Guide to Butt Joint Welding
Jan 24th 2024
Butt welding is a fundamental technique that many welders practice during a welding operation. It involves joining two pieces of material together at their ends, forming a 180-degree angle, which is known as a butt joint. The two pieces end up side by side with no overlap. It’s a simple and versatile technique that is used in numerous applications and industries, especially when fabricating structures or pipe systems.
Butt Joint Welding
When creating a butt weld, two materials are placed closely together, and in some instances, with a gap of approximately 3mm (1/8”) between them. This gap helps ensure proper penetration through the entire joint. If it’s too small, there won’t be enough penetration, but if it’s too big, it can create a bulky seam on the other side of the metal. To close this gap, the welder strikes an arc, introduces the filler metal, creates a pool of molten metal, and then moves the pool along the joint while continuously adding the filler. This creates the butt joint, holding the two pieces together.
A versatile operation, butt joint welding can be applied to various materials, including carbon steel, stainless steel, and aluminum. A successful weld depends on proper cleaning and preparation of these materials. It’s especially crucial to clean the joint surfaces thoroughly to remove contaminants. Additionally, beveling and edge preparation help create a groove for the weld, allowing for better penetration for a stronger result, but the amount and type of preparation required depends on the type of butt joint.
In order to successfully create a butt joint weld, a welder needs the precision and skill required for the task. It takes experience and a steady hand in order to tackle some of the more complex butt joints, such as the double U butt joint or double V butt joint. The right equipment is also needed, of course, but this depends on the project and its specifications, including the welding process (MIG, TIG, Stick, etc.), welding wire or electrode, material type, and material thickness. Always make sure you’re welding while wearing the appropriate PPE (personal protective equipment), especially the right welding helmet, gloves, and other safety gear.
Exploring the Different Types of Butt Joints
Butt joints comes in various shapes, and most are named after those shapes. Each of these shapes serves a different purpose with different factors that include the shape of the groove, layering, and width of the gap. Some butt joint types, such as the square butt joint, are simple to create while others, such as the double U butt joint, require more resources and labor.
Square Butt Joint
The square butt joint is a straightforward configuration that is ideal for projects in which penetration depth is less critical. It’s simple and easy to prepare with the two pieces being flat and side by side.
- Advantages: Simple and easy to prepare.
- Disadvantages: Does not offer adequate penetration on thicker materials.
- Applications: General fabrication.
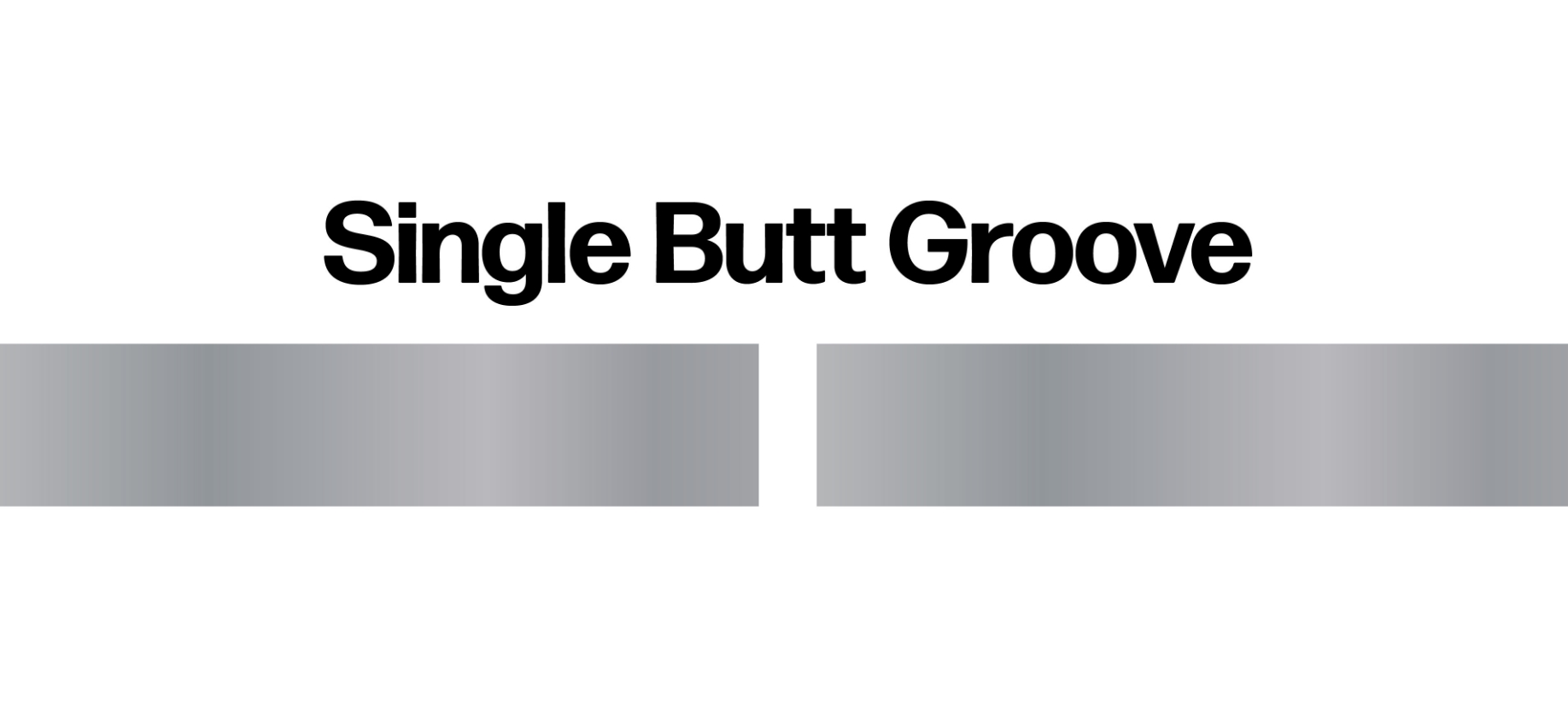
Single Bevel Butt Joint
The single bevel butt joint features a beveled edge on one side that enhances penetration compared to square butt joints. It’s excellent for structural applications, but the one-sided access makes it less suitable for thicker materials.
