There are no products listed under this category.
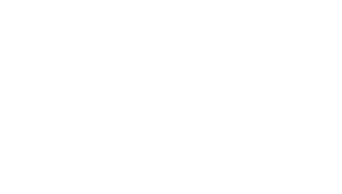
Women-Owned Business
Carbon steel MIG welding wire is used in a variety of welding applications because it can serve as a filler material that can help to join two pieces of metal together. When using carbon steel MIG welding wire for welding, the wire is melted and added to the joint to strengthen the weld and provide a more secure bond.
There are no products listed under this category.
NS ARC has a full product breadth of carbon steel MIG welding wires including both Copper-Glide™ copper-coated and Silver-Glide™ CopperFree™. The decision to use copper-coated or copper-free welding wire depends on several factors, including the welding process, the type of material being welded, and the specific application. It's always a good idea to consult with a welding expert or reference materials before making a decision. Our team is here to help, so contact us for more information and for any tips for your welding job.
Copper-coated welding wire is often used in the gas metal arc welding (GMAW) process and submerged arc welding (SAW) process. The copper coating provides several benefits, including improved electrical conductivity and better arc stability. The copper coating also helps to protect the welding wire from corrosion during storage, which can help to ensure the wire remains in good condition for longer periods of time.
On the other hand, copper-free welding wire may be preferred in certain applications where the presence of copper can be problematic. In these cases, copper-free welding wire may be a better choice.
Carbon steel welding wire can be coated with copper to provide a number of unique benefits in certain applications, including:
Carbon steel welding wire with copper coating features improved electrical conductivity thanks to copper's properties. This can help to improve the quality of the overall weld and reduce the risk of potential defects.
Copper is highly resistant to corrosion, so having the copper coating on the wire effectively protects it from corrosion. This is especially important in applications where the carbon MIG wire may be exposed to moisture in the form of humidity prior to use.
The copper coating on carbon steel welding wire aids in ensuring smooth and consistent feeding during the welding process. Smooth wire feeding ensures greater control and produces a consistent and uniform weld.
Copper-free welding wire is a reliable alternative to copper-coated wire that offers a considerable number of different benefits, including:
Welding with copper-free wire can improve the quality of the weld. This is essential for ensuring that the bonded materials remain structurally sound, even when faced with demanding applications.
Copper is also a known irritant and can cause health problems when it is inhaled or ingested. Welding with copper-free wire can help to reduce the risk of health problems for the welder and anyone else in the area. With proper ventilation, this is a good choice for welding in confined spaces to help reduce the risk of health complications.
In addition to being potentially harmful to people, copper is a heavy metal that can be toxic and harmful to the environment. Welding with copper-free wire can help to reduce the amount of copper that is released into the environment, which is especially important in areas where environmental regulations are strict.
Carbon steel welding wire is an essential tool that provides numerous benefits across a wide range of industries, including automotive, construction, energy, and manufacturing. Its strength and durability make it an ideal material for repairing and replacing damaged components in automotive and heavy equipment applications. It is also highly resistant to corrosion and chemical exposure, making it an excellent choice for welding pipelines, pressure vessels, and structures in the energy and construction industries. In manufacturing, carbon steel welding wire is a readily available material for welding various components and structures. With its versatility, availability, and affordability, carbon steel welding wire has become an indispensable tool for professionals across these industries, helping them to balance performance and reliability while maintaining the highest level of quality and safety.
Many automotive applications require the use of carbon steel welding wire for fabrication and repairs. Some of these applications include exhaust systems, frames, suspension components, and more.
Learn moreCarbon steel MIG wire is often used to weld structural steel in buildings, bridges, and other large-scale construction projects thanks to its excellent strength properties, making it ideal for use with thick materials.
Learn moreOne of the major benefits of using carbon steel MIG welding wire is its strength and durability, making it ideal for withstanding extreme temperatures and pressure fluctuations, which is imperative within the energy industry.
Learn moreCarbon steel MIG welding wire is widely used in manufacturing and fabrication. Applications like metal products, heavy machinery, and consumer goods are common.
Learn moreBecause this type of welding wire is very versatile and easy to use, it's a common choice among welders within the transportation industry as it allows them to work with a variety of materials with greater efficiency.
Learn moreCarbon steel MIG welding wire offers several unique benefits to the welding process and is suitable for a wide range of applications in several industries, making it a widely popular choice for steel repair and fabrication. Some of the major benefits of carbon steel MIG welding wire include:
Carbon steel MIG welding wire is known for its high strength and durability, making it an ideal choice for applications that require strong, reliable welds. It has the necessary strength for intense welding applications, such as welding construction equipment, pipes, trailers, and more.
Because NS ARC Copper-Glide™ Carbon Steel MIG welding wires are known for reliability and consistency, our customers are often able to save money in other areas such as downtime, rework, scrap, and other consumables such as shielding gas and tips.
