Welding Carbon Steel to Stainless Steel
Oct 23rd 2023
Welders generally have to handle various types of different metals, including various grades of carbon steel and stainless steel. Welding carbon steel to stainless steel presents a unique set of challenges due to the contrasting properties of these two materials. Let’s take a moment to explore the complexities of welding carbon steel to stainless steel, the potential issues that arise, and the solutions to overcome this challenging operation in order to achieve a successful weld.
Understanding Carbon Steel and Stainless Steel
Carbon steel and stainless steel are two of the most common metals that are welded in a variety of industries, including transportation, energy, construction, and manufacturing. Each presents its strengths for certain applications. For example, carbon steel promotes improved flexibility and durability for high-demanding operations while stainless steel offers its natural corrosion resistance for applications where moisture is present. Exploring each material’s unique properties and grades can help welders understand where their strengths lie.
Carbon Steel Properties
Carbon steel is an alloy primarily composed of iron and carbon. It is known for its strength and durability, making it a popular choice in construction and manufacturing industries. However, it is susceptible to corrosion in certain environments.
There are three common grades of carbon steel. They are listed as the following:
Low Carbon Steel:
- Composition: Contains 0.05-0.30% carbon (C) with small amounts of other elements
- Characteristics: Ductility, easily machinable, and good weldability; relatively low strength and hardness
- Applications: Automotive manufacturing, general fabrication, and trailers
- Filler Metals: Weld using mild steel welding wires
Medium Carbon Steel:
- Composition: Contains 0.31-0.60% carbon (C) with additional alloying elements
- Characteristics: Offers a balance of strength, hardness, and ductility. Suitable for applications requiring moderate strength
- Applications: Agricultural equipment, general fabrication, and infastructure
- Filler Metals: Weld using low-alloy welding wires, depending on the specific alloy and application
High Carbon Steel:
- Composition: Contains 0.61-1.50% carbon (C)
- Characteristics: Extremely hard and wear-resistant but lacks ductility and toughness
- Applications: Agricultural equipment, general fabrication, and railcars
- Filler Metals: Not typically used for welding due to its brittleness; if welding is required, specialized procedures and preheating may be necessary
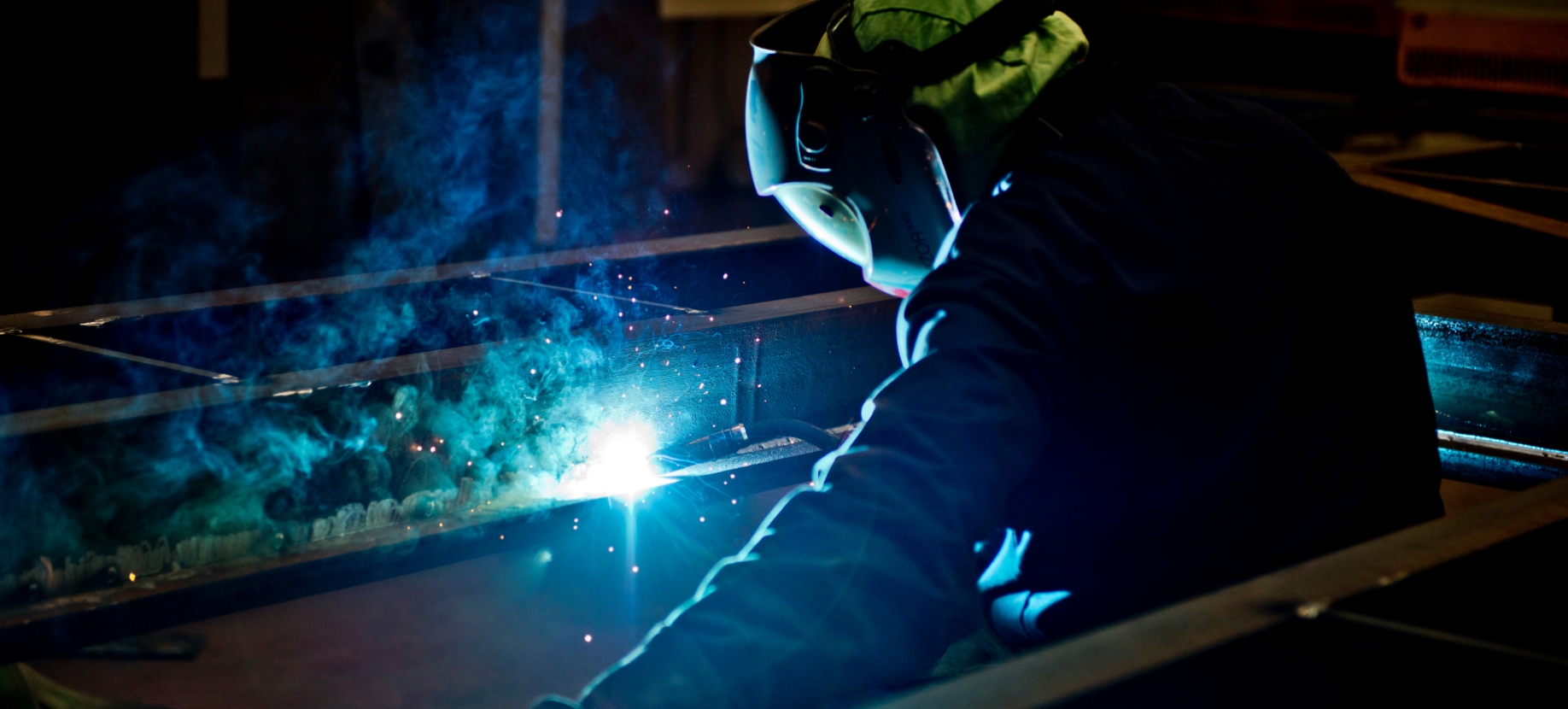
Stainless Steel Properties
Stainless steel is an iron-based alloy that contains variable amounts of chromium and other elements. This material is renowned for its exceptional corrosion resistance, making it ideal for applications where exposure to moisture or aggressive chemicals is a concern, such as in shipbuilding and pipe welding.
