Best Flux-Cored Welding Wire for Mild Steel
Dec 27th 2023
No two flux-core arc welding operations are the same, especially when working with mild steel, one of the more versatile materials to weld for numerous applications. That’s why there’s an extensive number of flux-cored welding wire solutions available that provide the right amount of weld strength to keep the pieces of mild steel firmly welded together. Whichever flux-cored welding wire is considered the “best” depends almost entirely on the type of job you’re working with as well as a number of factors that influence the decision. Let's explore the basics of flux-cored arc welding and what determines the best flux-cored welding wire for mild steel.
Properties of Mild Steel
Mild steel, which is sometimes referred to as low carbon steel or ASTM A36, is a common material that is often used in various industries, including construction, manufacturing, and transportation. With its lower carbon content of about 0.05% to 0.25%, it’s known for its high ductility, making it easier to work with and maneuver into the right shape for the application.
Mild steel is widely used due to its high weldability, allowing any welder to easily work with the material with minimal risk of breaking or cracking it during welding. It’s an excellent choice for flux-cored welding jobs that require optimal strength and unmatched reliability. All it needs is the right flux-cored welding wire that matches the chemical properties of the mild steel so that you can achieve the perfect weld.
Understanding AWS Welding Wire Designations
The American Welding Society (AWS) has created classifications of filler metals for arc welding processes under uniform specifications. For each welding wire classification, every letter and number indicate a very specific detail that helps determine the chemical and mechanical properties of the filler metal. Both gas-shielded and self-shielded flux-cored welding wires have their own designations that designate their properties. For an example, let’s break down the E71T-1C-H8 gas-shielded flux-cored welding wire, which is typically used for heavy fabrication and shipbuilding applications.
E = electrode – flux-cored wires can only be used as electrodes
70 = 70,000psi – this is the as-welded tensile strength in pounds per square inch
1 = welding position – 0 indicates flat or horizontal positions only, whereas 1 indicates all positions
T = tubular wire – this is not a solid electrode
1 = usability designator – 1-14 or “G” (or “GS”) refers to the usability of the electrode with requirements for polarity and general operating characteristics. “G” indicates that the polarity, shielding gas (if any), and general operating characteristics are not specified. “GS” indicates that the electrode is suitable only for single-pass welding.
C = shielding gas type – “C” indicates 100% CO 2, whereas “M” indicates a blend (typically 75% Ar/25% CO2)
H8 = maximum diffusible hydrogen level – this one represents 8 ml/100 grams of weld metal
