How to Easily MIG Weld Carbon Steel
Oct 23rd 2023
MIG (metal inert gas) welding is a staple process in the industry that involves continuously moving a solid welding wire and a shielding gas through a welding gun and into a weld pool in order to join two pieces of metal together. It’s often regarded as one of the easiest and most efficient methods of welding, making it a popular choice among hobbyists and professional welders. However, there are ways to make the process even easier, especially for beginners.
The Proper Tools and Equipment for MIG Welding Carbon Steel
When it comes to MIG welding carbon steel, most of the ease comes from being prepared for the process with the right set up and equipment. Since the equipment is doing most of the work, you need to ensure that it’s set up correctly to get the job done right. Each piece plays an essential role in MIG welding, so it’s important to ensure that each piece is properly prepared for the job.
The first and foremost pieces of equipment that you need for the job is your personal protective equipment (PPE). These include the following:
- Welding helmet
- Welding gloves
- Safety glasses
- Flame-resistant clothing
- Welding jacket or apron
- Steel-toed boots
- Respirator or dust mask
- Ear protection
Welding without PPE is incredibly dangerous as it puts your safety on the line. Make sure that all of this equipment is up to standard and replace anything that’s too worn down to guarantee your protection. You’ll find that MIG welding carbon steel is a lot easier when you’re not putting your safety at risk.
The next set of tools that you need is more specific. Remember to keep in mind exactly what type of carbon steel you’re working with since that plays a heavy role in what kind of equipment you need to get the job done right.
- MIG Welder: Your MIG welding machine needs to be compatible with carbon steel. It’s important to check that all of the cable connections are tight and free of any damage. The gun should be firmly connected in order to provide smooth wire feeding with no kinks or damage to the liner or internal components of the gun.
- Gas Cylinder: For carbon steel welding, a common, all-purpose shielding gas is a mixture of 75% argon and 25% carbon dioxide. Welders may also use 100% carbon dioxide, which offers deeper penetration when working with thicker materials. Make sure your gas cylinder is properly connected and secured and the gas flow is adjusted to the manufacturer's recommended settings.
- Welding Wire: The choice of which welding wire to use for the project depends on a number of factors, including the type of carbon steel, the thickness, and the application. In general, ER70S-6 carbon steel welding wire is an excellent choice due to its versatility and weld strength.
- Wire Brush: It is incredibly important to thoroughly clean the welding area using a wire brush. This helps eliminate debris, rust, scale, and other obstacles that could otherwise impair the quality of the weld. It’s also useful for post-weld cleanups.
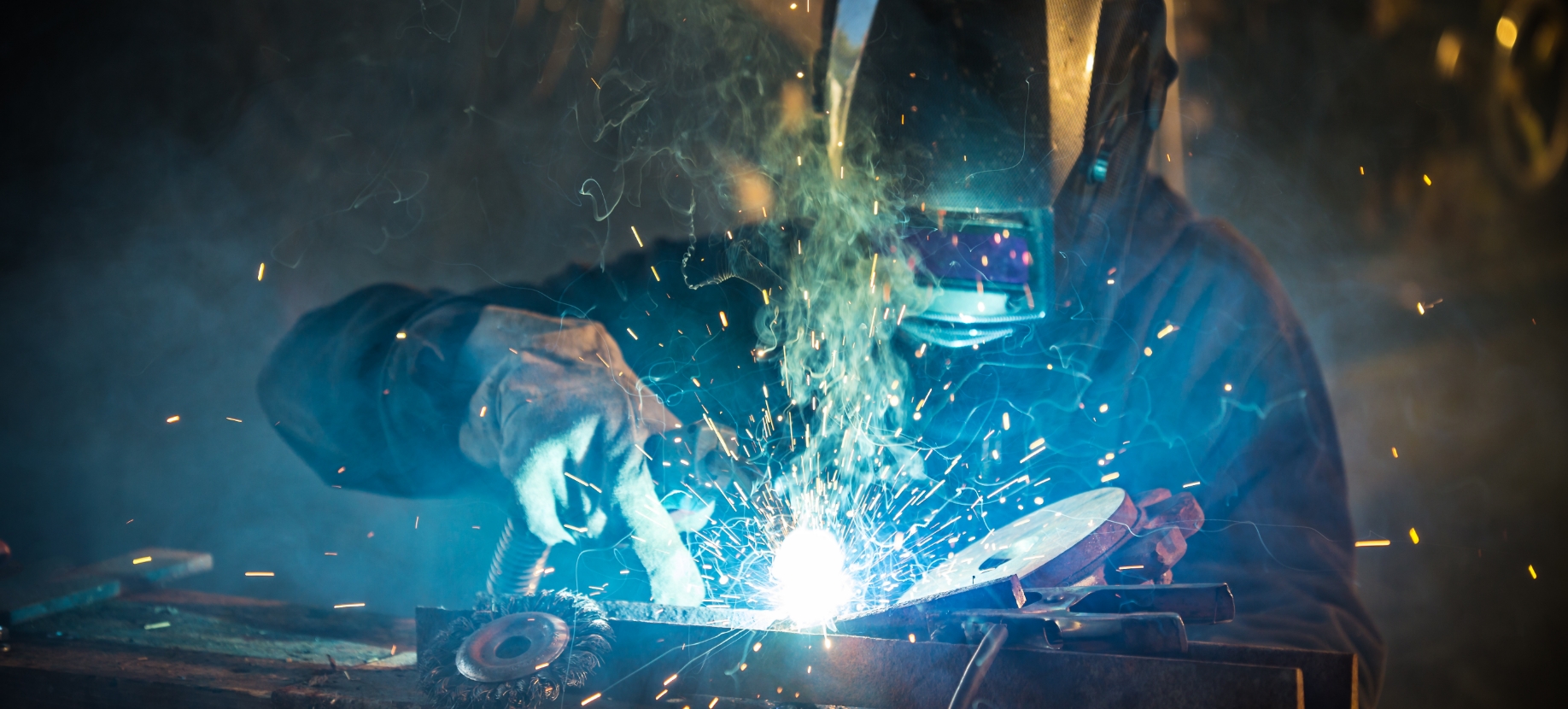
The Steps for a Successful Weld
With everything set, it’s time to begin MIG welding your carbon steel.
