Best MIG Welding Wire for Mild Steel
Dec 18th 2023
Every MIG welding operation with mild steel is different, so it’s difficult to pin down what exactly is the best MIG welding wire for the application. However, there are some types of welding wire that welders have come to rely on as the definitive solid filler metal that gets the job done right.
Properties of Mild Steel
Mild steel, or low carbon steel or ASTM A36, is a type of material that is commonly utilized in a wide variety of applications, including automotive manufacturing, general fabrication, pipe welding, pressure vessels, shipbuilding, and so much more. Its lower carbon content, ranging from 0.05% to 0.25%, makes it easier to work with and manipulate to the right shape for the job.
Mild steel is known for being highly ductile so that it can easily stretch, bend, roll, or form into various shapes without the risk of breaking or cracking. This feature, coupled with its superior weldability, makes it an excellent choice for MIG welding operations. You just need the right welding wire that matches the chemical composition of the mild steel to achieve the ideal weld.
Understanding AWS Welding Wire Designations
The American Welding Society (AWS) has created classifications of filler metals for arc welding processes under uniform specifications. For each welding wire classification, every letter and number indicate a very specific detail that helps determine the chemical and mechanical properties of the filler metal. For an example, we’ll look at one of the most common welding wires used for welding mild steel: ER70S-6.
ER = electrode or rod – this means that the filler metal can be used in electrode or rod form (in which case, it can be cut into lengths for GTAW)
70 = 70,000psi – this is the as-welded tensile strength in pounds per square inch
S = solid wire – this is not a tubular electrode
6 = chemical composition – this reflects that it contains more manganese and silicon than classifications with a smaller number, such as ER70S-3
Understanding exactly what every letter and number are referring to can help welders select their welding wire quickly and confidently. With just a glance at the designation, you’ll know which welding wire is the best solution for your next welding application.
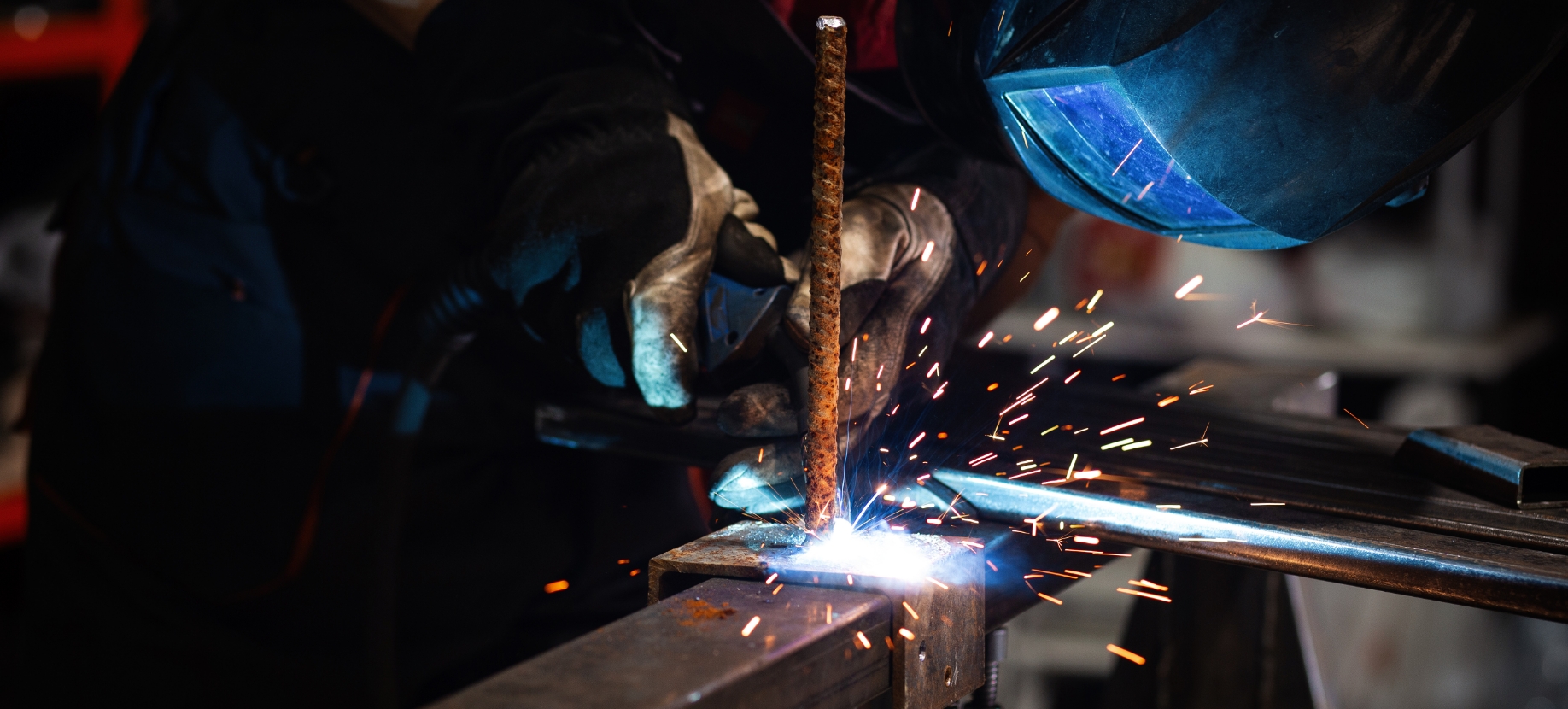
MIG Welding Mild Steel: A Summary