Understanding these designations can help any welder figure out which flux-cored welding wire is appropriate for the job. After familiarizing yourself with these designations, you’ll be confident enough to grab the right welding wire at just a single glance of the designation.
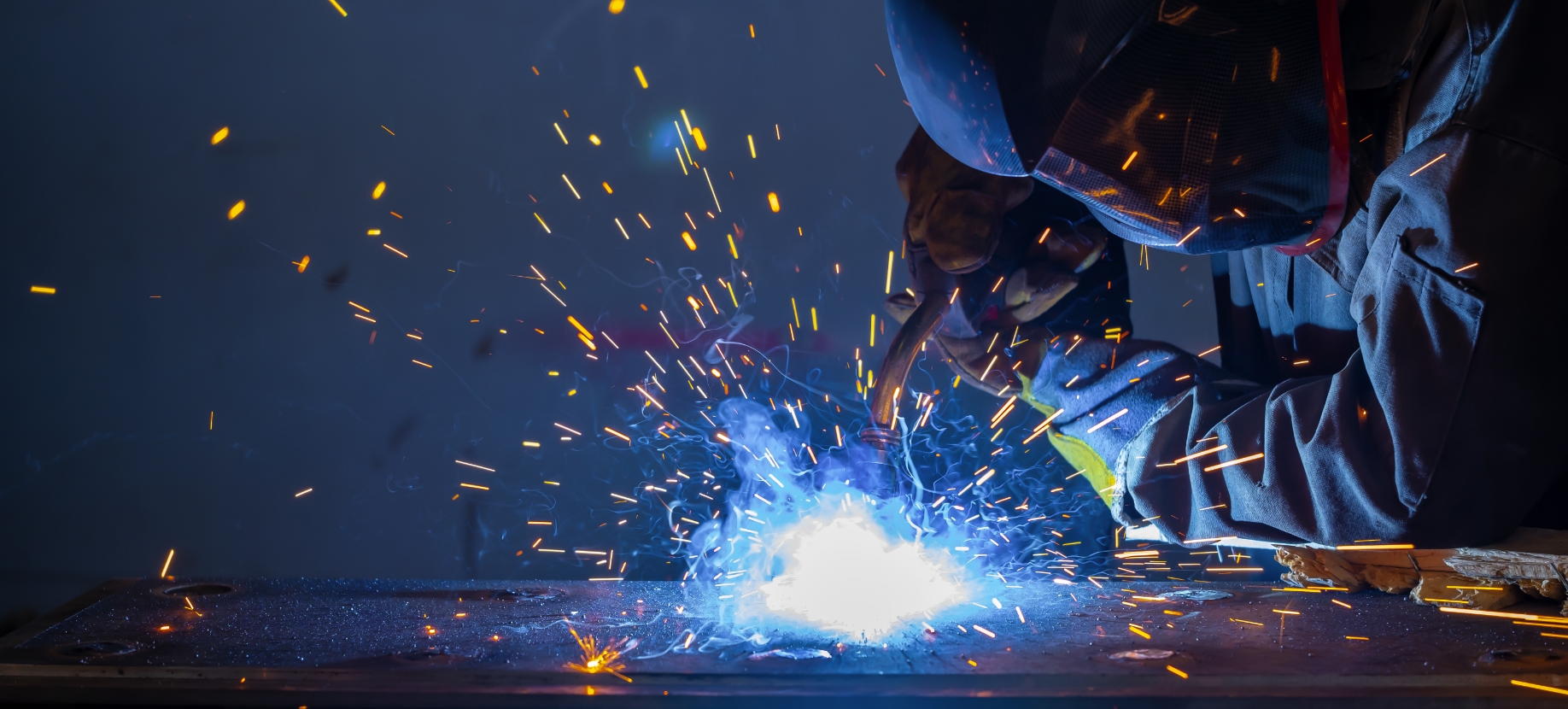
Flux-Core Welding Mild Steel: A Summary
Flux-cored welding, or FCAW, is a versatile welding method that is commonly used on a wide range of materials, including mild steel. It utilizes a continuously fed tubular flux-filled welding wire as opposed to the solid one used in MIG welding. Since it offers higher wire deposition rates and improved arc stability, it’s often preferred for high-speed welding applications, allowing the welder to achieve an excellent weld in less time without sacrificing quality. In most cases, its flexibility also allows for welding in all positions, including flat, vertical, horizontal, and overhead.
The Role of Welding Wire in Flux-Core Welding Mild Steel
Flux-cored welding wire is the heart of any flux-core arc welding operation. Utilizing a weak or incompatible welding wire for the job can result in a weakened bond between the two metals, which could compromise the integrity of the structure as a whole. That’s why it’s very important to carefully consider which welding wire is best suited for the job by reviewing the different types of wire and the factors that influence your decision.
Flux-core arc welding can be divided into two types: gas-shielded, which relies on an external shielding gas, and self-shielded, which relies on the flux core itself to protect the weld pool. Each type comes with its own advantages and disadvantages, depending on the welding application.
Gas-shielded flux-cored welding wires often utilize a blend of argon and carbon dioxide (typically, 25% carbon dioxide and 75% argon). The gas protects the weld pool from oxidation and contamination, resulting in a smoother bead appearance with less risk of distortion. In general, gas-shielded flux-cored welding wires generate cleaner welds with high-quality results, making them the preferred choice among welders.
On the other hand, self-shielded flux-cored welding wires utilize the flux-cored electrode to provide gas protection over the weld pool. The core contains slag-forming fluxing agents that produce shielding gases when exposed to the heat of the arc. This helps to quickly solidify the weld and prevent defects such as cracking while improving the weld’s mechanical properties.
The diameter of either gas-shielded or self-shielded flux-cored welding wires plays an important part in your decision making. Flux-core welding is usually used on thicker pieces of mild steel that require impressive penetration in order to establish a reliable structurally sound weld. Typically, when working with mild steel that’s 20-gauge and above, it’s recommended to use 0.045” diameter or above flux-cored welding wires to match your material thickness. Remember that thicker sheets of mild steel may require multiple passes to achieve a weld that meets your design requirements.