Prepare the Equipment & Material
Once you have the right equipment, it’s time to prepare your tools and machines for the job. Thoroughly check your welding machine to ensure that everything is firmly and properly attached with no leaks. Set the wire feed speed and electrode polarity according to the machine’s recommendations. Don’t forget that you’ll need to use your wire brush to completely remove any debris left on the surface of the carbon steel.
Position Yourself
It’s recommended that you stand in a comfortable position with a stable grip on the gun as this job requires a steady hand to ensure a smooth weld. Determine which welding angle you’ll be working in, whether it’s flat, horizontal, vertical, or overhead, and position yourself accordingly. Maintain a travel angle, which is the angle relative to the gun in a perpendicular position, at a steady 5-15 degrees. Going beyond this may result in less penetration, more spatter, and arc instability.
Start Welding
Begin by striking an arc and keeping the welding wire at the leading edge of the puddle. Pay close attention to that puddle as it should be the width of your joint and evenly filling the gap. Keep the contact tip at a consistent distance from the workpiece with a wire stick-out length of about 3/8”. The contact tip to the work distance (CTWD) is relative to wire diameter and amperage settings, so it should be about 3/8" to 1". Be careful not to have too long of a stick-out, which is a common problem welders encounter.
Move in a steady, straight line while maintaining a consistent travel speed and wire angle. Don’t go too fast as it can lead to under penetration, but don’t go too slow as it can cause distortion and excessive weld reinforcement or build-up. The exact speed you move depends heavily on a number of factors that change from job to job. It takes both time and practice to figure out the right combination of welding machine settings, speed, and angle to use.
Complete the Weld
Continue to weld until you reach the end of the joint. Allow the weld to cool down before inspecting it for any defects. If there are any defects, most of the time they can be grinded down. Make sure you use the wire brush to clean the material of any spatter and debris. Post-weld heat treatment may be required and should be performed to remove any stress in the carbon steel if recommended by the alloy of carbon steel being welded.
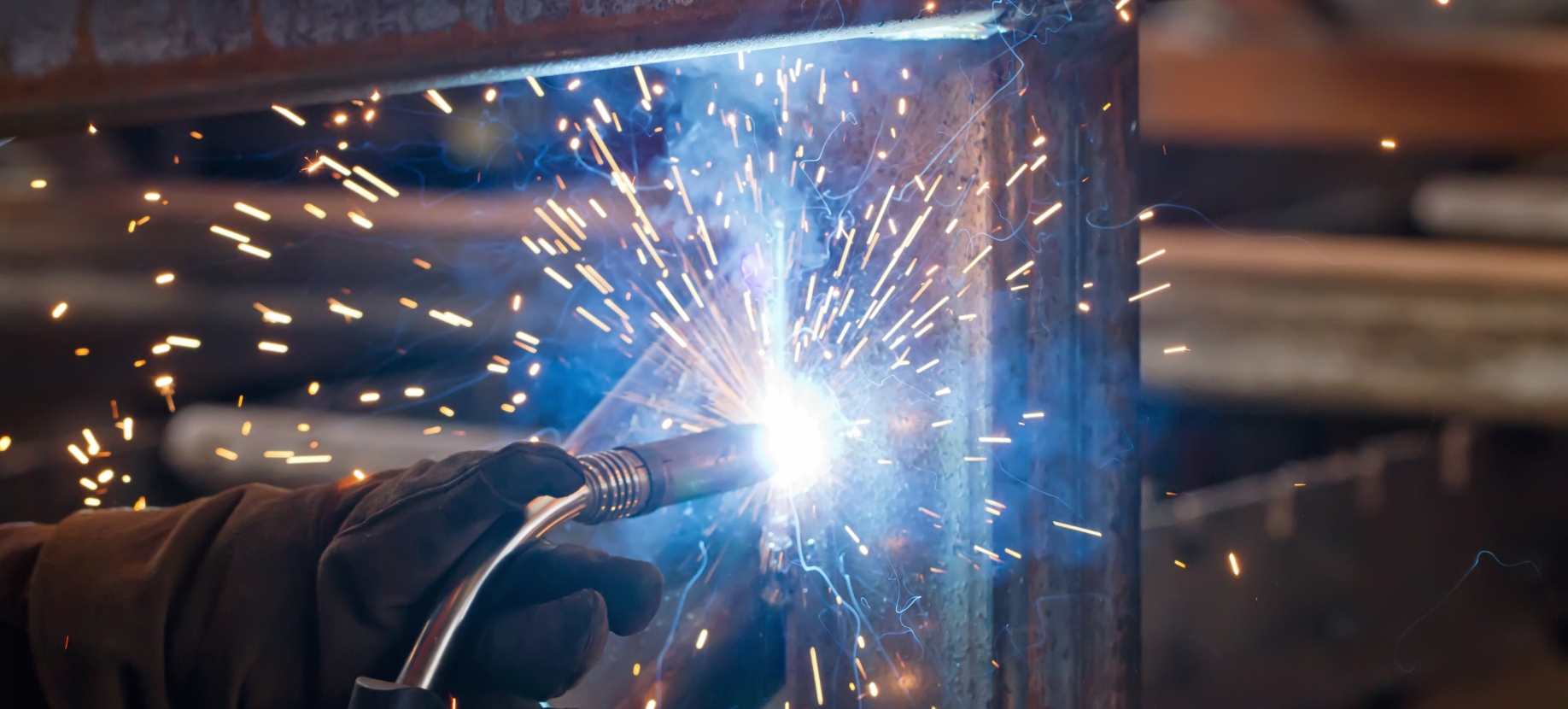
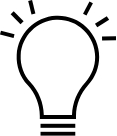
Tips for Successfully MIG Welding Carbon Steel with Ease
Here are some helpful tips to keep in mind while MIG welding carbon steel to make the job a lot easier.
- Produce even and uniform weld beads by maintaining a steady and focused hand. Bead appearance is one important role in the quality of the weld.
