Welding Wire for Carbon Steel MIG Welding
Oct 23rd 2023
MIG (Metal Inert Gas) welding, often referred to as GMAW (Gas Metal Arc Welding), is a popular and versatile welding process used in various industries, including energy, automotive, and construction. It’s a flexible process that is incredibly easy to learn, making it the more comfortable choice for beginners. It can be used with any welding position on carbon steel of various thicknesses, from 24-gauge to 1/2-inch thick.
When it comes to MIG welding carbon steel, choosing the ideal welding wire is critical for achieving strong, reliable welds. There are various types of wires commonly used in MIG welding for carbon steel, and each of these wires features its own characteristics and applications.
Welding Wire for MIG Welding Carbon Steel
Welding wire is the essential piece to properly MIG welding on carbon steel as it forms the solid and reliable connection between the two metals. Welding wire comes in a variety of types, lengths, and diameter, and the choice of which one to use can significantly impact the quality of the weld.
ER70S-6 Copper-Coated MIG Welding Wire
ER70S-6 is one of the most widely used solid welding wires for MIG welding of carbon steel. It is classified as an AWS A5.18/ASME SFA 5.18: ER70S-6 wire. This is a mild steel welding wire that typically contains silicon and manganese, which contribute to good arc stability and minimal spatter. It also offers good wetting action and excellent bead appearance.
ER70S-3 Copper-Coated MIG Welding Wire
ER70S-3 is similar to ER70S-6 but has slightly lower levels of silicon and manganese, making it ideal for applications where reduced silicon content is preferred. This includes welding thin materials or over light levels of rust and mill scale. Similar to ER70S-6, this welding wire provides good arc stability and clean welds with less silicon content.
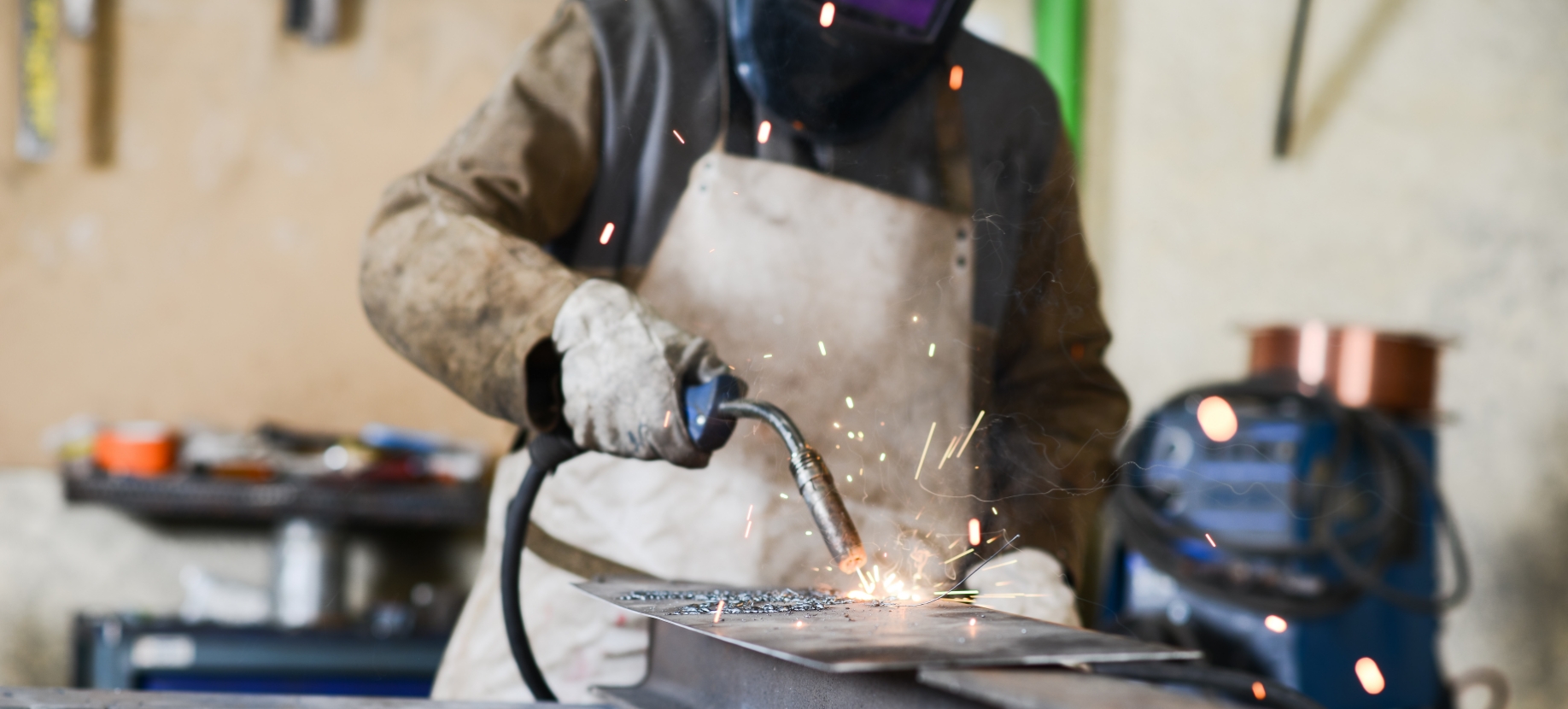
ER70S-(3/6) Copper-Free MIG Welding Wire
ER70S-(3/6) is also similar to the standard ER70S-6, except that it features no copper coating for use in environments or applications where copper in the weld can be problematic. It maintains good weldability while eliminating the risk of copper contamination, ensuring the integrity of the weld in sensitive environments.
E71T-1 Flux-Cored MIG Welding Wire
E71T-1 is a flux-cored welding wire that is popularly used in MIG welding of carbon steel. Classified as AWS A5.20/ASME SFA 5.20: E71T-1, this type of welding wire is a tubular wire with a flux core that provides the necessary shielding and arc stability. It’s often used in heavy-duty fabrication where high welding speeds and good penetration are necessary. It also offers excellent weld bead appearance, minimal spatter, and high productivity.
NS ARC Quality Welding Wire
Choosing the right carbon steel MIG welding wire is essential for achieving high-quality welds when working with carbon steel. NS ARC carries a wide selection of high-performing and reliable welding wires in various specifications. Our solid wires like the NS National-Arc™ Copper-Glide™ NS 115 and the NS National-Arc™ Copper-Glide™ NS 101 are excellent and versatile options while our NS National-Arc™ Silver-Glide NS 101 is a copper-free choice for specialized applications. Flux-cored wires like our Tru-Core® E71T-1 offer high productivity and are ideal for heavy-duty welding.
By understanding the properties and applications of these welding wires, welders can make informed decisions to ensure strong, reliable, and high-quality welds in their carbon steel MIG welding projects. For more information or if you would like some expert guidance on selecting the right MIG welding wire for your next carbon steel welding operation, you can contact the Pit Crew, our team of highly skilled experts who can walk you through which NS ARC welding wire is the best choice for the job.
DISCLAIMER: This information is descriptive in nature and not purely prescriptive. Refer to your own welding machine’s user manual for proper settings and consult a welding expert for support.