild steel MIG welding process.
Prep the Mild Steel for Welding
Your mild steel plate needs to be fully prepared for the welding process in order to ensure that the finished weld is strong and reliable. The material needs to be free of any kind of rust, dirt, debris, grime, paint, and any other contaminants that could cause defects in the weld. A wire brush can help remove them quickly and effectively and for heavier debris, a grinding wheel or sanding disc should be used.
If you’re working with a really thick piece of mild steel, then preheating may be necessary; check with the steel manufacturer for recommended welding practices. Preheating is typical for plates that are about 10-12mm thick. Preheating the material can help prevent cracking and other problems from occurring.
Joint preparation is also another crucial step. Like the base metal, you’ll need to remove any surface contamination from the edges of the joint. If you’re working with thick mild steel, then you should consider beveling the edges to improve penetration. It’s also recommended to keep the joint in place using clamps, fittings, or strong backs in order to ensure uniform welding.
Begin MIG Welding the Mild Steel
Welding requires unwavering concentration, so make sure you are in a comfortable position and begin welding the materials. You need to maintain a stable arc length between the welding gun and the base material. Make sure that you’re monitoring the heat input closely and be on the lookout for any distortion, burn-through, or other welding defects. Adjust your welding parameters as needed.
Your welding parameters depend on the thickness and type of mild steel you’re working with. The travel speed needs to be consistent to produce uniform weld beads. Going too fast can result in improper penetration while going too slow can result in burn-through. Keep the movement smooth and consistent.
The work angle should be approximately 10-15 degrees from perpendicular to the metal for good penetration and minimal spatter. The travel angle should be around 5-15 degrees from perpendicular to the metal, and you should push your nozzle in the direction of the weld (recommended for solid welding wire). This usually gives you a better view of where you’re welding. You can also pull the nozzle with the welding gun pointing back at the weld puddle, which can help produce a narrower bead and deeper penetration (all welds should be qualified to meet your requirements)..
Always remember to keep an eye on the weld pool. If the pool is too big or there’s too much heat input, it could negatively affect the weld, so increase your travel speed or adjust the heat input. If the pool is too small, slow down a bit. It’s all about staying in control during the entire welding process.
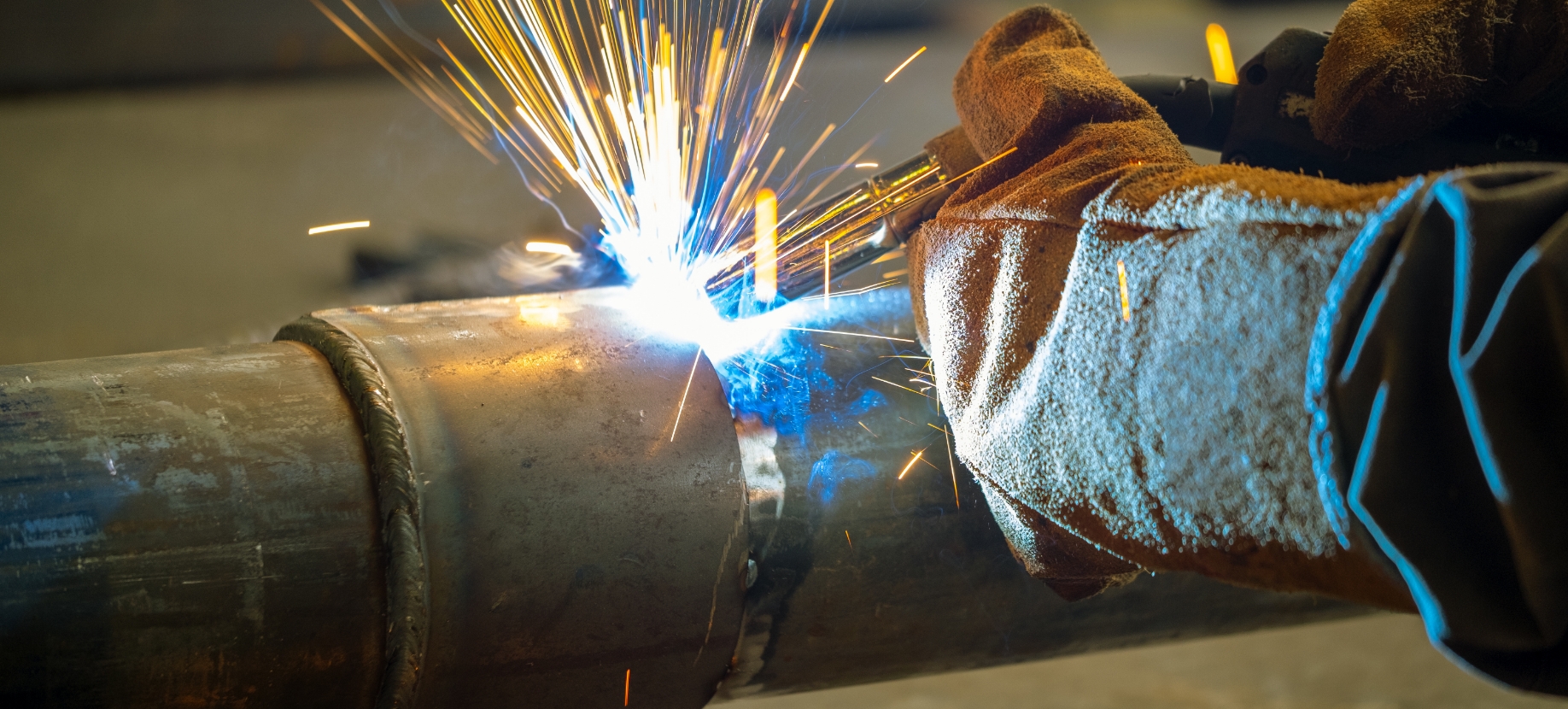
Post-Welding Cleanup
