Best Flux-Cored Welding Wire for Carbon Steel
Oct 23rd 2023
Flux-cored welding wire is a reliable and versatile filler metal that is used to establish a strong and solid bond between two pieces of metal. There are two types of flux-cored welding wire: gas-shielded, which requires an external shielding gas, and self-shielded, which does not. The gas-shielded type has a flux coating that solidifies faster than the molten weld material and works well with thicker metals. The self-shielded type generates the gas when the flux from the welding wire is burned, so it doesn’t require an external source.
Compared to solid wire or stick electrodes, flux-cored welding wires benefit from higher deposition rates, which allows you to complete welds at a more efficient pace, as well as deeper penetration for when working with thicker materials.
Another advantage of flux-cored welding wires is their versatility as some of them can be used in all welding positions, including flat, horizontal, vertical, and overhead. This allows welders to tackle a number of different welding projects that call for this level of flexibility without compromising the integrity of the weld.
There is no definitive “best” when it comes to flux-cored welding wire, but there are a number of factors that work together to determine which is the “best choice” for the welding job. When it comes to welding carbon steel materials, welders need to assess the grade of carbon steel, the thickness of the material, the location, and the application of the weld. These factors can help determine the appropriate flux-cored welding wire selection.
What to Consider When Selecting the Best Flux-Cored Welding Wire
The first and most crucial consideration is the compatibility of the type of flux-cored welding wire you want to use with the carbon steel material. We recommend that you focus on welding wires that are specifically designed for carbon steel applications. They should meet industry standards, such as AWS (American Welding Society) classifications.
The size and diameter of the welding wire should also be taken into careful consideration. They should be selected based on the thickness of the welded material and the welding equipment’s compacity. As a rule of thumb, thicker materials require larger-diameter flux-cored welding wires while thinner materials work best with smaller-diameter welding wires.