- Reduce the amperage or the machine’s temperature setting to minimize the heat-affected zone size and prevent the risk of burn-through.
- Adjust welding parameters as needed to achieve the perfect weld. This can include your travel speed, wire feed speed (amperage), gun angle, voltage, heat input, and welding procedure.
- Clean the area thoroughly, including the material that you’ll be welding, your workspace, and the welder’s gun nozzle. This can help eliminate the risk of contamination.
- Travel smoothly and consistently at the appropriate travel angle. It’s best to avoid sudden starts and stops to maintain a consistent and uniform weld.
- Increase the welder’s temperature when working with thicker materials. It’s also important to match the correct welding wire diameter to the thickness of being welded. For thinner to use 0.023” welding wire to reduce heat input and 0.045” welding wire for thicker metals to increase it.
- Choose the appropriate welding wire for the job. Copper-coated, copper-free, and flux-cored welding wires are often used for welding carbon steel.
- Examine the weld puddle throughout the process to ensure that it’s the appropriate size and shape for the joint.
One of the most reliable and straightforward tips that anyone can ever give on MIG welding carbon steel is practice. In fact, we’ve literally spelled it out for you in each tip that we just gave. Keep tackling these jobs one by one and get a feel for how each job has different tools, settings, positions, parameters, and applications. That’s the surest way to make each MIG welding job easy.
NS ARC Quality MIG Welding Wire
All it takes to make an easy MIG welding job even easier is having the right equipment, especially the welding wire. The welding wire is the heart of any good welding job as it’s what creates the bond that supports the integrity of the project. Over at NS ARC, we carry a wide selection of high-quality and reliable carbon steel welding wires that are engineered to provide unmatched welding strength.
Available in both copper-coated and copper-free options, our carbon steel MIG welding wires are known for their consistency and versatility throughout various industries, including construction, manufacturing, and transportation. Our Copper-Glide™ copper-coated welding wires offer improved electrical conductivity and corrosion resistance while our Silver-Glide™ CopperFree™ welding wires provide superior weld quality and smooth wire feeding. Both types are easy to use and can turn nearly any welding job into an easy and efficient one.
Check out our more in-depth guide to welding carbon steel to become a master of the craft!
Learn MoreDISCLAIMER: This information is descriptive in nature and not purely prescriptive. Refer to your own welding machine’s user manual for proper settings and consult a welding expert for support.