Differences Between MIG vs. TIG vs. Stick Welding
Jan 24th 2024
A successful welding job depends heavily on the choice of the right welding process. MIG welding, TIG welding, and stick welding are three prominent processes, and each one carries its own list of advantages, disadvantages, and characteristics. One technique offers a higher deposition rate, one works excellent on thin materials, and one is reserved for the experts of welding.
Understanding the nuances of these welding processes is essential for welders, whether they’re creating heavy-duty structures, fabricating pipelines, or manufacturing automotive components. Here, we’ll explore what makes MIG, TIG, and stick welding so different to help you understand which one is the best choice for the next welding operation.

MIG Welding Examined: A Guide to Mastering Metal Inert Gas Welding
Metal Inert Gas (MIG) welding, or Gas Metal Arc Welding (GMAW), is a widely used welding process that utilizes a solid wire electrode to produce a weld. This welding wire is continuously fed through a welding gun. A shielding gas is also employed over the area to protect the weld from contamination.
Regarded as one of the easier welding techniques to learn, MIG welding is an excellent choice for those learning the ropes of welding. Its ease and high deposition rate make it suitable for projects that demand efficiency and speed. Additionally, with the welding wire and shielding gas working together, they promote higher weld penetration with a reduction in weld bead porosity.
Offering excellent versatility, MIG welding can be used on a wide range of materials, including carbon steel, stainless steel, nickel, copper, aluminum, and more of varying sizes and thicknesses. This process excels in applications where efficiency and reliability are key, such as automotive manufacturing, construction, and general fabrication.
However, MIG welding is not the most precise welding technique to use for applications that require more control and a more delicate touch. It is also not the most cost-effective due to the need for good-quality shielding gas and equipment. Additionally, the need for shielding gas means that outdoor welding is very limited since drafts blow the gas away and expose the weld to contamination, resulting in possible defects that hinder the quality of the resulting weld.
Preparing for MIG Welding: The Essential Tools, Techniques, and Tips
MIG welding requires a fair amount of preparation before you can start welding. This involves getting the proper tools ready, cleaning the surface, and preparing the joint.
Some of the essential tools needed for MIG welding include a MIG welder, welding gun, the right welding wire, and the appropriate shielding gas. The welding wire choice depends on the size and type of material that’s being welded. The wire should be compatible with the base metal’s composition to achieve optimal welding strength. The choice of shielding gas – whether argon, carbon dioxide, or a mixture of both – also depends on the type of metal and welding wire you’ll be using.
Once you have the right tools, you need to perform some pre-welding preparation in order to produce a strong weld. This involves thoroughly cleaning the base metal and removing any trace of debris, dust, mill scale, and other contaminants. MIG welding is very sensitive to dirty surfaces, so make sure you run a wire brush or other abrasive scrubber over the material.
Joint preparation is also critical. Ensure the edges are clean and free of any defects. If the material is thick, consider beveling or other types of edge preparations to help allow for proper penetration. The joint should align and fit up accurately to ensure consistent welding and minimal distortion. We recommend using clamps, fixtures, or jigs to help keep the joint firmly in place.