There are five grades of stainless steel that have been classified according to their material properties and welding requirements. They are listed as the following:
Austenitic Stainless Steel:
- Composition: 16-26% chromium (Cr) and 8-22% nickel (Ni)
- Characteristics: Low thermal conductivity, sensitivity to hot cracking, and susceptibility to carbide precipitation
- Applications: Automotive manufacturing, structures, and general fabrication
- Filler Metals: Weld with matching composition welding wires; some alloys require ferrite inclusion
Ferritic Stainless Steel:
- Composition: 10.5-30% chromium (Cr) and up to 0.20% carbon (C)
- Characteristics: High thermal conductivity and low carbon content; reduced risk of sensitization and intergranular corrosion
- Applications: Automotive exhaust, heavy equipment, pressure vessels, shipbuilding
- Filler Metals: Weld with matching or exceeding Cr level welding wires
Martensitic Stainless Steel:
- Composition: 12-18% chromium (Cr) and up to 1.20% carbon (C)
- Characteristics: High hardenability and sensitivity to cracking
- Applications: Automotive manufacturing, general fabrication, and railcars
- Filler Metal: Weld with welding wires matching base metal elements or austenitic filler metals for toughness
Precipitation Hardening Stainless Steel:
- Composition: 14-17% chromium (Cr), 4-30% nickel (Ni), and other alloying elements
- Characteristics: Sensitivity to heat input and requires post-weld heat treatment
- Applications: Shipbuilding, pipe welding, and heavy fabrication
- Filler Metals: Weld with welding wires matching base metal elements; results depend on type of precipitation hardening stainless steel
Duplex Stainless Steel:
- Composition: Austenitic-ferritic combination with 22-26% chromium (Cr), 4-7% nickel (Ni), and 0-3% molybdenum (Mo)
- Characteristics: Requires balanced heat input for ferrite-austenite ratio and susceptible to intermetallic phase precipitation
- Applications: Pipe welding, pressure vessels, and infrastructure
- Filler Metals: Choice of welding wire depends on the application and material properties
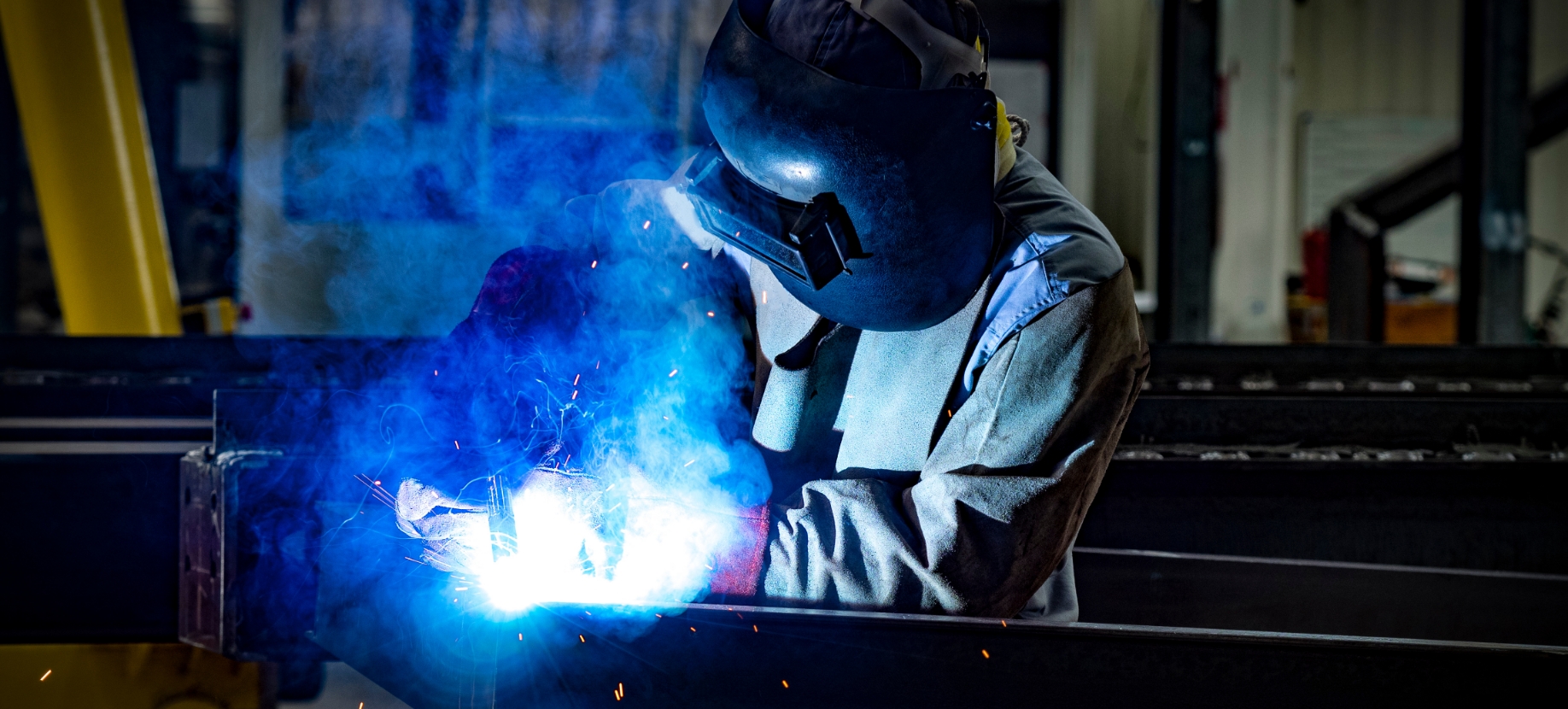
Challenges in Welding Carbon Steel to Stainless Steel
As you can see, these two types of materials and their grades present varying strengths and weaknesses. It’s not simple to just mix these materials while welding. These two dissimilar materials can be a challenge to work with since they have different thermal expansion rates, electrical conductivity, and thermal conductivity. During welding, these variations can cause stress and distortion in the weld joint.