- Advantages: Improved penetration compared to square butt joints.
- Disadvantages: Limited to one-side access.
- Applications: Structural welding, plate welding.
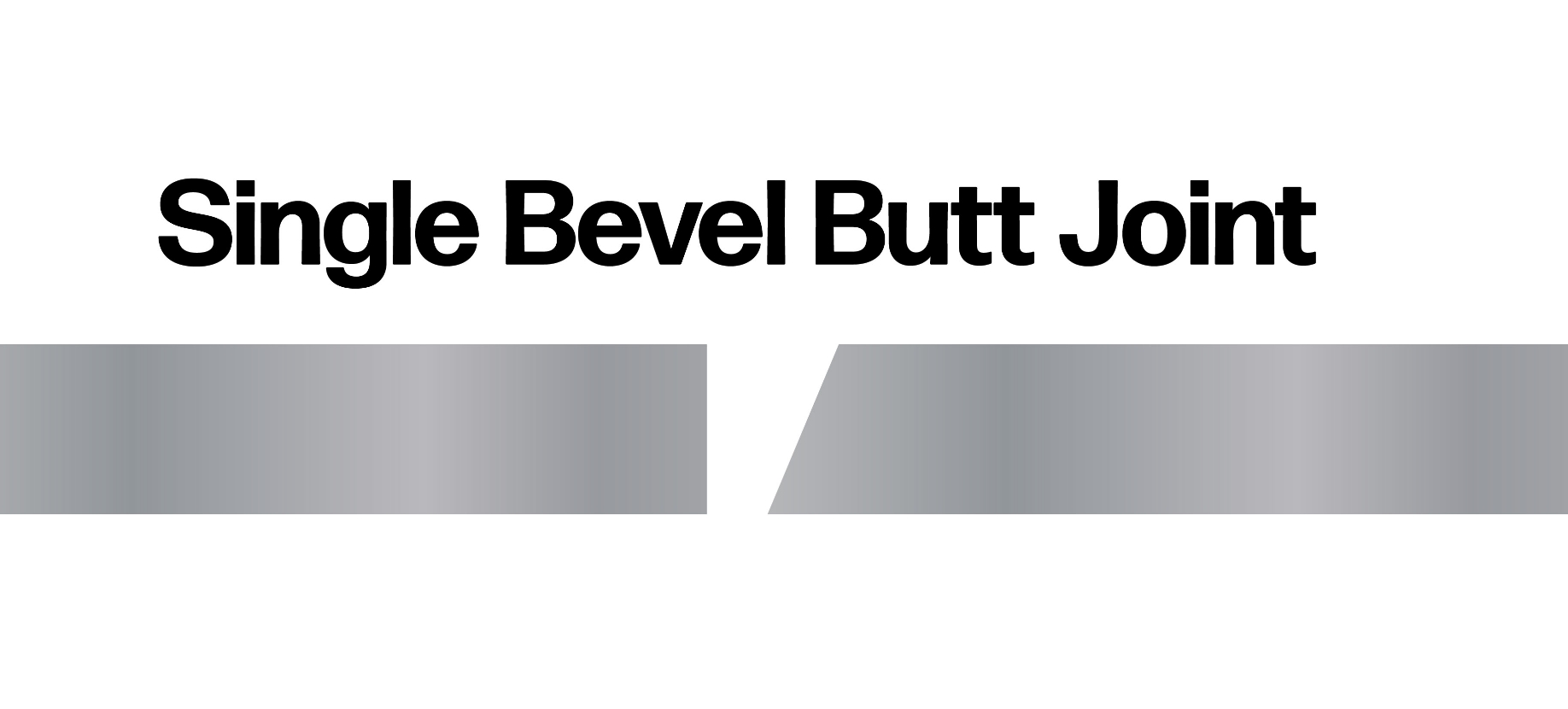
Double Bevel Butt Joint
Unlike the single bevel, the double bevel butt joint involves beveling both of the sides, providing better accessibility and penetration for thicker materials. It’s a more complex preparation, but it is incredibly useful for welding pressure vessels and other thicker structural components.
- Advantages: Increased penetration and improved accessibility.
- Disadvantages: Requires more complex preparation.
- Applications: Pressure vessels, pipe welding.