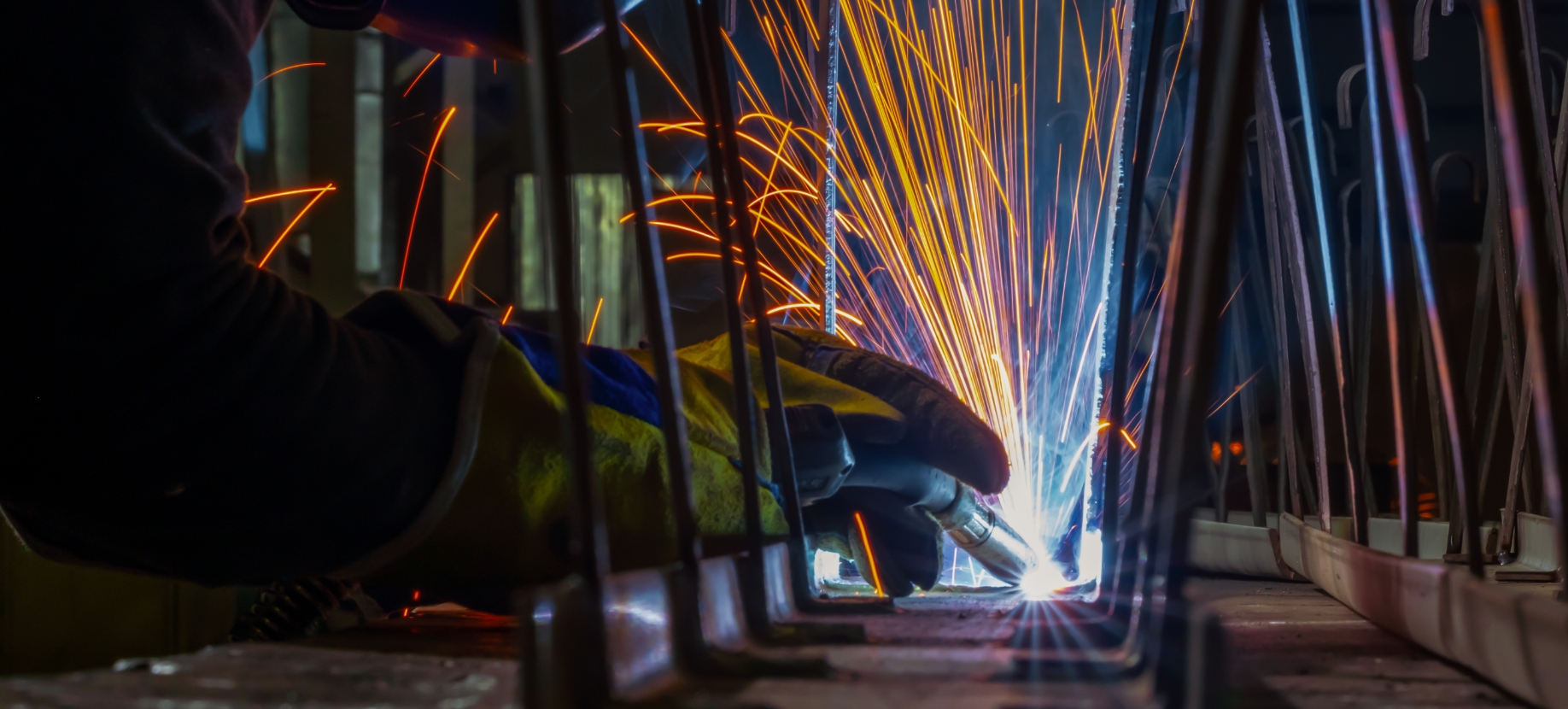
How to MIG Weld Like a Pro
When it's time to start welding, make sure that you maintain a consistent arc length between the welding wire and the material. This keeps a stable arc with the help of proper heat input. Ensure that the weld is penetrating and adhering to the joint by keeping your eyes on the weld pool. Use a steady hand to control the motion of the welding gun. If possible, choose a welding pattern to achieve an even bead appearance and proper fusion.
Once finished, you need to perform post-weld inspections, which involves cleaning the material of any residual spatter and slag and checking the weld for any defects, such as cracks, porosity, incomplete penetration, etc.
Post-weld heat treatment may need to be performed, depending on the type of material you’ve welded, such as stainless steel and aluminum. This helps reduce the level of residual stresses in the joint, restoring the material’s toughness and ductility.
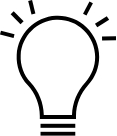
Remember These Pro Tips for MIG Welding
Weld Pool: When you first begin welding, take a second to allow the weld pool to form. Throughout the process, maintain a consistent weld pool size to create a more even weld.
Welding Angle: The MIG weld gun should be held at about a 5 to 15-degree angle for optimal penetration. This can also help reduce splatter when in horizontal and vertical positions.
Travel Speed: Keep the travel speed very consistent and even. Moving too fast can cause lack of penetration while moving too slow can cause burn-through, distortion, and over-welding.
Shielding Gas Coverage: Shielding gas selection depends on a number of factors, such as welding position and material thickness. Carbon dioxide provides deep penetration while Argon provides excellent arc stability. A combination of 75% argon and 25 carbon dioxide balances these advantages and is one mixture option but is a more costly than carbon dioxide alone.
