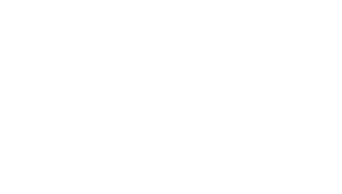
Women-Owned Business
Aluminum welding wire features an array of excellent benefits unique to itself. Distinctly lightweight and usable for a range of applications in several industries, aluminum wire boasts several advantages, including:
Aluminum welding wire is a reliable and efficient choice for welding aluminum structures and components, and it offers many benefits compared to other types of welding wire. Check with your welding wire manufacturer as to recommendations to ensure aluminum welding wire is the right choice for your application. If you require direct consultation, simply reach out to us today and one of our NS ARC Alumi-Glide® experts will help you find the best solution.
The best way to take full advantage of your aluminum welding wire depends on the specific application and the welding technique being used. However, there are some general guidelines that can help ensure successful welds when using aluminum welding wire.
First and foremost, you need to make sure that the area is thoroughly cleaned. Aluminum is highly reactive and can quickly form a layer of oxide on the surface. Before welding, it is important to clean the metal surface with a stainless-steel brush or a stainless-steel wire wheel to remove any oxide or other contaminants. This will help to ensure a strong and reliable weld.
The type of welding method used is incredibly important. Aluminum welding wire can be used with a variety of welding techniques, including MIG and TIG welding. The best technique will depend on the specific application and the desired outcome. For example, MIG welding may be faster and more efficient for larger projects, while TIG welding may be better for smaller, more detailed work. The type of filler material is equally important. Aluminum welding wire comes in a variety of grades and alloys, each with different properties and characteristics. It is important to choose the right filler material for the specific application to ensure a strong and reliable weld.
Also, make sure that you are using the right welding settings. For example, it may require a higher voltage and lower wire feed speed. It is important to follow the manufacturer’s recommendations for the specific welding wire being used. Steps should also be taken to avoid warping. Aluminum has a low melting point and can be more prone to warping or distortion during welding. To prevent warping, it may be necessary to use a lower heat input or to preheat the metal before welding.
Using aluminum welding wire requires attention to detail and careful consideration of the specific application and welding technique being used. By following best practices and taking steps to ensure a clean, strong, and reliable weld, it is possible to successfully use aluminum welding wire for a variety of applications.
If you have any questions before making a purchase chat with our online operators to get more information.
Ask An Expert or find our Questions & Answers