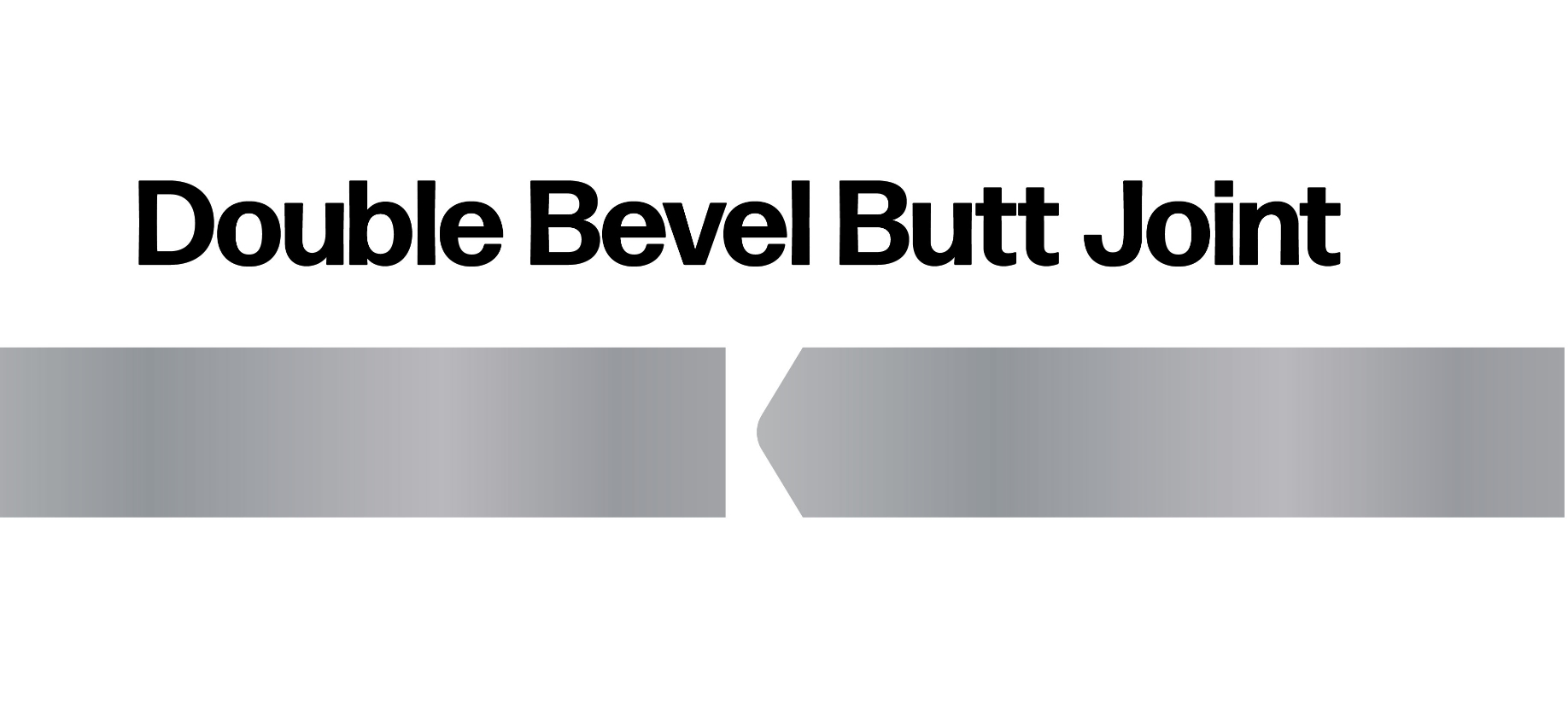
Single J Butt Joint
The single J butt joint enhances penetration on one side but is limited by this one-side only access. A more difficult configuration than a single V, the single J on thicker metals provides a stronger weld that requires less filler material.
- Advantages: Provides stronger welds that require less filler metal.
- Disadvantages: Requires expert level welding.
- Applications: Shipbuilding, structural welding.