TIG Welding Overview: Understanding the Precision and Craftsmanship
Tungsten Inert Gas (TIG) welding, or Gas Tungsten Arc Welding (GTAW), is another welding process that uses a non-consumable tungsten electrode to produce a weld. Like MIG welding, TIG requires an external shielding gas to protect and cool the tungsten and weld pool. A filler metal can be used to reinforce the weld.
TIG welding is extremely versatile and can be used to combine most ferrous and non-ferrous metals, such as steel, stainless steel, copper, brass, nickel, titanium, aluminum, and more. It’s mostly used in industrial applications that deal with sheet material and require precision control, such as aerospace, automotive, and pipe welding.
Although TIG welding’s travel speeds and deposition rates are relatively low compared to MIG welding, when performed by a skilled operator it works great with thin materials and can create strong and precise welds with visually pleasing bead appearances.
However, TIG welding is one of the more difficult welding techniques to learn. The fine point precision and advanced skill required comes from the fact that there is only a tiny area between the arc and the area being welded, so the welder needs to be in complete control to produce a high-quality weld. On the other hand, with plenty of practice and experience, a welder can develop these skills and grow to be a master at TIG welding.
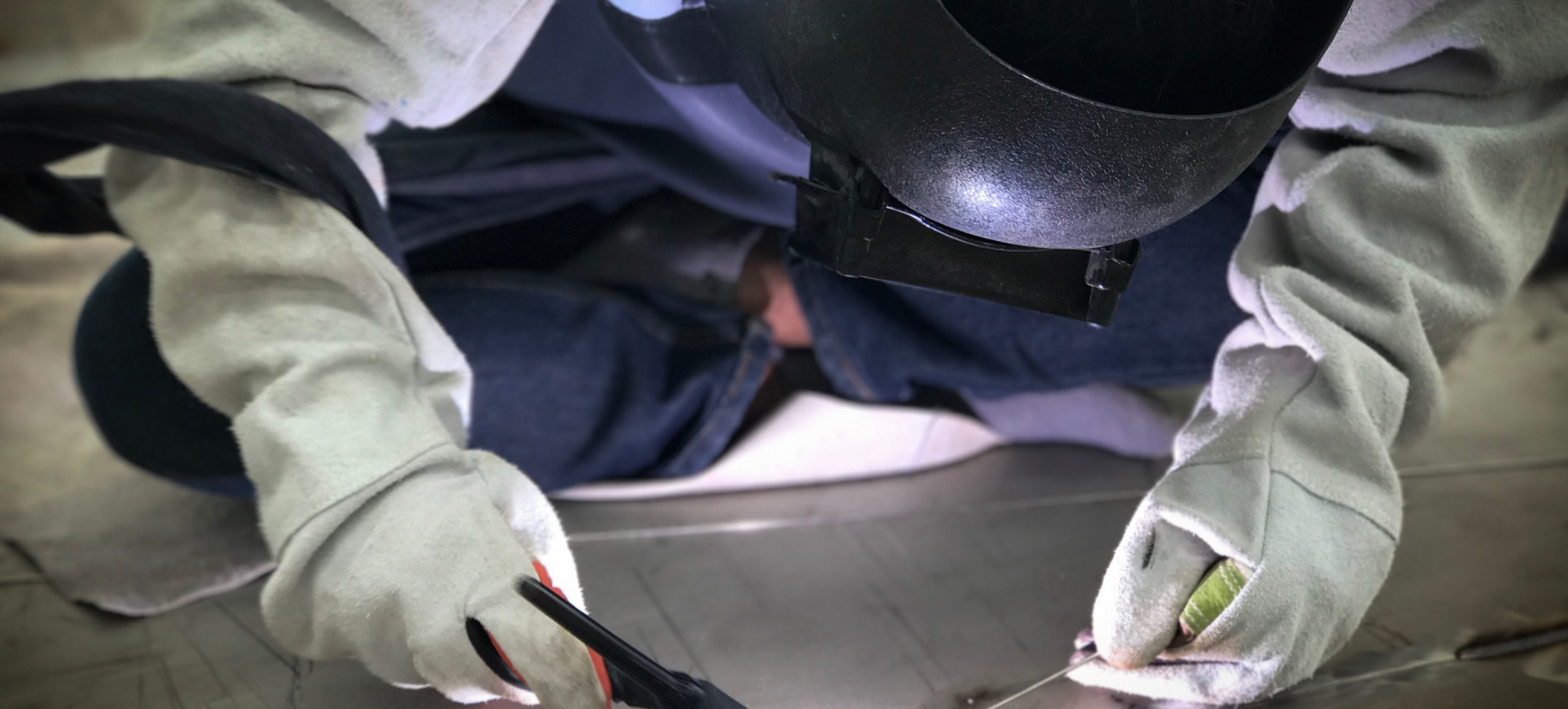
Preparing for TIG Welding: Top Tips, Tools, and Techniques
Preparation for TIG welding is very similar to MIG welding. The surface of the base material needs to be free of any debris to avoid contaminating the weld. Additionally, for this type of welding technique, you will need to select the proper tungsten alloy for the material and application at hand and sharpen the tungsten to a pencil point in order to achieve a successful arc.