Another challenge comes from their chemical composition. Carbon steel contains carbon, which can readily combine with the chromium in stainless steel during the welding process. This can lead to the formation of brittle iron-chromium compounds, reducing the corrosion resistance of the stainless steel.
The heat-affected zone (HAZ) of the stainless steel near the weld can become vulnerable to corrosion if not properly protected during welding. Additionally, since stainless steel is so susceptible to sensitization, it’s extra vulnerable when welded with carbon steel. Post-weld heat treatment is crucial for these situations.
Solutions for Welding Carbon Steel to Stainless Steel
So, can carbon steel be welded to stainless steel? The quick answer is yes! The long answer is that several precautions and steps need to be taken before beginning, during, and after the welding operation. To address the challenges associated with welding these dissimilar materials, these approaches can be taken.
As with any welding project, the choice of welding wire is crucial. The welding wire needs to be compatible with the chemical and mechanical properties of both types of materials. For example, welding austenitic stainless steel to low-carbon steel can be accomplished using a 309L welding wire to reduce the risk of intermetallic compounds forming while still achieving a strong weld. Introducing this buffer layer of a compatible welding wire creates a bridge between the carbon steel and stainless steel.
One general rule to keep in mind is that when welding dissimilar materials together, the welding wire should match or slightly exceed the mechanical properties of the weaker material.
Heat input is also incredibly important. You need to employ proper welding techniques to control heat input so that you can minimize the risk associated with the materials' microstructures. This includes maintaining precise welding parameters and avoiding excessive heat buildup. Precision and control throughout the entire welding process go a long way in protecting the integrity of the materials and the weld.
Post-weld heat treatment is often employed to alleviate residual stress and enhance the integrity of the weld. It also helps with minimizing sensitization and restoring the corrosion resistance in stainless steel. The specific process utilized depends on the grades of the materials.