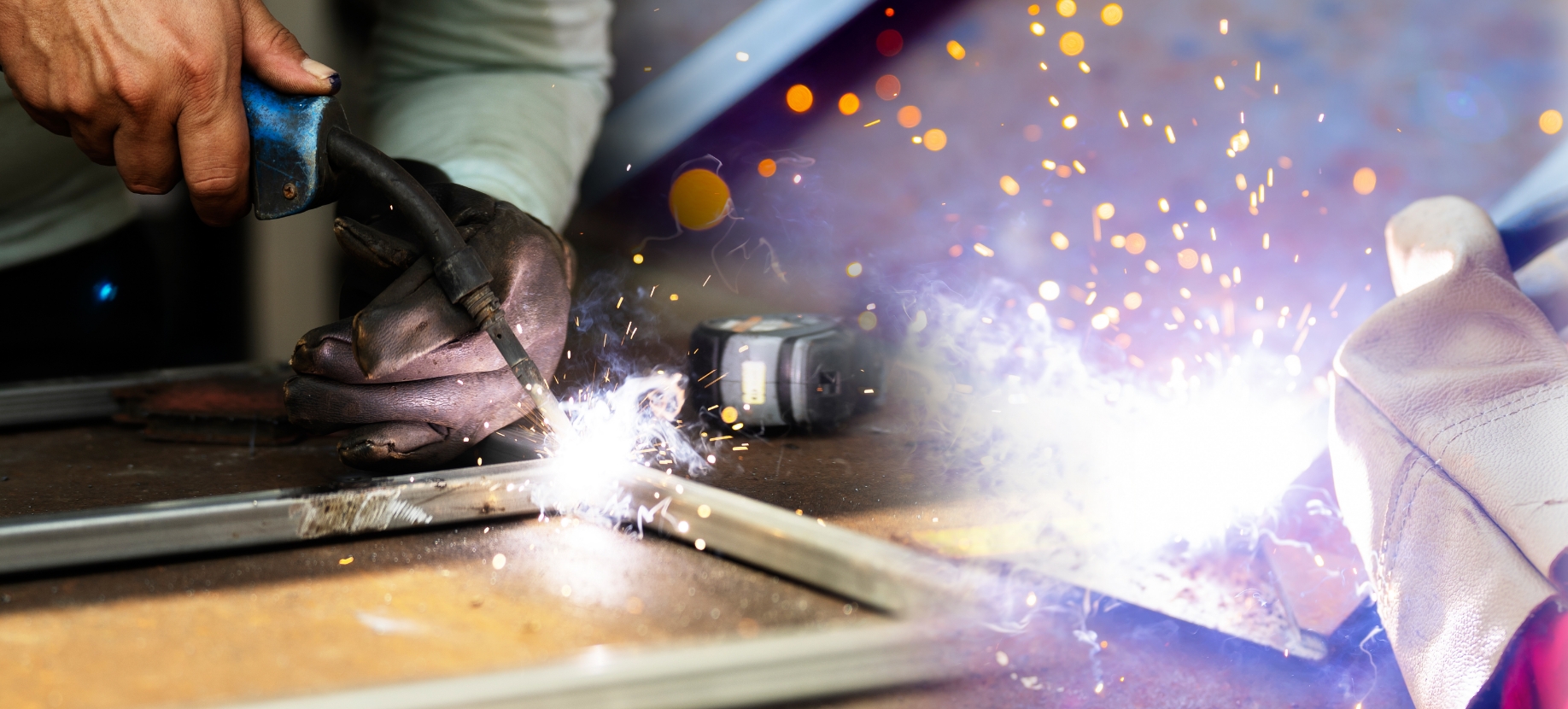
Best Flux-Cored Welding Wire for Mild Steel Welding
As with any low carbon steel welding operation, the choice of which flux-cored welding wire is the best depends entirely on numerous factors that need to be considered before welding. No two welding operations are the same, so there’s always the possibility of one type of flux-cored welding wire being the better choice than another, only for the situation to change and require an entirely different type of wire.
That being said, the E71T series of flux-cored welding wires is commonly regarded as the best general-purpose choice among welders. This type of welding wire provides excellent welding characteristics that improve the overall quality of the weld. Designed for all-position welding operations, it’s often used in projects where the welds undergo significant stress or heavy demands, such as heavy fabrication, trailer, and structural steel applications.
The E71T flux-cored welding wire demonstrates impressive arc performance and excellent weldability while generating quality bead appearance. Its higher deposition rate allows for quicker welding, leading to an increase in productivity. Well-suited for thicker pieces of mild steel, this welding wire delivers high-quality and consistent welds.
NS ARC Quality Flux-Cored Welding Wire for Mild Steel
For the best of the best flux-cored welding wires for working with mild steel, we recommend our NS ARC high-quality and reliable Tru-Core® welding wires. These flux-cored welding wires are engineered to provide unbeatable weld strength that works flawlessly with mild steel. Offering deep penetration capabilities, these wires deliver smooth stable arc transfer to ensure precise control and maneuverability.
Our Tru-Core ® flux-cored welding wires boast a wide range of exceptional welding characteristics that help improve nearly any mild steel welding job that you encounter. Most of our versatile wires can be used for all-position welding for greater flexibility. With excellent feedability for smooth wire feeding, our welding wires promote fewer interruptions, leading to increased productivity down the line.
Order a sample today to start welding with flux-cored welding wires designed to handle the toughest jobs with maximum strength and reliability.
Learn MoreDISCLAIMER: This information is descriptive in nature and not purely prescriptive. Refer to your own welding machine’s user manual for proper settings and consult a welding expert for support.