Carbon steel MIG welding wire is highly versatile and can be used in a wide range of welding applications, including construction, automotive repair, and manufacturing. Having a supply of carbon steel MIG welding wire on-hand can be an efficient way to tackle several different types of welding jobs in an industry.
Carbon steel MIG welding wire is relatively easy to work with and is a good choice for novice and experienced welders. Thanks to its highly consistent and uniform properties, welders find carbon steel MIG welding wire to be easy to control, including the wire’s ductility. Well-established and widely used welding parameters make carbon wire simple to use with different machines.
Thick materials, such as structural steel, require a solid and reliable wire to get the job done. Carbon steel MIG welding wire is often used for these purposes because of its strength and durability, making it an excellent choice for heavy-duty applications.
This type of wire is compatible with a wide range of welding equipment, including both MIG and TIG welders, which makes it a good choice for those working with different types of welding machines. This also means that carbon steel wire can be used for a wide range of applications, providing high-strength welds to nearly any kind of project.
Overall, if you need a strong, cost-effective, and versatile welding wire that is easy to use and compatible with a range of equipment, NS ARC Copper-Glide™ carbon steel MIG welding wire is an excellent choice.
Carbon steel welding wire is used in a wide variety of welding applications thanks to its compatibility and highly adaptable qualities. Some of the most common applications for using carbon steel welding wire include:
Agricultural equipment and heavy farm equipment are often constructed with carbon steel for long-lasting and dependable stability and functionality, making carbon steel MIG welding wire the obvious choice.
Carbon steel welding wire can be used to repair and replace damaged panels and components due to its strength and versatility, which allows to welder to work with a wide variety of different materials.
Due to its natural resistance to corrosion and its ability to withstand high-temperature environments, carbon steel welding wire is a popular choice for welding automotive exhaust systems.
Carbon steel MIG welding wire is often used for the fabrication of large components and structures in heavy equipment manufacturing due to its high strength and toughness, ensuring that the resulting bond is secure and reliable.
When it comes to general fabrication as well as heavy-duty fabrication, many welders can benefit from the versatility, strength, and durability, this type of welding wire is a popular choice as it effectively bonds various components and structures together.
Because carbon steel welding wire is highly resistant to corrosion and chemical exposure, it’s the right choice for a variety of pipe welding applications that often occur in tough environments.
This type of job often deals with harsh welding conditions, so carbon steel welding wire’s high strength and ability to withstand extreme temperature and pressure conditions make it the ideal choice for pressure vessel applications.
In an industry that demands security in its welding, many welders opt for using carbon steel MIG wire for the fabrication and repair of railcar components in the rail industry due to its ability to weld thick materials.
Carbon steel welding wire is commonly used to fabricate and join various components, including beams, columns, and trusses, in building and structural applications. Thanks to its high strength, it’s excellent for heavy-duty applications that depend on structural security.
When it comes to trailer manufacturing, carbon steel MIG welding wire is an essential tool that is commonly used for the fabrication of frames, suspensions, and other critical components.
Carbon steel MIG welding wire is used to weld ships and other marine structures, which must be able to withstand harsh environments and heavy use. With carbon steel’s high strength, long-lasting quality, and simple usability, shipbuilding and weld repairs are easier and more efficient to produce without sacrificing reliability.
Whether you’re looking for individual spools or operating hundreds of robots in a production environment, NS ARC has a package that will maximize your productivity, reduce downtimes associated with change-outs, and utilize pay-off systems that produce quality welds.
Drums are excellent for large-scale operations. The wire is packaged inside in a loose coil form. It takes on a large sine wave or an “S” shape.
Our traditional fiber spools feature the wire randomly wound on the spool. Our wire baskets, on the other hand, feature precision layer level wound. Both of these packaging options meet ISO 9001:2015 quality standards.
Our Smart Pak® boxes contain a barrel similar to our normal drums except a Smart Pak® is 100% recyclable. This helps to reduce waste and cuts down on the amount of space taken up by the drums in the trash. There are multiple engineered wire dispensing solutions as well. These packages are also designed with a lifting strap for easier placement in your production facility.
Our high-quality Tru-Trac® wood reels feature “Twist-free” wire let-off from a stationary tightly wound reel that requires only a few ounces of drag from up to 150’ from the wire feeder. This packaging is designed to maximize productivity and lower welding costs. The ability to stack reels minimizes the amount of space needed during storage and production vs a drum. The snag-free operations without drive roll overload deliver precise joint tracking while the wire maintains a consistent cast.
Our team of welding experts is available to provide you with the information that you’re looking for, whether you need some guidance or advice for your next welding project or you’re not sure which welding wire best suits your application.
If you have any questions before making a purchase chat with our online operators to get more information.
Ask An Expert or find our Questions & Answers