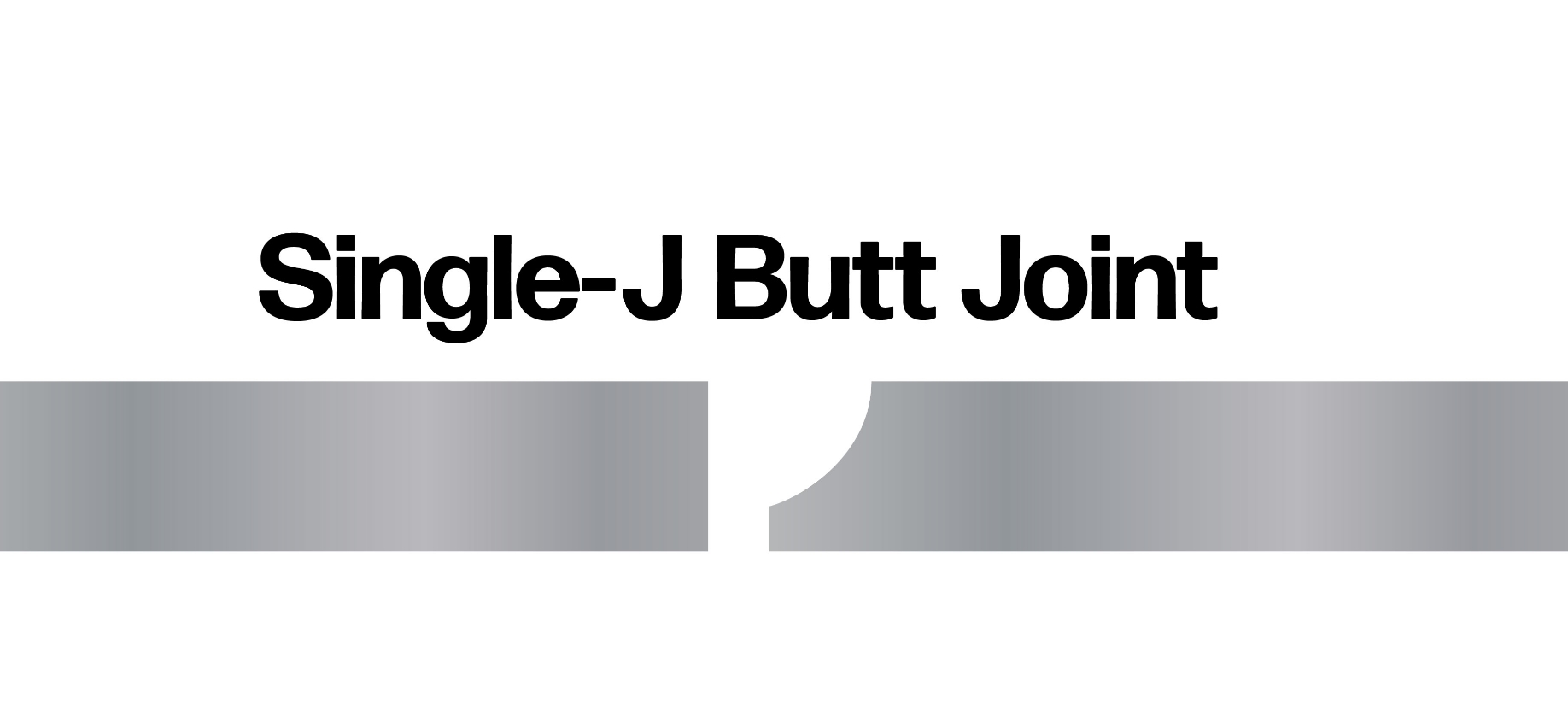
Double J Butt Joint
The double J butt joint, on the other hand, features enhanced accessibility without sacrificing penetration. It’s recommended to weld the butt joint in a horizontal position with the perpendicular edge on the bottom.
- Advantages: Features enhanced accessibility compared to single J butt joints.
- Disadvantages: More complex preparation and welding.
- Applications: Shipbuilding, bridge construction.
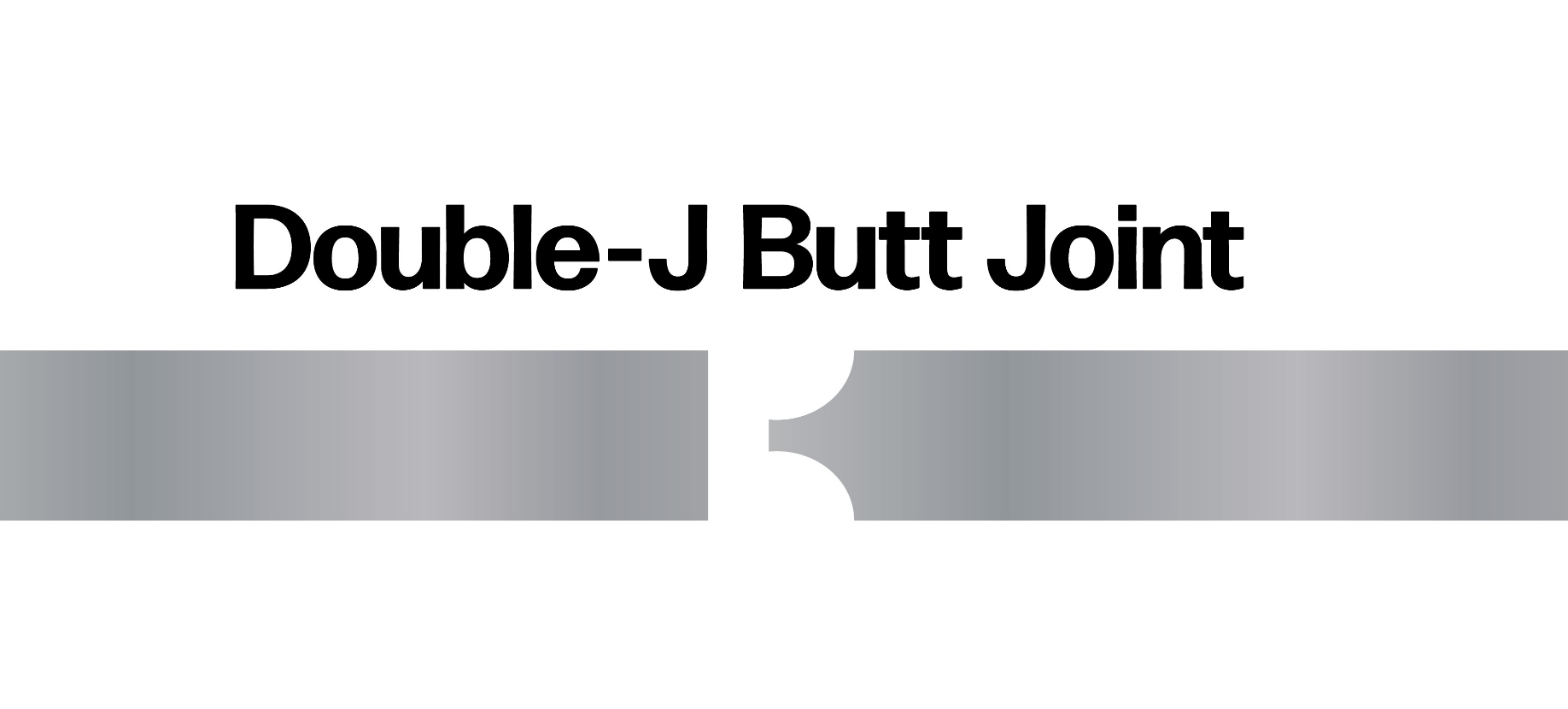
Single V Butt Joint
The single V butt joint is similar to a bevel joint, but both sides of the single V joint are beveled. This is one of the most common types of butt welds since it takes little effort to bevel the edges while still allowing for maximum penetration.