In terms of tools, TIG welding requires a power source, cut-length electrode, grounding cable, welding torch, and shielding gas tank. It’s important to perform an equipment check for your TIG welder. Make sure that all components are properly connected, that you’re using the appropriate tungsten for the job, and that all the welding parameters are correctly set.
TIG Welding: How to Master the Craft
When it’s time to start TIG welding, hold the TIG cups tungsten electrode about a half an inch away from the base metal if equipped with high frequency start. Use a remote foot pedal to work the TIG welder to introduce heat to the metal until the weld pool is formed. Once you have the weld pool established, dip the cut-length electrode into the puddle while keeping the molten metal protected by the shielding gas. Drag the arc along the metal to begin welding. The filler metal is typically held in the opposite hand from the TIG welding touch at a 15-degree angle. Gently dab the filler into the weld puddle in a quick and controlled manner as you move across the weld joint. Make sure you keep a steady hand and use the foot pedal to adjust the heat for the best results.
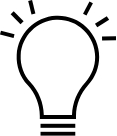
Pro Tips for Successful TIG Welding
Weld Pool: The weld pool diameter will depend on a number of factors, but when starting out, try practicing keeping a weld pool that is about 1/4" wide. Make sure that you keep this size consistent so that it doesn’t grow, shrink, spread, or narrow while you’re welding.
Welding Angle: The torch is kept at a 70- or 80-degree angle with a gap of about 1/8” to 1/4” (depending on amperage) between the tungsten and the workpiece. The filler metal is held at about a 10- to 25-degree angle. Make adjustments as necessary according to the joint type.
Travel Speed: Maintain a steady pace to avoid overheating the metal. Don’t move the torch too fast as it can blow the gas away from the cut-length or the weld pool, which can result in a blackened electrode. This can make starting the next weld extra challenging and leaves the possibility of contaminating the weld.
Shielding Gas Coverage: It's important to utilize the proper shielding gas when TIG welding. The most common shielding gas for this purpose is pure argon, but other mixtures including helium, nitrogen, and hydrogen may be used when special properties are needed. While welding, keep the gas flowing and directed at the weld pool until the orange color fades (typically seen when welding carbon steel). By maintaining post-flow gas coverage, the pool, cut-length electrode, and tungsten electrode can cool properly.