If you're uncertain about which flux-cored welding wire is best for your project, consult with experienced welders or welding engineers. Their expertise can help you make an informed choice based on the specifics of your welding job.
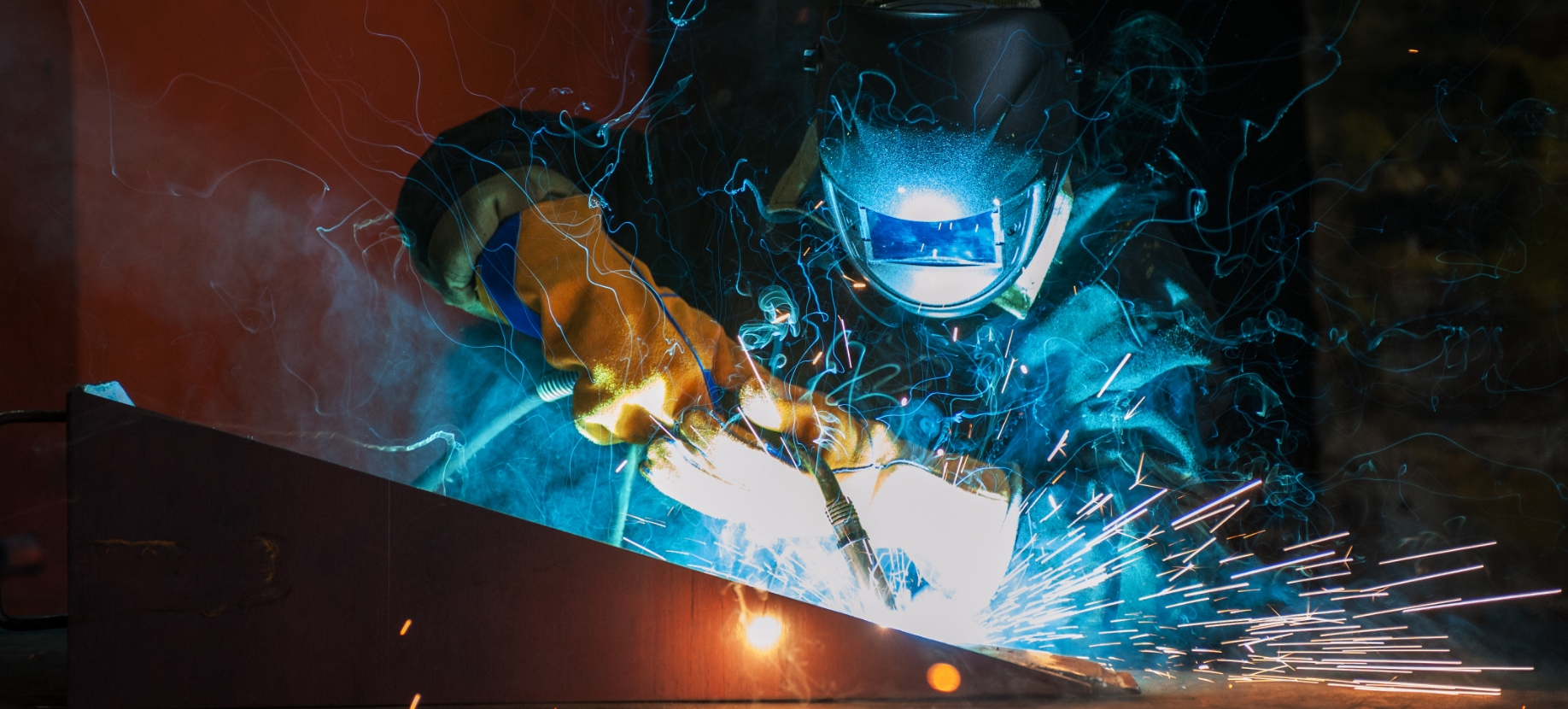
Best Choices for Flux-Cored Welding Wire
E70T-1 Welding Wire
- Characteristics: Used for single and multiple pass welding in flat or horizontal positions; operates with 100% CO2 shielding gas; suitable for welds requiring a minimum tensile strength of 70,000psi
- Common Applications: General fabrication, heavy equipment, and structural steel
- Advantages: Great choice for deep groove welds; easy slag removal; smooth arc transfer; low spatter; excellent feedability
E71T-1 Welding Wire
- Characteristics: Used for all-position single and multiple pass welding; suitable for welds requiring a minimum tensile strength of 70,000psi; excellent for work on 10-gauge sheet metal or heavy plate sections
- Common Applications: Agricultural equipment, structural steel, and trailers
- Advantages: Specially formulated slag system for a high melting point and quick-freezing properties; smooth wire feeding; excellent weld bead appearance
E71T-12 Welding Wire
- Characteristics: Gas-shielded; operates with gas blend (typically 75% Argon/25% CO2); all-position welding; single or multiple pass applications; suitable for welds requiring a minimum tensile strength of 70,000psi
- Common Applications: Heavy fabrication, pressure vessels, and railcars
- Advantages: Excellent performance with uniform results; small droplet arc transfer; enhanced flow and wetting; maintains consistent diffusible hydrogen levels
E81T-Ni1 Welding Wire
- Characteristics: Good CVN values at temperatures of -40°F and lower; all-position welding; single and multiple pass welds; suitable for welds requiring a minimum tensile strength of 80,000psi
- Common Applications: Heavy equipment, heavy fabrication, and structural steel
- Advantages: Fast freezing flag system; excellent bead geometry; smooth, small droplet arc transfer; minimum spatter residue; enhanced feedability
E81T-Ni2 Welding Wire
- Characteristics: Operates with 100% CO2 shielding gas; single and multiple pass welds; all-position welding; exceptional CVN values at temperatures as low as -40°F; suitable for welds requiring a minimum tensile strength of 80,000psi