- Advantages: Allows for maximum penetration, offers easy bevel fabrication.
- Disadvantages: More expensive than single bevel and square butt welds, requires more resources and setup.
- Applications: Plate welding, structural welding.

Double V Butt Joint
The double V butt joint is mostly used on thick metals or when welding can be performed from both sides of the work piece. It generally requires less filler material and compensates for warping forces, working to prevent stress from disforming the metal.
- Advantages: Uses less filler metals than double V butt joints, compensates for warping forces.
- Disadvantages: Requires more time and materials to prepare and fill the grooves.
- Applications: Structural welding.
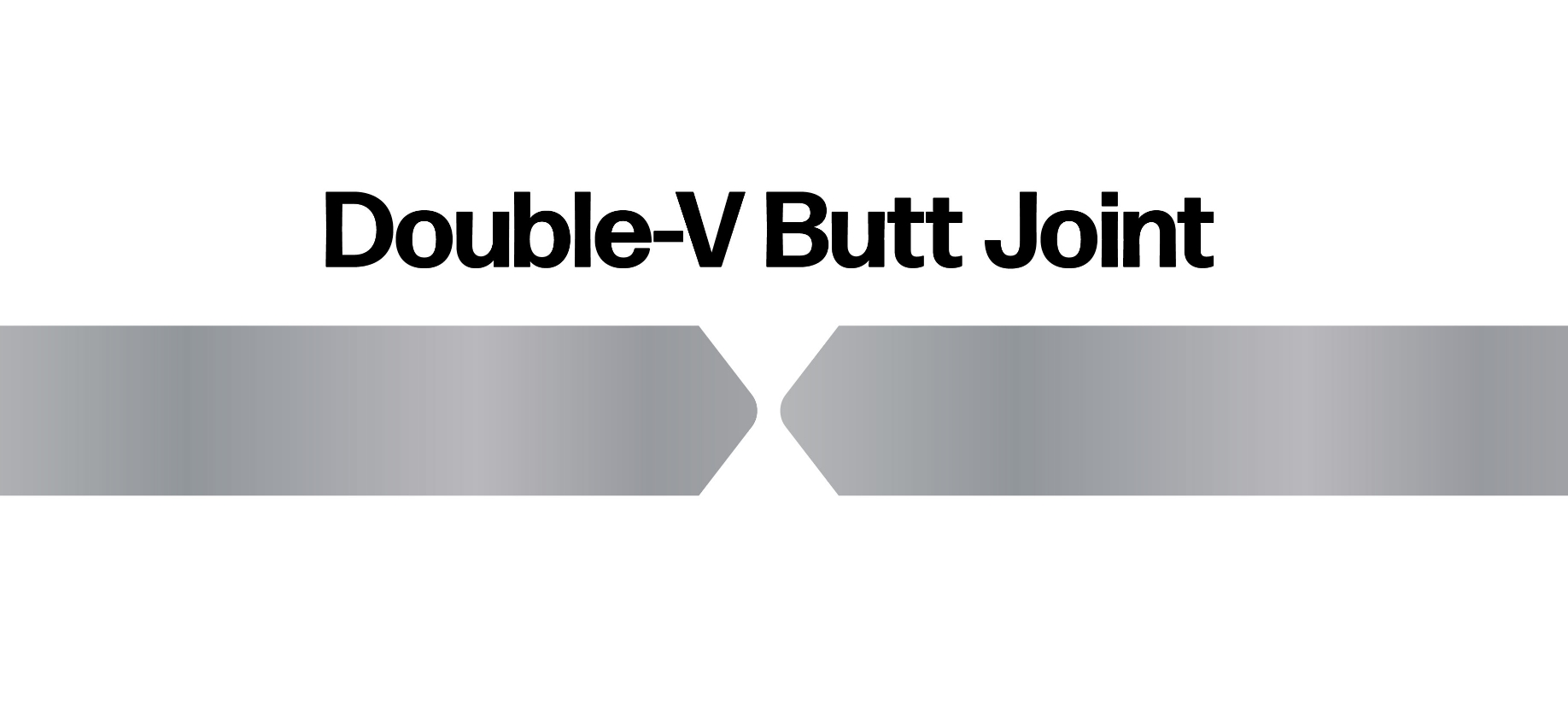
Single U Butt Joint
The single U butt joint has edges that require a concave treatment. Generally regarded as less expensive than a single V joint, this butt joint uses less filler metal to fill, but because of the joint’s skewed orientation, it requires more versatility in managing the weld pool, arc, and filler metal.