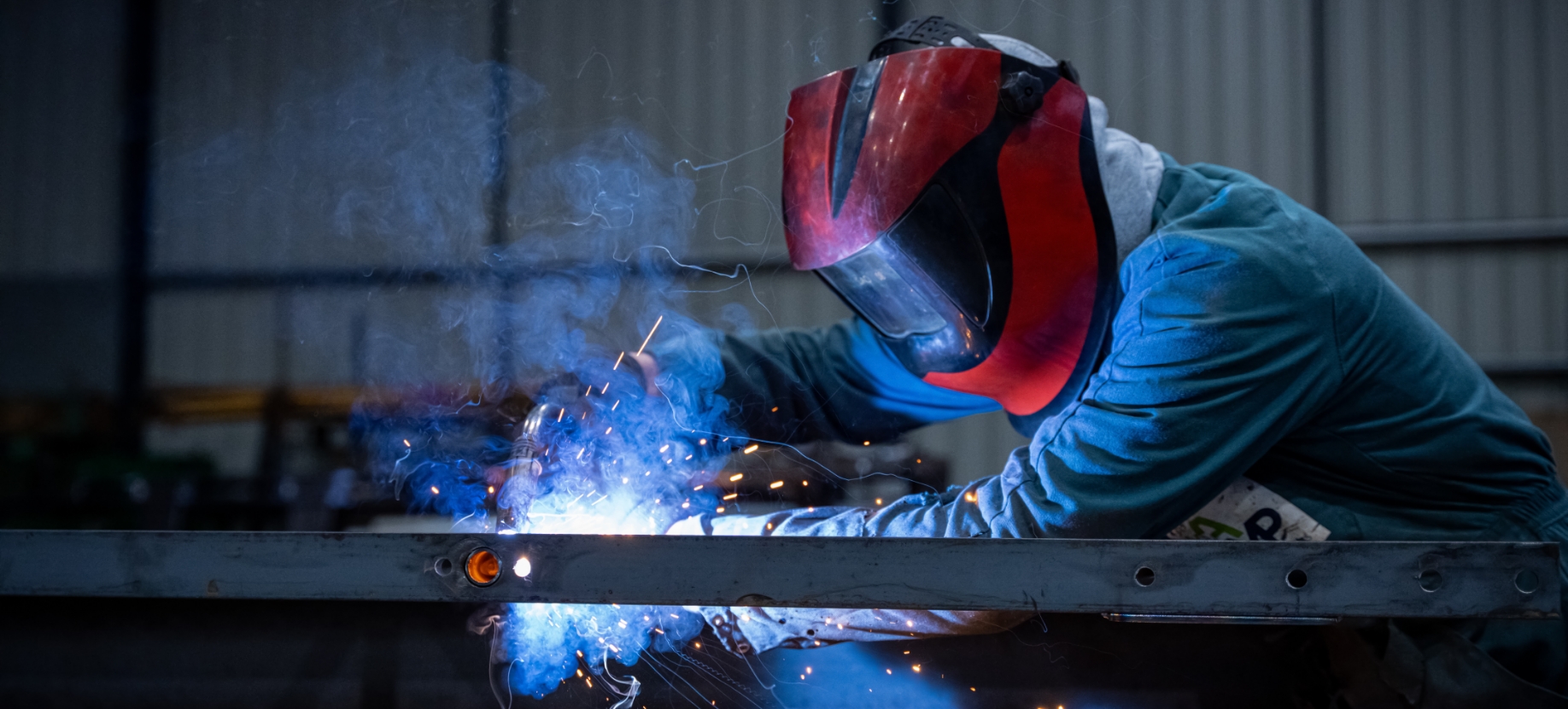
Understanding Stick Welding: When Simplicity Meets Versatility
Stick welding, or Shield Metal Arc Welding (SMAW), is a technique in which a power source is used to create an electric arc between a flux covered electrode and the base material. An arc is ignited by striking the electrode against the metal, which then melts the electrode into the joint to create the weld.
The flux coating on the electrode provides for a shielding gas that protects the arc while the slag layer protects the molten weld from contamination. This means that there’s no need to introduce an external shielding gas.
Stick welding is a straightforward technique that is easy to grasp thanks to its versatility. It’s often utilized in applications that work with various metals, including shipbuilding, pipe welding, and structural steel welding.
Suitable for many construction and repair jobs as well, stick welding is portable and easy to handle. It also has the advantage of being able to be used outside, even in windy conditions, since it doesn’t require external gas. Adaptable and versatile, this method works with various types of metals and is easy to adjust mid-weld because you just need to change the electrode without moving all of the equipment.
However, like most welding techniques, there are a few limitations to stick welding. Though faster than TIG welding, it has a slower deposition rate compared to MIG welding, so it’s not the best choice for jobs that require higher productivity. This method is also very prone to welding defects, requires a high level of skill, and can be challenging to work with thicker metals.
Preparing for Stick Welding: Getting into the Groove
Welding over dirty surfaces is a bit easier with stick welding, but in order to achieve a strong and reliable weld, it’s important to thoroughly clean the surface of the material. The ground clamp should also be placed on a clean spot to help maintain weld quality.
