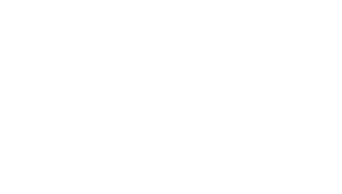
Women-Owned Business
The copper coating of carbon steel welding wire provides superior electrical conductivity and improved arc stability while also ensuring excellent corrosion resistance during storage. Often used in gas metal arc welding (GMAW) and submerged arc welding (SAW) applications, copper-coated steel welding wire is perfect when you require a consistent, long-lasting, and dependable solution. Copper-coated welding wire should be avoided, however, in applications where the presence of copper may cause issues. Please utilize our copper-free welding wire for superior results.
Copper-coated welding wire is a tool like any other in your arsenal. It has its uses that help bring out the best welds for the job. It also requires proper care in order to preserve its strength and capabilities. How to best use this wire entirely depends on the specific welding application and the type of welding being performed. This is subject to change per project, but there are some general guidelines that can help to ensure the best results.
The wire needs to be stored in a dry, clean area to prevent moisture and contaminants from affecting the quality of the wire. Typically, wire is stored in its original packaging, but it can also be stored in a sealed container or in a wire feeder to protect it from dust, dirt, and other contaminants from reaching the wire. Additionally, you should make sure that the base metal is properly cleaned before use. This helps you achieve a higher quality weld. Make sure that the metal is cleaned and free of any dust, dirt, grime, etc., before welding to ensure proper fusion and adhesion.
Before beginning the weld, you need to make sure that you have selected the correct diameter of welding wire, which is critical for achieving a quality weld. The diameter of the wire should be matched to the thickness of the metal being welded to ensure proper penetration and weld strength. Proper shielding gas is also essential for the job. The type of gas used depends on the type of welding that needs to be done, but a common choice is a mixture of argon and carbon dioxide.
Additionally, the correct amperage settings are important for achieving the right weld characteristics when using copper-coated welding wires. Starting welding parameters are provided by the manufacturer’s recommendations for the specific type and diameter of welding wire being used.
Please remember it is the responsibility of the consumer to validate and verify weld quality.
If you have any questions regarding the right amperage to use, our team is available to guide you through the perfect welding job.
If you have any questions before making a purchase chat with our online operators to get more information.
Ask An Expert or find our Questions & Answers