- Advantages: Creates more durable welds resistant to deformities and cracking.
- Disadvantages: Requires expert control over the weld pool, arc, and welding wire.
- Applications: Pipe welding, pressure vessels.
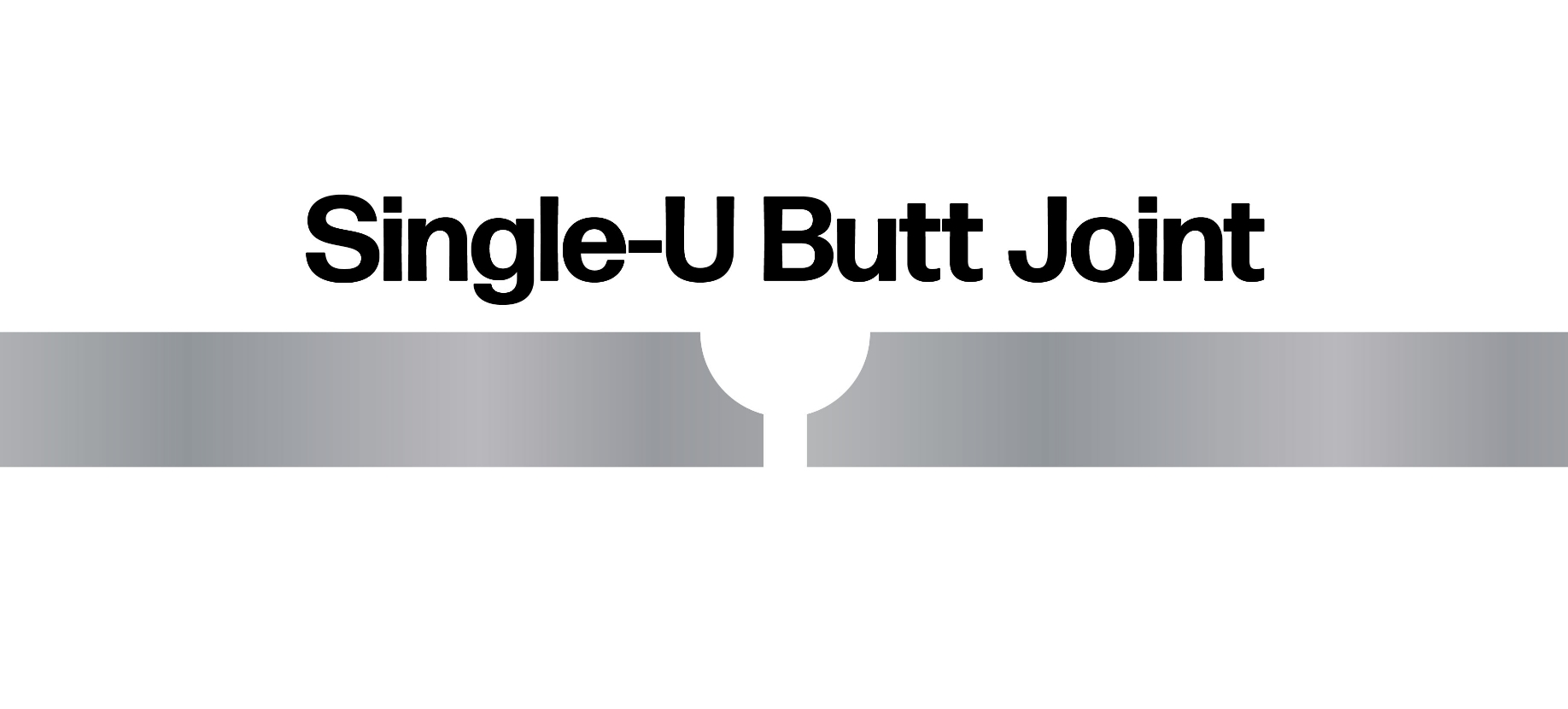
Double U Butt Joint
Double U butt joints provide better accessibility, but they are considered one of the most expensive edges to prepare and weld. Usually used on thick base metals, a double U joint is preferred when a double V butt joint would be at too extreme of an angle to fill.
- Advantages: Uses less filler metals.
- Disadvantages: Requires special tools for edge preparation.
- Applications: Heavy pressure vessels, heavy structural welding.