Your stance should be relaxed and in control. It’s best to position yourself in a way that lets you see the weld pool clearly. You need to make sure that you’re welding in the joint and keeping the arc on the leading edge of the pool.
Stick welding requires a welder and welding consumable electrodes. This type of technique uses stick welding electrodes, which come in a range of classifications and sizes for handling different applications and materials. Similar to welding wire, the stick electrode needs to match the base metal with a size that’s relevant to the thickness of the material. You will also need an electrode holder or stinger to hold the electrode.
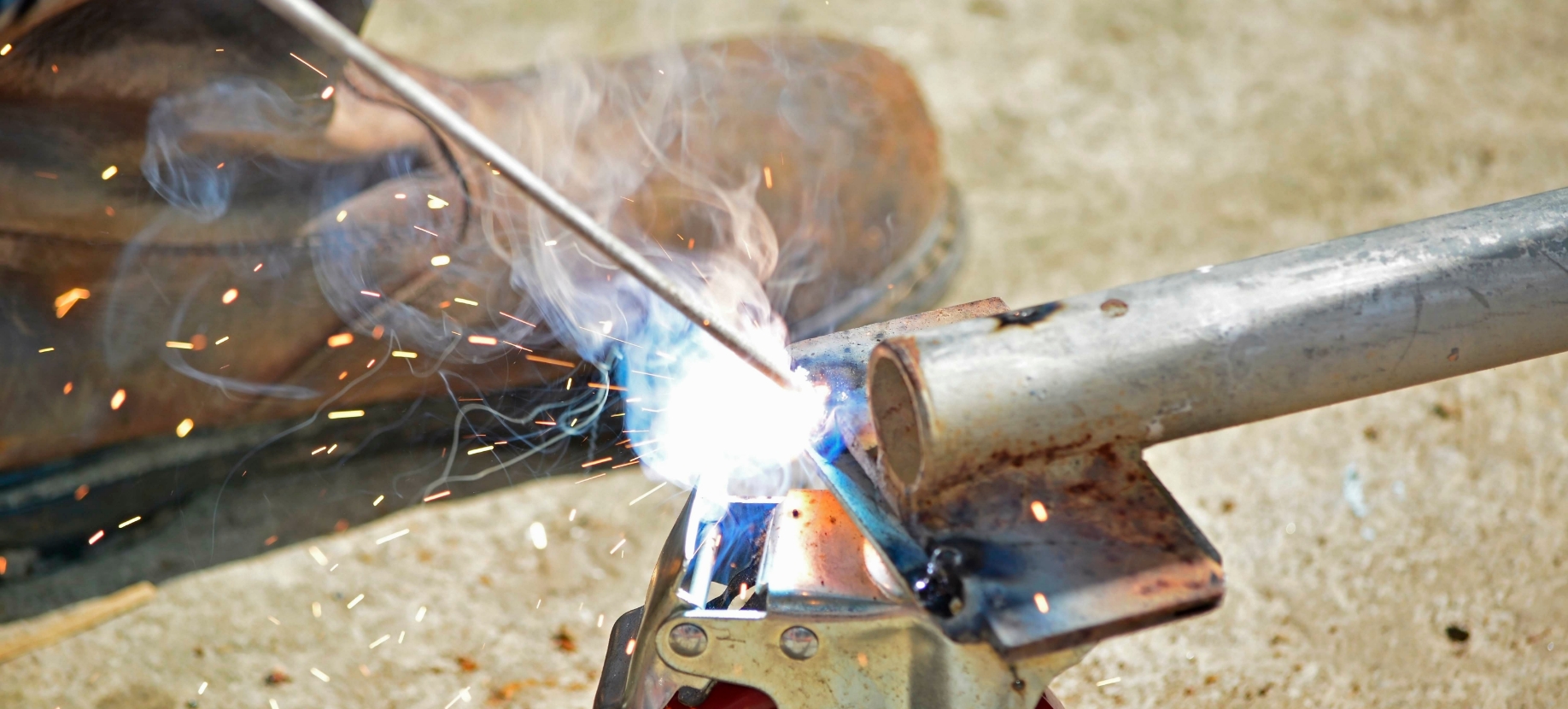
Stick Welding: How to Strike the Arcs and Manage the Slag
Stick welding begins by striking the stick electrode against the metal as if you were lighting a matchstick. Don’t pull it away too quickly, but don’t keep the electrode against the metal. The arc length shouldn’t be longer than your electrode diameter. With the arc ignited, one technique is to simply drag it along the weld with a steady hand. If you lose the arc, simply restart it by scratching the electrode along the metal again. Creating a clean restart may require chipping away the flux or using a wire brush or grinder.