Once the welding is finished, you need to remove any slag or spatter that may have accumulated during the process. The finished weld needs to be thoroughly examined for any signs of discontinuities and defects such as porosity, incomplete fusion, burn-through, excessive penetration, undercut, etc., each of which will have certain tolerances within the code or specification you are working to.
Keep on the lookout for cracks: crater cracks, hot cracks formed at elevated temperatures, and cold cracks that can form once the weld has cooled down. Cracks, except in the case of hardfacing, are defects that must be remedied.
Some defects can be corrected, but some may weaken the weld too much and may threaten the integrity of the entire structure. If that's the case, it's best and safest to start over.
Welding Mild Steel Problems Vs. Solutions
There are a lot of issues that a welder can encounter when working with low carbon steel. Even the most experienced veteran can still run into a problem that sets them back a bit. However, there is almost always a solution to a problem welding mild steel. Here are some of the most common ones.
Excessive Spatter
Problem: Spatter, which are those tiny metal droplets that splash around the weld area, are unsightly and require a lot of cleaning up. It can stick to your equipment and even your skin if you’re not wearing the correct PPE and aren’t properly covered up.
Solution: If you’re noticing a lot of spatter during your operation, you need to adjust your welding parameters. An unstable welding arc caused by incompatible voltage and amperage settings can be the cause. Using low-quality welding wire or the incorrect shielding gas can also lead to excessive spatter, so look for high-quality welding wire and make adjustments to counterbalance the carbon dioxide with more argon.
Porosity
Problem: Porosity is the small cavities within the weld bead that occur when excessive gases get trapped within the molten weld puddle during solidification. There are different types of porosity, including surface, subsurface, wormholing, and catering. Welding porosity can negatively impact the quality of the job as it can reduce the strength and corrosion resistance of the weld. If found in excess of certain limits, it is also a permanent defect, so the weld will need to be repaired and replaced, driving up time and material costs.
Solution: Avoiding porosity in the first place is the key to never having to deal with it. Pre-cleaning the surface of the metal can remove contaminants that could cause porosity. Always make sure that you are using the proper shielding gas and the recommended flow rate and pressure for the type of carbon steel you’re working with. You also need to keep a steady arc length as having too long of an arc can open-up room for atmospheric gases to seep into the weld puddle.