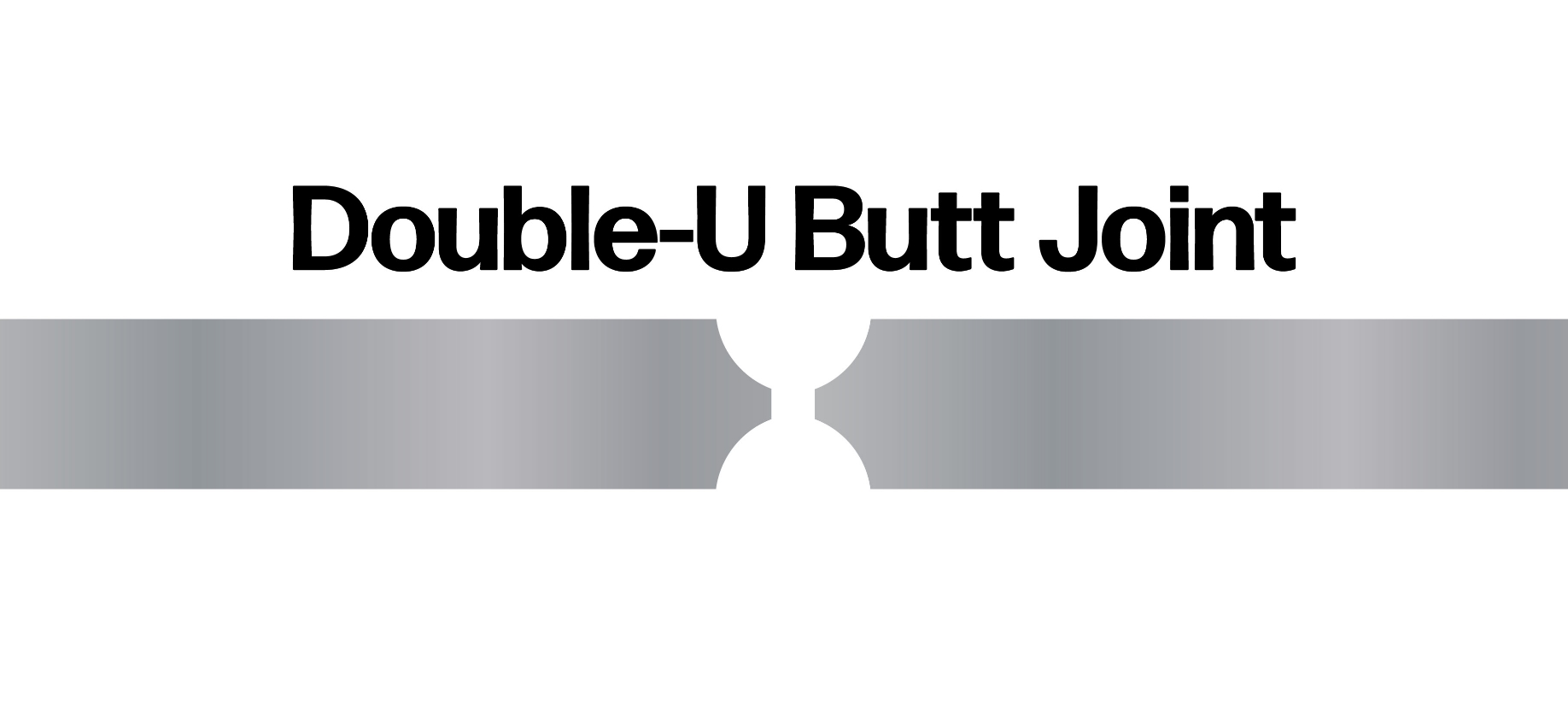
Butt Weld Vs. Fillet Weld: What’s the Difference
Butt welds and fillet welds both serve distinct purposes for different welding scenarios. Butt welds are meant to unite two materials side by side, on the same plane. Fillet welds do the opposite by joining two materials at an angle, usually 90 degrees. For fillet welds, the weld is deposited in the corner that is formed by the abutted surfaces.
Butt welds provide higher strength and structural integrity due to the increased cross-sectional area of the weld. Although butt welds require more edge preparation and materials, they can attain full penetration, which works to increase the strength of the weld.
Fillet welds are often used when connecting flanges to pipes and welding cross sections of infrastructure. Unlike with butt welds, the edges of the fillet weld don’t require extensive preparation, making it a quicker and more cost-effective method. However, fillet welds don’t typically provide 100 percent penetration, so they sometimes get discounted as not being critical welds. Critical welds will be determined by the design of the weldment and fillet welds can certainly be extremely critical to the design.