With the right welding wire in hand, the MIG welding operation for the mild steel material can go as smoothly as possible. MIG welding (metal inert gas), or GMAW (gas metal arc welding), is an arc welding process that involves continuously feeding a solid welding wire into a welding gun and weld pool in order to successfully join two pieces of mild steel together. It also utilizes a shielding gas, usually a mixture of 25% carbon dioxide and 75% argon, to protect the weld pool from atmospheric contamination. It’s a reliable process that is commonly used on pieces of mild steel that range in size from about 24-gauge to 3/8”.
The Role of Welding Wire in MIG Welding Mild Steel
Welding wire plays a critical role in MIG welding, acting as the heart of the weld that binds these two pieces of metal together. The choice of which welding wire to use greatly influences the rest of the MIG welding operation, possessing a significant impact on the overall quality and integrity of the weld.
There are many factors that influence the choice of welding wire for the MIG operation. One of the most compelling factors is wire diameter. Typically ranging from 0.023” to 0.062”, the size of welding wire that works best for the job depends on the thickness of the mild steel. Thicker materials require larger welding wire to produce proper penetration while thinner materials require smaller welding wire to prevent burn-through.
Another factor is the welding wire coating. Some solid carbon steel welding wires come with a copper coating to improve the electrical conductivity between the contact tip and the mild steel. It also promotes smooth wire feeding and excellent weld quality. However, there are certain applications in which copper can be a concern.
That’s when copper-free carbon steel welding wires come into play. These wires are an environmentally friendly alternative as they don’t release the level of copper particles into the air during the welding process that copper-coated welding wires may release. Copper-free welding wires are also known for producing less spatter for consistent joints while providing good arc characteristics and feeding performance.
Before selecting which welding wire you will use for your MIG welding operation, it is incredibly important to examine each factor to ensure that you are making the right decision. While the type of wire does play a crucial part, so does the diameter, coating, length, composition, and more. By ensuring that you are working with the right welding wire, you ensure that you can achieve the ideal weld with minimal risk of discontinuities or defects.