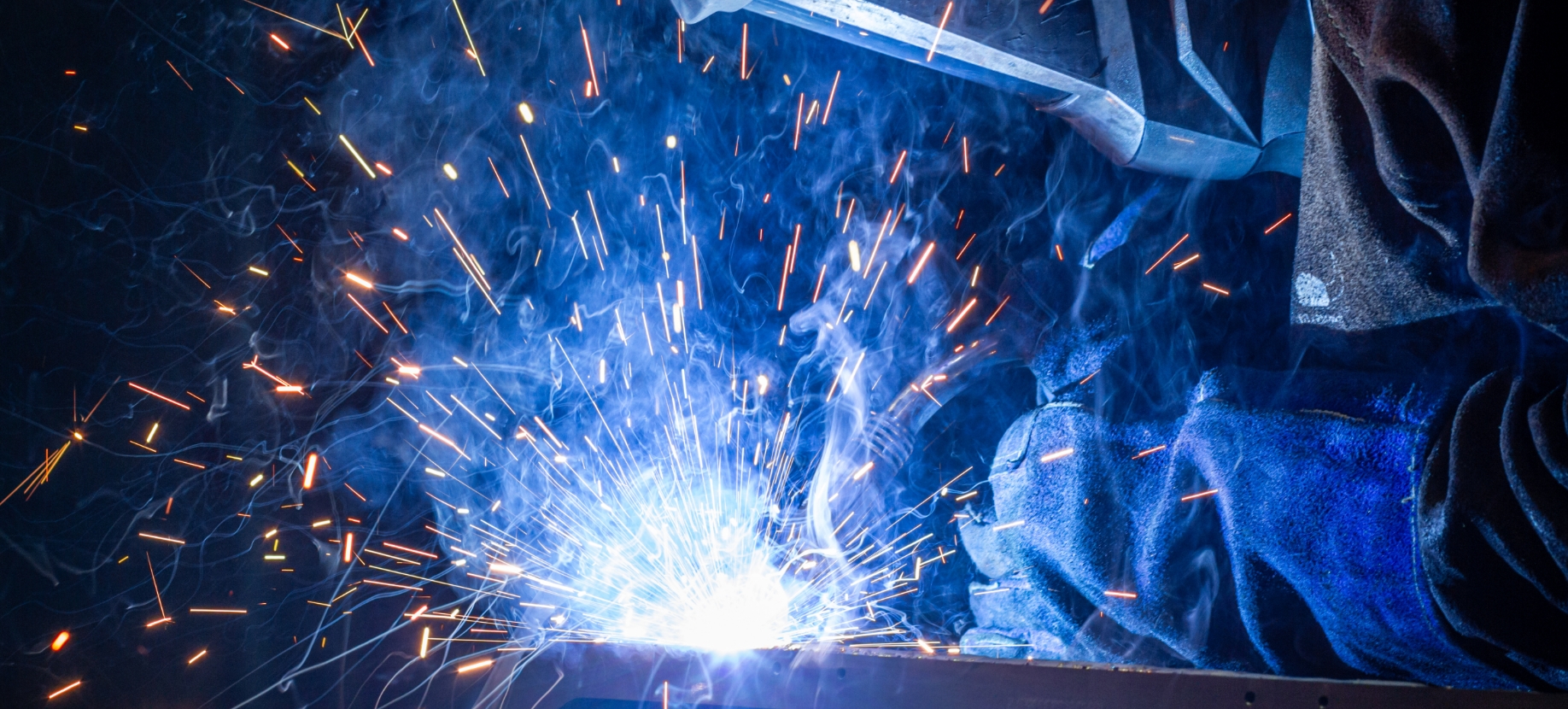
Burn-Through
Problem: When there’s too much heat input during the welding operation, you run the risk of experiencing burn-through, meaning the weld penetrates right through the mild steel. Not only does this leave a hole in the material, but it also weakens the strength of the weld and can increase the risk of cracking and deformity in the weld. There are a number of factors that can cause burn-through, so it’s best to keep an eye on your welding parameters throughout the welding process.
Solution: Since there are various causes of burn-through, having control and using the right settings for the project becomes important. It’s a good idea to decrease the heat input and increase your travel speed. The arc length should be consistent at the recommended length, and you should ensure that you’re working with a travel angle that’s about 10-15 degrees. And, once again, clean the surface before welding. The removal of debris and contaminants can go a long way in preventing various welding problems.
