There are no products listed under this category.
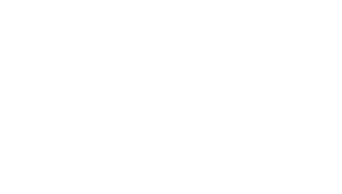
Women-Owned Business
NS ARC MIG (Metal Inert Gas) welding wire is of high quality and is manufactured to exceed industry standards. Easy to use and able to produce clean and tidy welds that require minimal cleanup, our MIG welding wire remains an industry standard for a reason. We offer MIG welding wire in different materials such as carbon steel, stainless steel, and aluminum alloys.
There are no products listed under this category.
Two popular welding processes are MIG welding (GMAW) and TIG welding (GTAW), and each requires a different welding technique.
MIG welding stands for Metal Inert Gas welding, also known as Gas Metal Arc Welding (GMAW). In MIG welding, a consumable wire electrode is fed continuously into the weld pool via a machine. The electrode causes the metals to heat up to their melting point, which creates the joint. The weld can be protected from contamination by a shielding gas, which is usually a mixture of argon and carbon dioxide. MIG welding wire is also generally thicker than TIG welding wire, ranging from 0.023 to 0.045 inches in diameter. Available in a wide range of metals and sizes, MIG welding wire is a versatile welding solution that is commonly used in many different industries.
TIG welding stands for Tungsten Inert Gas welding, also known as Gas Tungsten Arc Welding (GTAW). This type of welding is a slower process that requires far more skill and precision than MIG welding. In TIG welding, a non-consumable tungsten electrode is used to heat the metal and create the weld pool, while a hand-held filler wire (typically) is used to add filler material to create the weld. Ranging from 0.010 to 0.125 inches in diameter, TIG welding wire spans a wider range than MIG wire, and thus is unique in its application.
MIG welding wire utilizes a welding gun for semi-automatic feeding while TIG welding wire is welded by hand with the use of a tungsten electrode.
MIG welding is a faster process than TIG welding while TIG welding can produce high-quality, precision welds.
In general terms, TIG welding requires more skill and precision than MIG welding.
MIG welding wires are used to fill the gaps between different types of metals in varying applications. Each type of welding wire is designed for specific purposes. Here are some common types of welding wires that we offer:
Aluminum wire is specifically designed for welding aluminum and is available in both MIG and TIG varieties. Aluminum wire is softer than other types of wire and boasts unique features like a high strength-to-weight ratio, excellent ductility, and resistance to corrosion.
Flux-cored wire is another popular type of welding wire. This wire has a flux core, which is ideal for situations requiring a high-quality weld that increases both versatility and productivity.
Carbon steel is a popular choice for many welding projects due to its dependable strength, durability, and relatively low cost. Carbon steel welding wire is therefore highly versatile and can be used to weld a wide range of carbon steel materials, from low- to high-carbon steel. Thanks to its reliability and cost-effective nature, carbon steel welding wire is a popular choice among welders. Some carbon steel wire even features a unique copper coating on the exterior of the wire to enhance electrical conductivity and improve arc stability and feeding.
Metal-cored welding wire is similar to flux-cored wire in that it features a filled core, but instead of a flux material, the core is filled with metal powder. This metal powder core produces a stable arc with the outer shell creating a conductive path for the welding current, which provides excellent control and very high deposition rates. This means the welding process becomes far easier and faster to clean post-welding, lending to a highly efficient welding process. These qualities make metal-cored welding wire a popular choice for semi-automatic and automatic welding applications.
Stainless-steel wire is used for welding stainless steel, and boasts unique features like high weld strength, corrosion resistance, versatility, hygienic properties, and more. Utilized in a range of applications like fabrication, construction, and repair work, stainless-steel welding wire is popular in numerous industries, including aerospace, oil, gas, food, and much more.
When choosing a welding wire, it is crucial to consider the type of metal being welded, the application, and the service conditions to which the finished product will be subjected. Choosing the right type of welding wire ensures a high-quality weld, reduces the risk of welding defects, and improves the overall welding process. If you require direct consultation on which type of welding wire is the best choice for your application, simply reach out to us today. One of our experts will quickly be in touch with you to discuss the right welding solution for your business!
Many different industries take advantage of the speed and efficiency that is gained from the MIG (GMAW) welding method. As a versatile welding process, it can be used for a wide variety of applications that require a reliable way to join solid metals.