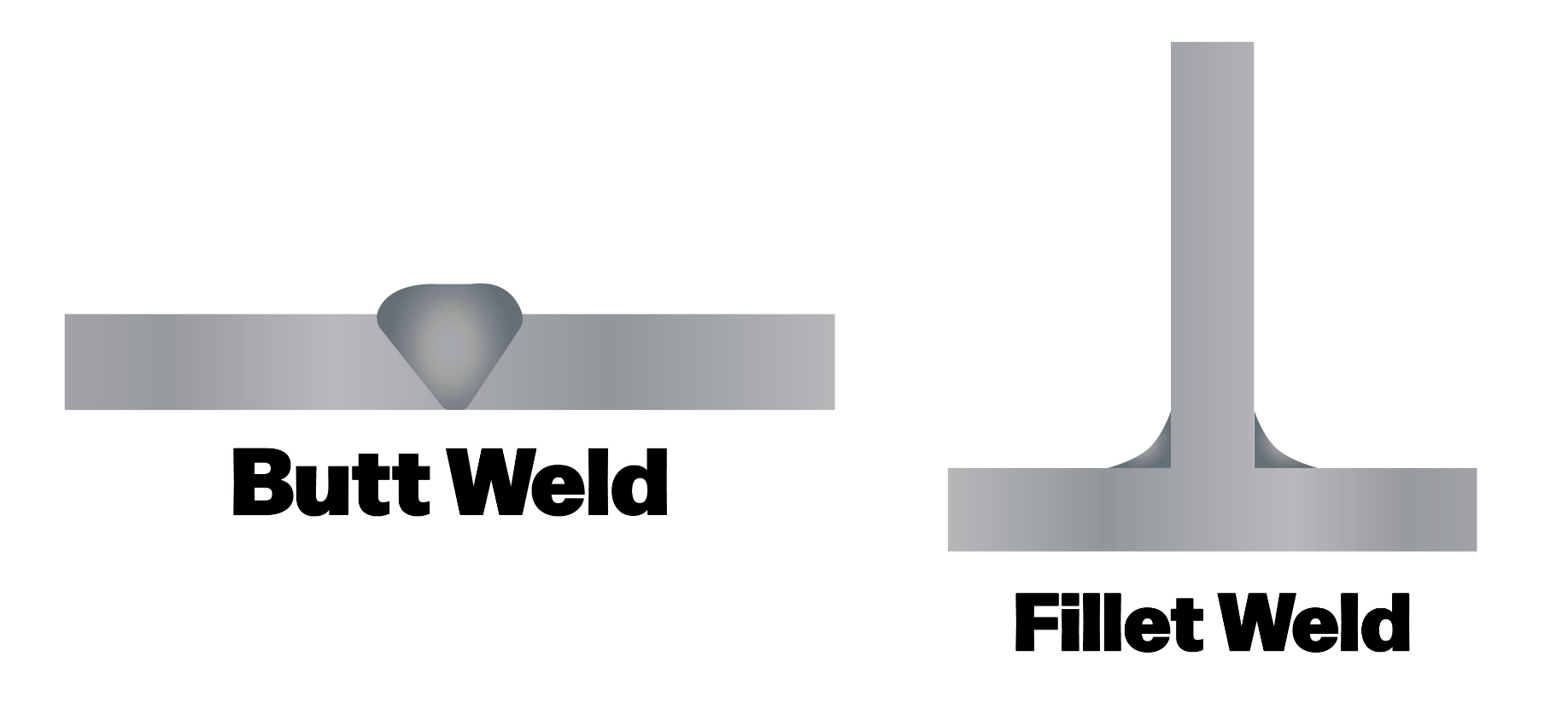
Advantages and Limitations of Welding a Butt Joint
Butt joint welding creates strong and reliable joints, but it’s not without its limitations. As one of the most commonly used welding techniques, it holds numerous advantages. The butt joints created are incredibly secure since the materials are welded together in a single welded seam, reinforcing the connection. It’s a straightforward process that’s easy to machine and easy to inspect. Additionally, with the filler metal deposited directly into the groove, it creates a smooth surface that’s aesthetically pleasing.
On the other hand, butt joint welding is not a flawless technique. If one of the pieces is thicker than the other, extra care needs to be taken, such as beveling the edges of the joint. Although it does create strong welds, there’s a high risk of cracking, warping, and insufficient penetration, so the welder needs to be extra cautious during the procedure. In addition, the technique is time-consuming and requires a lot of resources, depending on the type of butt joint involved. It takes a very skilled welder to successfully complete the weld quickly and efficiently.
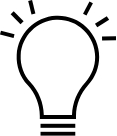
Butt Welding Tips to Help Achieve a Successful Weld
The best ways to enhance the quality of your butt joint welds are:
- Precision and Accuracy: Make sure that the measurements and alignments are precise to create a well-fit joint.
- Proper Cleaning: Always thoroughly clean the joint surfaces to eliminate debris, dust, rust, and other contaminants that could affect the quality of the weld.
- Correct Welding Wire/Electrode: Use the appropriate welding equipment, especially the welding consumables, that match the chemical and mechanical compositions of the base materials.
- Practice Regularly: Butt joint welding is a skill that requires experience, so regular practice is essential. We recommend working with various materials and applications to understand how to approach the technique under different circumstances.
Like with most welding techniques, butt joints come with their own set of problems that can occur. Some of these, which are common in most welding operations, include burn-through, porosity, cracking, or incomplete penetration or fusion. These problems can be avoided by remaining vigilant during the welding process, keeping an eye out for any signs of potential defects, and simply modifying the welding variables to make adjustments.
- Lack of Penetration: Increase voltage and amperage or use a thicker welding wire.
- Excessive Penetration: Reduce voltage and amperage or use a thinner welding wire.
- Incomplete Fusion: Adjust travel speed and maintain a consistent arc.
NS ARC Welding Wires for the Ultimate Welding Experience
Welding wire plays an especially important role in determining the success of the butt weld, and NS ARC can supply our welders with the best options available. Our team of experts can help walk you through our selection, helping you choose the correct welding wire that can help you achieve optimal penetration in butt joint welding. Whether you’re welding carbon steel, stainless steel, or aluminum, we carry the right wire with the appropriate composition, diameter, and type needed to achieve adequate penetration and fusion. Contact us today to start welding with unmatched strength and reliability.
Check out our entire selection of high-quality mig welding wires!
Learn MoreDISCLAIMER: This information is descriptive in nature and not purely prescriptive. Refer to your own welding machine’s user manual for proper settings and consult a welding expert for support.