Poor Bead Profile and Appearance
Problem: Weld bead appearance can have an impact on the quality of the weld. Some noticeable appearance irregularities include ripples, humps, or underfills and a non-uniform bead shape, all of which can be discontinuities or in excess defects to the weld. A professional weld should have a visually appealing look. The weld beads should be smooth and consistent and demonstrate proper fusion and penetration without any discontinuities or defects.
Solution: The best way to improve the appearance of your weld beads is by adopting best welding practices and techniques. Uniformity and consistency depend on welding position, travel speed, travel angle, voltage, using compatible welding wire and shielding gas, and wire feed rate. Having a steady hand and being in a comfortable position can help you maintain control during the welding process. One useful tip to improving bead appearance is to remove the end piece of the welding wire that had already been used (the ball that forms on the end of the wire) form the last welding job to avoid contaminating the next one.
Incomplete Fusion
Problem: When there’s insufficient energy input in the mild steel, it usually results in incomplete fusion. Using the incorrect welding parameters can cause this type of defect, including low heat input, high travel speed, large weld pools, wrong travel angle, and using the wrong welding wire diameter for the thickness of the carbon steel.
Solution: Properly balancing your welding parameters can go a long way in preventing incomplete fusion from impacting your welds. Using the appropriate amount of heat input and travel speed can result in proper fusion between the metals. For the right welding wire diameter, it’s recommended to use a smaller diameter welding wire for thinner sections of the carbon steel and larger diameter welding wire for thicker carbon steel.
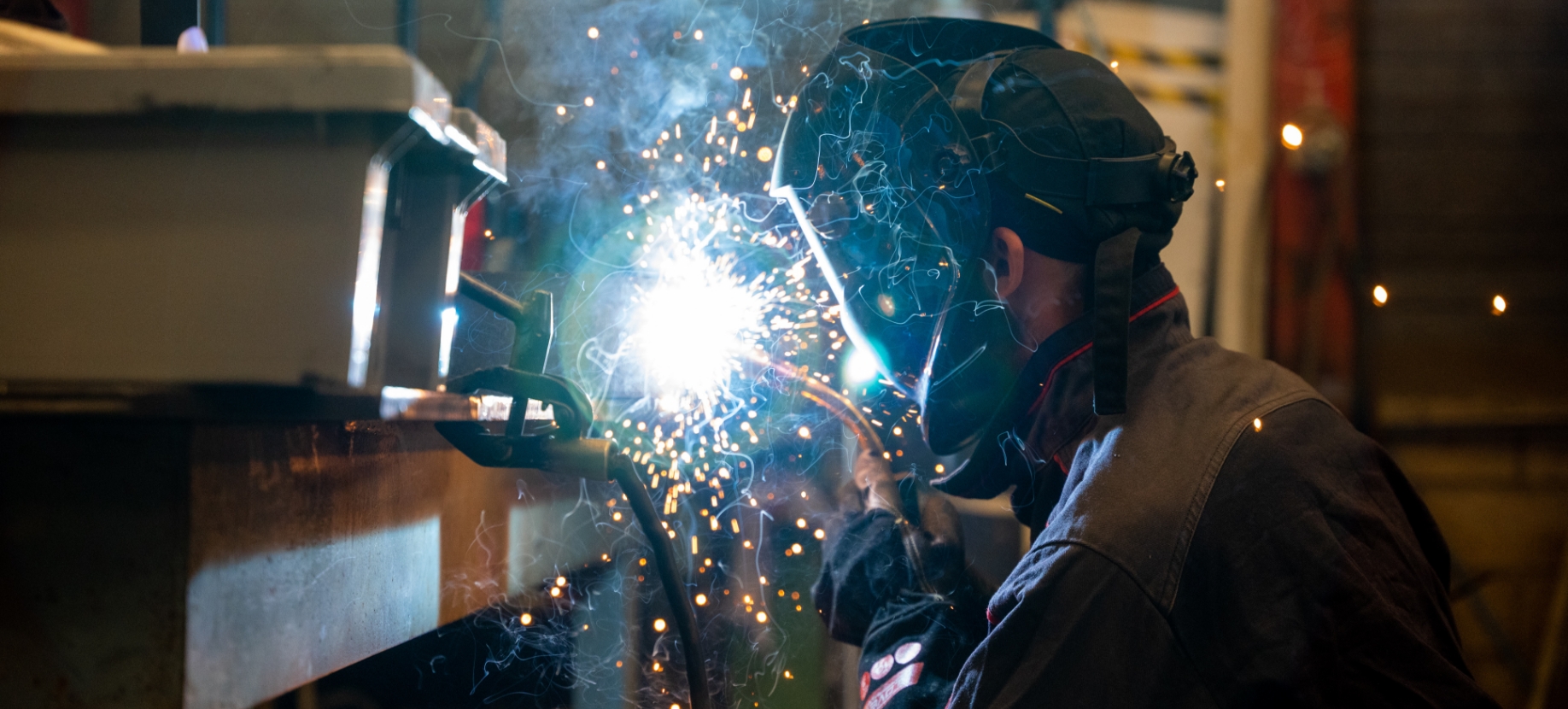
Incomplete Penetration
Problem: A weld joint’s strength is compromised when there’s incomplete penetration caused when the metal groove isn’t completely filled and the weld metal doesn’t make it to the bottom of the weld joint. Using the wrong welding technique or welding wire for the job can result in incomplete penetration.