This industry requires efficient welding in order to join components together, such as body panels and other sheet metal. It’s the ideal choice as it produces clean, precise welds that require minimal cleanup. It works well with the bodywork, chassis and frame assembly, exhaust systems, and engine components.
Learn moreMIG welding is also commonly used in the construction industry for welding structural steel and other metal components, such as piping, bridges, sheet metal, and staircases. This type of welding can be used on both thin and thick sections of metal to quickly produce strong and reliable welds.
Learn moreMIG welding can also be used in the energy industry for welding pipelines, storage tanks, power plants, generators, and other equipment and structures. MIG welding produces clean and solid welds on high-strength materials, with successful results that can be resistant to corrosion and fatigue, which is essential in this demanding industry.
Learn moreMIG welding is a fast and efficient welding process that is ideal for mass production in the manufacturing industry. As a versatile method, it can be integrated into automated welding systems within assembly lines for high-speed, consistent welding. Fabrication, metalworking, and repair and maintenance can also be completed with this method.
Learn moreThe transportation industry uses MIG welding for various applications, including the welding of car frames, trailer beds, and other components. MIG welding wire is utilized in this industry because it provides a strong and durable weld that can withstand the stress and strain of moving vehicles. It is also a fast and efficient process that can be used to weld large and complex structures.
Learn moreMIG welding wire is also a popular choice in other applications that often benefit from MIG welding wire’s easy-to-use functionality, consistency, and efficiency. Some of the other applications that utilize NS ARC MIG welding wires include:
Commonly used in the agricultural industry for welding farming equipment such as plows and cultivators. MIG welding also assists in equipment repairs and maintenance jobs to fix damaged components quickly.
The upper section of railcars and some railcar frames utilize MIG welding wire for their construction and fabrication along with passenger cars and tankers.
When it comes to the welding of high-strength steels, MIG welding is the right method to use, especially in the shipbuilding industry that often utilizes those materials to construct vessels. Whether it’s hull construction, deck structures and fittings, or pipe welding, MIG welding produces strong welds that help to ensure the integrity of the vessel.
Because MIG welding is a widely used and versatile welding process, many industries take advantage of NS ARC MIG welding wire’s many benefits in order to produce clean and effective welds. It’s a fast and efficient welding technique that produces welds with minimal cleanup, making it a popular choice for a wide range of welding applications.
MIG welding is a popular welding process that uses a spool or bulk package of welding wire with an electrical arc to join two metal pieces together. Compared to Stick (SMAW) and TIG (GTAW) welding, which are slower processes, MIG welding does not require frequent electrode changes, making it a more versatile and highly efficient method for production. Here are some of the benefits of welding with MIG welding wire:
This wire is a fast-welding process, meaning it can be used to quickly complete welding projects. The continuous wire feed system allows for faster welding, making it ideal for large-scale projects.
MIG welding produces less waste than other welding processes, such as stick welding, where not all the welding rod is consumed and produces significantly more waste. Instead, MIG welding uses a spool or bulk package of wire that is continuously fed into the weld.
MIG welding wire can be used to weld a wide range of metals, including stainless steel, aluminum, carbon steel, and more. With several diameters and types available, it is also suitable for welding thick and thin material, depending on the wire’s penetration and the application requirements.
MIG welding wire is known to produce high-quality welds while remaining simple to learn, easy to clean, and efficient to use. The quality of MIG welds is due in part to the wire’s good penetration and fusion characteristics, which creates strong, durable, and in some applications, corrosion-resistant welds.
With MIG welding, there’s a high deposition rate, which means it can deposit more weld metal in less time than other welding techniques. This is particularly useful when welding thicker materials and decreases cleanup time and increases overall efficiency.
MIG welding is relatively easy to learn and can be mastered with practice, making it an excellent option suitable for beginners. The MIG welding process can be more forgiving when compared to other types of welding, meaning it’s a great place to start and develop skills that transfer to other welding processes.
These benefits make MIG welding a popular choice for various applications, including manufacturing, automotive repair, and construction. If you require direct consultation on whether our MIG welding wire solutions are a good fit for your business, simply reach out to one of our experts today. We’ll be happy to discuss your situation and find the best solution for your application.
Our team of welding experts is available to provide you with the information that you’re looking for, whether you need some guidance or advice for your next welding project or you’re not sure which welding wire best suits your application.
If you have any questions before making a purchase chat with our online operators to get more information.
Ask An Expert or find our Questions & Answers