Stick welding leaves behind an increased amount of slag. Slag is the hardened layer that forms on the top of the weld when working with flux-cored welding. It protects the weld from oxidation and contamination from the atmosphere while also keeping the molten weld pool in the joint as it cools. However, it needs to be removed afterwards. The removal process can be time-consuming as it requires you to chip it away using hammers, wire brushes or wheels, or needle scalers.
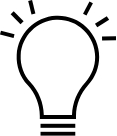
Pro Tips for Stick Welding with Success
Weld Pool: As with MIG and TIG, maintaining a steady and controlled weld pool is a crucial step in achieving a high-quality weld. Keep an eye on the puddle and adjust your welding parameters to stay in control.
Welding Angle: For the welding angle, place the stick into the joint then tilt it slightly sideways by 10 to 15 degrees. It’s important to use a drag (pull) method so you maintain a clear view of the weld during the entire process.
Travel Speed: Your travel speed helps you stay in control over the width of the weld pool. It should be about 1.5 times to no more than 2 times the electrode diameter. Keep this speed as consistent as possible.
Choosing the Right Welding Process for Your Project
So, which welding process is the right choice for your welding project? Given the many qualifying advantages, disadvantages, and applications of MIG welding, TIG welding, and stick welding, there is no one solid answer. The ability to achieve a strong and reliable weld depends heavily on your understanding of each welding technique and how to apply its advantages to the job.
MIG welding is one of the easiest welding techniques to learn, which is perfect for anyone entering the world of welding. It produces robust and heavy-duty welds and is suitable for applications that demand high productivity. It’s not versatile though, so it’s best used for flat and horizontal positions.
TIG welding, while more difficult to master, is a solid process that promotes precision and accuracy, especially on thinner materials. Having a slower deposition rate, it produces high-quality welds with excellent bead appearance and penetration.
Stick welding, in terms of difficulty, lies somewhere between MIG and TIG. It’s a straightforward process with high versatility for all-position welding operations. Although it’s very effective for welding outdoors in harsh conditions, it produces a large amount of slag that needs to be removed, which adds time to the process.