Solution: In order to completely penetrate the metal until a proper weld is achieved, you need to use the correct joint geometry and proper alignment while ensuring enough weld metal deposition. If you believe that the weld isn’t penetrating the mild steel enough, then we recommend reducing the travel speed. Like previously mentioned, the type of welding wire plays an essential role in properly welding low carbon steel. Be sure to pay close attention to the chemical composition and diameter of the welding wire to ensure that it’s compatible with the type of carbon steel and its thickness. Always qualify the weld to the application to ensure a successful weld and project.
Undercutting
Problem: Undercutting occurs when irregular grooves form in the mild steel during welding. This happens when the mild steel or another welding bead is melted but not properly filled by the welding filler metal wire. This type of defect is concerning because it compromises the structural integrity of the weld and could lead to further problems, such as cracking or other failures. It can happen if you’re using too much voltage, or the wrong torch angle, travel angle, type of welding wire, or travel speed.
Solution: To avoid undercutting, it’s best to reduce your travel speed and lower the voltage. Reducing the arc length can also help prevent the problem. Always check your welding consumables to make sure that you are using the right type of welding wire for your mild steel along with the appropriate mixture of shielding gas.
Cracking
Problem: Cracking is a significant problem as it weakens the integrity and strength of the weld and is a defect. If left unchecked or untreated, cracks can grow and worsen over time. Cracking can occur during the cooling phase of the weld or a few days after the welding operation. It is caused by a lack of preheating, high speed welding, contamination in the mild steel, or other factors.
Solution: Using the appropriate welding wire that matches the chemical properties of the carbon steel you’re working with can help prevent cracking. Preheating the metal before welding reduces cooling stresses which keeps the risk of cracking at a minimum. Post-weld heat treatment can also help in this way. Also, make sure that you don’t travel too fast so that you can sufficiently and properly fill the joint.
NS ARC Quality Welding Wire for Mild Steel
As a welder, it’s your job to ensure that you work with the best welding wires that produce a finished weld that is strong enough to support the integrity of the rest of the project, like NS ARC’s high-quality and reliable carbon steel welding wires. We carry both copper-coated and copper-free options that are available in a wide selection of diameters and packaging.
Our Copper-Glide™ copper-coated welding wires are an excellent choice for automotive manufacturing, general fabrication, and pressure vessels applications. Easy to use and versatile, this welding wire provides excellent arc stability and penetration. On the other hand, our Silver-Glide™ CopperFree™ is often used in the agricultural equipment, general fabrication, and pipe welding applications. This welding wire produces superior arcs and offers smooth wire feeding. We recommend exploring our wide and extensive catalog of high-quality welding wires to help you achieve outstanding welds for your next project.
Check out our guide on top tips and tricks for welding carbon steel to quickly become a pro welder!
Learn MoreDISCLAIMER: This information is descriptive in nature and not purely prescriptive. Refer to your own welding machine’s user manual for proper settings and consult a welding expert for support.