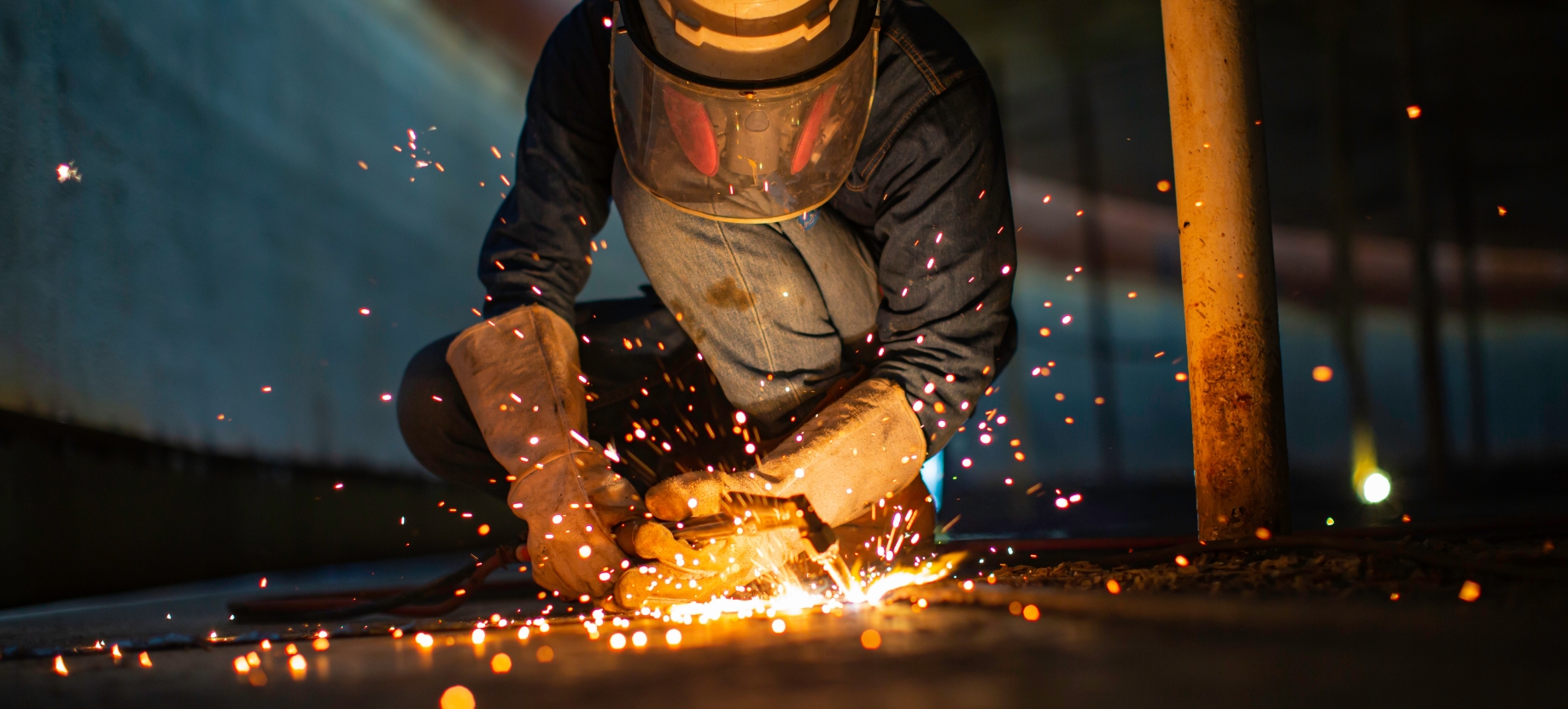
NS ARC Quality Welding Wire
Welding carbon steel to stainless steel is a complex process that requires careful consideration of material types, welding wires, and potential issues. While it can be challenging, with proper preparation and execution, successful welds can be achieved. It's important to consult with experienced welders and engineers, follow recommended welding procedures, and prioritize the quality and integrity of the joint when undertaking such welding projects.
When it comes to operations that call for the welding of these dissimilar materials, NS ARC offers a wide selection of both carbon steel welding wires and stainless-steel welding wires, each type engineered by our experts to promote a strong, sustainable, and reliable weld. Our NS National-Arc™ Copper-Glide™ NS 115 is the ideal choice for a premium mild steel solid filler metal for carbon steel. Likewise, our Satin Glide® 309L is one of the best choices for austenitic stainless-steel and the joining of dissimilar metals.
In situations in which you are unsure of which type of welding wire is best suited for joining carbon steel with stainless steel, contact our Pit Crew. Seeking the appropriate guidance before starting the welding operation can save immensely down the line. Our team can provide the right advice and information for your welding wire selection and can also help ensure that your next welding operation is a smooth one.
Get yourself a sample of NS ARC welding wire to start successfully welding carbon steel and stainless steel together!
Learn MoreDISCLAIMER: This information is descriptive in nature and not purely prescriptive. Refer to your own welding machine’s user manual for proper settings and consult a welding expert for support.