The requirements for the job, the materials you’re working with, the position you’re welding in, your skill as a welder, and the cost of equipment are all factors that affect the welding method. This is important to consider when it’s time to start the next welding operation.
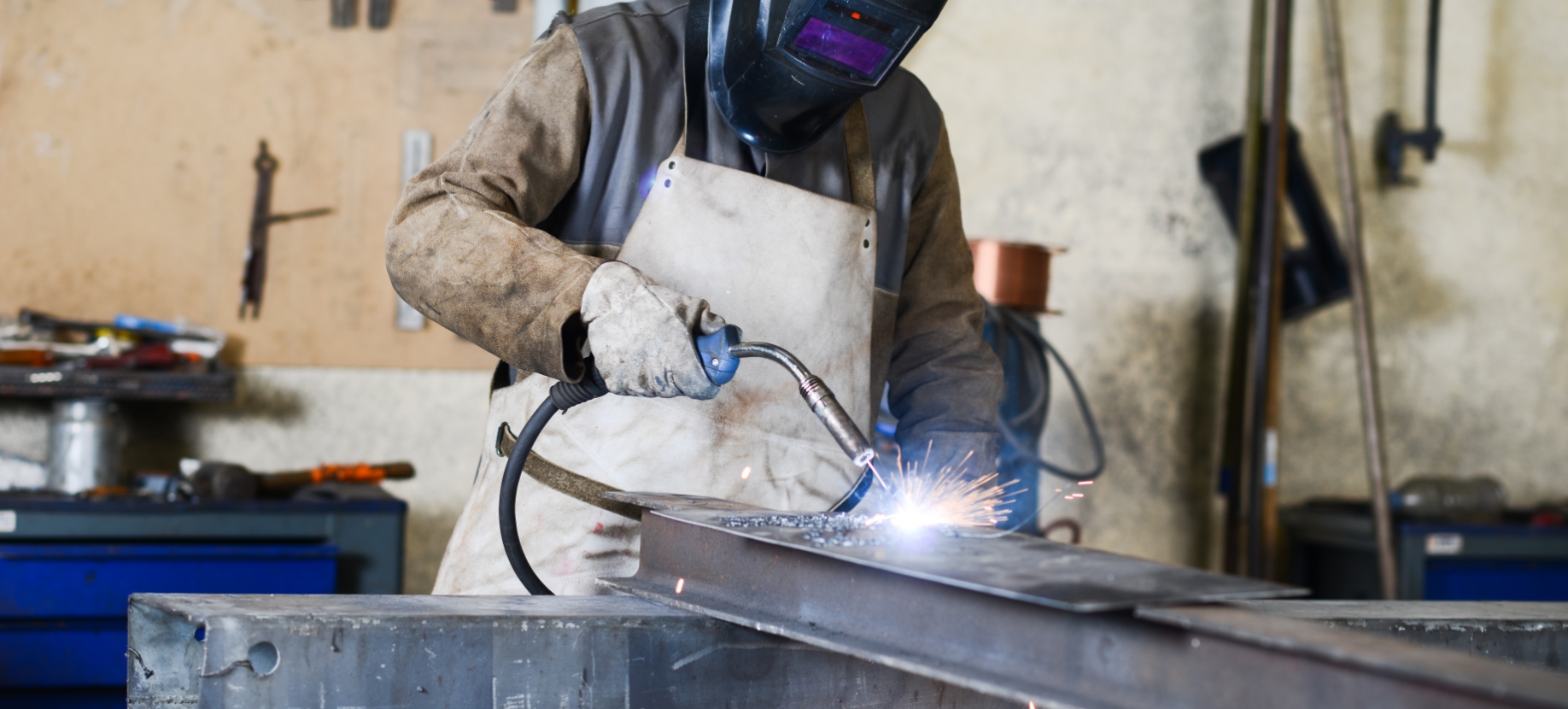
General Welding Tips: Enhancing Your Craft
We’ve compiled some general tips that can apply to nearly any type of welding method.
Always Wear Your PPE: Your Personal Protective Equipment (PPE), including a welding helmet, gloves, welding jacket, and safety glasses, is what stands between you and significant injury while on the job. Always remember to wear every protective piece before welding.
Clean Base Materials: Some welding methods are more forgiving on rusty or dirty surfaces, but in order to achieve the perfect weld with no defects, it’s important to always clean the base material. Thoroughly scrubbing it should be one of your first steps.
Maintain Consistent Travel Speed: It’s important to keep a steady hand and a consistent travel speed to produce quality welds. Moving too quickly can result in a lack of penetration. Moving too slowly can result in excessive heat and burn-through. Practice maintaining a steady pace.
Get the Right Welding Consumable: Choosing the right welding consumable, whether it’s a rod or a wire, can help guarantee an excellent weld result. Make sure you are working with the best available.
Elevate Your Welding Experience with NS ARC Welding Wire
For those looking for the best, NS ARC has you covered with our selection of high-quality welding wires. Available in numerous types and sizes, our welding wire is engineered to provide unrelenting welding strength for the job. The NS National-Arc™ Copper-Glide™ is our line of carbon steel copper-coated welding wires that delivers excellent performance and strength. It’s one of the best choices for nearly any MIG welding production.
If you are looking to weld Aluminum, our Alumi Glide® welding wire line is a versatile option that is available for both MIG weld and TIG weld operations. These wires feature optimized metal flow for precise and controlled weld bead appearance.
For more information, or if you’d like help exploring our extensive collection of welding solutions, contact us today. Our team of experts is ready to introduce you to welding perfection.
Learn MoreDISCLAIMER: This information is descriptive in nature and not purely prescriptive. Refer to your own welding machine’s user manual for proper settings and consult a welding expert for support.