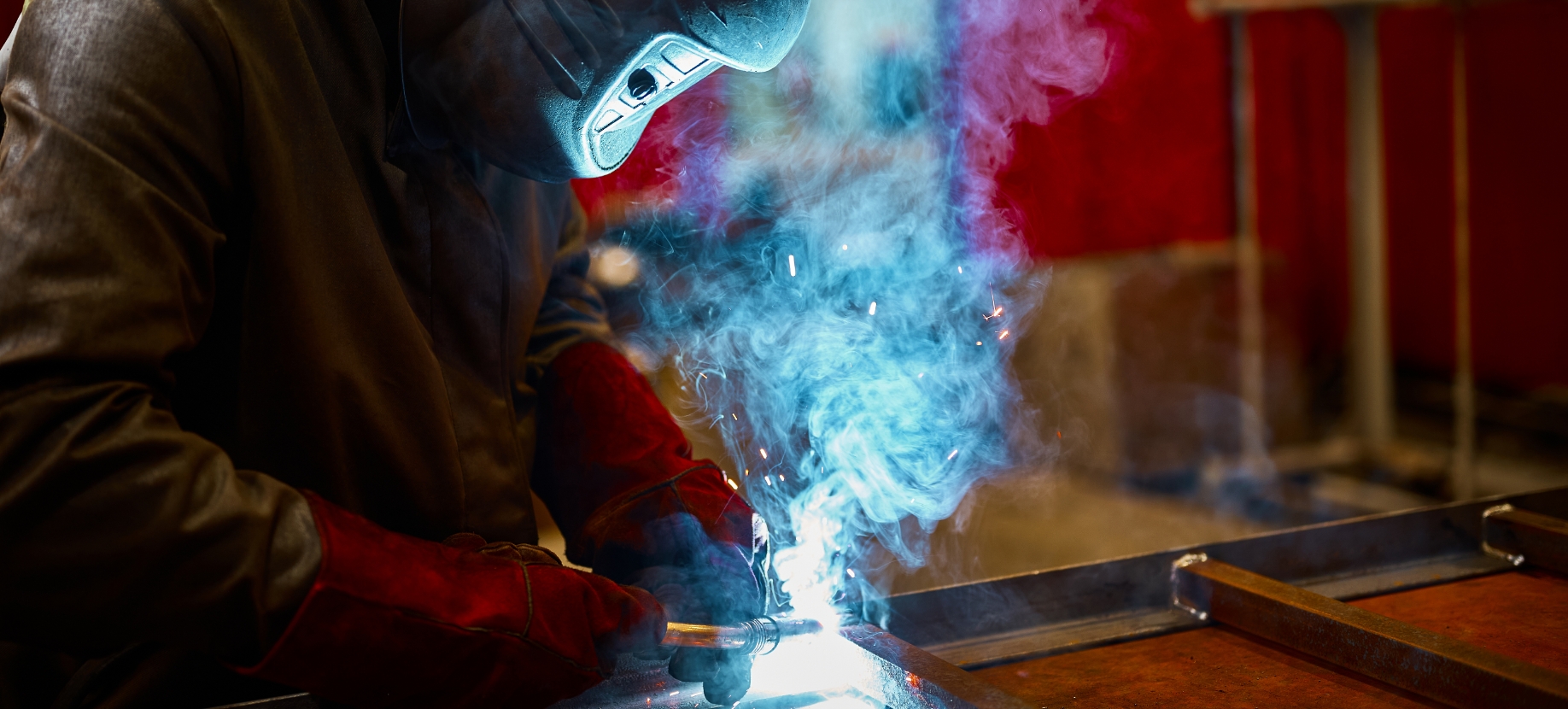
Best MIG Welding Wire for Mild Steel Welding
After taking all of the factors into consideration, many welders elect to utilize the ER70S-6 welding wire as their best MIG welding wire solution. This is because it is one of the most reliable and versatile options on the market that can handle mild steel with ease. It usually provides the required welding strength that so many applications depend on in order to ensure the structural integrity of the project.
Suitable for a wide variety of applications, such as general fabrication and automotive manufacturing, ER70S-6 welding wire lends its advantages to robotic, mechanized, or semi-automatic methods of welding. The added silicon present in this type of welding wire, as compared to the ER70S-3, provides better puddle fluidity for smoother and more consistent welds. Additionally, it brings good penetration, spatter control, and versatility to the project.
NS ARC Quality MIG Welding Wire for Mild Steel
Even though ER70S-6 may be considered the best among welders, there is no definitive “best” answer. The best solution to a MIG welding mild steel operation depends entirely on the operation in question. There are plenty of solutions to explore, and NS ARC carries a wide range of them. NS ARC welding wires are exceptionally engineered to provide all of the benefits needed to achieve the perfect weld.
Our Copper-Glide™ copper-coated welding wire provides excellent feedability and improved welding strength. These welding wires are designed to create smooth weld beads with uniform consistency. With their enhanced mechanical properties, including tensile strength and ductility, they are the right choice for handling heavy-duty demands of mild steel welding applications.
On the other hand, our Silver-Glide™ CopperFree™ welding wire is a reliable alternative as it offers great weld quality, promotes health and safety of the welder, and is excellent for environmental considerations. Contact the Pit Crew, our team of industry experts, if you’d like a more in-depth guide through selecting the ideal welding wire solution that best suits your next welding project.
Start welding with confidence today using our high-quality welding wires! Order a sample today!
Learn MoreDISCLAIMER: This information is descriptive in nature and not purely prescriptive. Refer to your own welding machine’s user manual for proper settings and consult a welding expert for support.