- Common Applications: Agricultural equipment, heavy equipment, and pipe welding
- Advantages: Exceptional weld bead geometry; quick freezing slag system; deep penetration; excellent flow and wetting properties; low spatter
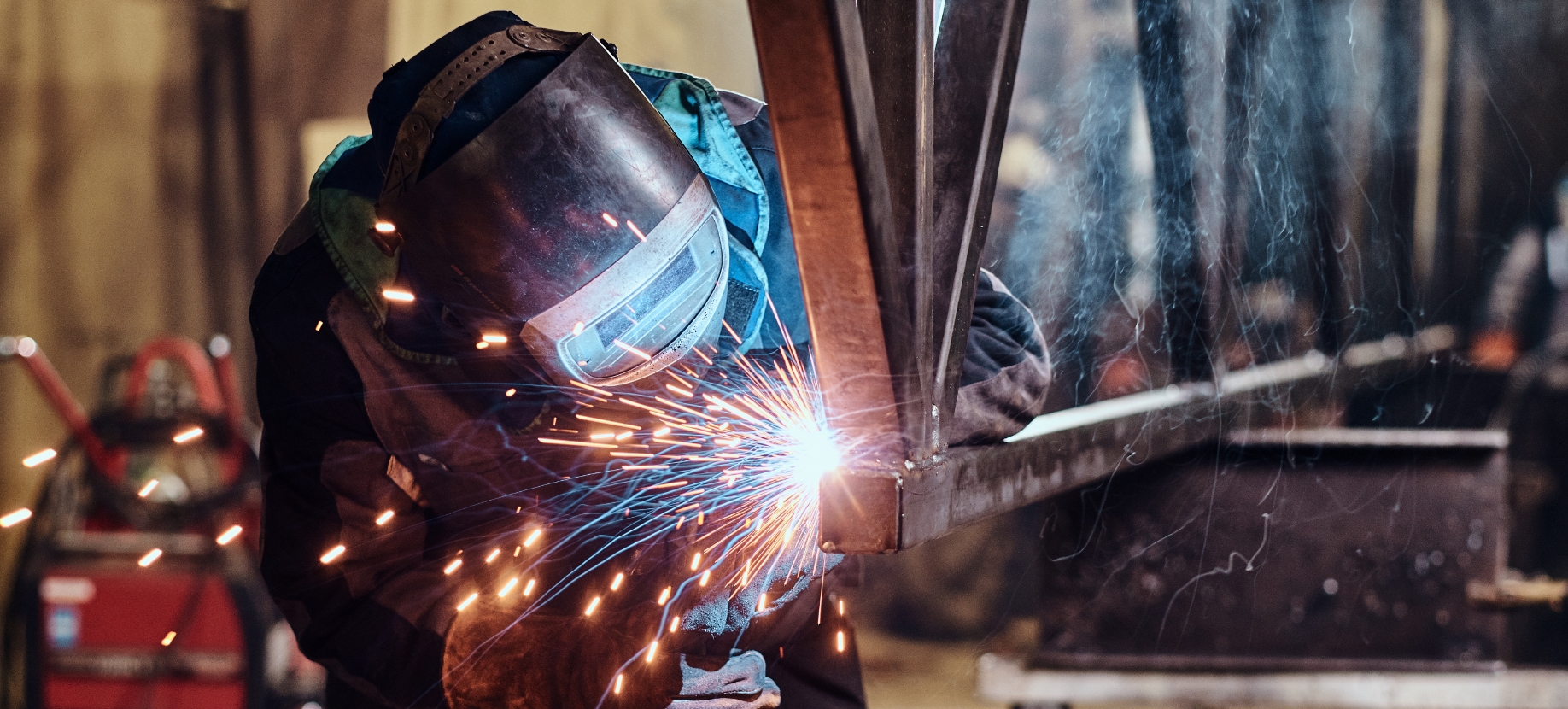
Other Key Factors to Consider
It’s important to consider the environmental conditions in which you'll be welding. For outdoor or windy conditions, self-shielding flux-cored welding wires may be the better choice since they don’t require external shielding gases.
The welding position you'll be working in, whether it’s flat, horizontal, vertical, or overhead, also plays a key role in choosing the right welding wire. Some flux-cored welding wires are designed for only flat or horizontal positions while others can be used in all-position welding, so select according to the specific job you’re working.
Quality control and assurance are also important factors to consider when selecting your flux-cored welding wire. Like almost every type of welding equipment, you need to make sure that the welding wire manufacturer adheres to stringent quality control standards and has the proper certifications and documents to back up their claims.
NS ARC Quality Flux-Cored Welding Wire
Welding carbon steel has never been easier with the reliability and strength of NS ARC Tru-Core® flux-cored welding wire in your hands. Our selection of high-quality flux-cored welding wires are engineered to promote superior weld quality as they produce a more stable arc and offer better penetration.
Our Tru-Core® FC 71T is an excellent choice for those who often work with E71T-1C H8, E71T-1M H8, E71T-9C H8, E71T-9M H8 wires as its user-friendly characteristics ensure precision and control for consistent and uniform welds. For more challenging applications, our Tru-Core® FC 81T-Ni2 provides unmatched welding strength to deliver outstanding results in demanding conditions. To learn more, contact the Pit Crew, our team of experts to help guide you through our full selection of flux-cored welding wire.
DISCLAIMER: This information is descriptive in nature and not purely prescriptive. Refer to your own welding machine’s user manual for proper settings and consult a welding expert for support.